Overview of Oil and Gas Separators and the Role of NDT in Preventing Accidents and Disasters
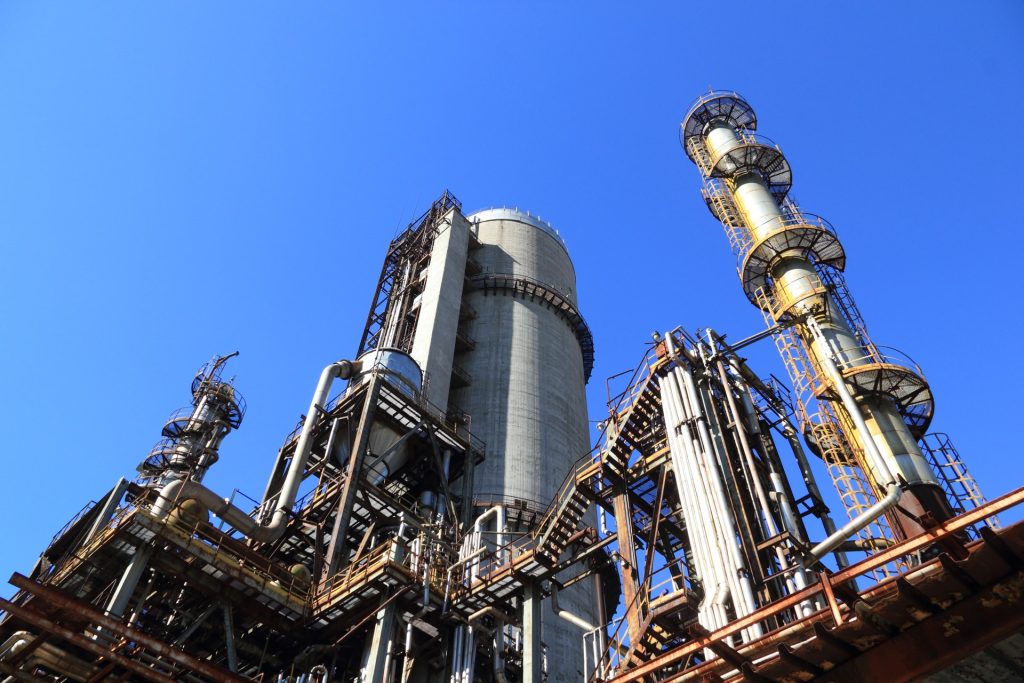
An oil and gas separator is a device used to separate oil and gas from a well stream. The well stream can contain a mixture of oil, water, and gas, and the separator is designed to separate these components into separate streams. There are several types of oil and gas separators, including horizontal, vertical, and spherical separators.
The design of the separator will depend on the characteristics of the well stream, such as the volume of oil and gas, the pressure and temperature of the stream, and the desired separation efficiency. Oil and gas separators are used in the upstream sector of the oil and gas industry, and play a vital role in the production and processing of hydrocarbons.
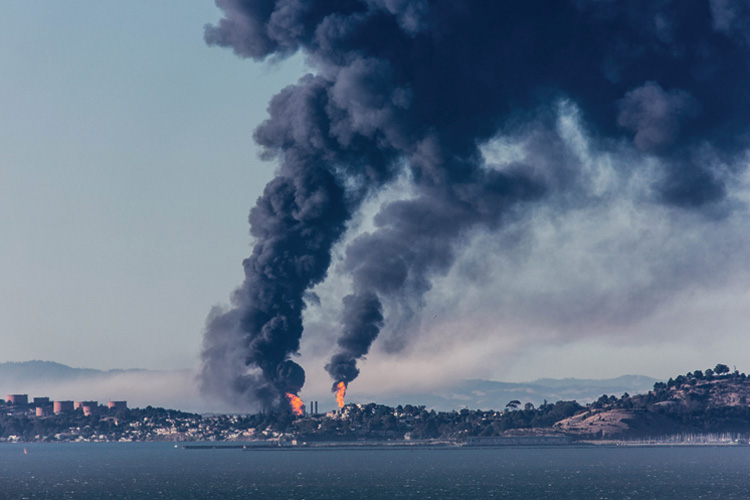
How does it work?
Oil and gas separators work by using the differences in density, size, and other physical properties of the oil, water, and gas components in the well stream to separate them. The well stream is introduced into the separator, which is typically a vessel or tank with an inlet and outlet. Inside the separator, the well stream is subjected to a number of processes that separate the components.
One common method of separation is to use gravity to allow the heavier oil and water components to settle to the bottom of the separator, while the lighter gas rises to the top. The separated oil and water are then drained off through the bottom outlet, while the gas is routed through the top outlet.
Other separation methods may be used as well, depending on the design of the separator. For example, a coalescer may be used to remove fine droplets of oil from the gas stream, or a mist extractor may be used to remove droplets of liquid from the gas. Separation efficiency can be improved by using a series of separators, each designed to separate specific components of the well stream.
Use of seperators
Oil and gas separators are used in the upstream sector of the oil and gas industry, which is concerned with the exploration, extraction, and processing of hydrocarbons. They are typically used at oil and gas production facilities, such as offshore platforms, onshore wells, and central processing facilities. Separators are used to separate the mixture of oil, water, and gas that is produced from an oil or gas well into its individual components.
Oil and gas separators are also used in other industries where liquids and gases are mixed and need to be separated, such as in the petrochemical, power generation, and food processing industries. In these industries, separators may be used to separate a wide range of liquids and gases, depending on the specific process being used.
NDT and inspection on seperators
NDT, or non-destructive testing, refers to a variety of techniques that are used to evaluate the properties of a material, component, or system without causing damage. NDT is commonly used in the oil and gas industry to inspect equipment and infrastructure for signs of wear, corrosion, or other defects that could impact their performance or safety.
Oil and gas separators can be inspected using a variety of NDT techniques, depending on the specific design and operating conditions of the separator. Some common NDT techniques that may be used on oil and gas separators include:
- Ultrasonic testing: This technique uses high-frequency sound waves to detect flaws or defects in the material.
- Magnetic particle inspection: This technique uses a magnetic field to detect surface or slightly subsurface defects in ferromagnetic materials.
- Liquid penetrant testing: This technique involves applying a liquid penetrant to the surface of the material and then removing the excess penetrant, leaving any penetrant that has seeped into surface defects.
- Eddy current testing: This technique uses electromagnetic fields to detect surface and slightly subsurface defects in conductive materials.
- Visual inspection: This technique involves visually inspecting the separator for signs of damage or defects using the naked eye or specialized visual inspection tools such as borescopes or fiberscopes.
NDT is an important tool for ensuring the safety and reliability of oil and gas separators and other equipment in the oil and gas industry.
Oil and gas seperator operating temperature
The operating temperature of an oil and gas separator will depend on a number of factors, including the type of hydrocarbons being processed, the pressure and flow rate of the well stream, and the design of the separator.
In general, the operating temperature of an oil and gas separator will be lower than the temperature at which the oil and gas components in the well stream are produced. This is because the separator is designed to cool the well stream as it is being processed, which can help to reduce the vapor pressure of the hydrocarbons and improve the separation efficiency. The specific operating temperature of a separator will depend on the characteristics of the well stream and the design of the separator.
It is important to note that the operating temperature of an oil and gas separator should not exceed the design limits of the separator or the materials of construction. Excessive temperatures can cause the separator to fail or degrade over time, leading to safety and reliability issues.
Separation process
There are several methods that can be used to separate water from oil in an oil refinery, and the specific method used will depend on the characteristics of the oil and water mixture and the desired separation efficiency. Some common methods for separating water from oil in an oil refinery include:
- Gravity separation: This method can be used to separate water from oil in an oil refinery by using the differences in density between the two components. The mixture is allowed to stand in a container, and the water settles to the bottom while the oil floats to the top. The water can then be drained off through a outlet near the bottom of the container, while the oil is skimmed off the top.
- Coalescence: This method uses a coalescer, which is a type of filter that removes fine droplets of water from the oil. The oil is passed through the coalescer, and the water droplets are attracted to and collect on the surface of the filter. The water droplets can then be removed from the filter, leaving the oil behind. Coalescence is often used in conjunction with other separation methods, such as gravity separation, to improve the overall separation efficiency.
- Centrifugation: This method uses a centrifuge to separate the water and oil based on their differences in density. The mixture is placed in a rotating drum, and the centrifugal force generated by the rotation causes the denser water to be forced to the outer edge of the drum, while the lighter oil is forced to the center. The separated water and oil can then be drained off through separate outlets. Centrifugation is often used in conjunction with other separation methods, such as gravity separation, to improve the overall separation efficiency.
- Distillation: This method uses the differences in boiling points between water and oil to separate them. The mixture is heated to a temperature above the boiling point of water but below the boiling point of oil. The water vaporizes and can be condensed back into a liquid, while the oil remains a liquid. The separated water and oil can then be collected. Distillation is often used in conjunction with other separation methods, such as gravity separation or centrifugation, to improve the overall separation efficiency.
NDT
NDT, or non-destructive testing, is a valuable tool for inspecting oil and gas separators and other equipment in the oil and gas industry. Some advantages of using NDT for separator inspection include:
- NDT can be used to inspect separators without disassembling them, which can save time and reduce the risk of damage to the equipment.
- NDT can be used to inspect separators that are in service, allowing for continuous operation of the equipment.
- NDT can be used to detect a wide range of defects and abnormalities, including cracks, corrosion, and other types of surface and subsurface damage.
- NDT can be used to inspect separators made from a variety of materials, including metals, plastics, and composites.
- NDT is often faster and more cost-effective than other inspection methods, such as visual inspection or disassembly.
- NDT can be used to inspect separators in a variety of environments, including offshore platforms and other locations where access may be limited.
Overall, NDT is an important tool for ensuring the safety and reliability of oil and gas separators and other equipment in the oil and gas industry. It helps to identify potential issues before they become serious problems, and can help to extend the lifespan of the equipment.
Disasters and accidents
Separators in the oil and gas industry can be vulnerable to disasters and accidents if they are not designed, constructed, and maintained properly. Some examples of separator disasters and accidents include:
- Explosion or fire: Separators can be vulnerable to explosion or fire if they are not designed and operated properly. For example, if the separator is not adequately protected against overpressure, it can rupture or explode. In addition, if flammable gases or liquids are present in the separator, they can ignite and cause a fire.
- Oil spills: Separators can leak oil if they are not properly maintained or if they are damaged. Oil spills can have serious environmental and economic consequences, and can be difficult and costly to clean up.
- Corrosion: Separators that are not protected against corrosion can suffer from structural failure and other issues. Corrosion can be caused by a variety of factors, including exposure to harsh environments, the presence of corrosive fluids, and poor maintenance.
- Structural failure: Separators that are not designed or constructed properly can suffer from structural failure, which can lead to leaks, spills, and other accidents. Structural failure can be caused by a variety of factors, including design flaws, improper construction, and overloading of the separator.
To prevent separator disasters and accidents, it is important to ensure that separators are designed, constructed, and maintained in accordance with industry standards and best practices. Regular inspections, maintenance, and repairs can help to ensure that separators are in good working order and are less likely to fail.
- In 2014, an explosion occurred at an oil refinery in Washington state, USA, when a failure in an oil-water separator led to a release of flammable vapors. The explosion caused several fires and resulted in the evacuation of thousands of people.
- In 2010, an oil spill occurred at an offshore platform in the Gulf of Mexico when a failure in an oil-water separator led to a release of oil into the ocean. The spill resulted in significant environmental damage and was one of the worst offshore oil spills in history.
- In 2018, a fire broke out at an oil refinery in California, USA, when an oil-water separator ruptured and released flammable liquids. The fire resulted in several injuries and significant damage to the refinery.
- In 2019, an explosion occurred at an oil refinery in Texas, USA, when a failure in an oil-water separator led to a release of flammable gases. The explosion resulted in several injuries and significant damage to the refinery.
These examples illustrate the potential consequences of separator failures in the oil and gas industry, and underscore the importance of designing, constructing, and maintaining separators in accordance with industry standards and best practices.
Responses