What is NDT?
NDT stands for Non-Destructive Testing. It is a method used to evaluate the properties of a material, component, or system without causing damage. The goal is to inspect and evaluate the material in order to ensure its quality, integrity, and reliability without affecting its future performance. NDT is widely used in various industries, including aerospace, petrochemical, construction, and manufacturing, to inspect equipment and materials for defects or anomalies.
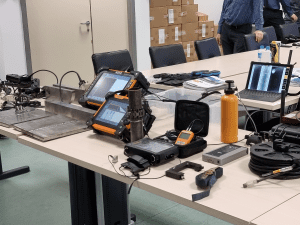
What are the common methods used in NDT?
Common NDT methods include:
- Ultrasonic Testing (UT) – using high-frequency sound waves to detect internal flaws or measure thickness.
- Radiographic Testing (RT) – using X-rays or gamma rays to produce an image of the material’s interior.
- Magnetic Particle Testing (MT) – using magnetic fields to detect surface and slightly subsurface discontinuities.
- Liquid Penetrant Testing (PT) – using a penetrant material to highlight surface flaws.
- Eddy Current Testing (ET) – using electromagnetism to detect flaws and measure material properties.
- Visual Testing (VT) – using the human eye to inspect the surface for defects.
- Acoustic Emission Testing (AE) – detecting and locating stress-related events in a material.
These methods are used separately or in combination, depending on the material, type of defect, and desired level of accuracy.
Where is NDT used?
NDT is used in a variety of industries and applications to ensure the safety, reliability, and quality of materials and equipment. Some common areas of use include:
- Aerospace industry – to inspect aircraft components and structures for defects and wear.
- Oil and gas industry – to inspect pipelines, storage tanks, and other equipment for corrosion and other anomalies.
- Manufacturing industry – to inspect raw materials, components, and finished products for quality and integrity.
- Construction industry – to inspect bridges, buildings, and other structures for structural integrity and potential safety issues.
- Power generation industry – to inspect boilers, turbines, generators, and other equipment for safety and reliability.
- Automotive industry – to inspect engines, transmissions, and other components for manufacturing defects and wear.
NDT is also used in the medical field to inspect implants, devices, and equipment for quality and performance. In addition, it is used in the art world to examine paintings, sculptures, and other works of art for authenticity and condition.
Why is NDT important for safety and quality control?
NDT is important for safety and quality control for several reasons:
- Early detection of problems: NDT helps to identify potential problems, such as cracks or corrosion, before they become major issues, reducing the risk of accidents, equipment failures, and other safety incidents.
- Quality assurance: NDT allows manufacturers and other organizations to assess the quality and integrity of materials and equipment, ensuring that they meet established standards and specifications.
- Cost savings: By detecting and addressing problems early, NDT can help to reduce the need for repairs and replacements, leading to significant cost savings.
- Reliability: NDT helps to ensure that equipment and structures are reliable and able to perform as intended, avoiding unplanned downtime and disruptions to operations.
- Compliance: NDT helps organizations comply with industry regulations and standards, which can be important for maintaining licenses, certifications, and other forms of recognition.
In summary, NDT is critical for ensuring the safety, quality, and reliability of materials and equipment, which can have a significant impact on overall operational performance, cost savings, and environmental protection.
Can NDT detect all types of defects in a material or component?
NDT cannot detect all types of defects in a material or component. The effectiveness of NDT depends on several factors, including the type of method used, the type of material being tested, and the size, location, and orientation of the defect. Some types of defects, such as subsurface cracks or inclusions, may be difficult or impossible to detect using certain NDT methods.
Additionally, some NDT methods may not be suitable for certain types of materials, such as very thick or dense materials, or materials that have a high level of electrical or magnetic interference.
Therefore, it is important to consider the capabilities and limitations of each NDT method and to use a combination of methods where appropriate, in order to obtain the most comprehensive and accurate inspection results possible.
What are the limitations of NDT and when should it be used in conjunction with other testing methods?
NDT has several limitations, including:
- Detection capabilities: Some types of defects may be difficult or impossible to detect using certain NDT methods.
- Accessibility: Some areas of a component or structure may be inaccessible for NDT inspection, making it difficult to obtain a comprehensive assessment.
- Surface conditions: Some surface conditions, such as heavy corrosion, paint, or dirt, can affect the accuracy of NDT results.
- Operator experience: The accuracy and reliability of NDT results can be affected by the experience and skill of the operator.
Therefore, NDT should be used in conjunction with other testing methods where appropriate, in order to obtain a more comprehensive understanding of the condition of a material or component. For example, NDT may be used in conjunction with visual inspection or destructive testing, where a sample is removed from the material or component and examined in detail.
In summary, while NDT is a powerful tool for detecting and assessing the condition of materials and components, it should be used in combination with other testing methods where necessary, in order to obtain the most comprehensive and accurate results.
How is the accuracy and reliability of NDT results ensured?
The accuracy and reliability of NDT results can be ensured through several measures, including:
- Operator qualifications: The operator performing the NDT should be properly trained and certified in the relevant NDT method, and have the experience and knowledge to perform the inspection effectively.
- Equipment calibration: The NDT equipment should be calibrated regularly to ensure that it is operating within the manufacturer’s specifications and producing accurate results.
- Quality control procedures: NDT results should be checked by a second operator or an independent quality control inspector to ensure that the results are accurate and consistent.
- Standard operating procedures: The NDT process should be carried out in accordance with established standard operating procedures, which outline the steps involved in the inspection and the criteria for evaluating the results.
- Record keeping: Detailed records of the NDT results, including any observations and measurements, should be maintained for future reference and for verification purposes.
In summary, the accuracy and reliability of NDT results can be ensured through a combination of properly trained operators, properly maintained and calibrated equipment, established quality control procedures, standard operating procedures, and comprehensive record keeping.
How has NDT evolved and what advancements are expected in the future?
NDT has evolved significantly since its inception, driven by advances in technology, changes in industry needs, and an increasing understanding of the benefits of NDT in various applications. Some of the key developments in NDT include:
- Improved imaging and analysis techniques: The development of advanced imaging technologies, such as computer tomography (CT) and digital radiography, has enabled NDT to produce higher quality images and to analyze those images in more detail.
- Automation and robotics: The automation of NDT procedures has increased the speed and accuracy of inspections, while robotics has enabled NDT to be performed in areas that were previously inaccessible.
- Increased use of NDT in new industries: NDT is being used in an increasingly diverse range of industries, including aerospace, medical devices, and power generation, as well as in traditional manufacturing and engineering applications.
- Integration with other technologies: NDT is being integrated with other technologies, such as artificial intelligence and machine learning, in order to increase its accuracy, efficiency, and effectiveness.
In the future, it is expected that NDT will continue to evolve and that new and innovative NDT methods will be developed to meet the changing needs of industry. Some of the areas of focus for NDT development are likely to include the use of artificial intelligence and machine learning for improved analysis, the integration of NDT with other technologies, such as the Internet of Things (IoT), and the use of NDT for real-time monitoring and condition assessment.
What qualifications and certifications are required for NDT technicians?
The qualifications and certifications required for NDT technicians vary depending on the country and industry, but typically include:
- Education: Many NDT technicians have a background in engineering, physics, or a related field, although some NDT positions may only require a high school diploma or equivalent.
- Training: NDT technicians must receive specialized training in the NDT methods they will be using, including both theoretical and hands-on instruction. This training can be provided by the employer, a training center, or a professional NDT organization.
- Certification: Many NDT technicians are required to be certified by a professional organization in order to demonstrate their knowledge and skills. The most widely recognized certification bodies for NDT technicians include the American Society for Nondestructive Testing (ASNT), the British Institute of Non-Destructive Testing (BINDT), and the Canadian General Standards Board (CGSB).
Certification usually requires passing an examination that covers the principles, procedures, and applications of the NDT methods, as well as demonstrating a certain level of practical experience. The certification process is designed to ensure that NDT technicians have the knowledge and skills necessary to perform NDT inspections effectively and accurately.
In summary, the qualifications and certifications required for NDT technicians typically include education, training, and certification from a professional organization. The specific requirements may vary depending on the country and industry, but the goal is to ensure that NDT technicians have the knowledge and skills necessary to perform their job effectively and safely.
What is the cost associated with NDT and how does it compare to other testing methods?
The cost of NDT depends on several factors, including the type of NDT method used, the size and complexity of the item being tested, and the duration of the inspection. In general, NDT is less expensive than many other testing methods, such as destructive testing, as it does not damage the item being tested and can often be performed more quickly.
For example, X-ray and ultrasonic inspections are often less expensive than destructive testing methods, such as cutting a sample from a part for laboratory testing. Similarly, visual inspections are often less expensive than other NDT methods, but may not provide the same level of detail or confidence in the results.
It is also worth noting that the cost of NDT may be offset by the benefits it provides, such as increased safety, improved quality control, and the ability to extend the service life of components and systems.
In summary, the cost of NDT varies depending on several factors, but it is generally less expensive than many other testing methods, and its benefits can help to offset its cost.
What is the role of NDT in the inspection and maintenance of critical infrastructure?
NDT plays a critical role in the inspection and maintenance of critical infrastructure, such as bridges, dams, pipelines, and power plants. The primary role of NDT in this context is to detect and evaluate potential flaws and damage in these structures, without causing additional damage or disruption to their normal operation.
NDT allows inspectors to examine the internal structure of critical infrastructure components, such as pipes and steel beams, without the need for disassembly or other destructive testing methods. This helps to minimize downtime and reduce the risk of further damage, while providing a thorough evaluation of the structural integrity of the component.
NDT techniques such as ultrasonic testing, radiographic testing, and magnetic particle inspection can be used to detect and quantify cracks, corrosion, and other types of damage, providing valuable information for maintenance and repair decisions.
In addition, NDT can also be used to monitor critical infrastructure over time, allowing engineers and maintenance personnel to track changes in the structure and identify developing problems before they become serious. This proactive approach to maintenance can help to extend the service life of critical infrastructure, minimize downtime, and reduce the risk of failure.
In summary, the role of NDT in the inspection and maintenance of critical infrastructure is to provide a non-destructive evaluation of the internal structure of components, detect and evaluate potential flaws and damage, and monitor changes over time in order to extend the service life of the infrastructure and minimize downtime.
How does NDT help organizations comply with industry regulations and standards?
NDT helps organizations comply with industry regulations and standards by providing a non-destructive way to inspect and evaluate the quality and safety of products and components. Many industry regulations and standards specify the use of NDT for various types of inspections and evaluations, as it provides a reliable and accurate way to assess the quality and safety of products and components without causing damage.
For example, the aerospace industry requires the use of NDT for the inspection of aircraft components, such as airframes and engines, to ensure that they meet specified standards for safety and performance. Similarly, the oil and gas industry uses NDT to inspect pipelines for corrosion and other types of damage, as specified by industry standards and regulations.
NDT can also provide valuable documentation for organizations, demonstrating that they have performed the required inspections and evaluations in accordance with industry regulations and standards. This documentation can be important in the event of a regulatory audit or lawsuit, as it provides evidence that the organization has taken appropriate steps to ensure the quality and safety of its products and components.
In summary, NDT helps organizations comply with industry regulations and standards by providing a non-destructive way to inspect and evaluate the quality and safety of products and components, and by providing valuable documentation that demonstrates compliance with industry regulations and standards.
Can NDT be used for remote or autonomous inspections?
Yes, NDT can be used for remote or autonomous inspections in some cases. Advances in technology and automation have made it possible to perform NDT inspections using remote and autonomous systems, such as drones and robots.
For example, unmanned aerial vehicles (UAVs) equipped with NDT sensors, such as ultrasonic sensors, can be used to inspect large structures, such as bridges and pipelines, from the air. This can be useful in situations where it is not safe or practical for human inspectors to access the structure directly, or where the structure is too large to inspect manually.
Similarly, robots equipped with NDT sensors can be used to perform internal inspections of pipelines, boilers, and other types of equipment. These autonomous systems can navigate through complex structures and provide a detailed evaluation of the internal condition of the component.
Remote and autonomous NDT inspections have several benefits, including increased safety, reduced inspection time, and improved access to difficult-to-reach locations. However, it is important to note that the use of remote and autonomous NDT systems still requires the expertise of NDT technicians, who must interpret the data collected by the system and make decisions based on the results.
In summary, NDT can be used for remote or autonomous inspections in some cases, using unmanned aerial vehicles and robots equipped with NDT sensors. These systems can provide increased safety and improved access to difficult-to-reach locations, but still require the expertise of NDT technicians to interpret the results.
How does NDT impact the environment and sustainability efforts?
NDT has a positive impact on the environment and sustainability efforts in several ways.
Firstly, NDT is a non-destructive testing method, meaning that it does not cause any damage to the component being tested. This is in contrast to other testing methods, such as destructive testing, which involves physically damaging the component in order to evaluate its quality and performance. By avoiding damage to the component, NDT reduces waste and the need for replacement components, which can have a positive impact on the environment and sustainability efforts.
Secondly, NDT can be used to evaluate the condition and performance of components and products in a way that can help organizations extend the life of their assets and reduce the need for replacement and disposal. This can help organizations reduce their environmental impact by reducing waste and conserving resources.
Thirdly, NDT can be used to evaluate the performance of energy systems and structures, such as wind turbines and pipelines, to ensure that they are functioning efficiently and effectively. This can help organizations reduce their energy consumption and greenhouse gas emissions, and contribute to sustainability efforts.
Finally, NDT can be used to evaluate the safety of structures and components, such as bridges and pipelines, to ensure that they are free from defects and damage that could lead to failure and environmental harm. This can help organizations prevent accidents and incidents that could have a negative impact on the environment and sustainability efforts.
What are the benefits of NDT for manufacturers and suppliers in terms of quality assurance and cost savings?
NDT offers several benefits for manufacturers and suppliers in terms of quality assurance and cost savings.
Quality assurance:
- NDT provides a non-destructive and efficient way of evaluating the quality and performance of components and products, which helps manufacturers and suppliers ensure that their products meet customer requirements and industry standards.
- NDT can detect defects and problems in components and products at an early stage, which can help manufacturers and suppliers avoid costly repairs and replacements down the line.
- NDT can help manufacturers and suppliers optimize their production processes, as it provides real-time feedback on the quality and performance of their products during the manufacturing process.
Cost savings:
- NDT is a cost-effective alternative to destructive testing, as it does not require the destruction of the component being tested.
- NDT can help manufacturers and suppliers reduce the cost of repairs and replacements by detecting defects and problems early on.
- NDT can help manufacturers and suppliers optimize their production processes and reduce the cost of production by providing real-time feedback on the quality and performance of their products.
- NDT can help manufacturers and suppliers reduce the cost of waste by reducing the need for scrap and rework, as it provides accurate and reliable information on the quality and performance of their products.
What are the most advanced and cutting-edge NDT technologies available today?
The field of NDT is constantly evolving, and new and advanced technologies are being developed to improve the accuracy and efficiency of NDT inspections. Some of the most advanced and cutting-edge NDT technologies available today include:
- Phased Array Ultrasonic Testing (PAUT): PAUT is a form of ultrasonic testing that uses multiple ultrasonic probes to perform a complete inspection of a component in a single pass. PAUT provides a faster and more efficient alternative to traditional ultrasonic testing and is particularly useful for inspecting complex geometries and irregular surfaces.
- Computed Tomography (CT) Scanning: CT scanning is a form of X-ray imaging that uses computer algorithms to produce high-resolution, three-dimensional images of internal structures and components. CT scanning is particularly useful for inspecting the internal structure of components and can detect cracks, voids, and other defects that are not visible using traditional NDT methods.
- Eddy Current Testing (ECT): ECT is a form of electromagnetic testing that uses electrical currents to inspect the surface and subsurface of conductive components for defects. ECT is particularly useful for inspecting thin-walled components and is capable of detecting cracks, corrosion, and other defects in real-time.
- Thermography: Thermography is a form of infrared imaging that uses heat to inspect the surface of components for defects and problems. Thermography can detect areas of heat loss, which can indicate the presence of insulation defects, air leaks, and other problems.
- Guided Wave Testing (GWT): GWT is a form of ultrasonic testing that uses guided waves to inspect the surface and subsurface of components for defects. GWT is particularly useful for inspecting long, thin components, such as pipes, and is capable of detecting corrosion, cracks, and other defects in real-time.
These are just a few examples of the advanced and cutting-edge NDT technologies available today. The field of NDT is constantly evolving, and new and innovative technologies are being developed to improve the accuracy, efficiency, and safety of NDT inspections.
How does NDT compare to other inspection methods, such as visual inspection or destructive testing?
NDT is different from visual inspection and destructive testing in several key ways:
- Non-Destructiveness: As the name suggests, NDT is a non-destructive testing method, which means that it does not damage or alter the component being tested in any way. This is in contrast to destructive testing methods, such as tensile testing or hardness testing, which involve physically altering or destroying the component to test its properties.
- Internal Inspection: NDT methods, such as ultrasonic testing, eddy current testing, and radiographic testing, can inspect the internal structure and properties of a component, whereas visual inspection and other methods are limited to only inspecting the surface.
- Real-Time Testing: NDT methods, such as eddy current testing and ultrasonic testing, can provide real-time inspection results, whereas visual inspection and destructive testing require time to remove the component, perform the test, and analyze the results.
- Cost and Time: NDT can often be more cost-effective and time-efficient than other inspection methods, especially for large or complex components. For example, NDT methods, such as ultrasonic testing, can perform a complete inspection of a component in a single pass, whereas visual inspection or destructive testing may require multiple tests to be performed.
- Repeatability: NDT methods, such as ultrasonic testing, provide consistent and repeatable results, whereas visual inspection and destructive testing can be subject to interpretation and human error.
In conclusion, NDT offers several advantages over other inspection methods, including non-destructiveness, internal inspection, real-time testing, cost and time-efficiency, and repeatability, which make it a valuable tool for organizations looking to ensure the quality and reliability of their components and systems.
What are the ethical considerations and safety implications of using NDT?
There are several ethical considerations and safety implications associated with using NDT:
- Radiation Safety: NDT methods that involve ionizing radiation, such as radiographic testing and gamma-ray testing, can pose a risk to both the operators and the surrounding environment if not properly managed. For example, exposure to high levels of ionizing radiation can cause cancer, genetic mutations, and other health problems.
- Data Accuracy: NDT results can have serious consequences for the component being tested, and therefore it is important to ensure the accuracy and reliability of the results. Technicians performing NDT must have proper training and qualifications to ensure that they are capable of interpreting the results accurately.
- Confidentiality: NDT results can contain sensitive information about the component being tested, and it is important to maintain the confidentiality of this information to prevent unauthorized access or misuse.
How can NDT be used in the art world to examine works of art for authenticity and condition?
Non-destructive testing (NDT) techniques can be used in the art world to examine works of art for authenticity and condition, without causing any damage to the artwork. Some common NDT methods used in the art world include:
- X-Ray Fluorescence (XRF): XRF is a non-destructive method used to analyze the composition of an artwork and determine the presence of any restoration materials.
- Infrared (IR) Thermography: IR thermography is used to examine the thermal properties of an artwork and detect any hidden layers or changes in the surface temperature that may indicate the presence of a forgery or restoration.
- Ultraviolet (UV) Fluorescence: UV fluorescence is used to detect the presence of any fluorescing materials in an artwork, such as certain pigments or varnishes, that are not visible under normal light.
- Micro-CT Scanning: Micro-CT scanning is a non-destructive method used to create high-resolution 3D images of an artwork, allowing for the examination of internal structures and hidden details.
By using these NDT techniques, art experts and conservators can gain valuable insight into the authenticity and condition of a work of art, and make informed decisions about preservation and restoration. Additionally, NDT can provide critical information for the authentication and attribution of artworks, helping to prevent the spread of forgeries and protect the cultural heritage of humanity.
In conclusion, Non-Destructive Testing (NDT) is a crucial tool for various industries and applications, including aerospace, automotive, energy, construction, manufacturing, and many more. NDT techniques provide a non-invasive way to inspect and evaluate the condition of structures, components, and materials without causing any damage. This makes NDT an important tool for quality assurance, safety inspections, and maintenance, helping organizations to identify and address potential problems early on.
NDT has evolved significantly over the years, with advancements in technology leading to the development of new and more sophisticated methods. NDT technicians require specialized training and certifications to perform NDT inspections and ensure accuracy and reliability of results. Despite the cost associated with NDT, it can provide significant cost savings in the long run by avoiding costly repairs and replacements.
NDT also plays an important role in helping organizations comply with industry regulations and standards, as well as supporting sustainability and environmental efforts. The benefits of NDT for manufacturers and suppliers include improved quality assurance, increased safety, and cost savings.
Overall, NDT is a versatile and valuable tool that provides critical information and insights, helping organizations to make informed decisions and ensure the safety and integrity of their assets and infrastructure.