What is NDT (Non-Destructive Testing) and Inspection Methods
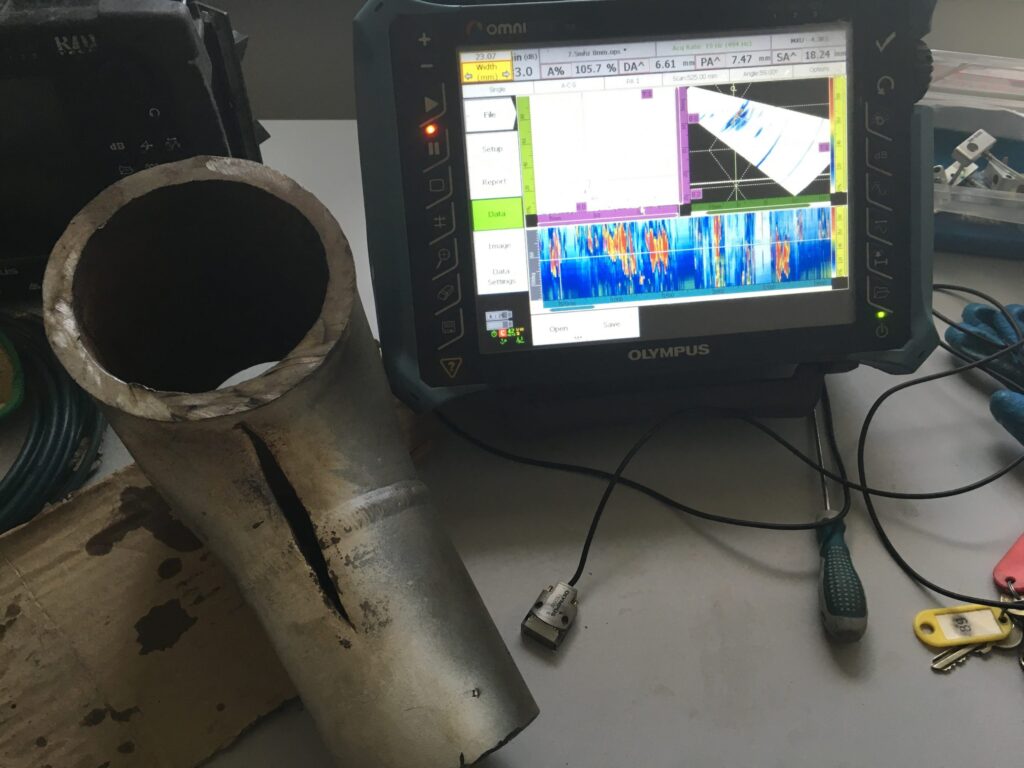
What is NDT?
What is NDT? NDT, or nondestructive testing, is a type of testing that is used to evaluate the properties of a material, component, or system without causing damage or altering its original condition. NDT is commonly used in industries such as manufacturing, construction, and transportation to ensure the safety and integrity of materials and components. It is also used in the oil and gas, aerospace, and power generation industries to monitor the condition of critical equipment and to identify potential problems before they cause failures or accidents.
NDT uses a variety of techniques and methods to detect and evaluate defects or abnormalities in materials and components. These methods include ultrasonic testing, radiographic testing, magnetic particle testing, liquid penetrant testing, visual testing, eddy current testing, acoustic emission testing, and phased array ultrasonics, among others. Each method is suited to different applications and materials, and they are used to detect a wide range of defects, including cracks, voids, inclusions, corrosion, and other surface or subsurface anomalies.
NDT is performed by trained and certified inspectors who follow established procedures and standards to ensure the accuracy and reliability of the testing. The inspectors use specialized equipment and tools to perform the testing, such as ultrasonic probes, x-ray generators, magnetic particle yokes, and other devices. The results of the NDT are typically presented in the form of images, data, or reports, which are analyzed and interpreted by the inspector to determine the condition of the material or component and any necessary repairs or actions.
NDT offers several advantages over other testing methods. It is a non-destructive method, so it does not alter the physical or chemical properties of the material being tested. This allows for the repeated testing of the same material or component, and it allows for the preservation of the material or component for other purposes, such as research or historical preservation. NDT is also a highly accurate and reliable method, and it can detect defects that are not visible to the naked eye or other testing methods. In addition, NDT is relatively fast and efficient, allowing for the rapid inspection of large areas or complex components.
Despite its many advantages, NDT does have some limitations. It is not suitable for all materials or applications, and it may not be effective for detecting certain types of defects, such as subsurface defects or defects that are not aligned with the direction of the testing. NDT also requires specialized equipment and trained personnel to perform the testing and interpret the results, which can make it more expensive than some other testing methods. Additionally, the results of NDT are highly dependent on the skill and experience of the inspector, and the quality of the testing can vary depending on the inspector’s qualifications and capabilities.
History of NDT
Non-destructive testing (NDT) is a relatively modern technology that was first developed in the early 20th century.
The development of NDT began in the early 1900s when X-ray technology was used to inspect welds in metal parts. Other techniques, such as ultrasonic testing and eddy current testing emerged shortly after. Since then, new technologies have been developed such as acoustic emission testing and magnetic particle testing. These methods are now widely used in a variety of industries to ensure the reliability and safety of products.
NDT Methods
- Ultrasonic testing: This method uses high-frequency sound waves to detect internal defects or measure the thickness of materials.
- Radiographic testing: This method uses X-rays or gamma rays to create an image of the internal structure of an object, allowing for the detection of flaws or defects.
- Magnetic particle testing: This method uses a magnetic field to detect surface or slightly subsurface discontinuities in ferromagnetic materials.
- Liquid penetrant testing: This method involves applying a liquid penetrant to the surface of an object and then removing any excess penetrant. The penetrant is then drawn into any surface-breaking defects, where it can be seen with the naked eye or under ultraviolet light.
- Visual testing: This method involves using the naked eye or a visual aid, such as a magnifying glass or borescope, to inspect the surface of an object for defects.
- Eddy current testing: This method uses electromagnetic fields to detect surface and subsurface defects in conductive materials.
- Acoustic emission testing: This method uses sensors to detect and locate the source of mechanical or acoustic activity, such as cracking or friction, within an object.
- Phased array ultrasonics: This method uses multiple transducers to produce and control the ultrasonic waves that are used to inspect a material or component.
- Time of Flight Diffraction: This method is a type of nondestructive testing method that uses ultrasonic waves to detect and measure defects in materials and components. It is often used in conjunction with phased array ultrasonics, where phased array transducers are used to create and control the ultrasonic waves.
- Hardness Testing: is a commonly used method for evaluating the hardness of materials.
- Internal Rotary Inspection: Also known as internal rotary ultrasonic inspection or internal rotary UT, is a nondestructive testing (NDT) method that is used to detect and evaluate defects or abnormalities in the internal surfaces of pipes, tubes, and other cylindrical components.
- Thermography: Also known as infrared thermography or thermal imaging, is a nondestructive testing (NDT) method that is used to detect and evaluate changes in temperature in materials or objects.
There are many other NDT methods, and new methods are constantly being developed. These methods are chosen based on the specific properties of the material being tested and the type of defects that are being sought.
1. Ultrasonic Testing (UT)
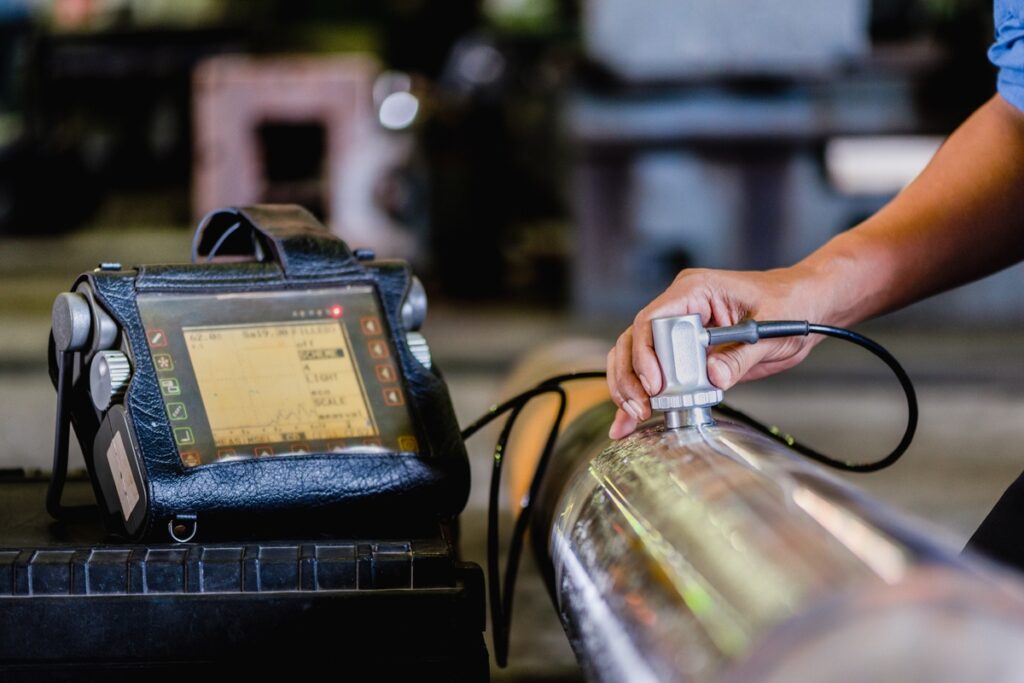
Ultrasonic testing (UT) is a type of nondestructive testing that uses high-frequency sound waves to detect internal defects or measure the thickness of materials. It is commonly used in industries such as manufacturing, construction, and transportation to ensure the integrity and safety of products and structures.
The UT process involves the use of a transducer, which generates and receives the ultrasonic waves. The transducer is typically made of piezoelectric material, which can convert electrical energy into mechanical energy (vibration) and vice versa. The transducer is placed in contact with the surface of the material being tested, and a high-frequency electrical signal is applied to it. This causes the transducer to vibrate and generate ultrasonic waves, which are transmitted into the material.
As the ultrasonic waves pass through the material, they are reflected by any internal defects or interfaces, such as changes in density or composition. These reflections are known as echoes, and they are detected by the transducer and converted back into an electrical signal. The time it takes for the ultrasonic waves to travel through the material and be reflected back to the transducer is measured, and this information is used to determine the location, size, and shape of the defects or interfaces.
In addition to detecting internal defects, UT can also be used to measure the thickness of materials. This is done by transmitting ultrasonic waves through the material and measuring the time it takes for the waves to travel through the material and be reflected back by the opposite surface. The thickness of the material can then be calculated based on the known speed of sound in the material and the measured time of flight.
There are several different types of UT methods, each of which is suited to different applications and materials. For example, pulse-echo UT is commonly used to detect defects in relatively thin materials, while through-transmission UT is used to detect defects in thicker or multi-layer materials. Phased array UT allows for the control of the direction, frequency, and intensity of the ultrasonic waves, and time of flight diffraction (TOFD) UT can be used to accurately determine the size and location of defects.
UT is a versatile and widely-used NDT method that provides many benefits over other testing methods. It is fast, accurate, and cost-effective, and it can be used to test a wide range of materials, including metals, plastics, ceramics, and composites. It is also a non-destructive method, meaning that it does not alter the physical or chemical properties of the material being tested. UT is typically performed by trained and certified inspectors who follow established procedures and standards to ensure the accuracy and reliability of the test results.
2. Radiographic Testing (RT)
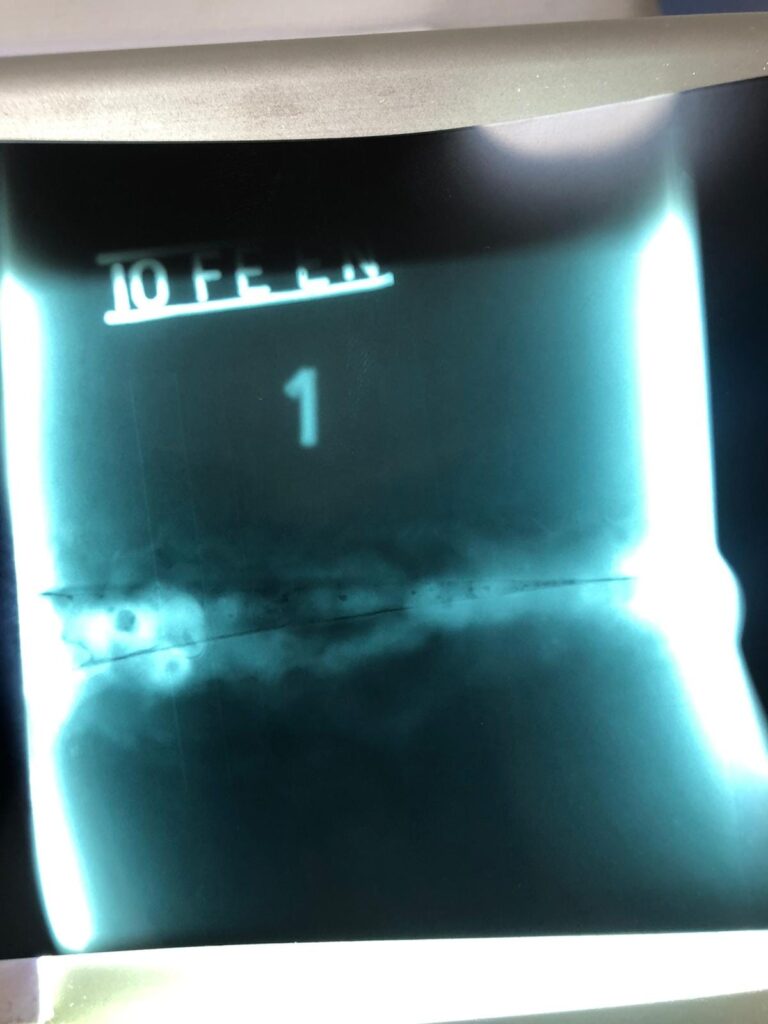
Radiographic testing (RT) is a type of nondestructive testing that uses X-rays or gamma rays to create an image of the internal structure of an object. This allows for the detection of internal defects or abnormalities that may not be visible with the naked eye. RT is commonly used in industries such as manufacturing, construction, and healthcare to ensure the safety and integrity of products and structures.
The RT process involves the use of a radiographic source, which produces the X-rays or gamma rays used to create the image. The source is typically a sealed tube or a radioactive isotope, and it is placed on one side of the object being tested. The intensity and energy of the radiation produced by the source is carefully controlled to ensure that it is suitable for the specific material and application.
On the opposite side of the object, a detector is used to capture the radiation that passes through the material. The detector may be a film-based system, where a radiation-sensitive film is used to record the image, or it may be a digital system, where a radiation-sensitive electronic detector is used to capture the image digitally. In either case, the resulting image is known as a radiograph.
The radiograph shows the internal structure of the object, and any defects or abnormalities will appear as variations in density or composition on the image. These variations can be analyzed by trained and certified RT inspectors to determine the type, size, and location of the defects or abnormalities. In addition to detecting defects, RT can also be used to measure the thickness of materials or to evaluate the internal geometry of an object.
There are several advantages to using RT as a NDT method. It is a fast and efficient way to inspect large or complex objects, and it can provide detailed information about the internal structure of an object. RT is also a non-destructive method, so it does not alter the physical or chemical properties of the material being tested. Additionally, RT can be used to test a wide range of materials, including metals, plastics, ceramics, and composites.
However, RT does have some limitations. It requires the use of ionizing radiation, which must be carefully controlled to ensure the safety of the operators and the surrounding environment. RT also requires specialized equipment and trained personnel to perform the testing and interpret the results, which can make it more expensive than some other NDT methods. Additionally, RT is not suitable for testing objects that are highly absorbent of radiation, such as lead or dense metals, as the radiation will not be able to pass through the material to create a useful image.
3. Magnetic Particle Testing (MPT)
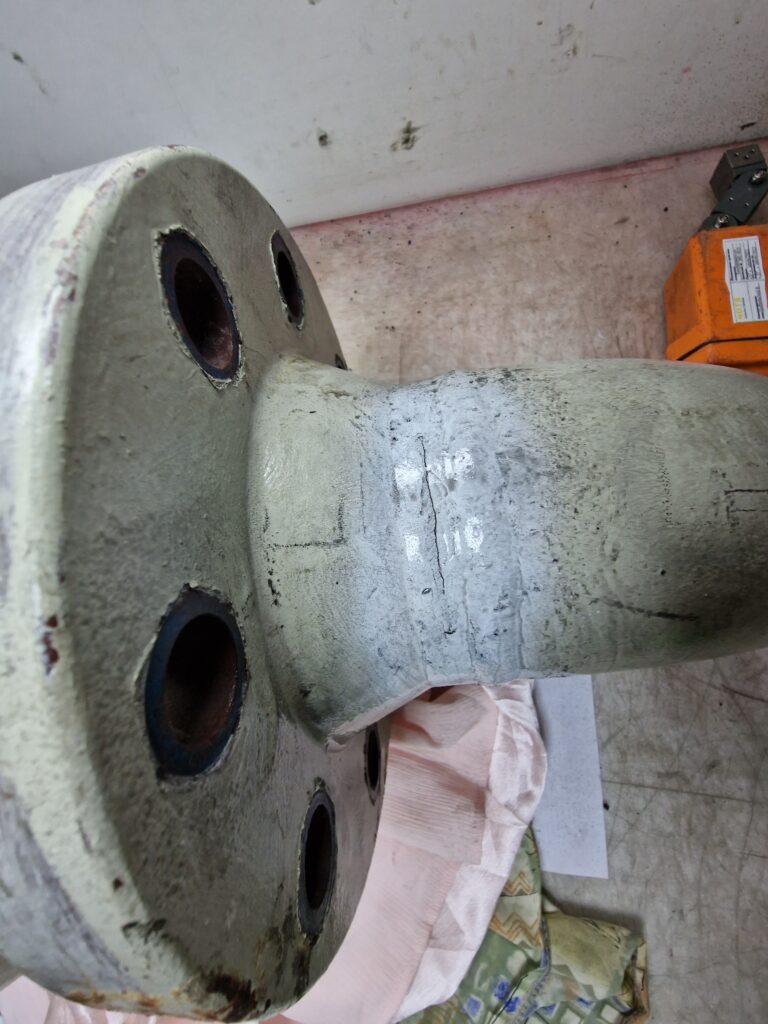
Magnetic particle testing (MPT) is a type of nondestructive testing that uses a magnetic field to detect surface or slightly subsurface discontinuities in ferromagnetic materials. It is commonly used in industries such as aerospace, automotive, and oil and gas to ensure the safety and integrity of materials and components.
The MPT process involves the use of a magnetizing force, which is typically produced by an electromagnet or a permanent magnet. The material being tested is placed in the magnetic field, and a current is passed through it. This creates a magnetic field within the material, which is then used to detect any discontinuities present on or near the surface.
To make the discontinuities visible, a magnetic particle suspension is applied to the surface of the material. The particles in the suspension are magnetic, and they are attracted to the areas of the material where the magnetic field is disrupted by the discontinuities. The particles will then gather at the discontinuities, forming a visible indication that can be easily seen by the inspector.
There are several types of MPT methods, each of which is suited to different applications and materials. For example, wet fluorescent MPT is commonly used to detect discontinuities on the surface of ferromagnetic materials, while dry powder MPT is used to detect discontinuities in ferromagnetic coatings. Alternating current MPT is used to detect very small or shallow discontinuities, and demagnetization MPT is used to remove residual magnetism from the material after testing.
MPT is a fast and effective way to detect surface-breaking defects in ferromagnetic materials. It is also a non-destructive method, so it does not alter the physical or chemical properties of the material being tested. In addition, MPT is relatively simple and inexpensive to perform, and it does not require specialized equipment.
However, MPT is not suitable for use on non-ferromagnetic materials, and it is not effective for detecting subsurface discontinuities or defects that are not aligned with the direction of the magnetic field.
4. Liquid Penetrant Testing (PT)
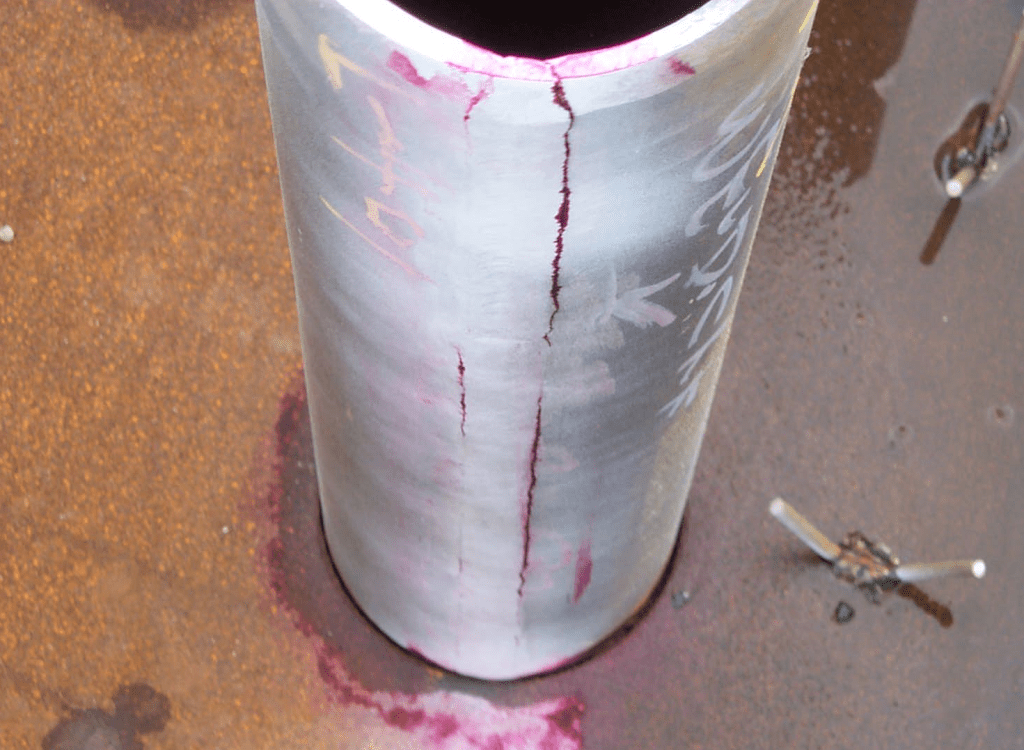
Liquid penetrant testing (PT) is a type of nondestructive testing that is used to detect surface-breaking defects in a wide range of materials. It is commonly used in industries such as aerospace, automotive, and petrochemical to ensure the safety and integrity of materials and components.
The PT process involves applying a liquid penetrant to the surface of the material being tested. The penetrant is typically a dye or a fluorescent solution that is applied to the surface and allowed to soak into any surface-breaking defects present. The excess penetrant is then removed from the surface, leaving the penetrant that has penetrated the defects behind.
The penetrant that remains on the surface is then made visible using a developer. The developer is typically a white or light-colored powder or liquid that is applied to the surface and absorbs the penetrant, making it visible to the inspector. The developer may be applied using a brush, a spray, or another method, depending on the specific application and the type of penetrant being used.
There are several types of PT methods, each of which is suited to different materials and applications. For example, visible dye penetrant testing is commonly used on ferrous materials, while fluorescent penetrant testing is used on non-ferrous materials. Solvent removable penetrant testing is used on materials that cannot be easily cleaned with water, and post-emulsifiable penetrant testing is used on materials that require a high level of sensitivity.
PT is a fast and effective way to detect surface-breaking defects in a wide range of materials. It is also a relatively simple and inexpensive method, and it does not require specialized equipment.
PT is also a non-destructive method, so it does not alter the physical or chemical properties of the material being tested. However, PT is not effective for detecting subsurface defects or defects that are not aligned with the direction of the penetrant flow. Additionally, PT may not be suitable for use on certain materials, such as porous or absorbent materials, as the penetrant may not be able to penetrate the defects effectively.
5. Visual Testing (VT)
Visual testing (VT) is a type of nondestructive testing that involves using the naked eye or a visual aid, such as a magnifying glass or borescope, to inspect the surface of an object for defects. It is commonly used in industries such as manufacturing, construction, and transportation to ensure the safety and integrity of products and structures.
The VT process involves carefully examining the surface of the object being tested to detect any visual indications of defects or abnormalities. The inspector may use the naked eye, a magnifying glass, or a borescope to perform the inspection, depending on the specific application and the type of defects being sought. A borescope is a small, flexible tube with a light and a camera at the end, which allows the inspector to see inside cavities or other areas that are not visible from the outside.
The inspector will typically follow a specific set of procedures and standards to ensure the accuracy and reliability of the VT inspection. This may include using a specific lighting setup, taking detailed notes and photographs, and following established acceptance criteria for the type and size of defects that are acceptable. The inspector may also use reference standards or other comparison objects to help with the inspection.
VT is a simple and cost-effective way to inspect the surface of an object for defects. It is also a non-destructive method, so it does not alter the physical or chemical properties of the material being tested. Additionally, VT can be performed by relatively untrained personnel, and it does not require specialized equipment. However, VT is limited by the inspector’s ability to detect defects, and it may not be suitable for detecting very small or subtle defects. VT is also not effective for detecting subsurface defects or defects that are not visible on the surface of the object.
6. Eddy Current Testing (ET)
Eddy current testing (ET) is a type of nondestructive testing that uses electromagnetic fields to detect surface and subsurface defects in conductive materials. It is commonly used in industries such as aerospace, automotive, and oil and gas to ensure the safety and integrity of materials and components.
The ET process involves the use of an eddy current probe, which is typically a coil of wire that is placed in close proximity to the surface of the material being tested. A high-frequency alternating current is passed through the coil, which generates an electromagnetic field around the coil. As the coil is moved over the surface of the material, the electromagnetic field is disrupted by any conductive defects present in the material.
The disruption of the electromagnetic field causes the flow of current within the material to be altered, creating small circulating currents, known as eddy currents, in the material. These eddy currents generate their own electromagnetic fields, which can be detected by the eddy current probe. The amplitude and phase of the eddy currents, as well as the resistance and inductance of the probe, are measured and analyzed to determine the location, size, and type of the defects present in the material.
There are several advantages to using ET as a NDT method. It is a fast and efficient way to inspect large or complex objects, and it can provide detailed information about the subsurface defects in a material. ET is also a non-destructive method, so it does not alter the physical or chemical properties of the material being tested. Additionally, ET can be used to test a wide range of conductive materials, including metals, alloys, and certain plastics.
However, ET does have some limitations. It is not suitable for use on non-conductive materials, such as ceramics or glass, as the electromagnetic fields will not be able to penetrate the material. ET is also sensitive to the electrical properties of the material being tested, so it may not be effective for materials with high levels of conductivity or magnetic permeability. Additionally, ET requires specialized equipment and trained personnel to perform the testing and interpret the results, which can make it more expensive than some other NDT methods.
7. Accoustic Emission Testing (AE)
Acoustic emission testing (AE) is a type of nondestructive testing that uses sensors to detect and locate the source of mechanical or acoustic activity, such as cracking or friction, within an object. It is commonly used in industries such as aerospace, oil and gas, and power generation to monitor the integrity and safety of materials and structures.
The AE process involves the use of sensors, which are typically piezoelectric transducers that are attached to the surface of the object being tested. The transducers convert the mechanical energy of the acoustic waves generated by the activity within the object into an electrical signal, which can be detected and analyzed by AE equipment. The equipment measures the amplitude, frequency, and time of arrival of the acoustic waves at each sensor, and this information is used to determine the location and nature of the activity within the object.
AE testing is typically performed in real-time, where the sensors are continuously monitored and any detected activity is immediately analyzed and reported. This allows for the early detection and diagnosis of potential problems, such as the development of cracks or corrosion, before they become serious or cause damage. AE testing can also be performed periodically, as a form of condition-based monitoring, to track the health and performance of materials and structures over time.
There are several advantages to using AE as a NDT method. AE is sensitive to a wide range of mechanical and acoustic activity, including micro-scale events that may not be detectable with other testing methods. In addition, AE can provide real-time monitoring and early warning of potential problems, allowing for timely intervention and preventative maintenance.
8. Phased Array Ultrasonics (PAUT)
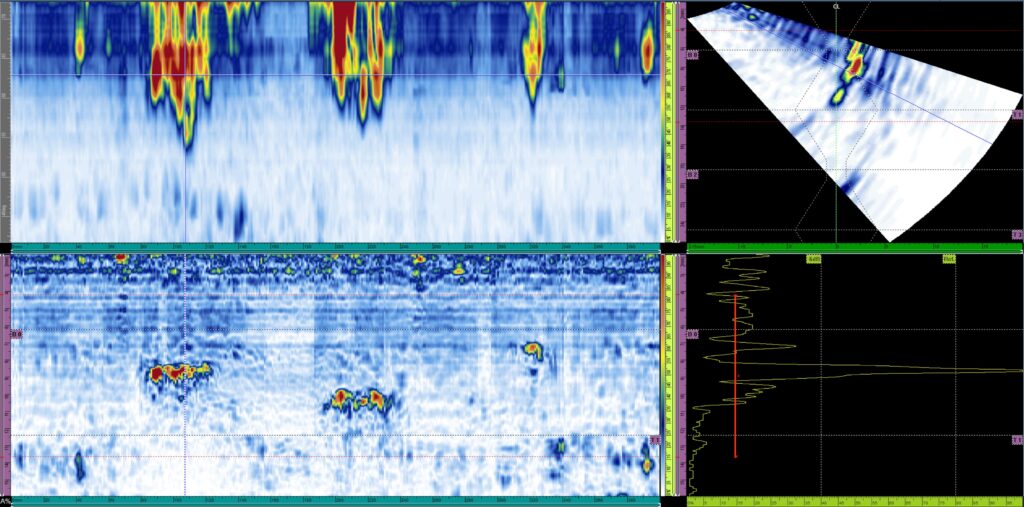
Phased array ultrasonics is a type of ultrasonic testing that uses multiple transducers to produce and control the ultrasonic waves that are used to inspect a material or component. The transducers are arranged in a specific pattern, and the sound waves are emitted at different phases, or times, to create a focused beam of sound. This allows the inspector to control the direction, frequency, and intensity of the ultrasonic waves, as well as the size and shape of the area being inspected.
The phased array ultrasonic testing process typically involves the use of a phased array ultrasonic instrument, which consists of a set of transducers, a beamformer, and a display or recording device. The transducers are attached to the surface of the material being tested, and they are energized by the beamformer to produce the ultrasonic waves. The beamformer controls the phase and amplitude of the ultrasonic waves at each transducer, allowing the inspector to steer and focus the ultrasonic beam.
As the ultrasonic beam passes through the material, it is reflected by any internal defects or interfaces, such as changes in density or composition. The reflected waves are detected by the transducers and converted back into an electrical signal, which is then processed by the beamformer and displayed or recorded by the instrument. The resulting image or data can be analyzed by the inspector to determine the location, size, and shape of the defects or interfaces within the material.
Phased array ultrasonics offers several advantages over other ultrasonic testing methods. It allows for the precise control of the ultrasonic beam, enabling the inspector to scan and inspect complex or hard-to-reach areas with greater accuracy and detail. It also allows for the rapid scanning of large areas, reducing the time and cost of the inspection.
9. Time of Flight Diffraction (ToFD)
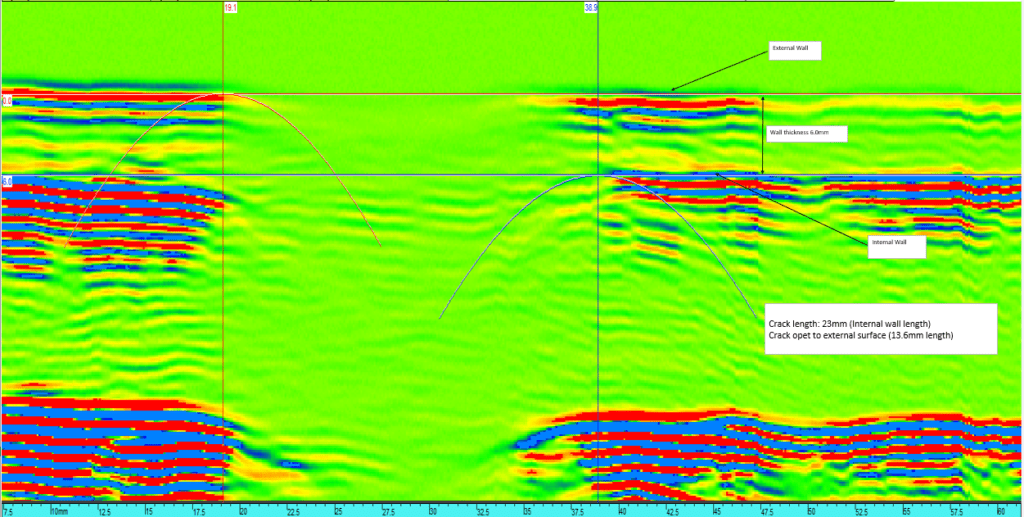
Time of flight diffraction (TOFD) is a type of ultrasonic testing that is used to detect and size defects in materials and components. It is commonly used in industries such as aerospace, oil and gas, and power generation to ensure the safety and integrity of materials and structures.
The TOFD process involves the use of two ultrasonic transducers, which are placed on opposite sides of the material being tested. The transducers are typically placed in a straight line, with one transducer at each end of the material, and they are used to transmit and receive ultrasonic waves. One transducer is used to transmit a pulse of ultrasonic energy into the material, while the other transducer is used to receive the reflected energy.
As the ultrasonic pulse travels through the material, it is reflected by any defects or interfaces present in the material. The reflected energy is received by the second transducer and converted into an electrical signal, which is then processed by the TOFD instrument. The TOFD instrument measures the time it takes for the ultrasonic pulse to travel from the transmitting transducer to the defect and back to the receiving transducer, known as the time of flight.
The time of flight is used to calculate the distance between the transducers and the defect, and this information is used to determine the location, size, and orientation of the defect. The resulting data is typically presented as a TOFD image, which shows the location and size of the defects in the material. The TOFD image can be analyzed by the inspector to evaluate the condition of the material and to identify any defects that may require repair or replacement.
TOFD offers several advantages over other ultrasonic testing methods. It is highly accurate and precise, allowing for the detection and sizing of small and shallow defects. It is also relatively fast and efficient, allowing for the rapid scanning of large areas. In addition, TOFD is a non-destructive method, so it does not alter the physical or chemical properties of the material being tested. However, TOFD requires specialized equipment and trained personnel to perform the testing and interpret the results, which can make it more expensive than some other NDT methods.
10. Hardness Testing (HT)
Hardness testing is a commonly used method for evaluating the hardness of materials. Hardness is a measure of a material’s resistance to indentation, penetration, or scratching, and it is an important property that affects the material’s performance and durability. Hardness testing is used to determine the hardness of a wide range of materials, including metals, ceramics, polymers, and composites, and it is an important tool for materials engineers and metallurgists.
It is performed using a variety of methods and instruments, depending on the type of material being tested and the desired level of accuracy. The most commonly used methods for hardness testing include Rockwell, Brinell, Vickers, and Shore. These methods use different types of indenters and loading mechanisms to apply a known force to the material, and the hardness of the material is determined by measuring the size of the indentation or the force required to cause the indentation.
The results of hardness testing are typically presented in the form of a hardness value, which is a numerical representation of the material’s resistance to indentation. The hardness value is typically expressed in a specific hardness scale, such as Rockwell, Brinell, or Vickers, and it is a relative measure of the material’s hardness compared to a reference standard. The hardness value can be used to evaluate the material’s performance and durability, and it can be used to compare the hardness of different materials.
Hardness testing is a widely used method for evaluating the properties of materials, and it is an important tool for materials engineers and metallurgists. It is a nondestructive method, so it does not alter the physical or chemical properties of the material being tested, and it provides valuable information on the material’s hardness and performance. Hardness testing is used in a variety of industries, including aerospace, automotive, and construction, and it is an essential tool for ensuring the quality and reliability of materials and components.
11. Internal Rotary Inspection (IRIS)
Internal rotary inspection, also known as internal rotary ultrasonic inspection or internal rotary UT, is a nondestructive testing (NDT) method that is used to detect and evaluate defects or abnormalities in the internal surfaces of pipes, tubes, and other cylindrical components. Internal rotary inspection is a specialized type of ultrasonic testing (UT) that uses a rotating transducer to generate and detect ultrasonic waves inside the material being inspected.
Internal rotary inspection is performed using a specialized inspection system that consists of a rotary transducer, a signal generator, and a data acquisition and analysis system. The rotary transducer is mounted on the end of a flexible drive shaft, which is inserted into the material being inspected through a small opening or opening. The transducer is rotated at a high speed, typically between 1500 and 5000 rpm, and it generates ultrasonic waves that are transmitted into the material.
The ultrasonic waves propagate through the material and are reflected by any defects or abnormalities on the internal surfaces of the material. The reflected waves are detected by the rotary transducer and are converted into electrical signals, which are then processed by the data acquisition and analysis system. The system uses specialized algorithms and software to analyze the signals and to detect and evaluate the defects or abnormalities in the material.
Internal rotary inspection is a highly sensitive and accurate method for detecting and evaluating defects in the internal surfaces of materials. It can detect a wide range of defects, including cracks, voids, inclusions, and other surface or subsurface anomalies. It can also be used to measure the thickness of the material, the distance to the defects, and the orientation of the defects. Internal rotary inspection is commonly used in industries such as aerospace, oil and gas, and power generation, where the safety and reliability of materials and components are critical.
12. Thermography (TH)
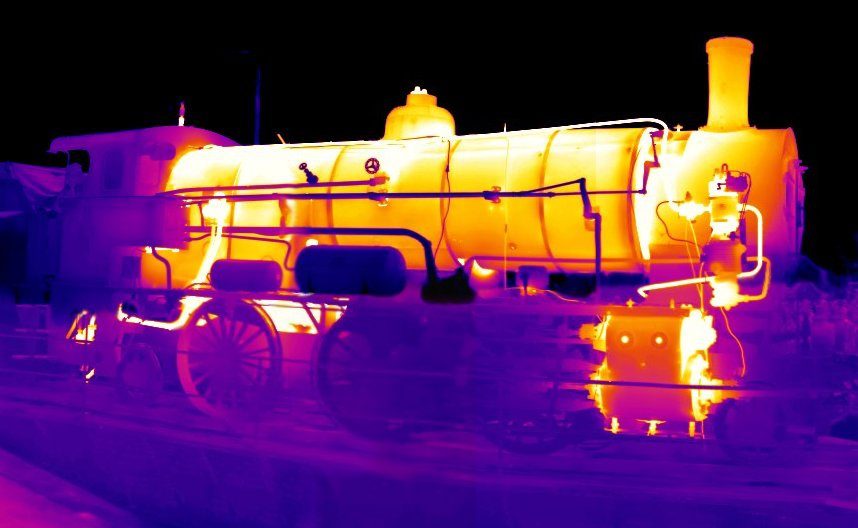
Thermography, also known as infrared thermography or thermal imaging, is a nondestructive testing (NDT) method that is used to detect and evaluate changes in temperature in materials or objects. Thermography is a passive imaging technique that uses specialized infrared cameras or sensors to measure the thermal radiation emitted by the materials or objects being inspected. The cameras or sensors are typically mounted on a tripod or other device, and they are pointed at the materials or objects being inspected.
Thermography is based on the principle that all materials and objects emit thermal radiation, which is a type of electromagnetic radiation that has a longer wavelength and lower frequency than visible light. The thermal radiation emitted by a material or object is determined by its temperature, and it increases with the temperature of the material or object. Infrared cameras or sensors are sensitive to thermal radiation, and they can detect and measure the thermal radiation emitted by materials or objects in the infrared spectrum.
The cameras or sensors used in thermography are typically equipped with specialized lenses, filters, and detectors that are optimized for the detection of thermal radiation in the infrared spectrum. They are also equipped with specialized software and algorithms that are used to convert the detected thermal radiation into images or data that can be interpreted and analyzed by the operator. The images or data produced by the cameras or sensors are typically presented in the form of grayscale or color-coded maps that show the temperature distribution across the materials or objects being inspected.
Thermography is a versatile and effective NDT method that is used in a wide variety of applications. It is commonly used to detect and evaluate changes in temperature in materials or objects that are difficult or impossible to access directly, such as electrical components, mechanical assemblies, or structures. It is also used to detect and diagnose thermal anomalies or defects in materials or objects, such as overheating, corrosion, or moisture ingress. Thermography is widely used in industries such as aerospace, automotive, and power generation, where the safety and reliability of materials and components are critical.
NDT Industry Use
Oil and Gas Sector
NDT, or nondestructive testing, is commonly used in the oil and gas industry to ensure the safety and integrity of materials and components used in exploration, production, and transportation. The oil and gas industry is a highly complex and critical sector, and it relies on a wide range of materials and components that must operate reliably and safely in challenging environments. NDT is used to inspect these materials and components for defects or abnormalities that could affect their performance or cause failures or accidents.
NDT is used in the oil and gas industry to inspect a wide range of materials and components, including pipes, fittings, valves, tanks, vessels, pressure vessels, and structural components. These materials and components are subject to a variety of stresses and conditions, such as high temperatures, high pressures, corrosive environments, and mechanical loads, and NDT is used to detect and evaluate any defects or abnormalities that may affect their performance or safety.
The most commonly used NDT methods in the oil and gas industry include ultrasonic testing, radiographic testing, magnetic particle testing, liquid penetrant testing, and visual testing. These methods are used to detect and evaluate a wide range of defects, including cracks, corrosion, inclusions, voids, and other surface or subsurface anomalies. The NDT methods are performed by trained and certified inspectors who follow established procedures and standards to ensure the accuracy and reliability of the testing.
The results of the NDT are typically presented in the form of images, data, or reports, which are analyzed and interpreted by the inspector to determine the condition of the material or component and any necessary repairs or actions. The NDT results are used to evaluate the safety and performance of the materials and components, and they are used to identify potential problems before they cause failures or accidents. This allows for timely intervention and preventative maintenance, which can help to reduce the risk of failures or accidents and improve the overall safety and reliability of the oil and gas industry.
Power Generation Sector
NDT is commonly used in the power generation industry to ensure the safety and integrity of materials and components used in power plants. The power generation industry is a critical sector, and it relies on a wide range of materials and components that must operate reliably and safely to generate electricity. NDT is used to inspect these materials and components for defects or abnormalities that could affect their performance or cause failures or accidents.
NDT is used in the power generation industry to inspect a wide range of materials and components, including boilers, turbines, generators, pipes, fittings, valves, tanks, vessels, and structural components. These materials and components are subject to a variety of stresses and conditions, such as high temperatures, high pressures, corrosive environments, and mechanical loads, and NDT is used to detect and evaluate any defects or abnormalities that may affect their performance or safety.
The most commonly used NDT methods in the power generation industry include ultrasonic testing, radiographic testing, magnetic particle testing, liquid penetrant testing, and visual testing. These methods are used to detect and evaluate a wide range of defects, including cracks, corrosion, inclusions, voids, and other surface or subsurface anomalies. The NDT methods are performed by trained and certified inspectors who follow established procedures and standards to ensure the accuracy and reliability of the testing.
The results of the NDT are typically presented in the form of images, data, or reports, which are analyzed and interpreted by the inspector to determine the condition of the material or component and any necessary repairs or actions. The NDT results are used to evaluate the safety and performance of the materials and components, and they are used to identify potential problems before they cause failures or accidents. This allows for timely intervention and preventative maintenance, which can help to reduce the risk of failures or accidents and improve the overall safety and reliability of the power generation industry.
Aerospace Sector
NDT is commonly used in the aerospace industry to ensure the safety and integrity of materials and components used in aircraft and spacecraft. The aerospace industry is a highly complex and critical sector, and it relies on a wide range of materials and components that must operate reliably and safely in challenging environments. NDT is used to inspect these materials and components for defects or abnormalities that could affect their performance or cause failures or accidents.
NDT is used in the aerospace industry to inspect a wide range of materials and components, including fuselages, wings, engines, propulsion systems, avionics, and structural components. These materials and components are subject to a variety of stresses and conditions, such as high temperatures, high pressures, extreme loads, and corrosive environments, and NDT is used to detect and evaluate any defects or abnormalities that may affect their performance or safety.
The most commonly used NDT methods in the aerospace industry include ultrasonic testing, radiographic testing, magnetic particle testing, liquid penetrant testing, and visual testing. These methods are used to detect and evaluate a wide range of defects, including cracks, corrosion, inclusions, voids, and other surface or subsurface anomalies. The NDT methods are performed by trained and certified inspectors who follow established procedures and standards to ensure the accuracy and reliability of the testing.
The results of the NDT are typically presented in the form of images, data, or reports, which are analyzed and interpreted by the inspector to determine the condition of the material or component and any necessary repairs or actions.
Chemical Sector
NDT is commonly used in the chemical industry to ensure the safety and integrity of materials and components used in the production, processing, and transportation of chemicals. The chemical industry is a complex and critical sector, and it relies on a wide range of materials and components that must operate reliably and safely in challenging environments. NDT is used to inspect these materials and components for defects or abnormalities that could affect their performance or cause failures or accidents.
NDT is used in the chemical industry to inspect a wide range of materials and components, including pipes, fittings, valves, tanks, vessels, reactors, and structural components. These materials and components are subject to a variety of stresses and conditions, such as high temperatures, high pressures, corrosive environments, and mechanical loads, and NDT is used to detect and evaluate any defects or abnormalities that may affect their performance or safety.
The most commonly used NDT methods in the chemical industry include ultrasonic testing, radiographic testing, magnetic particle testing, liquid penetrant testing, and visual testing. These methods are used to detect and evaluate a wide range of defects, including cracks, corrosion, inclusions, voids, and other surface or subsurface anomalies. The NDT methods are performed by trained and certified inspectors who follow established procedures and standards to ensure the accuracy and reliability of the testing.
The results of the NDT are typically presented in the form of images, data, or reports, which are analyzed and interpreted by the inspector to determine the condition of the material or component and any necessary repairs or actions. The NDT results are used to evaluate the safety and performance of the materials and components, and they are used to identify potential problems before they cause failures or accidents. This allows for timely intervention and preventative maintenance, which can help to reduce the risk of failures or accidents and improve the overall safety and reliability of the chemical industry.
NDT offers several advantages to the chemical industry. It is a non-destructive method, so it does not alter the physical or chemical properties of the materials and components being tested.
Nuclear Sector
Nondestructive testing is commonly used in the nuclear industry to ensure the safety and integrity of materials and components used in nuclear power plants. The nuclear industry is a critical sector, and it relies on a wide range of materials and components that must operate reliably and safely to generate electricity. NDT is used to inspect these materials and components for defects or abnormalities that could affect their performance or cause failures or accidents.
NDT is used in the nuclear industry to inspect a wide range of materials and components, including reactors, fuel rods, piping, vessels, and structural components. These materials and components are subject to a variety of stresses and conditions, such as high temperatures, high pressures, corrosive environments, and mechanical loads, and NDT is used to detect and evaluate any defects or abnormalities that may affect their performance or safety.
The most commonly used NDT methods in the nuclear industry include ultrasonic testing, radiographic testing, magnetic particle testing, liquid penetrant testing, and visual testing. These methods are used to detect and evaluate a wide range of defects, including cracks, corrosion, inclusions, voids, and other surface or subsurface anomalies. The NDT methods are performed by trained and certified inspectors who follow established procedures and standards to ensure the accuracy and reliability of the testing.
The results of the NDT are typically presented in the form of images, data, or reports, which are analyzed and interpreted by the inspector to determine the condition of the material or component and any necessary repairs or actions. The NDT results are used to evaluate the safety and performance of the materials and components, and they are used to identify potential problems before they cause failures or accidents.
NDT Technician and Inspector Training and Certification
NDT is a specialized field that requires specialized training and certification. NDT training and certification programs are designed to provide individuals with the knowledge and skills needed to perform NDT and interpret the results of the testing. NDT training programs are typically offered by educational institutions, technical schools, and professional organizations, and they are typically structured as formal courses or workshops that include both theoretical and practical components.
NDT training programs typically cover a wide range of topics, including the principles of NDT, the various NDT methods and techniques, the selection and use of NDT equipment, the interpretation of NDT results, and the application of NDT to specific industries and materials. The programs may also include hands-on training and practical exercises to allow students to gain experience in the use of NDT equipment and techniques.
NDT certification programs are designed to assess the knowledge and skills of individuals who have completed NDT training programs. The certification programs typically consist of written and practical exams, which are administered by certification bodies or professional organizations. The exams are designed to evaluate the individual’s understanding of the principles and techniques of NDT, as well as their ability to perform and interpret the results of NDT.
NDT certification is typically voluntary, but it is highly recommended for individuals who wish to pursue careers in NDT or who wish to work in industries that require NDT. NDT certification is often a requirement for employment in certain industries, such as aerospace, power generation, and oil and gas, and it is often a requirement for individuals who wish to work as NDT inspectors or technicians. NDT certification is also a way for individuals to demonstrate their knowledge and skills in NDT, and it can help them to advance their careers and enhance their professional opportunities.
There are 3 NDT certification levels.
NDT Level I
NDT level I is the entry-level certification for individuals who wish to work in the field of nondestructive testing (NDT). NDT level I certification is typically the first step in the NDT certification process, and it is designed to assess the individual’s basic knowledge and skills in NDT. NDT level I certification is typically required for individuals who wish to work as NDT technicians or assistants, and it is a prerequisite for individuals who wish to pursue higher levels of NDT certification.
NDT level I certification is typically obtained by completing an NDT training program and passing a written and practical exam. The training program is typically structured as a course or workshop that covers the basic principles and techniques of NDT, as well as the selection and use of NDT equipment. The program may also include hands-on training and practical exercises to allow students to gain experience in the use of NDT equipment and techniques.
The written and practical exams for NDT level I certification are typically administered by a certification body or professional organization. The exams are designed to evaluate the individual’s understanding of the principles and techniques of NDT, as well as their ability to perform and interpret the results of NDT. The exams may include multiple-choice and practical questions, and they may be conducted in a classroom or laboratory setting.
NDT level I certification is typically valid for a specific period of time, and it may require renewal through additional training or continuing education. The specific requirements for NDT level I certification vary depending on the certification body or organization, and individuals should consult the appropriate certification body for more information on the requirements and process for obtaining NDT level I certification.
NDT level I certification is an important credential for individuals who wish to work in the field of NDT. It demonstrates the individual’s basic knowledge and skills in NDT, and it is often a requirement for employment in industries that use NDT. NDT level I certification can also be a stepping stone to higher levels of NDT certification and more advanced career opportunities in the NDT field.
NDT Level II
NDT level II is the intermediate level of certification for individuals who work in the field of nondestructive testing (NDT). NDT level II certification is designed to assess the individual’s advanced knowledge and skills in NDT, and it is typically required for individuals who wish to work as NDT inspectors or supervisors. NDT level II certification is typically obtained by individuals who have already obtained NDT level I certification and who have gained additional experience and training in NDT.
NDT level II certification is typically obtained by completing an NDT training program and passing a written and practical exam. The training program is typically structured as a course or workshop that covers advanced topics in NDT, such as advanced NDT methods and techniques, the interpretation of NDT results, and the application of NDT to specific industries and materials. The program may also include hands-on training and practical exercises to allow students to gain experience in the use of advanced NDT equipment and techniques.
The written and practical exams for NDT level II certification are typically administered by a certification body or professional organization. The exams are designed to evaluate the individual’s advanced understanding of the principles and techniques of NDT, as well as their ability to perform and interpret the results of NDT. The exams may include multiple-choice and practical questions, and they may be conducted in a classroom or laboratory setting.
NDT level II certification is typically valid for a specific period of time, and it may require renewal through additional training or continuing education. The specific requirements for NDT level II certification vary depending on the certification body or organization, and individuals should consult the appropriate certification body for more information on the requirements and process for obtaining NDT level II certification.
NDT level II certification is an important credential for individuals who work in the field of NDT. It demonstrates the individual’s advanced knowledge and skills in NDT, and it is often a requirement for employment as an NDT inspector or supervisor. NDT level II certification can also be a stepping stone to higher levels of NDT certification and more advanced career opportunities in the NDT field.
NDT Level III
NDT level III is the highest level of certification for individuals who work in the field of nondestructive testing (NDT). NDT level III certification is designed to assess the individual’s expertise and leadership skills in NDT, and it is typically required for individuals who wish to work as NDT managers or executives. NDT level III certification is typically obtained by individuals who have already obtained NDT level I and II certification and who have gained extensive experience and training in NDT.
NDT level III certification is typically obtained by completing an NDT training program and passing a written and practical exam. The training program is typically structured as a course or workshop that covers advanced topics in NDT, such as advanced NDT methods and techniques, the interpretation of NDT results, and the application of NDT to specific industries and materials. The program may also include hands-on training and practical exercises to allow students to gain experience in the use of advanced NDT equipment and techniques.
The written and practical exams for NDT level III certification are typically administered by a certification body or professional organization. The exams are designed to evaluate the individual’s expertise and leadership skills in NDT, as well as their ability to perform and interpret the results of NDT. The exams may include multiple-choice and practical questions, and they may be conducted in a classroom or laboratory setting.
NDT level III certification is typically valid for a specific period of time, and it may require renewal through additional training or continuing education. The specific requirements for NDT level III certification vary depending on the certification body or organization, and individuals should consult the appropriate certification body for more information on the requirements and process for obtaining NDT level III certification.
NDT level III certification is an important credential for individuals who work in the field of NDT. It demonstrates the individual’s expertise and leadership skills in NDT, and it is often a requirement for employment as an NDT manager or executive. NDT level III certification can also be a stepping stone to advanced career opportunities and leadership roles in the NDT field.
Pressure Vessel Inspector
Pressure vessel inspector training and certification is a program that is designed to provide individuals with the knowledge and skills necessary to inspect and evaluate pressure vessels. Pressure vessels are specialized containers that are designed to hold fluids or gases at high pressure, and they are used in a wide range of industrial and commercial applications. Pressure vessels are subject to strict safety regulations, and they must be inspected regularly to ensure that they are operating safely and in compliance with the regulations.
Pressure vessel inspector training and certification programs are typically offered by technical schools, colleges, universities, or professional organizations that specialize in nondestructive testing (NDT) or materials engineering. The programs typically include classroom instruction, laboratory or hands-on training, and practical exercises that are designed to provide students with a comprehensive understanding of pressure vessels and their inspection requirements. The programs may also include internships or field experiences that allow students to gain practical experience in pressure vessel inspection.
The specific content and duration of pressure vessel inspector training and certification programs vary depending on the institution or organization offering the program. However, most programs cover a range of topics, including pressure vessel design and construction, pressure vessel codes and standards, inspection techniques and methods, and data analysis and reporting. The programs may also include training in specific NDT methods and techniques, such as ultrasonic testing, radiographic testing, or magnetic particle testing, that are commonly used in pressure vessel inspection.
Pressure vessel inspector training and certification programs typically culminate in a written and practical exam that is administered by a certification body or professional organization. The exams are designed to evaluate the individual’s knowledge and skills in pressure vessel inspection, and they may include multiple-choice and practical questions. Successful completion of the exams is typically required for individuals who wish to obtain pressure vessel inspector certification or other professional credentials in the field of NDT.
Pressure vessel inspector training and certification is an important step for individuals who wish to work as pressure vessel inspectors. The training and certification provide the knowledge and skills necessary to perform pressure vessel inspections safely and effectively, and they are often required by employers and regulatory bodies. Pressure vessel inspector certification can also be a valuable asset for individuals who wish to advance their careers in the NDT field or to pursue other opportunities in the pressure vessel industry.
Pipeline Inspector
A pipeline inspector is a professional who is responsible for inspecting pipelines to ensure that they are operating safely and in compliance with regulatory requirements. Pipeline inspectors typically have a background in engineering, materials science, or nondestructive testing (NDT), and they are trained to use specialized tools and techniques to evaluate the condition of pipelines and identify any defects or abnormalities. Pipeline inspectors may work for pipeline operators, engineering firms, government agencies, or other organizations that are involved in the design, construction, operation, or maintenance of pipelines.
Pipeline inspector training is a program that is designed to provide individuals with the knowledge and skills necessary to perform pipeline inspections safely and effectively. Pipeline inspector training programs are typically offered by technical schools, colleges, universities, or professional organizations that specialize in NDT or materials engineering. The programs typically include classroom instruction, laboratory or hands-on training, and practical exercises that are designed to provide students with a comprehensive understanding of pipelines and their inspection requirements. The programs may also include internships or field experiences that allow students to gain practical experience in pipeline inspection.
The specific content and duration of pipeline inspector training programs vary depending on the institution or organization offering the program. However, most programs cover a range of topics, including pipeline design and construction, pipeline codes and standards, inspection techniques and methods, and data analysis and reporting. The programs may also include training in specific NDT methods and techniques, such as ultrasonic testing, radiographic testing, or magnetic particle testing, that are commonly used in pipeline inspection.
Pipeline inspector training programs typically culminate in a written and practical exam that is administered by a certification body or professional organization. The exams are designed to evaluate the individual’s knowledge and skills in pipeline inspection, and they may include multiple-choice and practical questions. Successful completion of the exams is typically required for individuals who wish to obtain pipeline inspector certification or other professional credentials in the field of NDT.
Pipeline inspector training and certification is an important step for individuals who wish to work as pipeline inspectors. The training and certification provide the knowledge and skills necessary to perform pipeline inspections safely and effectively, and they are often required by employers and regulatory bodies. Pipeline inspector certification can also be a valuable asset for individuals who wish to advance their careers in the NDT field or to pursue other opportunities in the pipeline industry.
Welding Inspector
A welding inspector is a professional who is responsible for inspecting welds to ensure that they are of high quality and meet the specified requirements. Welding inspectors typically have a background in engineering, metallurgy, or nondestructive testing (NDT), and they are trained to use specialized tools and techniques to evaluate the condition of welds and identify any defects or abnormalities. Welding inspectors may work for welding contractors, engineering firms, government agencies, or other organizations that are involved in the design, construction, operation, or maintenance of welded structures.
Welding inspector training is a program that is designed to provide individuals with the knowledge and skills necessary to perform welding inspections safely and effectively. Welding inspector training programs are typically offered by technical schools, colleges, universities, or professional organizations that specialize in NDT or materials engineering. The programs typically include classroom instruction, laboratory or hands-on training, and practical exercises that are designed to provide students with a comprehensive understanding of welding and welding inspection. The programs may also include internships or field experiences that allow students to gain practical experience in welding inspection.
The specific content and duration of welding inspector training programs vary depending on the institution or organization offering the program. However, most programs cover a range of topics, including welding processes and procedures, welding codes and standards, inspection techniques and methods, and data analysis and reporting. The programs may also include training in specific NDT methods and techniques, such as ultrasonic testing, radiographic testing, or magnetic particle testing, that are commonly used in welding inspection.
Welding inspector training programs typically culminate in a written and practical exam that is administered by a certification body or professional organization. The exams are designed to evaluate the individual’s knowledge and skills in welding inspection, and they may include multiple-choice and practical questions. Successful completion of the exams is typically required for individuals who wish to obtain welding inspector certification or other professional credentials in the field of NDT.
Welding inspector training and certification is an important step for individuals who wish to work as welding inspectors. The training and certification provide the knowledge and skills necessary to perform welding inspections safely and effectively, and they are often required by employers and regulatory bodies. Welding inspector certification can also be a valuable asset for individuals who wish to advance their careers in the NDT field or to pursue other opportunities in the welding industry.
WORLDWIDE NDT INSTITUTIONS AND SOCIETIES
Argentina
AAENDE
Asociación Argentina de Ensayos No Destructivos y, structurales, Altolaguirre 1674, CP C1431ECF Ciudad de Buenos Aires
Brazil
ABENDI
Associação Brasileira de Ensaios Não Destrutivos e Inspeção, Avenida Onze de Junho, 1.317, Vila Clementino, 04041-054 São Paulo-SP
Colombia
ACOSEND
Asociación Colombiana de Soldadura y Ensayos No Destructivos, Carrera 16 No. 57 – 22, Piso 2., Bogotá D.C.
Spain
AEND
Associacion Española de END, Calle Bocangel, 28 – 2° izda, E-28028 Madrid
Uruguay
AENDUR
Asociaciòn Uruguaya de Ensayos No Destructivos, Plaza Independencia, 812 piso 2, 11100 Montevideo
Australia
AINDT
Australian Institute for NDT, PO Box 52, Parkville, 3052 Victoria
Italy
AIPnD
Italian Society for NDT, Via A Foresti 5, 25127 Brescia
US
American Society for Nondestructive Testing (ASNT)
The American Society for Nondestructive Testing, Inc. (ASNT) is the world’s largest technical society for nondestructive testing (NDT) professionals.
Moldova
AN NTD
National Society on NDT and Technical Diagnostics, 20 Meshterul Manole St, MD-2044 Kishinev
Romania
ARoENd
Romanian Association of NDT, 7 Soldanului St, Bloc 137, Sc A, Apt 4, Sector 4, CP 41-126 Bucharest Sector 1 042042 Bucharest
US
ASM International
Membership, career and technical information from the American Society of Metals
Venezuela
ASOVEND
Associacion Venezolana de Ensayos No Destructivos, Escuela de Ingeniería Metalurgica, Facultad de Ingeniería, Ciudad Universitaria (UCV), Entrada del Clínico, Paseo Los Ilustres, nivel Mezzanina, Caracas, Apatado Postal 47533
Australia
Australian Institute of NDT
Membership, events and general information from the Australian Institute of NDT
Indonesia
AUTRI
Indonesian Society for NDT (Asosiasi Uji Tak Rusak Indonesia)
c/o PATIR-BATAN, Jalan Lebak Bulus Raya 49, Pasar Jumat, 12440 Jakarta
Germany
BAM – Federal Institute of Materials Research and Testing, Germany
Federal Institute for Materials Research and Testing
Belarus
BANDT
Belarusian Association for NDT and Technical Diagnostic, Akademicheskaya 16, 220072 Minsk
Belgium
BANT
Belgian Association for NDT, Rue Lonhienne 14, B-4870 Trooz
Bulgaria
BGSNDT
Bulgarian Association for NDT, 6 Boncher Str, Bl 4 off 502, 113 Sofia
Bosnia and Herzegovina
Bosnian and Herzegovinan Society for NDT
Tvomicka 3, 71000 Sarajevo-Ilidza, BiH
UK
British Institute of Non-Destructive Testing
Organisation, membership, publications, events and employment opportunities
UK
British Society for Strain Measurement
Organisation, membership, training, diary, articles
Bangladesh
BSNDT
Bangladesh Society for NDT, c/o NDT Division, Atomic Energy Centre, 4 Kazi Nazrul Islam Avenue, Ramna, 1000 Dhaka
Canada
Canadian Institute for NDE
Code of Ethics, Executive and Board Directors, Members, Membership,Scholarship opportunities, the CSNDT Journal and Events
China
ChSNDT
Chinese Society for NDT, Floor 6, No 100 Huihe Road, 200437 Shanghai
Canada
CINDE
Canadian Institute for NDE, 135 Fennell Avenue West, Hamilton, L8N 3T2 Ontario
Czech Republic
CNDT
Czech Society for NDT, Technickà 2, CZ 616 69 Brno
France
COFREND
The French Institute of Non-Destructive Testing provides information, certification and regional groups.
Tunisia
COTEND
Tunisian Committee for NDT c/o CETIME, Z I Ksar Said, 2086 Douar Hicher Manouba
Croatia
CrSNDT
Croatian Society for NDT, Berislaviċeva 6, HR-10000 Zagreb
Algeria
CSC / FALEND
Centre de Recherche Scientifique et Technique en Soudage en Controle / Federation Algerienne des Essais Non Destructif, Route de Dely Ibrahim, BP64 Cheraga
Denmark
Danish Society for NDT
Park alle 345, DK-2605 Brøndby
Germany
DGZfP
German Society of Non-Destructive Testing (DGZfP)
Egypt
Egyptian Society for Industrial Inspection
3a Moaskar Romany Street, Rushdy, Alexandria
UK
Engineering Council
The Engineering Council is the UK regulatory body for the engineering profession. We hold the national registers of 222,000 Engineering Technicians (EngTech), Incorporated Engineers (IEng), Chartered Engineers (CEng) and Information and Communications Technology Technicians (ICTTech).
UK
Engineering UK
EngineeringUK is a not for profit organisation, which works in partnership with the engineering Community, forums and resources to promote the vital role of engineers and engineering to society.
Ecuador
ESPOL
Escuela Politecnica del Litoral, PO Box 09-01-5863, Guayaquil
Europe
European Federation for NDT
A Europe-wide partnership to promote NDT and related fields for the benefit of industry, the professions, users and the wider Community, forums and resources
Finland
Finnish NDT Society
c/o Inspecta, PO Box 94, FI-02151 Espoo
Sweden
FOP
Swedish Society for NDT (Föreningen för Oförstörande Provning), c/o CSM NDT Certification AB, Artilleriplan 4, S 691 50 Karlskoga
Greece
HSNT
Hellenic Society of NDT, PO Box 64066, Zographou, 15710 Athens
Global
ICNDT
ICNDT is a non-profit organisation devoted to the international development of the science and practice of Non-Destructive Testing in conjunction with individual NDT Societies and recognised continental grouping of NDT Societies.
Mexico
IMENDE
Instituto Mexicano De Ensayos No Destructivos A.C., Ruben M Campos no 2651, Colonia Villa de Cortes, Delegacion Benito Juarez, CP 03530 Mexico D.F.
UK
Institute of Acoustics
The UK’s professional body for those working in Acoustics, Noise and Vibration.
UK
Institute of Plant Engineers
Professional body for engineers having an interest in the specification,installation, operation, maintenance and inspection of industrial and mobile plant
Lebanon
IRI
Industrial Research Institute, IRI Building, Lebanese University Campus, Hadath (Baabda)
Iran
IRNDT
Iranian Society for Nondestructive Testing, Room 227, 2nd Floor, Allameh Univ. Bldg., Aban St. North, Karimkhan-e-Zand Ave, Tehran
India
ISNT
Indian Society for Non-Destructive Testing, Modules 60 & 61, 3rd Floor, Garmant Complex, SIDCO Industrial Estate, Giundy, 600032 Chennai, Tamilnadu
Israel
ISRANDT
The ISRANDT – Israeli National Society – was established in 1998. It is an associated member of the European Federation for NDT and a member of ICNDT
Japan
JSNDI
Japanese Society for Non-Destructive Inspection, MBR 99 Bldg, 4th Floor, 67 Kanda-Sakumagashi, Chiyoda-ku, 101-0026 Tokyo
Netherlands
KINT
Nederlandse Vereniging voor Kwaliteitstoezicht, Inspectie en Niet-destructieve Techniek, PO Box 134, 3220 AC Hellevoetsluis
Korea
KSNT
Korean Society for Nondestructive Testing, 635-4, Yeoksam-dong, KOFST Center Suite 710, Gangnam-gu, 137-703 Seoul
Latvia
Latvian NDT Scoiety
Vesetas 10-18, LV-1013 Riga
Lithuania
LNBD
Lithuanian Society for NDT and Technical Diagnostics, Studentu st 50, LT-51368 Kaunas
Hungary
MAROVISZ
Hungarian Association for NDT, 8-10 Varrogepgyar Str, H-1211 Budapest
Mongolia
MSNDT
Mongolian Society for NDT, MTU Campus-2, Room X302, Sukhbaatar Duureg, PO Box 46/943, Ulaan Baatar
Malaysia
MSNT
Malaysian Society of NDT, c/o Malaysian Nuclear Agency, Kompleks Puspati, Bangi, 43000 Kajang
Global
NACE International
Society of Corrosion Engineers
Costa Rica
National Committee for NDT
c/o Inst Tec Costa Rica, Apartado 159, Cartago
Kenya
NDTK
Non-Destructive Testing Society of Kenya, PO Box 34284, 00-100 Nairobi
Singapore
NDTSS
Non-Destructive Testing Society (Singapore), #02-02, 21 Woodlands Industrial Park E1, 757 720 Singapore
Nigeria
Nigerian Society for NDT
c/o Gammatec, Portharcourt
Kazakhstan
Non-Destructive Testing and Technical Diagnostic Association
Republic of Kazakhstan, Saryarka 37, 010000 Аstana
Norway
NSNDT
Norwegian NDT Society, NDT-foreningen, Postboks 76, N-1378 Nesbru
New Zealand
NZNDTA
New Zealand Nondestructive Testing Association Inc, c/o HERA House, PO Box 76134 Manukau City, Auckland
Austria
ÖGfZP
Austrian Society for NDT, Krugerstrasse 16, A1010 Wien
Pakistan
PASNT
Pakistan Society for NDT, c/o National Centre for NDT (NCNDT), Plot No 234, Street 7, Sector I-9/2, Industrial Area, PO Box No 1781, Islamabad
Philippines
PSNDT
Philippine Society for Nondestructive Testing Inc, c/o Philippine Nuclear Research Institute, Commonwealth Avenue, Diliman, Quezon City
Poland
PTBNIDT / SIMP
Polish Society for NDT and Technical Diagnostics, wietokrzyska 14a, 00-050 Warsaw
UK
RCNDE
EPSRC-sponsored collaboration between industry and academia to coordinate research intoNDE technologies, and to ensure research topics are relevant to the medium to longer-term needs of industry.
Portugal
RELACRE
Associação de Laboratórios Acreditados de Portugal, Estrada do Paço do Lumiar, Campus do Lumiar – Edificio D, 1º Andar, 1649-038 Lisboa
Russian Federation
RSNTTD
The Russian Society for NDT and Technical Diagnostics, 35 Usacheva str bld 1, 119048 Moscow
South Africa
SAINT
South African Institute for NDT, PO Box 76068, 0040 Lynnwood Ridge
Serbia
SDIBR
Serbian Society for NDT, Grcica Milenka 67, 11000 Belgrade
Switzerland
SGZP / SSNT
Schweizerische Gesellschaft für Zerstörungsfreie Prüfung (Swiss Society for Nondestructive Testing), Dübendorf, CH-8600
Sri Lanka
SNDT
Society for Non Destructive Testing, Sri Lanka, c/o Atomic Energy Authority – 343, Lanka Tractors Ltd Bldg, Baseline Raod, 60/460 Orugodawatta
Taiwan
SNTCT
Nondestructive Testing Society of China-Taipei, 130 Kee-Lung Rd, Sec 3, Taipei, Taiwan
Spain
Spanish Society for NDT (AEND)
Spanish Society for NDT – professional information, events and publications
Slovakia
SSNDT
Slovak Society for Non-Destructive Testing, Racianska 71, 831 02 Bratislava
Sudan
SSNDT
Sudanese Society for Non-Destructive Testing, Sudanese Petroleum Pipelines Co, Amarat, Street 29, Khartoum
UK
The Institute of Corrosion
Corrosion Institute providing professional development and training
Thailand
TSNT
Thai Society for NDT, c/o N.D.T. Inspection Co Ltd, 242/167 Soi Vibhavadi – Rangsid 82 Vibhavadi Rd, 10210 Bangkok
Turkey
TURK NDT
The Turkish Society for Nondestructive Testing, Tahribatsiz Muayene Dernegi, Keresteciler Sitesi E, Blok No 5, 06370 Ostim/Ankara
UK
United Kingdom Accreditation Service (UKAS)
The United Kingdom Accreditation Service (UKAS) is the sole national accreditation body for the United Kingdom. UKAS is recognised by government, to assess against internationally agreed standards, organisations that provide certification, testing, inspection and calibration services.
Ukraine
USNDT
Ukrainian Society for Non-Destructive Testing, Bozhenko 11, 03680 Kiev
Uzbekistan
UzSNDT
Uzbekistan Society for Non-Destructive Testing, 179A Baku Street, 100076 Tashkent
Vietnam
VANDT
Vietnam Association for NDT, 46 Nguyen Van Ngoc, Ba Dinh, Ha No
Source: https://ndtinspect.com/worlwide-ndt-institutions-and-societies/
Responses