OIL AND GAS SEPARATION PROCESS
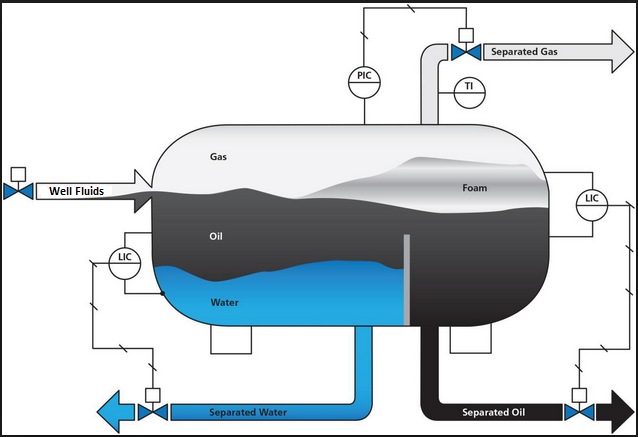
Introduction
The well-streams (or well fluids) produced from well platforms may consist of crude oil, gas, condensates, water and various contaminants. The purpose of the separator is to split the flow into desirable fractions. An oil/gas separator is a pressure vessel that is installed either in an onshore processing station or on an offshore platform. Based on the vessel configurations, the oil/gas separators can be divided into horizontal, vertical, or spherical separators. In teams of fluids to be separated, the oil/gas separators can be grouped into gas/liquid two-phase separator or oil/gas/water three-phase separator. In this paper, the three phase separator is used as the basis for the discussion and presentation of the Piping and Instrumentation Diagram (P&ID) of an oil and gas separation process.
The figure above shows a simplified flow diagram of the oil and gas 1st stage separation process.
Figure 1: Oil and Gas 1st Stage Separation Process flow Diagram (Simplified)
Inlet temperature is often in the range of 100-150 degrees C. On the example platform, the well stream is colder due to Subsea wells and risers.
The pressure is often reduced in several stages but commonly, three stages are used, and these allow controlled separation of volatile components. The purpose is to achieve maximum liquid recovery and stabilized oil and gas, and separate water. A large pressure reduction in a single separator will cause flash vaporization leading to instabilities and safety hazards.
The retention period is typically 5 minutes, allowing the gas to bubble out, water to settle at the bottom and oil to be taken out in the middle. In the first stage separator, the water content is typically reduced to less than 5%.
Figure 2 show the Piping and Instrumentation Diagram (P&ID) of the 1st stage (3-Phase) separator.
Figure 2: P&ID of an Oil and Gas 1st Stage (3-Phase) Separator
Piping
Piping is a system of pipes used to convey fluids (liquids and gases) from one location to another. The engineering discipline of piping design studies the efficient transport of fluid.
- Inlet Pipe for the Well Fluids
Figure 3: Inlet Pipe Diagram of an Oil and Gas Separation Process
From an oil or gas well, well fluids will enter the 1st stage separator vessel where its constituent components—oil, gas, and water will be separated. A gate valve is situated along the pipeline at the vessel’s entrance in order to allow or stop the flow of fluid. Figure 3 shows illustrates the diagram of this pipe flow.
- Flare System (Gas Section)
When the set pressure inside the separator vessel exceeded, the relief valve becomes the “path of least resistance” as the valve is forced open and a portion of the fluid (gas or liquid-gas mixture) is diverted through the auxiliary route. The diverted fluid cis usually routed through a piping system known as a flare header or relief header to a central, elevated gas flare where it is usually burned and the resulting combustion gases are released to the atmosphere. Figure at the left shows the diagram for this system
Figure 4: Flare System Diagram in an Oil and Gas Separation Process
Outlet Pipe for the Separated Gas (Vapor)
Figure 5: Gas Outlet Pipe System in Separation Process
The gas that has been separated from the well fluid mixture is directed through a pipe which is equipped with several valves including a pressure valve which by means is an actuator valve. The actuator valve works hand in hand with a pressure transmitter (PT) and control (PC) in order to monitor and regulate the pressure of the gas flowing through the piping system.
Outlet Pipe for the Separated Oil
Figure 6: Oil Outlet Pipe System in Separation Process
The oil that has been separated from the well fluid mixture is directed through a pipe that is equipped with several valves including a level valve which by means is an actuator valve. The actuator valve works hand in hand with a level transmitter (LT) and control (LC) in order to monitor and regulate the flow of the oil through the piping system. The same system is applied in the outlet pipe for the separated water. See Figures 6 and 7 accordingly.
Figure 7: Water Outlet Pipe System in Separation Process
Separator Vessel
Below are figures showing external (Figure 8) and internal view (illustrated and with the major components) of the separator vessel (Figure 9).
Figure 8: Separator Vessel
Figure 9: Major Components inside the Separator Vessel
At the crude entrance there is a baffle slug catcher that will reduce the effect of slugs (Large gas bubbles or liquid plugs). However some turbulence is desirable as this will release gas bubbles faster than a laminar flow. At the end there are barriers up to a certain level to keep back the separated oil and water. The liquid outlets from the separator will be equipped with vortex breakers to reduce disturbance on the liquid table inside. This is basically a flange trap to break any vortex formation and ensure that only separated liquid is tapped off and not mixed with oil or water drawn in though these vortices. Similarly the gas outlets are equipped with demisters, essentially filters that will remove liquid droplets in the gas.
System Control and Instrumentation
Gate Valve with spectacle blind flange
Gate valves are primarily designed to start or stop a flow (in this case the flow of well fluids) when a straight line flow of fluid and minimum flow restriction are needed. In service, these valves are pretty much kept either fully open, or fully closed. When turned open, the disc of the gate is completely removed allowing contents to pass. Although this gives the valve good shut-off properties and is bidirectional, they cannot be quickly opened or closed and are sensitive to vibration when open.
A spectacle blind is a safety device used to isolate a section of line or piece of equipment when the line or equipment needs to be inspected or removed from service. It is different than a valve in that the blind is a permanent or long-term isolation device.
One end of the blind will have an opening to allow flow through the pipe during operation and the other end is solid to block flow during maintenance.
Relief Valve
The relief valve is a type of valve used to control or limit the pressure in a system or vessel which can build up for a process upset, instrument or equipment failure, or fire. It is designed or set to open at a predetermined set pressure to protect pressure vessels and other equipment from being subjected to pressures that exceed their design limits.
Normally Closed Valve
Examples of normally-closed valves are sampling valves, which are only opened while a sample is taken for test. Other examples of normally-closed valves are emergency shut-down valves, which are kept open when the system is in operation and will automatically shut by taking away the power supply. This happens when there is a problem with a unit or a section of a fluid system such as a leak in order to isolate the problem from the rest of the system.
Flange
The flange in oil and gas applications can be a plate or ring to form a rim at the end of a pipe when fastened to the pipe (for example, a closet flange). A blind flange is a plate for covering or closing the end of a pipe. A flange joint is a connection of pipes, where the connecting pieces have flanges by which the parts are bolted together.
Actuators (Diaphragm or Globe)
Actuators are a means by which a valve can be automated so that no human interaction with the valve package is necessary to cycle the valve. Actuators can be remotely operated and can act as shutdown mechanisms in case of an emergency situation, wherein human interaction can be dangerous.
The diaphragm-style actuator includes a rubber diaphragm and stem in a circular steel housing. This style of actuators is ideal for valves requiring shorter travel, such as diaphragm valves and globe valves.
Reducer / Expander
Generally, the control valve size is smaller than the corresponding line size. This change in diameter should be clearly indicated in the P&ID with reducer and expander. The former is the component in a pipeline that reduces the pipe size from a larger to a smaller bore (inner diameter). While the latter on the other hand, expands the pipe size from a smaller to a larger bore.
Ball Valve (Normally Closed)
An increase in fluid pressure to the actuator is required to cause this valve to open.
Pressure Transmitter
A pressure transmitter senses a pressure and outputs a proportional current signal which is then transmitted to a monitor or controller
Pressure Controller (mounted in the control room)
.
Pressure controller receives data reading from pressure transmitter, compared that reading to a programmed setpoint, and signals a control element (in this case, an actuator valve) to either close or open depending on the corrective action needs to be taken.
Level Transmitter
Level transmitter provides an electrical output proportional to the well fluid level in the separator vessel. It may provide an output upon reaching a specified value (point level) or repeatedly after each measurement (continuous level).
Level Controller (mounted in the control room)
It regulates the level of the well fluids by processing the reading it receives from the level transmitter and then, compares the reading from a specified setpoint before it gives signal to the actuator valves which will either open or close depending on the corrective action that needs to be taken.