Stress Corrosion Cracking (SCC)
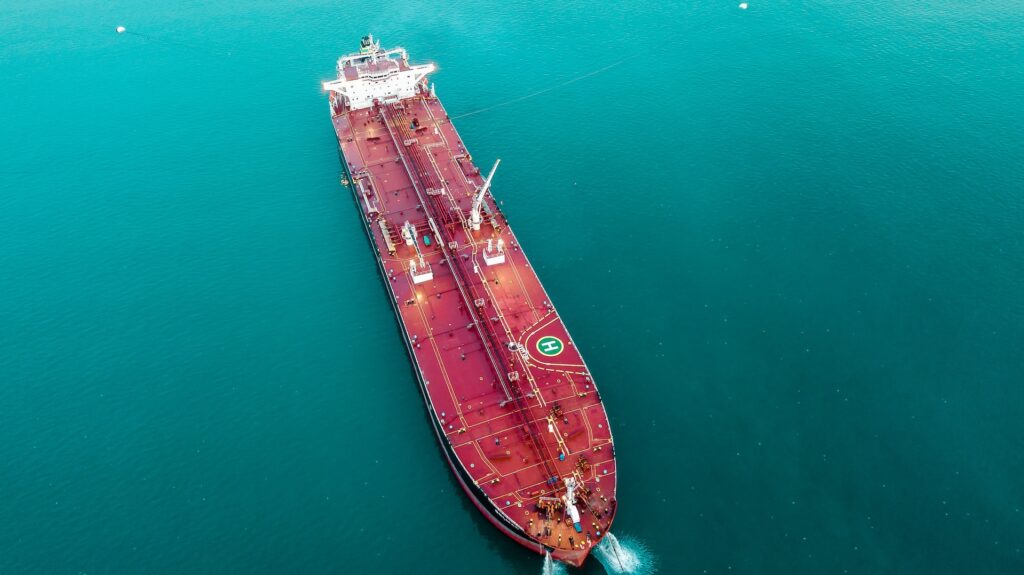
Stress corrosion cracking (SCC) is a type of corrosion that occurs when a material is subjected to both tensile stress and a corrosive environment. SCC is a significant concern for many materials and industries, as it can cause significant damage and lead to failure. Understanding the mechanisms and causes of SCC, as well as how to detect and prevent it, is essential for ensuring the safe and reliable operation of materials and equipment.
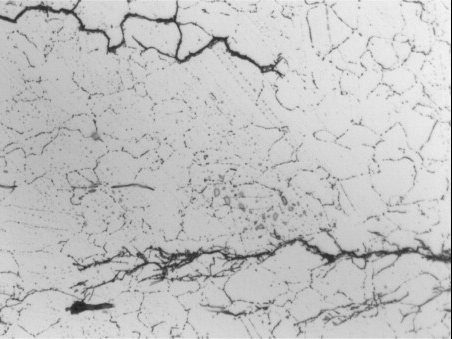
Formation of Stress Corrosion Cracking:
Stress corrosion cracking is formed when a material is subjected to both tensile stress and a corrosive environment. The combination of these two factors causes the material to crack and eventually fail. This type of corrosion can be initiated by small surface defects or by microscopic corrosion that weakens the material. The corrosion process is accelerated by the presence of tensile stress, which can cause the material to crack more quickly.
Factors Influencing the Formation of Stress Corrosion Cracking: Several factors can influence the formation of stress corrosion cracking, including:
- Material: The type of material used can impact the likelihood of SCC. Some materials, such as stainless steel and aluminum alloys, are more prone to SCC than others.
- Environment: The environment in which the material is used can impact the likelihood of SCC. High-temperature, high-pressure, and highly corrosive environments are more likely to cause SCC.
- Stress: The amount and type of stress that the material is subjected to can impact the likelihood of SCC. Tensile stress, in particular, can accelerate the formation of cracks.
Common Locations of Stress Corrosion Cracking:
Stress corrosion cracking can occur in a variety of materials and environments. Some of the most common materials that are prone to SCC include stainless steel, aluminum alloys, and high-strength steels. SCC is commonly found in high-temperature and high-pressure environments, such as power plants and oil and gas pipelines. SCC can also occur in a variety of structures, including bridges, buildings, and aircraft components.
Detection of Stress Corrosion Cracking: There are several methods used to detect stress corrosion cracking, including:
- Visual inspection: This involves inspecting the material for visible signs of cracking or corrosion.
- Ultrasonic testing: This method uses high-frequency sound waves to detect cracks or corrosion within the material. (Including PAUT and ToFD)
- X-ray testing: This method uses X-rays to produce images of the material’s internal structure and detect any signs of cracking or corrosion.
- Electrochemical testing: This method uses electrical current to detect signs of corrosion on the surface of the material.
Prevention and Mitigation of Stress Corrosion Cracking:
Once stress corrosion cracking has been detected, it is important to take steps to prevent its spread and mitigate its effects. Some common methods for preventing and mitigating SCC include:
- Material selection: Selecting materials that are resistant to SCC and are appropriate for the specific environment and conditions can help prevent the formation of cracks.
- Stress relief: Relieving tensile stress on the material can help prevent the initiation of SCC.
- Protective coatings: Applying protective coatings to the material can provide a barrier against corrosive environments and reduce the risk of SCC.
- Monitoring and inspection: Regular monitoring and inspection of materials can help detect SCC early on and prevent further damage.
- Repair and replacement: If stress corrosion cracking is detected, the affected material may need to be repaired or replaced to prevent further damage and failure.
- Corrosion inhibitors: Using corrosion inhibitors, such as inhibitors that are added to the corrosive environment, can help slow down the corrosion process and reduce the risk of SCC.
Industries Impacted by Stress Corrosion Cracking:
Stress corrosion cracking can have a significant impact on a variety of industries, including:
- Oil and gas: SCC can cause damage to pipelines, tanks, and other equipment in the oil and gas industry, leading to leaks and environmental damage.
- Power generation: SCC can cause problems in power plants, including damage to boilers and steam turbines.
- Chemical processing: SCC can impact chemical processing equipment, including tanks and reactors, leading to leaks and other safety concerns.
- Aerospace: SCC can affect aircraft components, including structural components, engines, and other parts, potentially leading to failure in flight.
- Construction: SCC can impact structures such as bridges and buildings, leading to potential collapse and other safety hazards.
Stress corrosion cracking is a widespread issue that can impact a variety of industries and materials. By understanding the mechanisms and causes of SCC, as well as taking steps to prevent and mitigate its effects, it is possible to reduce the risk of damage and failure and ensure the safe and reliable operation of materials and equipment. Regular monitoring and inspection, combined with appropriate material selection and protective measures, can help ensure that stress corrosion cracking is detected and addressed promptly, reducing the risk of further damage and failure.
For more info, please visit our forum section Failure Mechanisms
Responses