Ultrasonic Testing (UT)
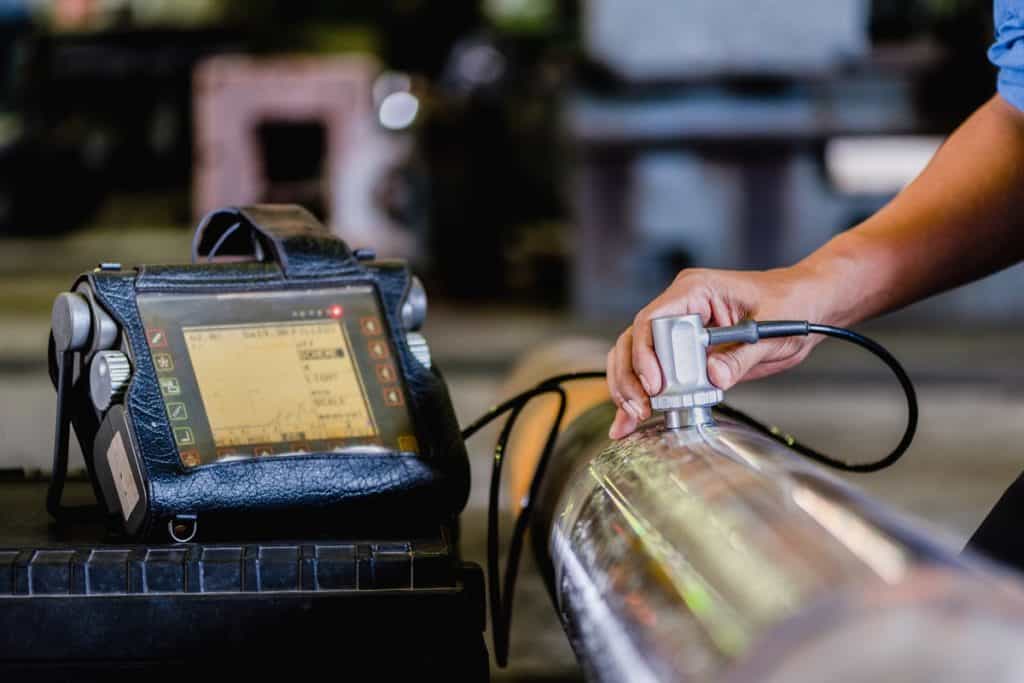
There are several non-destructive testing (NDT) that are used for testing the materials. Ultrasonic testing (UT) is one of them which required ultrasonic waves of high frequencies usually in the range of 0.5 to 20 MHz.
It is considered as an ideal testing technique for detecting defects without damaging the material. UT can be applied to a wide range of engineering materials including metals, ceramics, plastics, and composites. Wood and paper products are the common materials that are not suitable for UT. It is used in automobile, metallurgy, aerospace, construction as well as it is also applied in bio-medical fields for diagnosing and research purpose.
Principle of Ultrasonic Testing
Sound waves which have high frequencies are directional and will continue to travel through the material unless they come across any irregularity with a different boundary. Once they come across the boundary they will reflect back from that point towards their source.
When these reflections are analyzed, they will provide information regarding flaws and crack size, location, orientation, etc. During the UT, the material is observed with the help of the transducer which is passed over the object and is connected to the diagnostic machine. It is separated from the testing material by a couplant like water or oil. The couplant is needed to transfer sound energy to the parts efficiently from the transducer. If the non-contact method is used, using couplant is not necessary.
Working of Ultrasonic Testing
There are several units such as pulser and receiver, transducers, and monitor in a UT system. Pulser/receiver is an electronic device that generates high electrical voltage pulses. Transducers are made of piezoelectric material that generates high-frequency sound waves by converting electrical current into sound waves. The sound waves will enter the material and propagate inside the material through the waveform.
The part of the energy will reflect back if the sound waves are hit with diverse acoustical impedance and are converted into an electrical signal with the help of transducers and produce indications on the screen. The time required to travel as well as the velocity of sound waves determines the distance where the defect is present which results in acoustic impedance change. The information about the location, size, and orientation can be achieved with the help of the signal received
Defect detection in Ultrasonic Testing
Several types of irregularities that could risk the reliability of infrastructure, can be detected with the help of UT. Recognizing minute defects and the type of defect is the most important part of the analysis of the data as the minute defects go overlooked in other NDT. UT can detect defects that are small and difficult to be noticed in other NDT like cracking, corrosion, pitting, etc.
Advantages of Ultrasonic Testing
Generally, UT has many advantages like it can detect the surfaces as well as underneath surface defects and their size, shape, and position, even volumetric defects with better accuracy than other NDT techniques. It is effective both for the thick and thin materials. It requires access of only one side of material. It is portable and non-hazardous.
Limitations of Ultrasonic Testing
Although, UT has many advantages but it has certain limitations as well like it cannot be applied to all materials and required highly trained and skilled performers. Irregular and small parts are difficult to inspect. Surface preparation is required by cleaning thoroughly and is an expensive technique compared to other NDT techniques.