Essential Guide to Hot Tap Welding (Hot Tapping)
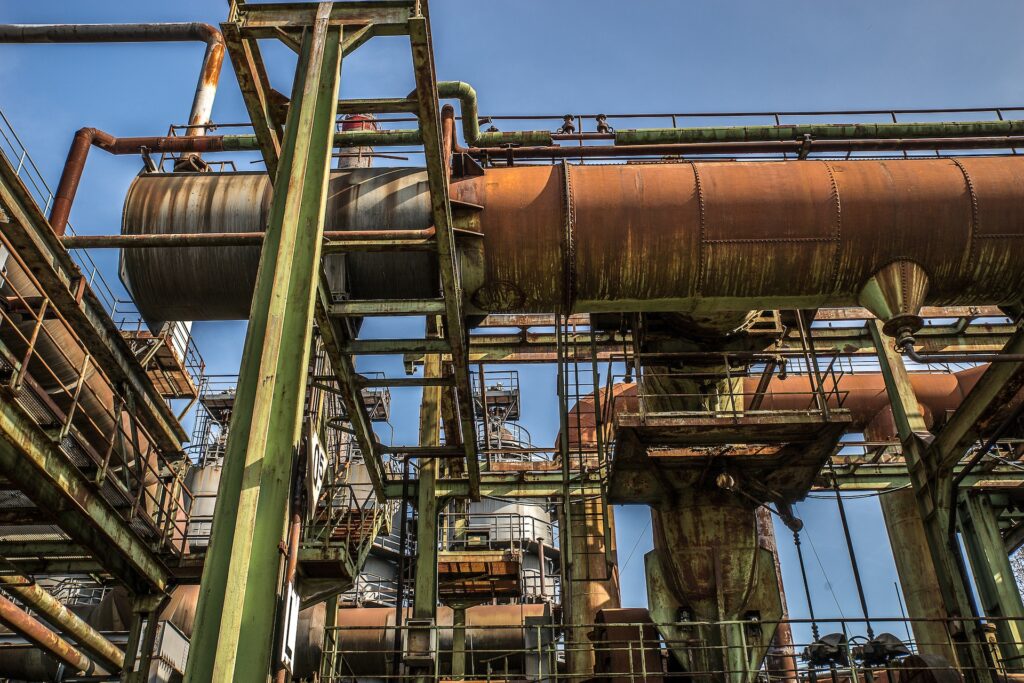
Hot tap welding, also known as hot tapping or in-service welding, is a specialized process that allows for the expansion or modification of a pipe or pipeline while it is still in service.
This process allows for the addition of new branches or connections to an existing pipeline without the need to shut it down and drain it of its contents. Hot tap welding is commonly used in the oil and gas industry, as well as in water and sewage treatment plants.
https://www.youtube.com/watch?v=0CXw6-R0JLw
One of the main benefits of hot tap welding is that it allows for the expansion or modification of a pipeline without the need to shut it down. This can save time and money, as the pipeline does not have to be drained and emptied before the welding can take place. It also minimizes the disruption to the flow of the contents within the pipe.
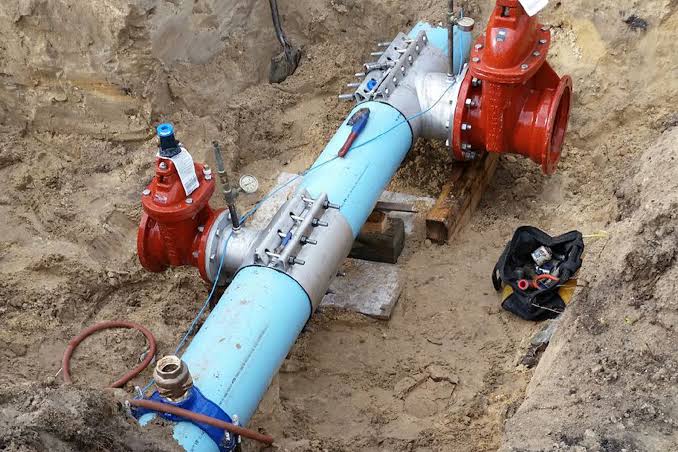
However, hot tap welding is not a simple task, and requires a high level of skill and expertise to be performed safely and effectively. In this article, we will provide an essential guide to hot tap welding, covering the techniques and best practices that are necessary for a successful hot tap welding project.
The first step in hot tap welding is to drill a hole in the pipe or pipeline at the desired location for the new branch or connection. This is typically done using a specialized drilling machine, such as a hot tap machine or a magnetic drill. The hole should be large enough to accommodate the new branch or connection, but small enough to minimize any disruption to the flow of the contents within the pipe.
Next, a valve is installed at the point of the hole to isolate the section of the pipe where the hot tap welding will take place. This is done to prevent any contents of the pipe from escaping during the welding process.
Once the valve is in place, the hot tap welding can begin. This process involves the use of a specialized welding machine, such as a tungsten inert gas (TIG) welder, to weld the new branch or connection to the existing pipe. The TIG welder uses a tungsten electrode to generate an electric arc, which melts the metal of the new branch or connection and the existing pipe, allowing them to be fused together.
There are several best practices that should be followed during the hot tap welding process to ensure the quality and safety of the welded joints. These include:
- Following all necessary safety precautions, including wearing protective gear and following proper handling procedures for any flammable or toxic substances that may be present in the pipe.
- Ensuring that the welders are qualified and experienced, and that they have received proper training in hot tap welding techniques.
- Developing and following a detailed welding procedure that outlines the steps to be taken during the hot tap welding process, including the equipment and materials to be used.
- Inspecting the welded joints thoroughly after the hot tap welding is complete to ensure that they meet all necessary quality standards.
Standards
There are several standards that apply to hot tap welding, including those related to the materials and equipment used, as well as the welding process itself. Some of the main standards that pertain to hot tap welding include:
- ASME B31.3: Process Piping – This standard covers the design, construction, testing, and maintenance of process piping systems. It includes requirements for hot tap welding, such as the minimum thickness of the pipe and the maximum allowable stress for the material being used.
- API 1104: Welding of Pipelines and Related Facilities – This standard covers the welding of pipelines and related facilities in the oil and gas industry. It includes requirements for the qualification of welders and welding procedures, as well as guidelines for the design, fabrication, and inspection of welded pipelines.
- AWS D1.1: Structural Welding Code – Steel – This standard covers the welding of structural steel components, including requirements for the qualification of welders and welding procedures, as well as guidelines for the design and fabrication of welded steel structures.
- ASME IX: Welding, Brazing, and Fusing Qualifications – This standard covers the qualification of welders and welding procedures, including requirements for the testing of welders and the development of welding procedures.
It is important for hot tap welders to be familiar with these standards and to follow them in order to ensure the quality and safety of the welded joints.
Safety
Hot tap welding is generally a safe process when it is performed by skilled and experienced welders who follow proper safety procedures and guidelines. However, as with any welding process, there are inherent risks involved, and it is important to follow all necessary precautions to minimize these risks.
Some of the potential safety concerns associated with hot tap welding include:
- Fire and explosion: The contents of the pipe being welded may be flammable or explosive, and proper precautions must be taken to prevent any ignition or explosion. This may include the use of specialized welding equipment and procedures, as well as the proper handling and storage of flammable substances.
- Toxic substances: The contents of the pipe may also be toxic, and proper precautions must be taken to protect the welders from exposure. This may include the use of protective gear and ventilation systems to ensure that the welders are not inhaling any harmful fumes.
- Physical injuries: Welding in general can be physically demanding, and hot tap welding is no exception. Welders should be in good physical condition and take breaks as needed to prevent fatigue and injuries.
Incidents
There have been several incidents that have occurred during hot tap welding projects, some of which have resulted in injuries or fatalities. These incidents are often the result of inadequate training, a lack of safety procedures, or equipment failure.
Some examples of incidents that have occurred during hot tap welding projects include:
- In 2018, a welder was killed and another was injured in a hot tap welding incident on an oil pipeline in West Virginia. The welders were working inside a pipeline when a pressure surge occurred, causing the weld to fail and the pipeline to rupture.
- In 2017, a hot tap welding incident on a natural gas pipeline in Oklahoma resulted in an explosion and fire that injured several workers. The incident was caused by a failure to properly follow safety procedures and to properly maintain the welding equipment.
- In 2016, a hot tap welding incident on an oil pipeline in Texas resulted in the death of one worker and the injury of another. The incident was caused by a failure to properly follow safety procedures and to properly maintain the welding equipment.
In conclusion, hot tap welding is a valuable technique that allows for the expansion or modification of a pipe or pipeline while it is still in service. It requires a high level of skill and expertise, and it is important to follow proper techniques and best practices to ensure the quality and safety of the welded joints. By following the guidelines outlined in this essential guide to hot tap welding, you can successfully complete your hot tap welding project and achieve your desired results.
Want to know more about welding and inspection? Visit welding group and forum
Hi
Why so important the welder have to be qualified in 6G position,