API 570 Course Notes
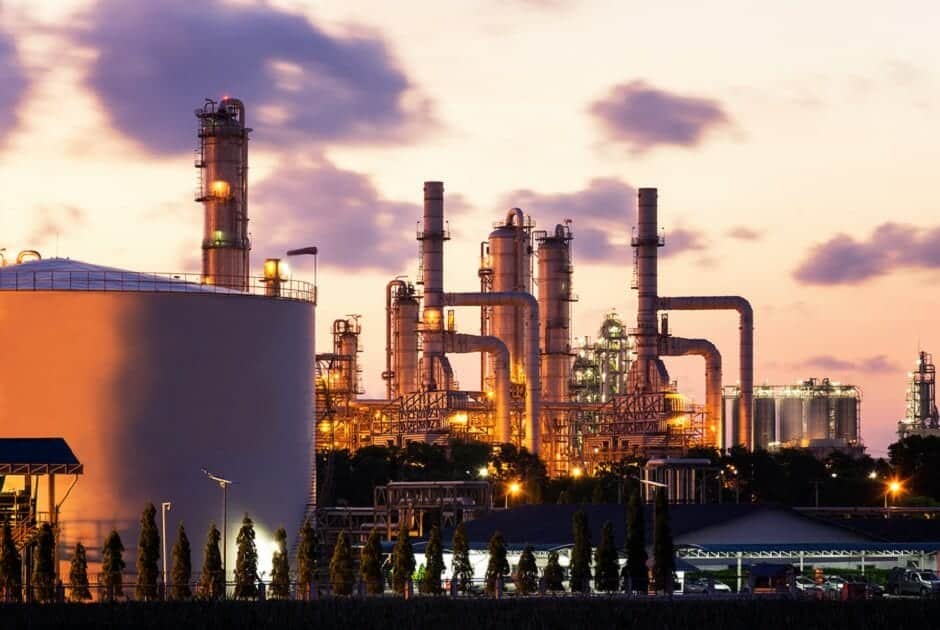
API 570 PIPING INSPECTOR
PREPARATORY COURSE
COURSE NOTES
API 570 PIPING INSPECTOR
PREPARATORY COURSE
TABLE OF CONTENTS
CHAPTER DESCRIPTION
1. Overwiew of API 570
2. Overview of RP- API 574
3. Overwiew of ASME B 31.3
4. Overview of ASME B 16.5
- Overview of ASME Section IX
6. Overview of ASME Section V
CHAPTER-1
570 PIPING INSPECTION CODE
- INTRODUCTION TO API-570
1.1 SCOPE
-
-
- Coverage :
-
API 570 covers inspection, repair, alteration, and rerating procedures for metallic piping systems that have been in service.
Repair ; The work necessary to restore a piping system to a condition suitable for safe operation at the design condition.
Alterations : A physical change in any component that has design implications affecting the pressure containing capability or flexibility of a piping system beyond the scope of its design.
Rerating : A change in either or both the design temperature or the maximum allowable working pressure of a piping system. A rerating may consist of an increase, a decrease, or a combination of both. Rerating below original design conditions is a means to provide increased corrosion allowance.
-
-
- LIMITATIONS :
-
API 570 shall not be used as a substitute for the original construction requirements governing a piping system before it is placed in service.
-
- SPECIFIC APPLICATIONS
1.2.1 Included Fluid Services :
API 570 applies to piping systems for process fluids, hydrocarbons, and similar flammable or toxic fluid services, such as the following.
-
- Raw, intermediate, and finished petroleum products.
- Raw intermediate, and finished chemical products.
- Catalyst lines.
- Hydrogen, natural gas, fuel gas, and flare systems.
- Sour water and hazardous waste streams above threshold limits, as defined by jurisdictional regulations.
- Hazardous chemicals above threshold limits, as defined by jurisdictional regulations.
- Excluded and Optional Piping Systems :
The fluid services and classes of piping systems listed below are excluded from the specific requirements of API 570 but may be included at the owner’s or user’s (owner/user’s) option.
- Fluid services that are excluded or optional include the following.
- Hazardous fluid services below threshold limits, as defined by jurisdictional regulations.
- Water (including fire protection systems) , steam, steam-condensate, boiler feed water, and Category D fluid services, as defined in ASME B 31.3
- Classes of piping systems that are excluded or optional are as follows :
- Piping systems on movable structures covered by jurisdictional regulations, including piping systems on trucks, ships, barges, and other mobile equipment.
- Piping systems that are an integral part or component or rotating or reciprocating mechanical devices, such as pumps, compressors, turbines, generators, engines, and hydraulic or pneumatic cylinders where the primary design considerations and/or stresses are derived from the functional requirements of the device.
- Internal piping or tubing of fired heaters and boilers, including tubes, tube headers, return bends, external crossovers, and manifolds.
- Pressure vessels, heaters, furnaces, heat exchangers, and other fluid handling or processing equipment, including internal piping and connections for external piping.
- Plumbing, sanitary sewers, process waste sewers, and storm sewers.
- Piping or tubing with an outside diameter not exceeding that of NPS ½.
- Nonmetallic piping and polymeric or glass-lined piping.
- DEFINITIONS
2.1 APPLICATION CODE :
The code, code section, or other recognized and generally accepted engineering standard or practice to which the piping system was built or which is deemed by the owner or user or the piping engineer to be most appropriate for the situation, including but not limited to the latest edition of ASME B 31.3
2.2 AUTHORIZED INSPECTION AGENCY :
Defined as any of the following. :
- The inspection organization of the jurisdiction in which the piping system is used.
- The inspection organization of an insurance company that is licensed or registered to write insurance for piping systems.
- An owner or user of piping systems who maintains an inspection organization for activities relating only to his equipment and not for piping systems intended for sale or resale.
- An independent inspection organization employed by or under contract to the owner or user of piping systems that are used only by the owner or user and not for sale or resale.
- An independent inspection organization licensed or recognized by the jurisdiction in which the piping system is used and employed by or under contract to the owner or user.
2.3 AUTHORIZED PIPING INSPECTOR :
An employee of an authorized inspection agency who is qualified and certified to perform the functions specified in API 570. A nondestructive (NDE) examiner is not required to be an authorized piping inspector. Whenever the term inspector is used in API 570, it refers to an authorized piping inspector.
2.4 AUXILLARY PIPING :
Instrument and machinery piping, typically small-bore secondary process piping that can be isolated from primary piping systems. Examples include flush lines, seal oil lines, analyzer lines, balance lines, buffer gas lines, drains and vents.
2.5 CUI :
Corrosion under insulation, including stress corrosion cracking under insulation.
2.6 DEADLEGS :
Components of a piping system that normally have no significant flow. Examples include the following : blanked branches, lines with normally closed block valves, lines with one end blanked, pressurized dummy support legs, stagnant control valve bypass piping, spare pump piping, level bridles, relief valve inlet and outlet header piping, pump trim bypass lines, high point vents, sample points, drains, bleeders, and instrument connections.
2.7 DEFECT :
An imperfection of a type or magnitude exceeding the acceptable criteria.
2.8 EXAMINER :
A person who assists the inspector by performing specific nondestructive examination (NDE) on piping system components but does not evaluate the results of those examinations in accordance with API 570, unless specifically trained and authorized to do so by the owner or user. The examiner need not be qualified in accordance with API 570.
2.9 HOLD POINT :
A point in the repair or alteration process beyond which work may not proceed until the required inspection has been performed and documented.
2.10 IMPERFECTIONS :
Flaws or other discontinuities noted during inspection that may be subject to acceptance criteria during an engineering and inspection analysis.
2.11 INDICATION :
A response or evidence resulting from the application of a nondestructive evaluation technique.
2.12 INJECTION POINT :
Locations where relatively small quantities of materials are injected into process streams to control chemistry or other process variables. Injection points do not include locations where two process streams join.
2.13 IN-SERVICE :
Refers to piping systems that have been placed in operation, as opposed to new construction prior to being placed in service.
2.14 INSPECTOR :
An authorized piping inspector.
2.15 LEVEL BRIDLE :
A level gauge glass piping assembly attached to a vessel.
-
- MAXIMUM ALLOWABLE WORKING PRESSURE (MAWP)
The maximum internal pressure permitted in the piping system for continued operation at the most severe condition of coincident internal or external pressure and temperature (maximum and minimum) expected during service. It is the same as the design pressure, as defined in ASME B 31.3 and other code sections, and is subject to the same rules relating to allowances for variations of pressure or temperature or both.
2.17 ON-STREAM :
Piping containing any amount of process fluid.
2.18 PIPING CIRCUIT :
A section of piping that has all points exposed to an environment of similar corrosivity and that is of similar design conditions and construction material.
2.19 PRIMARY PROCESS PIPING :
Process piping in normal, active service that cannot be valved off or, if it were valved off, would significantly affect unit operability. Primary process piping normally includes all process piping greater than NPS 2.
2.20 REPAIR ORGANIZATION :
Any of the following :
- An owner or user of piping systems who repairs or alters his or her own equipment in accordance with API 570.
- A contractor whose qualifications are acceptable to the owner or user of piping systems and who makes repairs or alterations in accordance with API 570.
- One who is authorized by, acceptable to, or otherwise not prohibited by the jurisdiction and who makes repairs in accordance with API 570.
2.21 SECONDARY PROCESS PIPING :
Small-bore (less than or equal to NPS 2) process piping downstream of normally closed block valves.
2.22 SMALL-BORE PIPING (SBP) :
Piping that is less than or equal to NPS 2.
2.23 SOIL-TO AIR (S/A) INTERFACE :
An area in which external corrosion may occur on partially buried pipe. The zone of the corrosion will vary depending on factors such as moisture, oxygen content of the soil, and operating temperature. The zone generally is considered to be from 12 inches (305 mm) below to 6 inches (150 mm) above the soil surface. Pipe running parallel with the soil surface that contacts the soil is included.
2.24 SPOOL :
A section of piping encompassed by fianges or other connecting fittings such as unions.
2.25 TEMPER EMBRITTLEMENT :
A loss of ductility and notch toughness in susceptible low-alloy steels, such as 1 ¼ Cr and 2 ¼ Cr, due to prolonged exposure to high-temperature service [700o F-1070oF (370oC-575oC) ]
2.26 TEMPORARY REPAIRS :
Repairs made to piping systems in order to restore sufficient integrity to continue safe operation until permanent repairs can be scheduled and accomplished within a time period acceptable to the inspector or piping engineer.
2.27 TEST POINT :
An area defined by a circle having a diameter not greater than 2 inches (50 mm) for a line diameter not exceeding 10 inches (250 mm) or not greater than 3 inches (75 mm) for larger lines. Thickness readings may be averaged within this area. A test point shall be within a thickness measurement location.
2.28 THICKNESS MEASUREMENT LOCATIONS (TMLs) :
Designated areas on piping systems where periodic inspections and thickness measurement’s are conducted.
2.29 WFMT :
Wet fluorescent magnetic -particle testing.
- OWNER/ INSPECTION ORGANISATION
- API AUTHORIZED PIPING INSPECTOR QUALIFICATION AND CERTIFICATION :
Authorized piping inspectors shall have education and experience in accordance with Appendix A of this inspection code. Authorized piping inspectors shall be certified by the American Petroleum Institute in accordance with the provisions of Appendix A. Whenever the term inspector is used in this document, it refers to an authorized piping inspector.
3.2 RESPONSIBILITIES :
3.2.1 An owner/user organization is responsible for developing, documenting, implementing, executing, and assessing piping inspection systems and inspection procedures that will meet the requirements of this inspection code. These systems and procedures will be contained in a quality assurance inspection manual or written procedures and shall include :
- Organization and reporting structure for inspection personnel.
- Documenting and maintaining inspection and quality assurance procedures.
- Documenting and reporting inspection and test results.
- Corrective action for inspection and test results.
- Internal auditing for compliance with the quality assurance inspection manual.
- Review and approval of drawings, design calculations, and specifications for repairs, alterations, and re-ratings.
- Ensuring that all jurisdictional requirements for piping inspection, repairs, alterations, and re-rating are continuously met.
- Reporting to the authorized piping inspector any process changes that could affect piping integrity.
- Training requirements for inspection personnel regarding inspection tools, techniques, and technical knowledge base.
- Controls necessary so that only qualified welders and procedures are used for all repairs and alterations.
- Controls necessary so that only qualified nondestructive examination (NDE) personnel and procedures are utilized.
- Controls necessary so that only materials conforming to the applicable section of the ASME Code are utilized for repairs and alterations.
- Controls necessary so that all inspection measurement and test equipment are properly maintained and calibrated.
- Controls necessary so that the work of contract inspection or repair organizations meet the same inspection requirements as the owner/user organization.
- Internal auditing requirements for the quality control system for pressure-relieving devoices.
3.2.2 PIPING ENGINEER :
The piping engineer is responsible to the owner/user for activities involving design, engineering review, analysis, or evaluation of piping systems covered by API 570.
3.2.3 REPAIR ORGANIZATION :
The repair organization shall be responsible to the owner/user and shall provide the materials, equipment, quality control, and workmanship necessary to maintain and repair the piping systems in accordance with the requirements of API 570.
3.2.4 AUTHORIZED PIPING INSPECTOR :
When inspections, repairs, or alterations are being conducted on piping systems, an API authorized piping inspector shall be responsible to the owner/user for determining that the requirements of API 570 on inspection, examination, and testing are met, and shall be directly involved in the inspection activities. The API authorized piping inspector may be assisted in performing visual inspections by other properly trained and qualified individuals, who may or may not be certified piping inspectors. Personnel performing nondestructive examinations shall meet the qualifications identified in 3.12, but need not be API authorized piping inspectors. However, all examination results must be evaluated and accepted by the API- authorized piping inspector.
3.2.5 OTHER PERSONNEL :
Operating, maintenance, or other personnel who have special knowledge or expertise related to particular piping systems shall be responsible for promptly making the inspector or piping engineer aware of any unusual conditions that may develop and for providing other assistance, where appropriate.
INSPECTION AND TESTING
- RISK BASED INSPECTION (RBI)
RBI is identifying and evaluating potential degradation consequence of which may be a risk of creation of unsafe conditions (for plant, process, people ) and / or likely failure of component.
RBI involves following essential elements :
- Expected type of degradation i.e. type of degradation process as well as environmental factors may cause.
- Likely areas affected i.e. identifying the most prone areas and possible locations to look for the type of degradation.
- Measurement of degradation i.e. quantifying the amount of degradation.
- Assessment and evaluation i.e. analysis of degradation and likely consequences.
- Above all effectiveness of inspection practices, tools techniques employed have a great bearing of success of RBI program.
- PREPARATION :
Prior to actual inspection proper preparation and safety precautions are essential particularly if components are to be inspected internally. This essentially involves –
- Isolating and segregating the piping system, installing blanks (blids) etc.
- Removal of harmful liquids, gases, vapors, flushing out and purging to bring down residual content to safe levels.
- Obtain suitable permissions to work i.e. cold work permit (CWP), Hotwork Permits (HWP) etc.
- Protective equipment, clothing, masking as required.
- Safety equipments shall be subjectto operating facilities safety requirements. (e. g. electrical requirements, flame arrester etc.)
3. INSPECTION FOR SPECIFIC TYPES OF CORROSION AND CRACKING :
Each owner/ user should provide specific attention to the need for inspection of piping system that are susceptible to the following specific types & areas of deterioration :
- Injection points.
- Deadlegs.
- Corrosion under insulation ( CUI ).
- Soil-to-air (S/A ) interfaces. .
- Services specific & localized corrosion.
- Erosion &c orrosion/erosion.
- Environmental cracking.
- Corrosion beneath linings & deposits.
- Fatigue cracking .
- Creep cracking.
- Brittle fracture.
- Freeze damage.
3.1 Injection Points : Injection points are sometimes subject to accelerated or localized corrosion.
When designating an injection point circuit for the purposes of inspection, the recommended upstream limit of the injection point circuit is a minimum of 12 inches (300) or three pipe diameters upstream of the injection point, whichever is greater. The recommended downstream limit of the injection point circuit is the seconed change in flow direction past the injection point, or 25 feet (7.6 m) beyond the first change in flow direction, whichever is less. In some cases, it may be more appropriate to extend this circuit to the next piece of pressure equipment.
Guide Lines For Selecting TMLS :
- Establish TMLs on appropriate fittings within the injection point circuit.
- Establish TMLs on the pipe wall at the location of expected pipe wall impingement of injected fiuid.
- TMLs at intermediate locations along the longer straight piping within the injection point circuit may be required.
d. Establish TMLs at both the upstream & downstream limit of the injection point circuit.
The preferred methods of inspecting injection points are radiography and/or ultrasonics, as appropriate, to establish the minimum thickness at each TML.
For some applications, it is beneficial to remove piping spools to facilitate a visual inspection of the inside surface. However, thickness measurements will still be required to determine the remaining thickness.
During periodic scheduled inspections, more extensive inspection should be applied to an area beginning 12 inches (300 mm) upstream of the injection nozzle and continuing for at least ten pipe diameters downstream of the injection point. Additionally, measure and record the thickness at all TMLs within the injection point circuit.
-
- Deadlegs : The corrosion rate in deadlegs can vary significantly from the adjacent active piping. The inspector should monitor wall thickness on selected deadlegs, including both the stagnant end and at the connection to an active line. In hot piping systems, the high-point area may corrode due to convective currents set up in the deadlegs. Consideration should be given to removing deadlegs that serve no further process purpose.
- Corrosion Under Insulation : External inspection of insulated piping systems should include a review of the integrity of the insulation system for conditions that cold lead to corrosion under insulation (CUI) and for signs of ongoing CUI. Sources of moisture may include rain, water leaks, condensation and deluge systems. The most common forms of CUI are localized corrosion of carbon steel and chloride stress corrosion cracking of austenitic stainless steels.
Below are the guidelines for indentifying potential CUI areas for inspection. The extent of a CUI inspection program may vary depending on the local climate – warmer marine locations may require a very active program; whereas cooler, drier, mid-continent locations may not need as extensive a program.
3.4 Insulated Piping Systems Susceptible to CUI : Certain areas and types of piping systems are potentially more susceptible to CUI, including the following :
- Areas exposed to mist overspray from cooling water towers.
- Areas exposed to steam vents.
- Areas exposed to deluge systems
- Areas subject to process spills, ingress of moisture , or acid vapors.
- Carbon steel piping systems, including those insulated for personnel protection, operation between 250 F- 2500 F (-40C-1200 C). CUI is particularly aggressive where operating temperatures cause frequent or continuous condensation and re-evaporation of atmospheric moisture.
- Carbon steel piping systems that normally operate in-service above 2500 F (1200C) but are in intermittent service.
- Deadlegs and attachments that protrude from insulated piping and operate at a different temperature than the operating temperature of the active line.
- Austenitic stainless steel piping systems operating 1500F- 4000 F (650C-2040C). (These systems are susceptible to chloride cracking. )
- Vibrating piping systems that have a tendency to inflict damage to insulation jacketing providing a path for water ingress.
- Steam traced piping systems that may experience tracing leaks, especially at tubing fitting beneath the insulation.
- Piping systems with deteriorated coatings and/or wrappings.
- Common Locations on Piping Systems Susceptible to CUI : The areas of piping systems listed above may have specific locations within them that are more susceptible to CUI, including the following :
- All penetrations or breaches in the insulation jacketing systems, such as :
- Deadlegs (vents, drains, and other similar items)
- Pipe hangers and other supports.
- Valves and fittings (irregular insulation surfaces)
- Bolted-on pipe shoes.
- Steam tracer tubing penetrations.
- Termination of insulation at flangers and other piping components.
- Damaged or missing insulation jacketing
- Insulation jacketing seams located on the top of horizontal piping or imporperty lapped or sealed insulation jacketing.
- Termination of insulation in a vertical pipe.
- Caulking that has hardened, has separated, or is missing.
- Bulges or staining of the insulation or jacketing system or missing bands (Bulges may indicate corrosion product buildup).
- Low points in piping systems that have a known breach in the insulation system, including low points in long unsupported piping runs.
- Carbon or low-alloy steel flanges, bolting, and other components under insulation in high-alloy piping systems.
- Soil-to–Air Interface : Soil-to-air (S/A) interfaces for buried piping without adequate cathodic protection shall be included in scheduled external piping inspections.)
Thickness measurements and excavation may be required to assess whether the corrosion is localized to the S/A interface or extends to the buried system.
Thickness readings at S/A interfaces may expose the metal and accelerate corrosion if coatings and wrappings are not properly restored.
If the buried piping is uncoated at grade, consideration should be given to excavating 6 inches to 12 inches (150 mm to 300 mm) deep to assess the potential for hidden damage.
3.7 Service Specific & Localized Corrosion : An effective inspection program includes the following three elements, which help identify the potential for service specific & localized corrosion & select appropriate TMLs :
a. An inspector with knowledge of the service & where corrosion is
likely to occur.
- Extensive use of nondestructive examination (NDE).
- Communication from operating personnel when process upsets occur that may affect corrosion rates.
- Dew point corrosion in condensing streams.
- Mixed grades of carbon steel piping in hot corrosive oil service (450 deg F [230 deg]C) or higher temperature & sulfur content in the oil greater than 0.5 percent by weight.
- Non silicon kiled steel pipe, such as A-53 & API 5L, may corrode at higher rates than does silicon killed steel pipe, such as A-106 especially in high –temperature sulfidic environments.
- Erosion & corrosion/ erosion : Erosion can be defined as the removal of surface material by the action of numerous individual impacts of solid or liquid particles. It can be characterized by grooves, rounded holes, waves, & vallys in a directional pattern. Erosion usually occurs in areas of turbulent flow, such as at change of direction in a piping system or downstream of control valves where vaporization may take place.
- Erosion damage is usually increased in streams with large quantities of solid or liquid particles flowing at high velocities. A combination of corrosion & erosion ( corrosion/erosion )results in significantly greater metal loss than can be expected from corrosion occurs at high velocity & high turbulence areas.
Examples of places to inspect include the following :
- Downstream of control valves, especially when flashing is
occurring.
- Downstream of orifices.
- Downstream of pump discharges.
- At any point of flow direction change, such as the inside & outside radii of elbows.
- Environmental Cracking : Piping system construction materials are normally selected to resist the various forms of stress corrosion cracking (SCC). However, some piping system may be susceptible to environmental cracking due to upset process conditions, CUI unanticipated condensation, or exposure to wet hydrogen sulfide or carbonates.
Examples of environmental cracking include :
a. Chloride SCC of austenitic stainless steels due to moisture &
chlorides under insulation, under deposits , under gaskets, or in crevices.
- Caustic SCC ( sometimes known as caustic embrittlement ).
- Scc in environments where wet hydrogen sulfide exists, such as systems containing sour water.
- Hydrogen blistering & hydrogen induced cracking ( HIC ) damage .
4. CORROSION BENEATH LININGS AND DEPOSITS :
4.1 General:
If external or internal coatings, refractory linings, and corrosion-resistant linings are in good condition and there is no reason to suspect a deteriorated condition behind them, it is usually not necessary to remove them for inspection of the piping system.
The linings should be inspected for separation, breaks, holes, and blisters. If any of these conditions are noted, it may be necessary to remove portions of the internal lining to investigate the effectiveness of the lining and the condition of the metal piping beneath the lining.
Corrosion beneath refractory linings can result in separation and bulging of the refractory. If bulging or separation of the refractory lining is detected, portions of the refractory may be removed to permit inspection of the piping beneath the refractory.
4.2. FATIGUE CRACKING :
Fatigue cracking of piping systems may result from excessive cyclic stresses that are often well below the static yield strength of the material. The onset of low-cycle fatigue cracking is often directly related to the number of heat-up and cool-down cycles experienced. Excessive piping system vibration (such as machine or flow-induced vibrations) also can cause high-cycle fatigue damage.
Fatigue cracking can typically be first detected at points of high-stress intensification such as branch connections. Locations where metals having different coefficients of thermal expansion are joined by welding may be susceptible to thermal fatigue. Preferred NDE methods of detecting fatigue cracking include liquid-penetrant testing (PT) or magnetic-particle testing (MT). Acoustic emission also may be used to detect the presence of cracks that are activated by test pressures of stresses generated during the test.
It is important that the owner/user and the inspector understand that fatigue cracking is likely to cause piping failure before it is detected with any NDE methods. Of the total number of fatigue cycles required to produce a failure, the vast majority are required to initiate a crack and relatively fewer cycles are required to propagate the crack to failure. Therefore, proper design and installation in order to prevent the initiation of fatigue cracking are important.
4.2.12 CREEP CRACKING :
Creep is dependent on time, temperature, and stress. Cracking is accelerated by creep and fatigue interaction when operating conditions in the creep range are cycle. If excessive temperatures are encountered, mechanical property and microstructural changes in metals also may take place.
NDE methods of detecting creep cracking include liquid-penetrant testing, magnetic-particle testing, ultrasonic testing, radiographic testing, and in-situ metallography. Acoustic emission testing also may be used to detect the presence of cracks that are activated by test pressures or stresses generated during the test.
4.2.13 BRITTLE FRACTURE :
Carbon low-alloy, and other ferritic steels may be susceptible to brittle failure at or below ambient temperatures. Brittle fracture usually is not a concern with relatively thinwall piping. Most brittle fractures have occurred on the first application of a particular stress level (that is, the first hydrotest or overload) unless critical defects are introduced during service. The potential for a brittle failure shall be considered when rehydrotesting.
4.2.14 FREEZE DAMAGE :
At subfreezing temperatures, water and aqueous solutions in piping systems may freeze and cause failure because of the expansion of these materials. After unexpectedly severe freezing weather, it is important to check for freeze damage to exposed piping components before the system thaws. If rupture has occurred, leakage may be temporarily prevented by the frozen fluid. Low points, riplegs, and deadlegs of piping systems containing water should be carefully examined for damage.
4.3 TYPES OF INSPECTION AND SURVEILLANCE :
Different types of inspection and surveillance are appropriate depending on the circumstances and the piping system . These include the following :
- Internal visual inspection.
- Thickness measurement inspection.
- External visual inspection.
- Vibrating piping inspection
- Supplemental inspection.
4.3.1 INTERNAL VISUAL INSPECTION :
Internal visual inspections are not normally performed on piping. When possible and practical, internal visual inspections may be scheduled for systems such as large-diameter transfer lines, ducts, or other large-diameter piping systems. Such inspections are similar in nature to pressure vessel inspections and should be conducted with methods and procedures similar to those outlined in API 510.
4.3.2 THICKNESS MEASUREMENT INSPECTION :
A thickness measurement inspection is performed to determine the internal condition and remaining thickness of the piping components. Thickness measurements may be obtained when the piping system is in or out of operation and shall be performed by the inspector or examiner.
4.3.3 EXTERNAL VISUAL INSPECTION :
In addition to these scheduled external inspections that are documented in inspection records, it is beneficial for personnel who frequent the area to report deterioration or changes to the inspector.
4.3.4 SUPPLEMENTAL INSPECTION :
Other inspections may be scheduled as appropriate or necessary. Examples of such inspections include periodic use of radiography and/or thermography to check for fouling or internal plugging, thermography to check for hot spots in refractory lined systems, or inspection for environmental cracking. Acoustic emission, acoustic leak detection, and thermography can be used or remote leak detection and surveillance. Ultrasonics and/or radiography can be used for detecting localized corrosion.
4.4 THICKNESS MEASUREMENT LOCATIONS :
4.4.1 GENERAL :
Thickness measurement locations (TML’s) are specific areas along the piping circuit where inspections are to be made. The nature of the TML varies according to its location in the piping system. The selection of TML’s shall consider the potential for localized corrosion and service-specific corrosion as described in 5.3
4.4.2 TML MONITORING :
Each piping system shall be monitored by taking thickness measurements at TML’s. Piping circuits with high potential consequences if failure should occur and those subject to higher corrosion rates or localized corrosion will normally have more TMLs and be monitored more frequently.
The minimum thickness at each TML can be located by ultrasonic scanning or radiography. Electromagnetic techniques also can be used to identify thin areas that may then be measured by ultrasonics or radiography. When accomplished with ultrasonics, scanning consists of taking several thickness measurement at the TML searching for localized thinning. The thinnest reading or an average of several measurement readings taken within the area of a test point shall be recorded and used to calculate corrosion rates, remaining life, and the next inspection date.
Where appropriate, thickness measurements should include measurements at each of the four quadrants on pipe and fittings, with special attention to the inside and outside radius of elbows and tees where corrosion/erosion could increase corrosion rates. As a minimum, the thinnest reading and its location shall be recorded.
TML’s should be established for areas with continuing CUI, corrosion at S/A interfaces, or other locations of potential localized corrosion as well as for general uniform corrosion.
TMLs should be marked on inspection drawings and on the piping system to allow repetitive measurements at the same TMLs. This recording procedure provides data for more accurate corrosion rate determination.
4.4.3 TML SELECTION :
In selecting or adjusting the number and locations of TMLs the inspector should take unto account the patterns of corrosion that would be expected and have been experienced in the process unit.
More TMLs should be selected for piping systems with any of the following characteristics :
- Higher potential for creating a safety or environmental emergency in the event of a leak.
- Higher expected or experienced corrosion rates.
- Higher potential for localized corrosion.
- More complexity in terms of fittings, branches, deadlegs injection points, and other similar items.
- Higher potential for CUI
Fewer TMLs can be selected for piping systems with any of the following three characteristics :
- Low potential for creating a safety or environmental emergency in the event of a leak.
- Relatively non-corosive piping systems.
- Long, straight-run piping systems.
TMLs can be eliminated for piping systems with either of the following two characteristics :
- Extremely low potential for creating a safety or environmental emergency in the event of a leak.
- Non-corrosive systems, as demonstrated by history or similar service, and systems not subject to changes that could cause corrosion.
4.5 THICKNESS MEASUREMENT METHODS :
Ultrasonic thickness measuring instruments usually are the most accurate mean for obtaining thickness measurements on installed pipe larger than NPS 1. Radiographic profile techniques are preferred for pipe diameters of NPS 1 and smaller. Radiographic profile techniques may be used for locating areas to be measured, particularly in insulted systems or where non-uniform or localized corrosion is suspected.
Where practical , ultrasonics can then be used to obtain the actual thickness of the areas to be recorded. Following ultrasonic readings at TMLs, proper repair of insulation and insulation weather coating is recommended to reduce the potential for CUI.
Radiographic profile techniques, which do not require removing insulation, may be considered as an alternative.
When ultrasonic measurements are taken above 150oF (65oC), instruments, couplants, and procedures should be used that will result in accurate measurements at the higher temperatures.
Measurements should be adjusted by the appropriate temperature correction factor.
- Improper instrument calibration.
- External coatings or scale.
- Excessive surface roughness.
- Excessive “rocking” of the probe (on the curved surface)
- Subsurface material flaws, such as laminations.
- Temperature effects [at temperatures above 150oF (65oC)]
- Small flaw detector screens.
- Thickness of less than 1/8 inch (3.2 mm) for typical digital thickness gauges.
In addition, it must be kept in mind that the pattern of corrosion can be non-uniform.
For corrosion rate determinations to be valid, it is important that measurements on the thinnest point be repeated as closely as possible to the same location. Alternatively, the minimum reading or an average of several readings at a test point may be considered.
When piping systems are out of service, thickness measurements may be taken through openings using calipers. Calipers are useful in determining approximate thicknesses of castings, forgings, and valve bodies, as well as pit depth approximations from CUI on pipe.
Pit depth measuring devices also may be used to determine the depth of localized metal loss.
4.6 PRESSURE TESTING OF PIPING SYSTEMS :
Pressure tests are not normally conducted as part of a routine inspection. Exceptions to this include requirements of local jurisdictions, after welded alterations or when specified by the inspector or piping engineer. When they are conducted , pressure tests shall be performed in accordance with the requirements of ASME B 31.3
If a pressure test is to be maintained for a period of time and the test fluid in the system is subject to thermal expansion, precautions shall be taken to avoid excessive pressure.
When a pressure test is required, it shall be conducted after any heat treatment.
A pneumatic pressure test may be used when it is impracticable to hydrostatically test due to temperature, structural, or process limitations. However, the potential risks to personnel and property of pneumatic testing shall be considered when carrying out such a test. As a minimum, the inspection precautions contained in ASME B 31.3 shall be applied in any pneumatic testing.
During a pressure test, where the test pressure will exceed the set pressure of the safety valve on a piping system, the safety relief valve or valves should be removed or blanked for the duration of the test. As an alternative, each valve disk must be held down by a suitably designed test clamp.
The application of an additional load to the valve spring by turning the adjusting screw is not recommended. Other appurtenances that are incapable of withstanding the test pressure, such as gage glasses, pressure gages, expansion joints, and rupture disks, should be removed or blanked. Lines containing expansion joints that cannot be removed or isolated may be tested at a reduced pressure in accordance with the principles of ASME B 31.3. If block valves are used to isolate a piping system for a pressure test, caution should be used to not exceed the permissible seat pressure as described in ASME B 16.34 or applicable valve manufacturer data.
Upon completion of the pressure test, pressure relief devices of the proper settings and other appurtenances removed or made inoperable during the pressure test shall be reinstalled or reactivated.
4.7 MATERIAL VERIFICATIONS AND TRACEABILTY :
During repairs or alterations of low- to high alloy piping systems, the inspector shall verify the installation of the correct new materials. At the discretion of the owner/user or the inspector, this verification can be either by 100 percent checking or testing in certain critical situations or by sampling a percentage of the materials.
Testing can be accomplished by the inspector or the examiner with the use of suitable portable methods, such as chemical spot testing, optical spectrographic analyzers, or X-ray fluorescent analyzers. Checking can involve verifying test reports on materials, markings on piping components and bolting, and key dimensions.
If a piping system component should fail because an incorrect material was inadvertently substituted for the proper piping material, the inspector shall consider the need for further verification of existing piping materials.
The extent of further verification will depend upon circumstances such as the consequences of failure and the likelihood of further material errors.
4.8 INSPECTION OF VALVES :
Normally, thickness measurements are not routinely taken on valves in piping circuits. The body of a valve is normally thicker than other piping components for design reasons. However, when valves are dismantlted for servicing and repair, the shop should be attentive to any unusual corrosion patterns or thinning and, when noted, report that information to the inspector.
If gate valves are known to be or are suspected of being exposed to corrosion/erosion, thickness readings should be taken between the seats, since this is an area of high turbulence and high stress.
Control valves or other throttling valves, particularly in high pressure drop-and-slurry services, can be susceptible to localized corrosion/erosion of the body downstream of the orifice. If such metal loss is suspected, the valve should be removed from the line for internal inspection. The inside of the downstream mating flange and piping also should be inspected for local metal loss.
Critical check valves should be visually and internally inspected to ensure that they will stop flow reversals.
An example of a critical check valve may be the check valve located on the outlet of a multistage, high head hydro-processing charge pump. Failure of such a check valve to operate correctly could result in over pressuring the piping during a flow reversal. The normal visual inspection method should include :
- Checking to insure that the flapper is free to move, as required, without excessive looseness from wear.
- The flapper stop should not have excessive wear. This will minimize the likelihood that the flapper will move past the top dead central position and remain in an open position when the check valve is mounted in a vertical position.
- The flapper nut should be secured to the flapper bolt to avoid backing off in service.
Leak checks of critical check valves are normally not required.
4.9 INSPECTION OF WELDS IN- SERVICE :
Inspection for piping weld quality is normally accomplished as a part of the requirements for new construction, repairs, or alterations. However, welds are often inspected for corrosion as part of a radiographic profile inspection or as part of internal inspection. When preferential weld corrosion is noted, additional welds in the same circuit or system should be examined for corrosion.
If the noted imperfections are a result of original weld fabrication, inspection and/or engineering analysis is required to assess the impact of the weld quality on piping integrity. This analysis may be one or more of the following
- Inspector judgment.
- Certified welding inspector judgment.
- Piping engineer judgment.
- Engineering fitness-for-service analysis.
Issues to consider when assessing the quality of existing welds include the following
- Original fabrication inspection acceptance criteria.
- Extent, magnitude, and orientation of imperfections.
- Length of time in-service.
- Operating versus design conditions.
- Presence of secondary piping stresses (residual and thermal)
- Potential for fatigue loads (mechanical and thermal).
- Primary or secondary piping system.
- Potential for impact or transient loads.
- Potential for environmental cracking.
- Weld hardness.
In many cases for in-service welds, it is not appropriate to use the random or spot radiography acceptance criteria for weld quality in ASME B 31.3 These acceptance criteria are intended to apply to new construction on a sampling of welds, not just the welds examined, in order to assess the probable quality of all welds (or welders) in the system.
Some welds may exist that will not meet these criteria but will still perform satisfactorily in service.
4.10 INSPECTION OF FLANGED JOINTS :
The markings on a representative sample of newly installed fasteners and gaskets should be examined to determine whether they meet the material specification. The markings are identified in the applicable ASME and ASTM standards. Questionable fasteners should be verified or renewed.
Fasteners should extend completely through their nuts. Any fastener failing to do so is considered acceptably engaged if the lack of complete engagement is not more than one thread.
Flanged and valve bonnet joints should be examined for evidence of leakage, such as stains, deposits, or drips. Process leaks onto flange and bonnet fasteners may result in corrosion or environmental cracking.
This examination should include those flanges enclosed with flange or splash-and-spray guards.
5. FREQUENCY AND EXTENT OF INSPECTION
5.1 GENERAL :
The frequency and extent of inspection piping circuits depend on the forms of degradation that can affect the piping and consequence of a piping failure.
Inspection strategy based on likelihood and consequence of failure, is referred to as risk-based inspection. Piping classification scheme in Section given below is based on the consequence of a failure. The classification is used to establish frequency and extent of inspection. The owner/user may devise a more extensive classification scheme that more accurately assesses consequence for certain piping circuits. The consequence assessment would consider the potential for explosion, fire, toxicity, environmental impact and other potential effects associated with a failure.
After an effective assessment is conducted, the results can be used to establish a piping circuit inspection strategy and more specifically better define the following :
- The most appropriate inspection methods, scope, tools and techniques to be utilized based on the expected forms of degradation;
- The appropriate inspection frequency;
- The need for pressure testing after damage has been incurred or after repairs or modifications have been completed; and
- The prevention and mitigation steps to reduce the likelihood and consequence of a piping failure.
5.2 PIPING SERVICE CLASSES :
All process piping systems shall be categorized into different classes. Such a classification system allows extra inspection efforts to be focused on piping systems that may have the highest potential consequences if failure or loss of containment should occur. In general, the higher classified systems require more extensive inspection at shorter intervals in order to affirm their integrity for continued safe operation. Classifications should be based on potential safety and environmental effects should a leak occur.
5.2.1 CLASS 1 :
Services with the heist potential of resulting in an immediate emergency if a leak were to occur are in Class 1. Such an emergency may be safety or environmental in nature. Examples of Class1 piping include, but are not necessarily limited to, those containing the following :
- Flammable services that may auto-refrigerate and lead to brittle fracture.
- Pressurized services that may rapidly vaporize during release, creating vapors that may collect and form an explosive mixture, such as C2, C3 and C4 streams.
- Hydrogen sulfide (greater than 3 percent weight ) in a gaseous stream.
- Anhydrous hydrogen chloride.
- Hydrofluoric acid.
- Piping over or adjacent to water and piping over public through ways.
5.2.2 CLASS 2 :
Services not included in other classes are in Class 2. This classification includes the majority of unit process piping and selected off-site piping . Typical examples of these services include those containing the following :
- On-site hydrocarbons that will slowly vaporize during release.
- Hydrogen, fuel gas and natural gas
- On-site strong acids and caustics.
5.2.3 CLASS 3 :
Services that are flammable but do not significantly vaporize when they leak and are not located in high activity areas are in Class 3 . Services that dare potentially harmful to human tissue but are located in remote areas may be included din this class. Examples of Class 3 service are as follows :
- On site hydrocarbons that will not significantly vaporize during release.
- Distillate and product lines to and from storage and loading.
- Off-site acids and caustics.
5.3 INSPECTION INTERVALS :
The interval between piping inspections shall be established and maintained using the following criteria :
- Corrosion rate and remaining life calculations.
- Piping service classification.
- Applicable jurisdictional requirements
- Judgment of the inspector, the piping engineer, the piping engineer supervisor, or a corrosion specialist, based don operating conditions, previous inspection history, current inspection results, and conditions that may warrant supplemental inspections covered in 5.4.5 of code.
Thickness measurements should be scheduled based on the calculation of not more than half the remaining life determined from corrosion rates indicated or at the maximum intervals suggested in Table 6-1, whichever is shorter. Shorter intervals may be appropriate under certain circumstances. Prior to using Table 6-1, corrosion rates should be calculated in accordance with 7.13 of code.
The inspection interval must be reviewed and adjusted as necessary after each inspection or significant change in operating conditions. General corrosion, localized corrosion, pitting, environmental cracking, and other forms of deterioration must be considered when establishing the various inspection intervals.
5.4 EXTENT OF VISUAL EXTERNAL AND CUI INSPECTIONS :
External visual inspections, including inspections for corrosion under insulation (CUI), should be conducted at maximum intervals listed in Table 6-1 to evaluate items such as those in Appendix D. The external visual inspection on bare piping is to assess the condition of paint and coating systems, to check for external corrosion, and to check for other forms of deterioration. This external visual inspection for potential CUI is also to assess insulation condition and shall be conducted on all piping systems susceptible to CUI listed in 5.3.3.1 of code
Following the external visual inspection of susceptible systems, additional examination is required for the inspection of CUI. The extent and type of the additional CUI inspection are listed in Table 6-2 . Damaged insulation at higher elevations may result in CUI in lower areas remote from the damage. NDE inspection for CUI should also be conducted as listed in Table 6-2 at suspect locations of 5.3.3.1 (excluding c ) meeting the temperature criteria for 5.3.3.1 (e,f,h).
Radiographic examination or insulation removal and visual inspection is normally required for this inspection at damaged or suspect locations. Other NDE assessment methods may be used where applicable. If the inspection of the damaged or suspect areas has located significant CUI, additional area should be inspected and, where warranted, up to 100 percent of the circuit should be inspected.
The extent of the CUI program described in Table 6-2 should be considered as target levels for piping systems and locations with no CUI inspection experience. It is recognized that several factors may affect the likelihood of CUI to include :
- Local climatic conditions
- Insulation design.
- Coating quality.
- Service conditions.
Facilities with CUI inspection experience may increase or reduce the CUI inspection targets of Table 6-2. An exact accounting of the CUI inspection target is not required. The owner/user may confirm inspection targets with operational history or other documentation.
Piping systems that are known to have a remaining life of over 10 years or that are adequately protected against external corrosion need not be included for the NDE inspection recommended in Table 6-2. However, the condition of the insulating system or the outer jacketing, such as a cold-box shell, should be observed periodically by operating or other personnel. If deterioration is noted, it should be reported to the inspector. The following are examples of these systems :
- Piping systems insulated effectively to preclude the entrance of moisture.
- Jacketed cryogenic piping systems
- Piping systems installed in a cold box in which the atmosphere is purged with an inert gas.
- Piping systems in which the temperature being maintained is sufficiently low or sufficiently high to preclude the presence of water.
5.5 EXTENT OF THICKNESS MEASUREMENT INSPECTION :
To satisfy inspection interval requirements, each thickness measurement inspection should obtain thickness readings on a representative sampling of TMLs on each circuit . This representative sampling should include data for all the various types of components and orientations (horizontal and vertical) found in each circuit. This sampling also must include TMLs with the earliest renewal date as of the previous inspection. The more TMLs measured for each circuit, the more accurately the next inspection date will be projected. Therefore, scheduled inspection of circuits should obtain as many measurements as necessary.
The extent of inspection for injection points is covered in 5.3.1 of code.
-
- EXTENT OF SMALL-BORE, AUXILIARY PIPING, AND THREADED – CONNECTIONS INSPECTIONS :
5.6.1 SMALL BORE PIPING INSPECTION :
Small bore piping (SBP) that is primary process piping should be inspected in accordance with all the requirements of this document.
SBP that is secondary process piping has different minimum requirements depending upon service classification. Class1 secondary SBP shall be inspected to the same requirements as primary process piping. Inspection of Class2 and Class 3 secondary SBP is optional. SBP deadlegs (such das level bridles) in Class 2 and Class 3 systems should be inspected where corrosion has been experienced or is anticipated.
5.6.2 AUXILIARY PIPING DDDDINSPECTION :
Inspection of secondary, auxiliary SBP associated with instruments and machinery is optional. Criteria to consider in determining whether auxiliary SBP will need some form of inspection include the following :
- Classification.
- Potential for environmental or fatigue cracking.
- Potential for corrosion based on experience with adjacent primary
system.
- Potential for CUI.
5.6.3 THREADED-CONNECTIIONS INSPECTION :
Inspection of threaded connections will be according to the requirements listed above for small-bore and auxiliary piping. When selecting TMLs on threaded connection, include only those that can be radio-graphed during scheduled inspection.
Threaded connections associated with machinery and subject to fatigue damage should be periodically assessed and considered for possible renewal with a thicker wall or upgrading to welded components. The schedule for such renewal will depend on several issues, including the following :
- Classification piping
- Magnitude and frequency of vibration.
- Amount of unsupported weight.
- Current piping wall thickness.
- Whether or not the system can be maintained on stream.
- Corrosion rate.
- Intermittent service.
TABLE 6-1—-RECOMMENDED MAXIMUM INSPECTION INTERVALS
Types of Circuit |
Thickness Measurements |
Visual External |
Class 1 |
5 years |
5 years |
Class 2 |
10 years |
5 years |
Class 3 |
10 years |
10 years |
Injection points |
3 years |
By Class |
Soil-to-air interfaces |
—- |
By Class |
Note : Thickness measurements apply to systems for which TMLs have been
established in accordance with 5.5
TABLE D6-2 — RECOMMENDED EXTENT OF CUI INSPECTION
FOLLOWING VISUAL INSPECTION
Approximate Amount of Followup Examination with NDE or Insulation Removal at Areas with Damaged Insulation |
Approximate Amount of CUI Inspection by NDE at Suspect Areas ( 5.3.3.2 ) on Piping Systems within Susceptible Temperature Ranges ( 5.3.3.2 e.f.h ) |
|
Pipe Class |
||
1 |
75% |
50% |
2 |
50% |
33% |
3 |
25% |
10% |
6. INSPECTION DATA EVALUATION
6.1 CORROSION RATE DETERMINATION :
-
-
- REMAINING LIFE CALCULATIONS :
-
The dreaming life of the piping system shall be calculated from the following formula :
t actual – t minimum
Remaining life (years) = —————————–
Corrosion rate
[inches (mm) per year]
where :
t actual = the actual minimum thickness, in inches (mm),determined at the
time of inspection as specified 5.6
t minimum = the minimum required thickness, in inches (mm) for the limiting
section or zone.
The long term (L.T.) corrosion rate of piping circuits shall be calculated from the following formula :
Corrosion rate (L.T.) = t initial – t last
———————————
time (years) between last
and initial inspections
The short term (S.T.) corrosion rate of piping circuits shall be calculated from the following formula :
Corrosion rate (S.T.) = t previous – t last
—————————
time (years) between last
and previous inspections
Long term and short term corrosion rates should be compared to see which results in the shortest remaining life.
6.1.2 EXISTING PIPING SYSTEMS :
Corrosion rates shall be calculated on either a short term or a long term basis. For the short term calculation, readings from the two most recent inspections shall be used. For the long term calculation, wall thicknesses from the most recent and initial (or nominal) inspections shall be used. In most cases, the higher of these two rates should be used to estimate remaining life and so set the next inspection interval.
If calculations indicate that an inaccurate rate of corrosion has been assumed, the rate to be used for the next period shall be adjusted to agree with the actual rate found.
6.2 MAXIMUM ALLOWABLE DWORKING PRESSURE DETERMINATION :
The maximum allowable working pressure (MAWP) for the continued use of piping systems shall be established using the applicable code. Computations may be made for known materials if all the following essential details are known to comply with the principles of the applicable code :
- Upper and/or lower temperature limits for specific materials.
- Quality of materials and workmanship.
- Inspection requirements.
- Reinforcement of openings.
- Any cyclical service requirements.
For unknown materials, computations may be made assuming the lowest grade material and joint efficiency in the applicable code. When the MAWP is recalculated, the wall thickness used in these computations shall be the actual thickness as determined by inspection (see definition) minus twice the estimated corrosion loss before the date of the next inspection. Allowance shall be made for the other loadings in accordance with the applicable code. The applicable code allowances for pressure and temperature variations from MAWP are permitted provided all of the associated code criteria are satisfied.
6.3 MINIMUM REQUIRED THICKNESS DETERMINATION :
The minimum required pipe wall thickness, or retirement thickness, shall be based on pressure, mechanical, and structural considerations using the appropriate design formulas and code allowable stress. Consideration of both general and localized corrosion shall be included. For services with high potential consequences if failure were to occur, the piping engineer should consider increasing the required minimum thickness above the calculated minimum thickness to provide for unanticipated or unknown loadings, undiscovered metal loss, or resistance to normal abuse.
6.4 REPORTING AND RECORDS FOR PIPING SYSTEM INSPECTION
Any significant increase in corrosion rates shall be reported to the owner/user for appropriate action.
The owner/user shall maintain appropriate permanent and progressive records of each piping system covered by API 570. These records shall contain pertinent data such as piping system service; classification; identification numbers; inspection intervals; and documents necessary to record the name of the individual performing the testing, the date, the types of testing, the results of thickness measurements and other tests, inspections, repairs (temporary and permanent), alterations, or rerating. Design information and piping drawings may be included. Information on maintenance activities and events affecting piping system integrity also should be included. The date and results of required external inspections shall be recorded. (see API RP 574 for guidance on piping inspection records).
The use of a computer based system for storing, calculating, and analyzing data should be considered in view of the volume of data that will be generated as part of a piping test-point program. Computer programs are particularly useful for the following :
- Storing the actual thickness reading.
- Calculating short and long term corrosion rates, retirement dates, MAWP, and reinspection intervals on a test point by test point basis.
- Highlighting areas of high corrosion rates, circuits over-due for inspection, close to retirement thickness, and other information.
7. REPAIRS, ALTERATIONS, RERATING
7.1 REPAIRS AND ALTERATIONS :
The principles of ASME B31.3 or the code to which the piping system was built shall be followed.
7.1.1 AUTHORIZATION :
All repair and alteration work must be done by a repair organization as defined in Section 3 and must be authorized by the inspector prior to its commencement. Authorization for alteration work to a piping system may not be given without prior consultation with, and approval by, the piping engineer. The inspector will designate any inspection hold points required during the repair or alteration sequence. The inspector may give prior general authorization for limited or routine repairs and procedures, provided the inspector is satisfied with the competency of the repair organization.
7.1.2 APPROVAL :
All proposed methods of design, execution, materials, welding procedures, examination, and testing must be approved by the inspector or by the piping engineer, as appropriate. Owner/user approval of on stream welding is required.
Welding repairs of cracks that occurred in service should not be attempted without prior consultation with the piping engineer in order to identify and correct the cause of the cracking. Examples are cracks suspected of being caused by vibration, thermal cycling, thermal expansion problems, and environmental cracking.
The inspector shall approve all repair and alteration work at designated hold points and after the repairs and alterations have been satisfactorily completed in accordance with the requirements of API 570
7.1.3 WELDING REPAIRS (DDINCLUDING ON0STREAM) :
7.1.3.1 TEMPORARY REPAIRS :
For temporary repairs, including on steam, a full encirclement welded split sleeve or box type enclosure designed by the piping engineer may be applied over the damaged or corroded area. Longitudinal cracks shall not be repaired in this manner unless the piping engineer has determined that cracks would not be expected to propagate from under the sleeve. In some cases, the piping engineer will need to consult with a fracture analyst.
If the repair area is localized (for example, pitting or pinholes) and the specified minimum yield strength (SMYS) of the pipe is not more than 40,000 psig (275,800 kPa), a temporary repair may be made by fillet welding a properly designed split coupling or plate patch over the pitted area (See 7.2.3 for design considerations and Appendix C for an example ) The material for the repair shall match the base metal unless approved by the piping engineer.
For minor leaks, properly designed enclosures may be welded over the leak while the piping system is in service, provided the inspector is satisfied that adequate thickness remains in the vicinity of the weld and the piping component can withstand welding without the likelihood of further material damage, such as form caustic service.
Temporary repairs should be removed and replaced with a suitable permanent repair at the next available maintenance opportunity. Temporary repairs may remain in place for a longer period of time only if approved and documented by the piping engineer.
7.1.3.2 PERMANENT REPAIRS :
Repairs to defects found in piping components may be made by preparing a welding groove that completely removes the defect and then filling the groove with weld metal deposited din accordance with 7.2
Corroded areas may be restored with weld metal deposited din accordance with 7.2 Surface irregularities and contamination shall be removed before welding. Appropriate NDE methods shall be applied after completion of the weld.
If it is feasible to take the piping system out of service, the defective area may be removed by cutting out a cylindrical section and replacing it with a piping component that meets the applicable code.
Insert patches (flush patches) may be used to repair damaged or corroded areas if the following requirements are met :
- Full penetration groove welds are provided.
- For Class 1 and Class 2 piping systems, the welds shall be
100 percent radio-graphed or ultrasonically tested using NDE procedures that are approved by the inspector.
- Patches may be any shape but shall have rounded corners
(1 inch (25mm) minimum radius)
7.1.4 NON-WELDING REPAIRS (ON STREAM) :
Temporary repairs of locally thinned sections or circumferential linear defects may be made on stream by installing a properly designed and fabricated bolted leak clamp. The design shall include control of axial thrust loads if the piping component being clamped is (or may become) insufficient to control pressure thrust. The effect of clamping (crushing) forces on the component also shall be considered.
During turnarounds or other appropriate opportunities, temporary leak sealing and leak dissipating devices, including valves, shall be removed and appropriate actions taken to t\restore the original integrity of the piping system. The inspector and/or dipping engineer shall be involved in determining repair methods and procedures.
Procedures that include leak sealing fluids (pumping) for process piping should be reviewed for acceptance by the inspector or piping engineer. The review should take into consideration the compatibility of the sealant with the leaking material; the pumping pressure on the clamp (especially when re[pumping); the risk of sealant affecting downstream flow meters, relief valves, or machinery, the risk of subsequent leakage at bolt threads causing corrosion or stress corrosion cracking of bolts; and the number of times the seal area is re-pumped.
7.2 WELDING AND HOT TAPPING :
All repair and alteration welding shall be done in accordance with the principles of ASME B 31.3 or the code to which the piping system was built.
Any welding conducted on piping components in operation must be done in accordance with API Publ 2201. The inspector shall use as a minimum the ‘ Suggested Hot Tap Checklist” contained in API Publication 2201 for hot tapping performed on piping components.
7.2.1 PROCEDURES, QUALIFICATIONS, AND RECORDS :
The repair organization shall use welders and welding procedures qualified in accordance with ASME B31.3 or the code to which the piping was built.
The repair organization shall maintain records of welding procedures and welder performance qualifications. These records shall be available to the inspector prior to the start of welding.
7.2.2 PERHEATING AND POSTWELD HEAT TREATMENT :
7.2.2.1 PREHEATING :
Preheat temperature used in masking welding repairs shall be in accordance with the applicable code and qualified welding procedure. Exceptions for temporary repairs must be approved by the piping engineer.
Preheating to not less that 300oF (150oC) may be considered as an alternative to postweld heat treatment (PWHT) for alterations or repairs of piping systems initially postweld heat heated as a code requirement (see note). This applies to piping constructed of the P-1 steels listed in ASME B31.3. P-3 steels , with the exception of Mn-Mo steels, also may receive the 300oF(150oC) minimum preheat alternative when the piping system operating temperature is high enough to provide reasonable toughness and when there is no identifiable hazard associated with pressure testing , shutdown, and startup. The inspector should determine that the m9inimum preheat temperature is measured and maintained. After welding, the joint should immediately be covered with insulation to slow the cooling rate.
NOTE : Preheating may not be considered as an alternative to environmental cracking prevention.
Piping systems constructed of other steel initially requiring PWHT normally are postweld heat treated if alterations or repairs involving pressure retaining welding are performed. The use of the preheat alternative requires consultation with the piping engineer who should consider the potential for environmental cracking and whether the welding procedure will provide adequate toughness. Examples of situations where this alternative could be considered include seal welds, weld metal buildup of thin area, and welding support clips.
7.2.2.2 POSTWELD HEAT TREATMENT :
PWHT of piping system repairs or alterations should be made using the applicable requirements of ASME B31.3 or the code to which the piping was built. See 7.2.2.1 for an alternative preheat procedure for some PWHT requirements. Exceptions for temporary repair must be approved by the piping engineer.
Local PWHT may be substituted for 360- degree banding on local repairs on all materials, provided the following precautions and requirements are applied.
- The application is reviewed, and a procedure is developed
by the piping engineer.
- In evaluating the suitability of a procedure, consideration
shall be given to applicable factors, such as base metal thickness, thermal gradients, material properties, changes resulting from PWHT, the need for full penetration welds, and surface and volumetric examinations after PWHT. Additionally, the overall and local strains and distortions resulting from the heating of a local restrained area of the piping wall shall be considered in developing and evaluating PWHT procedures.
- A preheat of 300oF (150oC), or higher as specified by
specific welding procedures, is maintained while welding.
- The required PWHT temperature shall be maintained for a
distance of not less than two times the base metal thickness measured form the weld. The PWHT temperature shall be monitored by a suitable number of thermocouples (a minimum of two) based on the size and shape of the area being heat treated.
- Controlled heat also shall be applied to any branch
connection or other attachment within the PWHT area.
- The PWHT is performed for code compliance and not for
environmental cracking resistance.
7.2.3 DESIGN :
Butt joints shall be full penetration groove welds.
Piping components shall be replaced when repair is likely to be inadequate. New connections and replacement s shall be designed and fabricated according to the principles of the applicable code. The design of temporary enclosures and repairs shall be approved by the piping engineer.
New connections may be installed on piping systems provided the design, location, and method of attachment conform to the principles of the applicable code.
Fillet-welded patches require special design considerations, especially relating to weld-joint efficiency and crevice corrosion. Fillet-welded patches shall be designed by the piping engineer. A patch may be applied to the external surfaces of piping, provided it is in accordance with 7.1.3 and meets either of the following requirements. :
- The proposed patch provides design strength equivalent to a reinforced opening designed according to the applicable code.
- The proposed patch is designed to absorb the membrane strain of the part in a manner that is in accordance with the principles of the applicable code, if the following criteria are met :
- The allowable membrane stress is not exceeded in the piping part
or the patch.
-
- The strain in the patch does not result in fillet weld stresses exceeding allowable stresses for such welds.
- An overlay patch shall have rounded corners (se Appendix C)
7.2.4 MATERIALS :
The materials used in making repairs or alterations shall be of known weldable quality, shall conform to the applicable code, and shall be compatible with the original materials. For material verification requirements see 4.8
7.2.5 NON-DESTRUCTIVE EXAMINATION :
Acceptance of a welded repair or alteration shall include NDE in accordance with the applicable code and the owner/user’s specification, unless otherwise specified in API 570
7.2.6 PRESSURE TESTING :
After welding is completed, pressure test in accordance with 4.7 shall be performed if practical and deemed necessary by the inspector. Pressure tests are normally required after alterations and major repairs. When a pressure test is not necessary or practical, NDE shall be utilized in lieu of a pressure test. Substituting special procedures for a pressure test after an alteration or repair may b e done only after consultation with the inspector and the piping engineer.
When it is not practical to perform a pressure test of a final closure weld that joins a new or replacement section of piping to an existing system, all of the following requirements shall be satisfied :
- The new or replacement piping is pressure tested.
- The closure weld is a full penetration butt-weld between a weld neck flange and standard piping component or straight sections of pipe of equal diameter and thickness, axially aligned ( not miter cut ), and of equivalent materials. Acceptable alternatives are
- slip-on flanges for design cases upto Class 150 and 500oF,
(260oC) and
-
- socket welded flanges or socket welded unions for sizes NPS 2 or
less and design cases upto Class 150 and 500oF (260oC). A spacer designed for socket welding or some other means shall be used to establish a minimum 1/16 inch (1.6 mm ) gap. Socket welds shall be per ASME B31.3 and shall be a minimum of two passes.
- Any final closure butt-weld shall be of 100 percent radiographic quality;
OR angle beam ultrasonics flaw detection may be used, provided the appropriate acceptance criteria have been established.
- MT or PT shall be performed on the root pass and the completed weld for
butt-welds and on the completed weld for fillet welds.
7.3 RERATING
Rerating piping systems by changing the temperature rating or the MAWP may be done only after all of the following requirements have been met :
- Calculations are performed by the piping engineer or the inspector.
- All ratings shall be established in accordance with the requirements of the code to which the piping system was built or by computation using the appropriate methods in the latest edition of the applicable code.
- Current inspection records verify that the piping system is satisfactory for the proposed service conditions and that the appropriate corrosion allowance is provided.
d. Rerated piping systems shall be leak tested in accordance with the code to which the piping system was built or the latest edition of the applicable code for the new service conditions, unless documented records indicate a previous leak test was performed at greater than or equal to the test pressure for the new condition. An increase in the rating temperature that does not affect allowable tenside stress does not require a leak test.
- The piping system is checked to affirm that the required pressure relieving devices are present, are set at the appropriate pressure, and have the appropriate capacity at set pressure.
f. The piping system rerating is acceptable to the inspector or piping engineer.
g. All piping components in the system (such as valves, flanges, bolts, gaskets, packing, and expansion joints) are adequate for the new combination of pressure and temperature.
h. Piping flexibility is adequate for design temperature changes.
i. Appropriate engineering records are updated.
j. A decrease in minimum operating temperature is justified by impact test results, if required by the applicable code.
8. INSPECTION OF BURIED PIPING
Inspection of buried process piping is different from other process piping inspection because significant external deterioration can be caused by corrosive soil conditions. Since the inspection is hindered by the inaccessibility of the affected areas of the piping, the inspection of buried piping is treated in a separate section of API 570.
8.1 TYPES AND METHODS OF INSPECTION
-
-
- Above Grade Visual Surveillance :
-
Indications of leaks in buried piping may include a change in the surface contour of the ground, discoloration of the soil, softening of paving asphalt, pool formation, bubbling water puddles, or noticeable odor. Surveying the route of buried piping is one method of identifying problem areas.
-
-
- Close Interval Potential Survey :
-
The close interval potential survey performed at ground level over the buried pipe can be used to locate active corrosion points on the pipe’s surface.
Corrosion cells can form on both bare and coated pipe where the bare steel contacts the soil. Since the potential at the area of corrosion will be measurably different from an adjacent area on the pipe, the location of the corrosion activity can be determined by this survey technique.
-
-
- Pipe Coating Holiday Survey :
-
The pipe coating holiday survey can be used to locate coating defects on buried coated pipes, and it can be used on newly constructed pipe systems to ensure that the coating is intact and holiday free. More often it is used to evaluate coating serviceability for buried piping that has been in service for an extended period of time.
8.1.4 Soil Resistivity :
Corrosion of bare or poorly coated piping is often caused by a mixture of different soils in contact with the pipe surface. The corrosiveness of the soils can be determined by a measurement of the soil resistivity. Lower levels of resistivity are relatively more corrosive than higher levels, especially in areas where the pipe is exposed to significant changers in soil resistivity.
8.1.5 Cathodic Protection Monitoring :
Cathodically8 protected buried piping should be monitored regularly to assure adequate levels of protection. Monitoring should include periodic measurement and analysis of pipe to soil potentials by personnel trained and experienced in cathodic protection system operation. More frequent monitoring of critical cathodic protection components, such as impressed current rectifiers, is required to ensure reliable system operation.
8.1.6 Inspection Methods :
Several inspection methods are available. Some methods can indicate the external or wall condition of the piping, whereas other methods indicate only the internal condition. Examples are as follows :
-
- Intelligent pigging. This method involves the movement of a device (pig) through the piping either while it is in service or after it has been removed from service. Several types of devices are available employing different methods of inspection.
- Video cameras. Television cameras are available that cana be inserted into the piping. These cameras may provide visual inspection information on the internal condition of the line.
- Excavation. In many cases, the only available inspection method that can be performed is unearthing the piping in order to visually inspect the external condition of the piping and to evaluate its thickness and internal condition.
8.2 FREQUENCY AND EXTENT OF INSPECTION :
8.2.1 Above-Grade Visual Surveillance :
The owner/ user should, at approximately 6 month intervals survey the surface conditions on and adjacent to each pipeline path.
8.2.2 Pipe to Soil Potential Survey :
A close interval potential survey on a cathodically protected line may be used to verify that the buried piping has a protective potential throughout its length. For poorly coated pipes where cathodic protection potentials are inconsistent, the survey may be conducted at 5 year intervals for veritication of continuous corrosion control.
For piping with no cathodic protection or in areas where leaks have occurred due to external corrosion, a pipe to soil potential survey may be conducted along the pipe route. The pipe should be excavated at sites where active corrosion cells have been located to determine the extent of corrosion damage.
8.2.3 Pipe Coating Holiday Survey :
The frequency of pipe coating holiday surveys is usually based on indications that other forms of corrosion control are ineffective. For example, on a coated pipe where there is gradual loss of cathodic protection potentials or an external corrosion leak occurs at a coating defect, a pipe coating holiday survey may be used to evaluate the coating.
8.2.4 Soil Corrosivity :
For piping buried in lengths greater than 100 feet ( 30 m ) and not cathodically protected, evaluations of soil corrosivity should be performed at 5 year intervals. Soil resistivity measurements may be used for relative classification of the soil corrosivity.
8.2.5 Cathodic Protection :
If the piping is cathodically protected, the system should be monitored at intervals in accordance with Section 10 of NACE RP0169 or Section 11 of API RP 651.
8.2.6 External and Internal Inspection Intervals :
If internal corrosion of buried piping is expected as a result of inspection on the above grade portion of the line, inspection intervals and methods for the buried portion should be adjusted accordingly. The inspector should be aware of and consider the possibility of accelerated internal corrosion in deadlegs.
The external condition of buried piping that is not cathodically protected should be determined by either pigging, which can measure wall thickness or by excavating according to the frequency given in Table 9-1. Significant external corrosion detected by pigging or by other means may require excavation and evaluation even if the piping is cathodically protected.
Piping inspected periodically by excavation shall be inspected in lengths of 6 feet –8 feet ( 2.0 m-2.5 m ) at one or more locations judged to be most suspectible to corrosion. Excavated piping should be inspected full circumference for the type and extent of corrosion ( pitting or general ) and the condition of the coating.
If inspection reveals damaged coating or corroded piping, additional piping shall be excavated until the extent of the condition is identified. If the average wall thickness is at or below retirement thickness, it shall be repaired or replaced.
If the piping is contained inside a casing pipe, the conditional of the casing should be inspected to determine if water and/ or soil has entered the casing. The inspector should verify the following :
-
- both ends of the casing extend beyond the ground line;
- the ends of the casing are sealed if the casing is not self-draining; and
c. the pressure carrying pipe is properly coated and wrapped.
8.2.7 Leak Testing Intervals :
An alternative or supplement to inspection is leak testing with liquid at a pressure atleast 10 percent greater than maximum operating pressure at intervals one-half the length of those shown in Table 9-1 for piping not cathodically protected and at the same intervals as shown in Table 9-1 for cathodically protected piping. The leak test should be maintained for a period of 8 hours.
Four hours after the initial pressurization of the piping system, the pressure should be noted and, if necessary, the line repressurized to original test pressure and isolated from the pressure source.
If, during the remainder of the test period, the pressure decreases more than 5 percent, the piping should be visually inspected externally and/ or inspected internally to find the leak and assess the extent of corrosion. Sonic measurements may be helpful in locating leaks during leak testing.
Buried piping also may be surveyed for integrity by using temperature-corrected volumetric or pressure test methods.
Table 9-1 Frequency of Inspection for Buried Piping
Without Effective Cathodic Protection
Soil Resistivity( ohm-cm ) |
Inspection Interval ( years ) |
< 2,000 |
5 |
2,000 to 10,000 |
10 |
> 10,000 |
15 |
Other alternative leak test methods involve acoustic emission examination and the addition of a tracer fluid to the pressurized line ( such as helium or sulfur hexafloride ). If the tracer is added to the service fluid, the owner/ user shall confirm suitability for process and product.
8.3 REPAIRS TO BURIED PIPING SYSTEMS :
8.3.1 Repairs to Coatings :
Any coating removed for inspection shall be renewed and inspected appropriately.
For coating repairs, the inspector should be assured that the coating meets the following criteria :
-
- It has sufficient adhesion to the pipe to prevent under film migration of
moisture.
-
- It is sufficiently ductile to resist cracking.
- It is free of voids and gaps in the coating ( holidays ).
- It has sufficient strength to resist damage due to handling and soil stress.
- It can support any supplemental cathodic protection.
In addition, coating repairs may be tested using a high voltage holiday detector. The detector voltage shall be adjusted to the appropriate value for the coating material and thickness. Any holidays fould shall be repaired and retested.
8.3.2 Clamp Repairs :
If piping leaks are clamped and reburied, the location of the clamp shall be logged in the inspection record and may be surface marked.
Both the marker and the record shall note the date of installation and the location of the clamp. All clamps shall be considered temporary. The piping should be permanently repaired at the first opportunity.
8.3.3 Welded Repairs :
Welded repairs shall be made in accordance in 8.2 of Code.
8.3.4 Records :
Record systems for buried piping should be maintained in accordance with 7.6 of Code. In addition, a record of the location and date of installation of temporary clamps shall be maintained.
******
RECOMMENDED PRACTICE API- 574
1 REASONS FOR INSPECTION
-
- GENERAL
- The primary purpose of inspection is to identify active deterioration mechanisms and to specify repair, replacement, or future inspections for affected piping.
- By developing a database of inspection history, the user may predict and recommend future repairs and replacements.
- The user can act to prevent or retard further deterioration and, most importantly, prevent loss of containment.
- This should result in increased operating safety, reduced maintenance cost, and more reliable and efficient operations.
- API 570, Piping Inspection Code provides the basic requirements for such an inspection program. This recommended practice supplements API 570 by providing piping inspectors with information that can improve skill and increase basic knowledge and practices.
- SAFETY
- A leak or failure in a piping system may be only a minor inconvenience, or it may become a potential source of fire or explosion, depending on the temperature, pressure, contents, and location of the piping.
- Adequate inspection is a prerequisite for maintaining the lines containing flammable fluids and toxic chemicals in a safe operable condition.
- Several safety regulations mandate piping, that carries hazardous chemicals be inspected according to accepted codes and standards, which includes API 570.
- RELIABILITY AND EFFICIENT OPERATION
- Thorough inspection and analysis and the use of historical records of piping systems are essential to the attainment of acceptable reliability, efficient operation, and optimum on stream service.
- Piping replacement schedules can be developed to coincide with planned maintenance turnaround schedules through methodical forecasting of piping service life.
- REGULATORY REQUIREMENTS
- Regulatory requirements usually cover only those conditions that affect safety and environmental concerns.
- Inspection groups in the Petrochemical industry familiar with the industry’s problems inspect for other conditions that adversely affect plant operation.
- Each plant should be familiar with the local requirements for process piping inspection.
2 CORROSION MONITORING OFPROCESS PIPING
- The single most frequent reason for replacing piping is thinning due to corrosion.
- The key to the effective monitoring of piping corrosion is identifying and establishing thickness monitoring locations (TMLs) .
- TMLs are designated areas in the piping system where thickness measurements are periodically taken. By taking repeated measurements and recording at the same points over extended periods, corrosion rates can more accurately be calculated.
Some of the factors to consider when establishing the corrosion monitoring plan for process piping are :
-
- Classifying the piping in accordance with API 570.
- Categorising the piping into circuits of similar corrosion behavior.
- Identifying susceptible locations where accelerated corrosion is expected.
- Accessibility of the TMLs for monitoring.
PIPING CIRCUITS:
- A piping circuit is a section of piping of which all points are exposed to an environment of similar corrosivity and which is of similar design conditions and construction material.
- By identifying like environments as circuits, the spread of calculated corrosion rates of the TMLs in each circuit is reduced.
- Corrosion rates are normally increased at areas of increased velocity and/ or turbulence. Elbows, reducers, tees, control valves, and orifices are examples of piping components where accelerated corrosion may occur because of increased velocity and / or turbulence.
- Such components are normally areas to locate additional TMLs in a piping circuit.
- Areas of no flow, such as deadlegs ( Section 6.3.2 ) may cause accelerated corrosion and may need additional TMLs.
INJECTION POINTS:
- Injection points are some times subject to accelerate or localized corrosion.
- Injection points may be treated as separate inspection circuits and need to be inspected thoroughly on a regular schedule.
*********
FREQUENCY AND TIME OF INSPECTION
GENERAL:
The frequency of piping inspections should be determined by the following conditions :
-
- The consequence of a failure ( piping classification ),
- The degree of risk ( likelihood and consequence of a
failure )
-
- The amount of corrosion allowance remaining
- The historical data available
- Regulatory requirements.
API 570 requires classifying piping systems according to the consequences of failure.
The frequency and thoroughness of piping inspections will range from often and extensive in low piping classes where deterioration is extreme, to seldom and cursory in high piping classes in non-corrosive services.
INSPECTION WHILE EQUIPMENT IS OPERATING
An effective, program of piping inspection will include obtaining as many of the required wall thickness measurements as possible while a plant is on stream. Both ambient and high temperature ultrasonic thickness measurements may be taken. On most piping, wall thickness radiographs can be taken independently through undisturbed insulation. Radiographs can also be used to identify corroded areas.
On stream inspection can reduce downtime by the following means :
- Extending process runs by assuring piping conditions are suitable for continued operation.
- Permitting fabrication of replacement piping before a shutdown.
- Eliminating unnecessary work and reducing shutdown personnel requirements; for example, personnel who are otherwise used to remove insulation and break flanges for inspection during the turnaround can be made available for other work.
- Aiding maintenance planning to reduce surges in work-load, thus, stabilizing personnel requirements.
INSPECTION WHILE EQUIPMENT IS SHUT DOWN
Inspections that cannot be made while the equipment is operating must be made when the system is shut down. In addition, when piping is opened for any reason, it should be inspected internally as far as accessibility permits. Adequate follow up inspections should be conducted to determine the causes of defects, such as leaks, misalignment, vibration, and swaying that were detected while the unit was operating.
*****
SAFETY PRACTICES IN INSPECTION
( API 574 – CHAPTER 8 )
A ) SAFETY PRECAUTIONS ( 8.1 )
Procedures for segregation of piping, installation of blinds etc. shall be integral part of safety practices of the plant. In general piping to be opened shall be :
- Isolated from all sources of harmful liquids and gases, vapours.
- Purging to remove all oil and toxic gases
- Precautions should be taken before hammer testing which may cause cracks, failures, or allow contents to be released.
B ) PREPARATORY WORK ( 8.2 )
All possible preparatory work should be done before scheduled start of inspection which include :
- Scaffolds erection
- Excavation of buried piping at inspection points
- Check availability and working condition of inspection tools required
- Availability and condition of equipments and clothing for personnel safety
- Necessary warning signs
- Barricades
INSPECTION PROCEDURES
( API-574 – CHAPTER 10 )
A ) INSPECTION DURING OPERATION :
- Leakage spots ( corrosion product build up at pipe support and clamps contact area )
- Signs of misalignment, vibrations
- Supports and vibrations
d External condition of piping insulation
a ) Leakage spots: :
Leaks in utility piping may not be hazardous.
Leaks in hot toxic, volatile gases may be dangerous. leak drippings may corrode piping below. attention shall be given to flange joints, packing glands,
expansion joints, valve bonnets etc. Leaks may be stopped or reduced by tightening flanges, packing glands. Isolate the piping and attend to it if situation warrants.
b ) Misalignment
- Pipes dislodged from supports,
- Shifting of base plate, breaking of foundation
- Pipe supports forced out of plumb
- Expansion joints excessively damaged
- Equipment walls at terminal points showing deformation
- Excessive repair of bearings of rotating machinery to which piping is connected.
c ) Supports & Vibrations
- Physical damage, distortion , movement of supports, failure or loosening of foundation bolts
- Restricted operations of pipe rollers, slide plates
- Broken pipe anchors
- Damage to small branch line due to thermal movement of larger lines ( X-Y-Z directions )
- If excessive vibrations are observed in a piping welds shall be inspected for cracks, especially at points of restraints, anchors
- Additional supports may be considered for poorly supported lines
- Seek advice of Consultant / Piping Engineer to eliminate / dampen the vibrations
d ) External Corrosion
- Due to defects in Coating, painting or damaged insulation
- Survey for CUI shall be done in operation to the extent possible
- Lines that sweat, liquid spills, condensate (relief valves down stream ) may cause external corrosion
- Hot spots due to damage of internal refractory lining.
- Night glow or balding of pipes may be seen
- To arrest balding external cooling by water, air, may be used till system is removed for maintenance
INSPECTION DURING SHUT DOWN
- Visual inspection after pipe is opened at various flanged joints and valves. ( Flash light and extension lights and mirrors magnifying glasses may be used ) may reveal following :
a ) Excessive corrosion / Erosion, fouling
b ) Cracks ( welds are most prone areas ) investigate cracks further by blast cleaning and wet fluorescent MPI, LPI and UT
c ) Gasket faces of flanges shall be checked for scratches, cuts, pitting etc ( Ref. ASME B 16.5 Para 6.0 )
d ) Valves, bodies to be checked for thickness, flanged ends for defects © above and other parts ( seat stem spring for damage and breakage, check studs and nuts for deformation, shaving of threads etc.
e ) Check threaded joints for loose threads, corrosing, cross threading, ensure new Teflon tapes are used while putting back in place
f ) Areas seen as hot spots externally shall be inspected for damage internally and repaired
g ) Damage to internal painting, coating, cladding shall be surveyed and repaired
PRESSURE TESTS
1 ) Piping systems subject to pr. Test include :
- Underground lines and other inaccessible piping
- Water and other non-hazardous utility lines
- Long oil-transfer lines in arcas where a leak or spill would not be hazardous to personnel or harmful to the environment.
- Complicated manifold systems.
- Small piping and tubing systems.
- All systems after a chemical cleaning operation.
2 ) API 570 sec. 3.7 gives guidelines for preparing piping for pressure Testing.
3 ) During liquid pressure Test, all air must be expelled, or else failure could be more violent than liquid-full system.
4 ) Avoid over pressure
– yield limit may exceed. Use calibrated pressure Gauges (gauge range 1 ½ to 4 times test pressure). However, 2 to 3 times Pt is preferred.
5 ) Fluids used –
- water – (preferred )
- Liquid products normally carried if not toxic or inflammable
- Steam
- Air, Nitrogen, Helium
6 ) Water as test medium may not be suitable for
- Acid lines
- Vacuum lines ( vertical lines )
- Corrosion of Austentic Steels ( SCC )
- May freeze in cold weather
7 ) Steam may be used particularly if it is used for heating or purging. However,
- difficulty in draining condensate from all areas and
- Compressibility (unsafe )
- Inaccessibility and burn to personnel on leakage could put severe restrictions. All precautions of pneumatic testing stated in ASME B 31.3 must be observed for steam testing as well.
Pneumatic tests:
- Pneumatic tests with soap solutions are permissible. However, best gaseous mediums would be inert gases like nitrogen Helium etc.
- Helium is ideal as it can detect minutest cracks which otherwise would be missed in water, air, steam or Nitrogen testing.
- Helium leakage in ppm levels can be detected by Helium sniffers.
Hence they are used when service conditions are particularly critical.
HAMMER TESTING
- Hammer testing is old method to detect unexpected thin sections.
- Cast Irons and Caustic lines inside coated lines should not be hammered
- Requires personal expertise
- Hammer test shall be followed up by other methods like UT at suspected areas.
*******
NSPECTION OF UNDERGROUND PIPING
1 In addition to product corrosion the Underground Piping is exposed to soil corrosion. Following methods are adopted in inspection of Underground Piping :
- A survey above ground of the piping route could show discoloration of soil, pool formation, noticeable odor etc. for which corrosion and leak may be probable cause.
All Pipes are inspected at and just below the point where they enter earth, concrete, asphalt etc. since these areas are more prone to corrosion.
- Close internal potential survey – This technique measures the potential of the pipe to the soil directly over pipe at fixed intervals ( 5 ft, 10 ft. etc. )
Pipe contact can be made at an above ground attachment. Sudden change of P/S potential is location for further scrutiny ( by excavation, if required ).
- Holiday pipe coating survey is employed to ensure that coating is intact and holiday free.This technique is used for predicting corrosion activity in specific area and coating replacement decisions.
- Soil resistivity testing : This technique is used for relative classification of the soil resistivity.Lower levels of resistivity are more corrosive than higher levels.
- Cathodic Protection Monitoring : This shall be carried out regularly to assure adequate levels of protection.
Periodic monitoring includes checking condition of sacrifical anodes or rectifier currents in impressed current system.
- Intelligent Pigging : This method involves movement of device (pig) through piping. However, this technique requires line to be free from restrictions (i.e. full bore valves, absence of reduces) and five diameter bankds. Very effective technique in long distance piping. However, blant piping has limited use.
- Video Cameras : These provide direct visual information on internal condition of pipe.
- Excavation : Sometimes the only available method is unearthing of piping for visual inspection of external condition of piping and evaluate its thickness.
- Leak testing : VIG lines that can not be visually inspected should be periodically.
- Pressure decay method : Pressurise the line, block it, remove source of pressure, monitoring over a period of time will provide indicating of pressure tightness. Performance can be confirmed by leak simulation.
- Volume in/ volume out method uses volumetric measuring meter at each end of the line. Performance can be determined by leak simulation.
- Single point volumetric method is similar to pressure decay method except that a graduated cylinder is employed to check level reduction by leakage.
- Maker chemical (tracer) may be added to line to detect leak and soil gas samples near line are tested for presence of maker chemicals.
- Accoustic emission technology detects and locates leaks by sound created by leak and detected by senser.
********
RETIREMENT THICKNESS FOR PIPES
( API 574 Par. 11.1 )
1 ) Thickness formulas from ASME B31.3 shall be used.
t = tm + A
PD
Where tm = —————- + A or,
2SE +2PY
PD
tm = ——– … ( Barlow formula)
2SE
( for t > D/6 or P/SE > 0.385, special considerations
required )
In practice t is generally higher due to rounding up of pipe
schedule to higher number.
2 ) For low pressure and temperatures, above thicknesses could be so small for sufficient structural strength for span and other UDL ( insulation, snow etc. )
3 ) Absolute minimum thickness ( ta ) shall be determined based on internal pressure, sag, buckling etc.
Pipe should not be permitted to deteriorate below this thickness ( ta ), which is called “Retirement Thickness” i.e. Pipe shall be retired ( replaced ) at this thickness.
4 ) Above calculations shall be performed by or under direction of Piping Engineer.
RETIREMENT THICKNESSFOR VALVES & FLANGED FITTINGS:
( API 574 – Para 11.2 )
1.Stress pattern for valves and flanges in quite complex due to simultaneous effects of :
- Internal pressure
- Bolts load forces and movements
- Stress concentration due to shape
- ASME B 16.34 determines that min. Valve wall thickness (tv) shall be
tv = 1.5 x t ….. for Valve classes 150 – 2500
tv = 1.35 x t … for Valve class 4500
Where, t = Thickness of Cylinder with S = 7000 psi and Pressure same as that from P – T ratings
Actual thickness ( ta ) given in B 16.34 = tv + 0.1 In.(fixed)
Valve thickness per API 600 have additional corrosion and erosion requirement over ( ta ) from B 16.34
- Where corrosion / erosion is anticipated thickness measurements shall be made to determine metal loss.
- Formula for calculating retirement thickness of pipe can be used for Valves and flanged fittings using factor 1.5 and 5 Valves from ASME B 31.3.
Calculations described above not required for welded fittings. Pipe thickness can be adopted for welded fittings using appropriate corrections for shape, if necessary.
INSPECTION RECORDS
( API 570 – Chapter 12 )
-
- Inspection records provide :
- A comprehensive picture of general condition ( i.e. health ) of piping system
- Decide on additional / supplementary inspections
- Evaluation of remaining useful life
- Deciding on probable retirement and replacement programmes and take advance action for the same.
The data should be arranged on suitable forms so that successive inspection records furnished a chronological picture.
- Sketches : Original isometric sketches may be used or new sketches made to show TMLs and other relevant information.
- Thickness Data : Record of thickness data obtained from periodic or scheduled inspections shall be shown on sketches and tabulated and attached sketches ) Fig. 34 sample form
- Review of Records : Records of previous inspection shall be reviewed soon after current data is available from field and follow-up action sheets shall be prepared showing :
- Approaching retirement thickness
- Need of further investigation based on past and present data ( i.e. excessive corrosion rates on both occasions )
- In other cases specific features to be monitored during on-stream or next shut down inspection.
- A list for predictable repairs and alterations shall be made so that maintenance dept. can obtain materials, keep components ready, if nessary, fabricate well ahead of next shut down. This list will also help to plan manpower for next shut down.
*********
PLANT PIPING CODE – ASME B 31.3
PIPING FUNDAMENTALS
- General :
Prior to study of Plant piping code, a quick review of piping fundamentals is essential for prper understanding of the code.
A pipe or a tube is hollow, longitudinal product. `A tube’ is a general term used for hollow product having circular, elliptical or square cross-section or for that matter cross-section of any closed perimeter.
A pipe is tubular product of circular cross-section that has specific sizes and thicknesses governed by particular dimensional standard.
- Classification :
Pipe can be classified based on methods of manufacture or based on their applications.
- Methods of manufacture :
Seamless pipes are manufactured by drawing or extrusion process. ERW pipes ( Electric resistance welded pipes ) are formed from a strip which is longitudinally welded along its length. Welding may be by Electric resistance, high frequency, or induction welding, ERW pipes can also be drawn for obtaining required dimensions and tolerances.
Pipes in small quantities are manufactured by EFW ( Electric fusion welding ) process where in instead of electric resistance welding, the longitudinal seam is welded by manual or automatic electric arc process.
There are spiral seam welded pipes, which are large dia pipes 500 NB and above, and pipes are made by welding a spiral seam produced by forming continuous steel skelp into circular shape.
Centrifugally cast pipes are made by spraying molten metal along a rotating die where the pipes are cast in shape due to centrifugal action.
Classification based on end use :
Pipes a re classified as :
- Pressure pipes or Process pipes
- Line pipes
- Structural pipes
- Pressure pipes are those which are subjected to fluid pressure and or temperatures. Fluid pressure in generally internal pressure due to fluid being conveyed or may be external pressure ( e.g. jacked piping ) and are mainly used as plant piping.
- Line Pipes are mainly used for long distance conveying of the fluids and are subjected to fluid pressures. These are generally not subjected to high temperatures.
- Structural pipes are not used for conveying fluids and therefore not subjected to fluid pressures or temperatures. They are used as structural components ( e.g. handrails, columns, sleeves etc. ) and are subjected to static loads only.
- Pipes Dimensional Standards :
Diameters : Pipes are designated by Nominal size, Starting form 1/8” Nominal size, and increasing in steps.
- Pipe sizes increases in steps of 1/8” fir 1/8” to ½” : 1/8”, ¼”, 3/8”, ½” Nominal size.
- Sizes in steps of ¼” : ½”, ¾”, 1”, 1 ¼”, 1 ½”
- In steps of ½” upto 4” : 1 ½”, 2”, 2 ½”, 3”, 3 ½”, 4”
- In steps of 1” upto 6” : 4”. 5”, 6”
- In steps of 2” upto 36” : 6”, 8”, 10” ……. Etc.
For the Nominal size upto including 12”, there is one unique O.D. ( different from nominal size ) and I.D. would vary depending on schedule number. For Nominal sizes 14” and above, O.D. is same as Nominal size.
5. Schedule No. :
Pipes are designated by schedule number or weight designation like Std. (S), Extra Strong (XS) and Double Extra Strong (XXS)
Pipe schedule number S is defined as :
Sch. NO. S = 1000 P/S
Where P = Internal Pressure (psi)
S = Allowable tensile strength of material used.
Common pipe schedules are Sch 40, Sch 80, Sch 120, Sch 160, for larger pipe sizes intermediate schedule numbers ( Sch20, Sch 30 etc. ) are also employed ( Ref. Pipe Dimension Chart )
For Carbon steel, Pipe wall thickness tolerance is + 12 ½% i.e. Pipe wall thickness can vary 12 ½% from thickness obtained from dimension chart.
For stainless steels schedule numbers are designated by suffix S i.e. 10S, 40S, 80S e tc.
Length : Pipes are manufactured in `random length’ which is + 20’ –0” and in double random length + 40’ –0”.
- Fittings
Pipe fittings are the components which tie together pipe lines, valves, and other parts of a piping system. They are used in “making up” a pipe line. Fittings may come in screwed, welded, soldered, or flanged varieties and are used to change the size of the line or its direction and to join together the various parts that make up a piping system.
The majority of pipe fittings are specified by the nominal pipe size, type, material and the name of the fitting. Besides the end connections mentions above (screwed, welded, soldered, flanged) it is also possible to order bell and spigot fittings, which are usually cast iron and used for low pressure service.
In general, a fitting is any component in piping system that changes its direction, alters its function, or simply makes end connections. A fitting is joined to the system by bolting, welding or screwing, depending on many variables in the system.
-
- Butt-Welded Fittings
Welded fittings are used primarily in systems meant to be permanent. They have the same wall thickness as the mating pipe. Among the many advantages of butt welded systems are the following :
-
- They have a smooth inner surface and offer gradual direction change with minimum turbulence.
- They require much less space for constructing and hanging the pipe system.
- They form leak-proof constructions.
- They are almost maintenance free.
- They have a higher temperature and pressure limit.
- They form a self-contained system.
- They are easy to insulate
- They offer a uniform wall thickness through-out the system.
One of the major disadvantages of butt-welded systems is that are not easy to dismantle. Therefore, it is often advisable to provide the system with enough flanged joints so that it can be broken down at intervals. ( One of the main uses of the butt-welded system, is for steam lines, which are usually in high-temperature/ high-pressure service ).
-
- Socket Welded Fittings
Socket welded fittings have certain advantages over butt-welded fittings. They are easier to use on small-size pipelines and the ends of the pipes need not be beveled since the pipe end slips into the socket of the joint. With socket-welded fittings there is no danger of the weld protruding into the pipeline and restricting flow or creating turbulence. Thus, the advantages of the socket-welded system are :
- The pipe does not need to be beveled.
- No tack welding is necessary for alignment since joint and the pipe are self -aligning.
- Weld a material can not extend into the pipeline.
- It can be used in place of threaded fittings, therefore, reducing the likelihood of leaks, which usually accompany the use of threaded fittings.
- It is less expensive and easier to construct than other welded systems.
One of the major disadvantages of this type of fitting is the possibility of a mismatch inside the fitting where improperly aligned or mated parts may create a recess where corrosion could start.
Socket-welded fittings have the same inside diameter as standard (Schedule 40), extra strong (Schedule 80), and double extra strong (Schedule 160) pipe, depending on the weight of the fitting and mating pipe. Socket-welded fittings rare covered in ASA B16.11. They are drilled to match the internal diameter of schedule 40 or schedule 80 pipe.
-
- Flanged Fittings
Flanged connections are found on piping systems throughout the petrochemical and power generation fields on pipelines that are a minimum of 2 in.(5.08 cm ) in diameter. The majority of flanged fittings are made of cast steel or cast iron.
Flanged steel fittings are used in place of cast iron where the system is subjected to shock or high-temperature/ high-pressure situations where the danger of fire is prevalent, because cast iron has a tendency to c rack or rupture under certain stresses. A flange may be cast or forged onto the ends of the fitting or valve and bolted to a connecting flange which is screwed or welded onto the pipeline, thereby providing a tight joint. An assortment of facings, ring joint grooves, and connections are available in flange variations.
One advantage of flanged systems is that they are easily dismantled and assembled. One of the disadvantages is that they are considerably than an equally rated butt-welded system, because of the large amount of metal that go into making up joints and flanges. Moreover, flanged fittings occupy far more space than the butt-welded or screwed equivalents. Because of this higher weight load, a flanged system becomes far more expensive to support or hang from the existing structure.
*****
STUDY OF ASME B 31.1 CODE REQUIREMENTS
1.1 GENERAL :
The Code sets forth engineering requirements deemed necessary for safe design and construction of pressure piping.
Unless agreement is specifically made between contracting parties to use another issue, or the regulatory body having jurisdiction imposes the use of another issue, the latest Edition and Addenda issued at least 6 months prior to the original contract date for the first phase of activity covering a piping installation shall be the governing document for all design, materials, fabrication erection, examination, and testing for the piping until the completion of the work and initial operation.
-
- SCOPE :
Rules for the Process Piping Code Section B31.31 have been developed considering piping typically found in petroleum refineries; chemical, pharmaceutical, textile, paper, semiconductor, and cryogenic plants; and related processing plants and terminals within the property limits.
This Code prescribes requirements for materials and components, design, fabrication, assembly, erection, examination, inspection, and testing of piping.
-
- DEFINITIONS :
1.3.1 Chemical plant : an industrial plant for the manufacture or processing of chemicals, or of raw materials or intermediates for such chemicals. A chemical plant may include supporting and service facilities, such as storage, utility, and waste treatment units.
-
-
- Fluid service : a general term concerning the application of a piping system, considering the combination of fluid properties, operating conditions, and other factors which establish the basis for design of the piping system. See Appendix M.
-
- Category D Fluid Service : a fluid service in which all the following apply :
- the fluid handled is nonflammable, nontoxic, and not damaging to human tissues as defined in para 300.2 ;
- the design gage pressure does not exceed 1035 kPA (150 psi) ; and
- the design temperature is from –29o C (-20o F) through 186o C (366o F)
- Category M Fluid Service : a fluid service in which the potential for personnel exposure is judged to be significant and in which a single exposure to a very small quantity of a toxic fluid, caused by leakage, can produce serious irreversible harm to persons on breathing or bodily contact, even when prompt restorative measures are taken.
- High Pressure Fluid Service : a fluid service for which the owner specifies the use of Chapter IX for piping design and construction; see also para. K300
- Normal Fluid Service : a fluid service pertaining to most piping covered by this Code, i.e. not subject to the rules for Category D, Category M, or High Pressure Fluid Service.
1.3.3 Petroleum refinery – an industrial plant for processing or handling of petroleum and products derived directly from petroleum. Such a plant may be an individual gasoline recovery plant, a treating plant, a gas processing plant (including liquefaction), or an integrated refinery having various process units and attendant facilities.
1.3.4 Piping components – mechanical elements suitable for joining or assembly into pressure-tight fluid-containing piping systems. Components include pipe, fittings, flanges, gaskets, bolting, valves, and devices such as expansion joints, flexible joints, pressure hoses, traps, strainers, in-line portions of instruments, and separators.
********
DESIGN OF PIPES FOR SERVICE CONDITIONS
-
- DESIGN CONDITIONS :
This paragraph defines the temperatures, pressures, and forces applicable to the design of piping, and states the considerations that shall be given to various effects and their consequent loadings.
-
-
- Design Pressure :
-
The design pressure of each component in a piping system shall be not less than the pressure at the most severe condition of coincident internal or external pressure and temperature (minimum or maximum) expected during service.
-
-
- Design Temperature :
-
The design temperature of each component in a piping system is the temperature at which, under the coincident pressure, the greatest thickness or highest component rating is required.
-
-
- Design Minimum Temperature :
-
The design minimum temperature is the lowest component temperature expected in service.
-
-
- Bases for Design Stresses :
-
The bases for establishing design stress values (allowable stress values) for metallic materials in this Code are as follows.
Basic allowable stress values at temperature for materials not exceed the lowest of the following :
- the lower of one-third of SMTS and one-third of tensile strength at temperature;
- the lower of two-third of SMYS and two – thirds of yield strength at temperature;
2.2 WELD JOINT QUALITY FACTOR, EJ :
Basic Quality Factors. The weld joint quality factors Ej tabulated in Table A-1B are basic factors for straight or spiral longitudinal welded joints for pressure-containing components as shown in Table 302.3.4
Increased Quality Factors. Table 302.3.4 also indicates higher joint quality factors which may be substituted for those in Table A-1B for certain kinds of welds if additional examination is performed beyond that required by the product specification.
-
- PRESSURE DESIGN OF COMPONENTS :
- Straight Pipe :
- PRESSURE DESIGN OF COMPONENTS :
The required thickness of straight sections of pipe shall be determined in accordance with following equation.
tm = t + c
The minimum thickness T for the pipe selected considering manufacturer’s minus tolerance, shall be not less than tm.
The following nomenclature is used in the equations for pressure design of straight pipe.
tm = minimum required thickness, including mechanical,
corrosion, and erosion allowances.
t = pressure design thickness.
c = the sum of the mechanical allowances (thread or groove
depth) plus corrosion and erosion allowances.
T = pipe wall thickness (measured or minimum per purchase
specification
d = inside diameter of pipe.
P = internal design gage pressure.
D = outside diameter of pipe as listed in tables of standards or
specification or as measured.
E = quality factor from Table A-1A or A-1B
S = stress value of materials.
Y = coefficient from Table 304.1.1, valid for t < D/6 and for
materials shown. The value of Y may be interpolated for
intermediate temperatures.
For t > D/6,
d + 2c
Y = ————
D + d+2c
Straight Pipe Under Internal Pressure :
For t < D/6, the internal pressure design thickness for straight pipe shall
be not less than that calculated in accordance with Eq. (3a) :
PD
t = —————
2(SE + PY)
Following Equation may be used instead of above equation
PD
t = ——-
2SE
For t > D/6 or for P/SE > 0.385, calculation of pressure design thickness
for straight pipe requires special consideration of factors such as theory of
failure, effects of fatigue, and thermal stress.
-
-
- Blanks :
-
The minimum required thickness of a permanent blank (representative configurations shown in Fig. 304.5.3) shall be calculated in accordance with Eq. (15)
3P
tm = dg ——— + c
16SE
where-
dg = inside diameter of gasket for raised or flat face flanges, or
the gasket pitch diameter for ring joint and fully retained gasketed flanges.
E = same as defined earlier.
P = design gage pressure
S = same as defined earlier
c = sum of allowances defined earlier.
****
2 . MATERIALS
Generic Description:
Classification of materials by generic description involves the grouping of materials into broad categories according to certain attributes such as general composition, mechanical properties, product form, or end use.
There are no precise rules governing which attributes to apply in defining material groups, and the level of detail afforded the classification system depends largely on the level of detail needed to communicate specific ideas. Consequently, materials may be generically grouped according to very broad characteristics, for example metal or nonmetal, ferrous or nonferrous, or cast or wrought. Alternatively, materials may be placed in more narrowly defined generic groups such as mild steel, 3XX series stainless steel, or NiCrMo alloy.
With piping materials, generic grouping based on alloy content is most popular. These groups usually reflect the primary alloy content, and may include varying levels of complexity depending upon the extent to which one needs to communicate specific material needs. Table-5.1 gives an indication of the progression from simple generic descriptors, to complex generic descriptors, which may involve some elements of a standardized classification system (e.g., 300 series austenitic stainless steel).
Table 5.1 Levels of Generic Classification of Materials
Simple |
Intermediate |
Complex |
Carbon Steel |
Low Carbon Steel |
Fully Killed, Low Carbon Steel |
Low Alloy Steel |
Cr-Mo Steel |
2 ¼ Cr-1Mo Steel |
Stainless Steel |
Austenitic Stainless Steel |
300 Series Austenitic Stainless Steel |
Nickel Alloy |
High Nickel Alloy |
NiCrMo Alloy |
Generic material descriptions are frequently used during the early stages of a project, including project definition, conceptual design, front end design, preliminary design, process design, and/or budget estimation. For materials selection purposes during these stages, the user must be aware of Code requirements, but is not looking for a precise solution for each piping system.
Rather, the user should be looking at more global issues including resistance of generic material groups to various forms of corrosion, material cost and availability for various product forms, delivery times, need for qualification testing, and existence of suitable forming and joining technology.
Trade Names and Proprietary Designations
Trade names are used by manufacturers to uniquely identify their materials and products. Sample trade names include Inconel 625, Incoloy 825, Hastelloy C-275, Carpenter 20Cb-3, Allegheny- Ludlum Al-6 XN, Mather & Platt Xeron 100, Lincoln Fleetweld 5P+, and VDM 1925hMo.
Although there are definite commercial reasons for the existence of trade names (e.g., typically to induce purchasers to specify and buy only the product of a particular manufacturer), many manufacturers and trade associations publish trade name equivalency charts. Consequently, there is usually no need to restrict material selections through use of a single trade name. However, two exceptions do exist where it may be necessary to specify materials by trade name. The exceptions are:
- Materials of very recent development, still be protected by patent right, and
- Sophisticated materials required for very severe service situations, where all potential manufacturers may not be equally capable of making the same quality of product. (For certain high alloy materials, minor chemistry or processing modifications can dramatically affect alloy performance.)
Common ASTM Carbon Steel Piping Materials:
For everyday work, most piping systems are constructed from carbon steel. Material designations are seemingly inconsistent and random and, for the most part, knowledge of specifications and grades can only be gained with experience.
Nevertheless, for practical guidance, specification and grade designations can be grouped according to product form and notch toughness properties, as in Table 5.10.
Table 5.10 Common ASTM Carbon Steel Piping Material Specifications & Grades
Product Forms |
See Note(s) |
ASTM Materials without Impact Tests |
ASTM Materials with Impact Tests |
Pipe |
2 |
A 53 Gr. B A 106 Gr.B |
A 333 Gr. 1 A 333 Gr. 6 |
Flanges & Forged Fittings |
3 |
A 105 |
A 350 Gr. LF2 |
Wrought Fittings |
A 234 Gr. WPB |
A 420 Gr. WPL6 |
|
Castings |
A 216 Gr. WCB A 216 Gr. WCC |
A 352 Gr. LCB A 352 Gr. LCC |
|
Bolts, Studs, and Cap Screws |
4,5 |
A 193 Gr. B7 A 193 Gr. B7M |
A 320 Gr. L7 A 320 Gr. L7M |
Nuts |
4,5 |
A 194 Gr. 2H A 194 Gr. 2HM |
A 194 Gr. 7 A 194 Gr. 7M |
Notes to Table 5.10
|
Material Requirements of B31.3:
Materials considerations are specifically covered in B31.3 Chapter III, but there are also material references in many other chapters. The Code categorises various fluids as below , the material selection many times is governed by nature of fluid.
Table 5.11 Fluid Service Categories
Normal Fluid ServiceCategory D ServiceCategory M Service High Pressure (K) Service |
Pertains to most piping covered by the Code and includes piping not classified within the other fluid services listed below [¶300.2]. Service in which the fluid is nonflammable, nontoxic, and not damaging to human tissue; the design pressure does not exceed 150 psig (1030 kPag); and the design temperature is from -20ºF (-29ºC) TO 366ºF (186ºC)[¶300.2]. Service in which a single exposure to a very small quantity of toxic fluid can produce serious irreversible harm on breathing or body contact, even when prompt restorative measures are taken [¶300.2]. Service which applies when designated by the owner, typically for pressures in excess of that allowed by ASME B16.5 Class 2500 rating, for the specified design temperature and material group [¶k300(a)]. |
. Notes to Table 5.11
|
Materials and Specifications [¶323.1]
B31.3 classifies materials as listed, unlisted, unknown, or reclaimed, and places conditions on the used of such materials. Table 5.12 summarizes the characteristics of each material classification.
In most cases, Code users deal with listed materials. These may be considered as materials, which are “prequalified” for Code use based on inherent properties [¶323] and listed in B31.3 Tables A-1 and A-2. For pressure design purposes, the Code provides stress values for the listed materials as a function of temperature (since mechanical behavior is temperature dependent). However, the suitability of a particular material for a particular fluid service is beyond the scope of the Code [¶300(c)(6)]. A materials specialist should be consulted to ensure correct materials selection for a fluid service.
Temperature Limitations [¶323.2]
B31.3 recognizes that material properties and behavior in service are temperature dependent. A significant portion of b31.3 Chapter III deals with temperature limitations for materials, in particular lower temperature limits where impact testing may apply. The Code also imposes cautionary and restrictive temperature limits in Tables A-1 and A-2, and requires designers to verify that materials are suitable for service throughout the operating temperature range [¶323.2].
Table 5.12 Material Classifications [ ¶323.1]
Listed Materials Unlisted Materials Unknown Materials Reclaimed Materials |
[¶323.1.1] Those materials or components which conform to a specification listed in B31.3 Appendix A, Appendix B, or Appendix K, or to a standard listed in B31.3 Table 326.1, A326.1 or K326.1. for pressure design, listed materials and allowable stress values are provided for listed materials, these are most convenient to use. [¶323.1.2] Those materials which conform to a published specification covering chemistry, physical, and mechanical properties, method and process of manufacture, heat treatment, and quality control, and which otherwise meet the requirement of the Code. [¶323.1.3] Those materials of unknown specifications, not to be used for pressure containing piping components. [¶323.1.4] Used materials, which have been salvaged and properly identified, as conforming to a listed or published specification. |
Upper Temperature Limits [¶323.2.1]
Upper temperature limits for listed limited materials are the maximum temperatures for which a stress value or rating is shown directly in or referenced by the Code. The Code may also provide notes to the stress value tables, precautionary information in Appendix F, and /or restrictions within the text of Code. For example, from Table A-1, the upper temperature limit for ASTM A 106 Grade B pipe is 1100ºF even though there are two notes pertaining to use of the material above 800ºF and 900ºF, respectively. ¶F323.4(a)(2) and ¶F323.4(a)(4) also discuss these notes.
Of course, the Code does permit use of listed materials at temperatures above the maximum indicated by the stress value or rating, provided there is no prohibition in the Code [¶323.2.2(a)] and provided the designer verifies the serviceability of the material [¶323.2.1(b)]. Verification would typically involve material specialists with an engineering background and a “sound scientific program carried out in accordance with recognized technology” [¶323.2.4].
Lower Temperature Limits and Impact Testing [¶323.2.2]
Lower temperature limits for materials are established as a means of controlling risk of brittle fracture. Terms frequently used in lower temperature limit discussions include notch sensitivity, impact testing, Charpy testing, and notch brittleness.
For must Code users, the basic question to be answered is: “Do I need to use impact tested materials”, answering the question can be complex and convoluted; however, the basic steps to determining the answer are listed below and are discussed in detail in the following paragraphs.
- select the design minimum temperature for the piping. This may involve process engineering and or heat transfer specialists, and consideration of ambient temperature effects.
b. obtain the minimum permissible temperature for the proposed piping materials according to B31.3 rules.
- Follow the instructions of B31.3 to determine whether impact tests are required (e.g., Table 323.2.2).
- If impact tests are required, consult the additional requirements of B31.3 regarding impact test methods and acceptance criteria.
Common Code Paragraphs Relating to Notch Toughness and Low Temperature Requirements
For the convenience of users of the guide, several clauses and tables applicable to B31.3 impact testing requirement are listed in Table 5.15 below. Users are cautioned that this guide is not a substitute for the ASME B31.3 Code, which should be consulted for all requirements affecting pressure piping design and construction.
Table 5.15 B31.3 Clauses and Tables Applicable to Impact Testing
Clause or Table |
Description |
301.3.1 301.5.1 301.9 302.2.4(h) 309.2.2 321.1.4(c ) 323.2 323.2.2 323.2.3 323.3 323.4.2(a) 323.4.2(b) Table 323.3.1 Table 323.2.2 Table 323.3.5 Table A-1 Table A-2 |
Design Minimum Temperature Dynamic Effects – Impact Reduced Ductility Effects Allowances for Pressure and Temperature Variations (below the minimum temperature shown in Appendix A) Carbon Steel Bolting (note that B7M, L7M, B7, L7, 2HM, 7M, 2H, and 7 are low alloy steels, not carbon steels) Materials (of unknown specification used for piping supports) Temperature Limitations Lower Temperature Limits, Listed Materials Temperature Limits, Unlisted Materials Impact Testing Methods and Acceptance Criteria Ductile Iron Other Cast Irons Impact Testing Requirements for Metals Requirements for Low Temperature Toughness Tests for Metals Minimum Required Charpy V-Notch Impact Values Basic Allowable Stresses in Tension for Metals (see Min. Temp. column and Note 6 at the beginning of the table) Design Stress Values for Bolting Materials (see Min. Temp. column and Note 6 at the beginning of the table) |
Materials Selection
When selecting materials for plant piping systems, legal, code, commercial, and technical considerations must be addressed.
Legal Considerations
Legal considerations include understanding and appreciation of:
- legislation applicable to the jurisdiction having authority over the design, construction and operation of the piping system; and
- contracts which exist between various parties.
For example, many states, provinces, and countries have legislated the use of B31.3 rules for construction of piping systems, so the Code essentially become a legal document. Local jurisdictions may also operate under government acts and regulations, which impose additional requirements that, may be:
- technical (e.g., prohibitions concerning certain materials or design practices), or
- organizational (e.g., registration of designs, registration of welding procedures, registration and accreditation of quality control systems)
For many projects, contract documents, including specifications prepared by the owner or owner’s engineer, impose restrictions on:
- Materials (e.g., quality level, notch toughness properties, service environment, product form), and
- Fabrication/construction methods (e.g., bending, forming, welding, heat treating, hydrotest water quality, cleaning chemicals)
B31.3 Code Considerations
As indicated earlier in this chapter, the B31.3 Code is concerned with pressure integrity (safety). This is manifest, for example, through provision of allowable design stresses as a function of temperature, rules for notch toughness evaluation and brittle fracture avoidance, restrictions for various fluid service categories, requirements for weld procedure qualifications, restrictions on forming and bending practices, examination requirements, and numerous prohibitions, limitations, conditions, and precautionary measures scattered throughout the Code.
Although Code issues must be considered in the material selection process, the Code does not instruct the user on how to select specific materials. ¶300( c)(6) states: “Compatibility of materials with the service and hazards from instability of contained fluids are not within the scope of this Code. See Para. F323”. The first sentence of ¶F323(a) states: “Selection of materials to resist deterioration in service is not within the scope of this Code”. Clearly, the technical issues related to materials selection must be considered by personnel with specific training in this area.
Commercial Considerations
Materials decisions invariably have an impact on project cost and schedule. Can the material be purchased in the requirement form? What will be the initial cost? When will the material be available? What is the life cycle cost relative to other material options? Who can fabricate the material into a piping system? When can it be delivered and at what cost? What are the anticipated maintenance costs with the selected material?
These questions can be difficult to answer, but every materials decision has a commercial impact, which must be considered. The level of detail given to study of the commercial impact is widely variable depending on project scope, technical complexity, and management.
Technical Considerations
Technical considerations begin with an understanding of process and containment requirements including pressure, temperature, fluid velocity, and fluid characteristics, as well as risk and consequences of failure. Material properties are then evaluated in light of this understanding, and generally include consideration of chemical, mechanical, and physical properties, as well as corrosion resistance, weldability, and formability. Fundamentally, final materials selection involves the proper matching of material properties with process design conditions, mechanical design conditions, fabrication and construction conditions, and operating conditions.
Table 5.16 provides and overview of some material selection issues relative to other project variables.
Project Variable |
Materials Selection Issues |
Process Design Conditions and Corrosion Resistance Mechanical Design Conditions and Mechanical Properties |
|
Fabrication and Construction Conditions |
|
Operating Conditions |
|
From Table 5.16, one might correctly assume that selection of materials is an evolutionary process, especially for technically complex projects. Generally the materials selection process involves a series of steps, separated in time, with each step narrowing down possibilities until the best option is determined. As project details unfold, this narrowing of options is typically manifested by a change in the way materials are identified, going from very generic descriptions (e.g., stainless steel) to specifications, type, and grade (e.g., ASTM A 312 TP304L).
The level of detail applied during materials selection depends heavily on factors such as the scope, size and complexity of the project, the stage of the project, the corporate style of the participants, and the availability of materials specialists. Although the steps sometimes overlap, careful analysis of several projects would show at least three distinct phases of materials selection with the following characteristics:
- Conceptual design – overview of process technology
- Process design – details of process technology
- Mechanical design – primary scope of B31.3
Conceptual Design – overview of Process Technology
Development of a materials selection and corrosion control philosophy for a project normally begins with evaluation and understanding of the process technology. Although this step in the materials selection process is not always evident or obvious, and may even be omitted when the process is well understood, it is a logical starting point for a grass roots project.
As an example, in the very early stages of project development, where “ballpark” economics are being thrashed out, the main interest of management is “big picture” material costs. That dreaded classic question generally reaches the materials specialist. How much stainless steel do we have to buy?. Of course, at the conceptual stage process details can be sketchy at best, so there is much crystal ball gazing at this point. Nevertheless, best efforts are made to provide a very generic overview of material options, knowing that management doesn’t generally understand that there are at least fifty different kinds of stainless steel, each with its own unique price and delivery terms, and hundreds of material options that go by much stranger sounding names than “stainless steel”.
The job of the materials specialist, who may also be called the corrosion specialist, is to examine the proposed process for any major issues, which could jeopardize the project in financial and/or schedule terms. This is normally done in consultation with process professionals who have defined the process in terms of block flow diagrams, process stream compositions, and chemical reactions that may occur. A few typical questions to be answered during conceptual design are listed below.
- Are carbon steels adequate?
- Can coatings or chemicals be used economically to control corrosion?
- If high alloy materials are required, how much will they cost?
- How well is the interaction between the process environment and the material understood?
- Is there a requirement for materials testing prior to selection?
- Could required materials testing jeopardize the project in financial or schedule terms?
As an example, consider conceptual design for a plant for handling high velocity wet natural gas at 1000psi, with 25% CO2 and H2S AT 200ºF. Bare carbon steel would not be a likely candidate material due to excessive weight loss corrosion. Inhibitors could be considered, but adequate corrosion control may not be possible. The process is a bit hot for conventional organic coatings or plastic liners. Both CO2 and H2S could permeate the coating and cause coating failure if the system were subject to rapid pressure changes. Intermediate alloys containing chromium could work with adequate control welding and heat treatment. High alloy steels (stainless steels) could also work, but there is a large increment in cost and there may be potential for chlorides and resultant chloride stress corrosion cracking (CISCC).
Process Design
If development economics favor further work, the next phase of material selection is generally made coincident with or slightly lagging behind process design. Process information is examined in detail and materials are selected based on compatibility with process stream characteristics and other external variables if they are known. Decisions often require consultation with process engineers for clear understanding of process conditions, including steady and non-steady state conditions such as start-up, upset, planned shutdown, and unplanned shutdown.
As an example of the material selection process for a given stream, one might designate piping materials such as carbon steel (CS) with a suitable corrosion were important. However, if it is also known that the pipe might be exposed to low ambient temperatures where impact properties were required, one might upgrade the material selection to CSIT (carbon steel, impact tested). For another stream, which could be considered very corrosive, one might specify 3XXL stainless steel, where “L” grade is imposed to resist HAZ sensitization during welding, and the possibility of intergranular corrosion is service. If that same stream contained an aqueous chloride phase at 80ºC, 3XX would be susceptible to CISCC. In that case, one might specify a duplex stainless steel or superduplex stainless steel, depending upon chloride level, oxygen content and temperature.
While there is no single method for making and documenting materials selection decisions, the normal output at this stage of a project is a Corrosion and Materials Report. The word corrosion is generally included in the title of the report, since many of the material selection decisions reflect a response to corrosion predictions. The report typically contains the basis for decision making, as well as narratives describing issues, concerns, and limitations governing final materials selection for a given portion of the process.
Material selection diagrams (MSD’s) and/or material selection tables are generally included with the Corrosion and Materials Report. MSD’s are typically modified process flow diagrams (PFD’s) showing generic material choices and corrosion allowances for each corrosion circuit. Corrosion circuits are elements of the process with similar corrosion characteristics, and are frequently equivalent to process streams defined on the PFD, or to subsets of process streams. Presentation of materials selection data in diagram is generally the most useful format for communication with other design professionals, who will use the information during completion of subsequent work. Such presentation also assists in maintaining materials engineering input on the project. A simplified example of a MSD for an amine sweetening unit is shown in Figure 5.1
During the mechanical design stage, the process characteristics shown by process simulations and PFD’s and the material requirements shown by the Corrosion and Materials Report and MSD’s, are carefully examined. Then a piping class, which summarizes detailed mechanical and material requirements, is generally assigned to each line in the piping system. Note that the use of piping classes is not a B31.3 requirement; it is a typical approach to mechanical design within the pressure piping industry.
An example of a simple piping class is shown in Figure 5.2. It is a table of information for a given pressure rating and service characteristic, which describes acceptable piping component types and dimensions, as well as material specifications, types, classes, and/or grades. Piping components include pipe, forgings, fittings, valves, bolting, gaskets, and other piping specials. Usually the piping class contains information about corrosion allowance, postweld heat treatment, and nondestructive examination. Within a corporation, piping classes often exist from previous projects, or are supplied by the firm contracted to complete the engineering. When they do not exist, they are usually developed on the basis of process, material, and mechanical requirements.
The piping class designator is typically an alphanumeric descriptor such s D2 or AA2U, which is shown on the piping drawings (collectively, a group of drawings including P & ID’s, MFD’s, piping plans and sections, and isometrics), usually as part of the line number. a typical line number would be 6 in HC-34212-D2, where 6 in. is the nominal pipe size, HC is the commodity descriptor (e.g., hydrocarbon), 34212 is the line serial number, and D2 is the piping class. Specification breaks, which may be for material or pressure reasons, are also applied to piping drawings.
Depending on project scope and technical complexity, the mechanical design stage may also include preparation of detailed material specifications (stand alone or supplementary) to address issued such as material chemistry, processing requirements, product form (cast, forged, welded), fracture toughness, weldabilty, heat treatment, nondestructive examination, and various forms of corrosion resistance.
********
3. FABRICATION, ASSEMBLY, AND ERECTION
Introduction:
Chapter V of the B31.3 Code is devoted to the fabrication, assembly, and erection of piping systems. These terms are defined by ¶300.2 as follows.
- Fabrication is the preparation of piping for assembly, including cutting, threading, grooving, forming, bending, and joining of components into subassemblies. Fabrication may be performed in the shop or in the field.
- Assembly is the joining together of two or more piping components by bolting, welding, bonding, screwing, brazing, soldering, cementing, or use of packing devices as specified by the engineering design.
- Erection is the complete installation of a piping system in the locations and on the supports designated by the engineering design, including any field assembly, fabrication, examination, inspection, and testing of the system as required by the code.
Fabrication, assembly, and erection require the use of many special processes including:
- Forming and bending by cold and hot methods;
- Joining by welding, brazing, soldering, or mechanical methods including threading, flanging, specialty high pressure connections, and mechanical interference fits (MIF); and
- Heat treatment by local methods, or by permanent or temporary furnaces.
B31.3 assumes some understanding of the special processes used during fabrication, assembly, and erection of piping systems. However, as with materials of construction, the level of understanding is widely varied and often restricted to a few processes in the user’s repertoire of experience.
Consequently, the objective of this chapter is to explore the basic technology behind some of the special processes in relation to requirements of the Code.
Bending and Forming [¶332]
General
Bending and forming processes are sophisticated technical operations. An evaluation of the effects of bending and forming on material properties is integral to the use of such products in piping systems. In this light, the following Code statements should be considered as more than simple motherhood:
- ¶332.1 states: “pipe may be bent and components may be formed by any hot or cold method which is suitable for the material, the fluid service, and the severity of the bending or forming process.”
- ¶332.3 states: “the temperature range for forming shall be consistent with material, intended service, and specified heat treatment”.
These Code clauses are intended to trigger the engineering input necessary to verify that final material properties will be satisfactory for the intended service. And, even though the Code does impose requirement for design (e.g., ¶304.2) and fluid service (e.g.,¶306.2), engineering input is still needed. The Code does not and can not provide rules to address the specific requirements of every situation.
As part of an engineering evaluation, below are some useful starting questions regarding the effects of bending and forming on material properties for a specific service.
- What effect will the bending or forming temperature and deformation parameters (e.g., cold, warm, or hot bending, strain rate and total strain) have on strength, ductility, hardness and notch toughness of the resulting bend?
- What effect will the resulting microstructure have on general corrosion, localized corrosion (galvanic, pitting, and/or crevice corrosion), stress corrosion cracking, or long-term mechanical properties?
- What are the risks relative to formation of hard spots, undesirable precipitation effects, fatigue resistance, and creep resistance?
Hopefully the above questions would be answered with the help of metallurgical and/or corrosion specialists, in combination with suitable testing when appropriate.
Bending
The need for changes to the direction of flow in piping systems has traditionally been accommodated through the use of manufactured fittings such as elbows and tees. However, changes to direction of flow may also be made through the use of pipe bends. In fact, with modern equipment, substantial economic benefits can be derived from the use of bends, by virtue of reduced fitting, welding, and nondestructive examination (NDE) costs.
Before examining bends in detail, a few comments regarding bend types may be useful to readers with no bending experience. In the bending and piping industries, bend types are often described by a multitude of terms. Although a formal classification system does not exist, bends are usually referred to in terms of:
- Method of manufacture, including cold bends, hot bends, furnace bends, induction bends, arm bends, ram bends, three point bends, miter bends, segmented bends, corrugated bends, and creased bends;
- Location of manufacture, that is, field bends or factory bends;
- Shape or appearance, such as L-bends, S-bends, wrinkle bends, miter bends, segmented bends, corrugated bends, and creased bends; and
- Function or end-use, such as sag bends, overbends, side bends, and combination bends.
Note that several of the terms described in (c) and (d) above are rooted in cross-country pipeline construction, where bends are normally used to accommodate changes of elevation associated with the terrain or to provide for expansion and contraction of the pipeline with changes of temperature. For plant piping systems, it is most common to use bending terms reflective of the method of manufacture, which may include combinations of terms (e.g., three point cold bend, hot furnace bend, hot induction bend).
Regardless of bend type, all bends have certain features and dimensional characteristics which must be carefully specified during piping design and controlled during bend procurement and manufacture (see Figure 6.1).
.
B31.3 addresses limitations on outer fiber elongation (strain) in clauses dealing with post bend heat treatment [¶332.4]. In addition to B31.3 requirements, be cautions about outer fiber strain restrictions imposed by other standards, which may be applicable to the piping system (e.g., NACE MRO176).
Although not specified in B31.3, when longitudinally welded pipe is used for bending, the longitudinal weld should be placed as near as practical to the neutral axis of the bend.
Heat Treatments Required After Bending or Forming
Through heat treatment rules B31.3 does address some of the adverse effects of bending and forming operations on material properties. The rules are based on type of bending operation (hot or cold), type of material, and outer fiber strain.
Regardless of material thickness, heat treatment is required according to conditions prescribed by ¶331:
- After hot bending and forming operations carried out on P nos.3, 4, 5, 6, and 10A materials;
- After cold bending and forming.
- of P-No. 1 to P-No.6 materials where the outer fiber elongation in the direction of severest forming (usually extrudes) exceeds 50% of specified minimum elongation stated for the specification grade, and thickness of the starting pipe material;
- of any material requiring impact testing, if the maximum calculated fiber strain after bending or forming exceeds 5%; and
- when specified by the engineering design.
With regard to (a) above, the materials listed are capable of transformation hardening when cooled from hot bending and forming temperatures, so heat treatment is aimed at restoring mechanical properties to a level reasonably consistent with the starting materials. With regard to (b) above, work hardening effects imparted by cold bending and forming reduce the ductility and notch toughness (impact strength) of materials. As well, cold bending and forming operations generate residual stresses in the finished parts. Heat treatment is therefore applied as a tool to reduce the negative consequences of these effects (e.g., brittle fracture).
Welding
Most people associated with the pressure piping industry will, at some point, come in contact with welding. This could mean:
- Writing a welding procedure,
- Qualify a welding procedure or welding personnel,
- Reviewing a welding procedure for acceptance of rejection in a specific application, or
- Doing the welding, which will likely involve trying to interpret someone else’s welding procedure.
To laymen, welding is a magic act. With the common arc welding processes, the arc ignites with a flash of bright light, the magician (welder) moves the bright light along the interface between the metals and “presto”, a weld is created. Of course, well-informed piping professionals know that welding is a lot more than smoke and mirrors. It is a very complex interdisciplinary science involving aspects of mechanical, civil, electrical, and metallurgical engineering. Thorough technical understanding of welding operations requires specific training, which is only available at select engineering, technical, and trade schools.
B31.3 provides welding guidance in the areas of:
- responsibility [¶328.1],
- qualifications[¶328.2], and
- technical and workmanship criteria [¶328.3 through ¶328.6].
these are discussed in detail in the following sections.
Welding Responsibility [¶328.1]
B31.3 is very clear regarding responsibility for welding. ¶328.1 states: “each employer is responsible for the welding done by the personnel of his organization and; except as provided in paragraphs. 328.2.2 and 328.2.3, shall conduct the tests required to qualify welding procedures, and to qualify and as necessary requalify welders and welding operators”. This philosophy is consistent with other sections of the ASME code and with similar codes, standards, and specifications around the world.
The two exceptions in ¶328.1, regarding the need for employers to conduct welding qualification tests, are:
- Procedure Qualifications By others [¶328.2.2], and
- Performance Qualification By Others [¶328.2.3]
Although these exemptions exist, the employer is not exempt from responsibility for welds prepared according to procedures or personnel qualified by others. Close examination of the conditions attached to these exemptions will enhance understanding as to why the employer is responsible for all welding.
Regarding exemption of an employer from weld procedure qualifications through use of welding procedures qualified by others, interpretation of B31.3 restrictions shows that the exemption is limited to low risk situations. For the exemption to apply, the Code has the following requirements:
- The inspector must be satisfied [¶328.2.2(a)]:
- With the capability of the organization providing the procedure [¶328.2.2(a)(1)]; and
- That the employer intending to use the procedure has not made any changes to it.
- Base metals are restricted to P-No. 1, P-No. 3, P-No. 4 Gr. 1 (13%Cr max.), or P-No. 8 [¶328.2.2(b)].
- Impact tests are not required [¶328.2.2(b)].
- Base metals to be joined are of same P-No., except P-No. 1, P-No. 3, and P-No. 4 Gr. 1 may be welded to each other as permitted by ASME Section [X[¶328.2.2( c)].
- Base metal thickness does not exceed ¾ in. (19 mm) [¶328.2.2( d)].
- PWHT is not required [¶328.2.2( d)]
- Design pressure does not exceed ASME/ANSI B16.5 Class 300 at design temperature [¶328.2.2( e)].
- Design temperature is in the range -20ºF through 750ºF (-29ºC through 399ºC), inclusive [¶328.2.2( e)]
- Welding processes are restricted to SMAW or GTAW or combination thereof [¶328.2.2( f)].
- Welding electrodes are restricted to those listed in ¶328.2.2( g).
- Employer accepts responsibility for both the WPS and PQR by a signature [¶328.2.2( h)].
- Employer has at least one welder/welding operator who, while in his employ, has passed a performance qualification test using the procedure and the P-No. of material specified in the WPS. Qualification must have been with a bend test per ASME Section IX Para QW-302. Qualification by radiography alone is not acceptable [¶328.2.2(i)].
Always consult the latest revision of the Code for any changes to the exemption restrictions, which may occur from time to time.
Regarding exemption of an employer from performance qualification testing, a performance qualification made another employer may be accepted, subject to the following restrictions [¶328.2.3]:
- The inspector must specifically approve the exemption.
- The qualification is limited to piping using the same or equivalent procedure with essential variables within the limits of ASME Section IX.
- The employer must obtain a copy of the performance qualification test record from the previous employer, which contains information prescribed by ¶328.2.3. This requirement seriously restricts the portability of welding qualifications. For example, why would an employer release such records to a competitor, unless the competitor is part of the same corporate group?
The restriction has been overcome in some North American locations through qualification tests administered by the jurisdiction having authority over the work (e.g., state or province). In other locations, especially developing countries where massive projects are undertaken, the portability restriction has been overcome by general acceptance of qualification cards issued by some large local industrial organization. Typically, the qualifying organization issues each welder a laminated ID card containing the welder’s photograph and other qualification information.
Of course, welder performance qualification cards are valuable. Laminated photographic ID is essential and must be carefully controlled. For example, without laminated photographic ID it would be quite possible to have one qualified welder showing up at different test centers, passing qualification tests for all of his friends. Alternatively, it would be possible for unqualified welders to be substituted on the work by forgery of qualification cards without photographic ID.
Welding Qualification [¶328.2]
Although the qualification exemptions discussed above may be used, normally the employer is required to conduct welding qualifications. B31.3 controls the details of welding qualifications by referencing:
- ASME Section IX[¶328.2.1(a)],
- Supplementary technical requirements [¶328.2.1(b) through 328.2.1( f)], and
- Requirements for qualification records [¶328.2.4].
By external reference to ASME Section IX, the B31.3 Code takes advantage of a general working document governing welding qualifications for the entire ASME Code. Topics in the following paragraphs, which address welding variables listed in ASME Section IX, are indicated by the “QW” prefix to clause numbers.
Joints [¶QW-402]
The terminology used to describe weld joints can be confusing, with meaning often dependent on the industry sector where work is carried out, as well as on applicable codes and standards. Experience and intuition often form the basis for understanding various terms. For example, the term “butt weld” is commonly used in pressure piping applications to describe a butt joint with a groove weld, which is typically a full penetration groove weld.
To properly communicate welding requirements it is important to make some basic distinction relative to:
- joint types,
- weld types, and
- joint geometry and end preparation.
Following from these basics, several supplementary details should also be considered, including:
- degree of joint penetration full or partial,
- weld profile – convex or concave,
- alignment and fit-up details,
- backing type, if used, including weld metal and backwelded joints, and
- access for welding (i.e., single welded joints, double welded joints)
Joint Types
There are five basic types of joints, as described in Table 6-1. Note that the joint is the interface between the members. This distinction is important, since it governs interpretation of weld symbols and thickness of the joint (e.g., for preheat purposes).
Table 6.1 Five Basic Joint Types
Butt Joint |
A joint between two members aligned approximately in the same plane. |
Corner Joint |
A joint between two members approximately at right angles (90º) to each other |
Tee joint |
A joint between two members approximately at right angles (90º) to each other, in the form of a T. |
Lap joint |
A joint between two overlapping members. |
Edge joint |
A joint between the edges of two or more parallel or nearly parallel members. |
Types of Welds
There are three basic types of welds, as listed in Table 6.2
Table 6.2 Basic Weld Types
Groove Weld Fillet Weld Plug or Slot Weld |
A weld made in the groove between two members to be joined. A weld of approximately triangular cross section, joining two surfaces approximately at right angles to each other. A weld made through a circular or elongated hole in one member of a lap or T joint, joining that member to the surface of the other member exposed through the hole. |
End Preparation And Joint Geometry
End preparation [¶328.4.2] refers to the shape and dimensions of the base metal when viewed as a cross section at the welding end, prior to fit-up and welding. Joint geometry refers to the shape and dimensions of a joint when viewed in cross section after fit-up and prior to welding.
For pressure piping, joint geometry refers mainly to the type of groove to be used, of which there are many. B31.3 provides some guidance concerning end preparations and resultant joint geometry [¶328.4.2(a)(2) and Fig. 328.4.2].
For manually welded piping butt joints, the single-vee groove is most common. For thick joints, however, compound vee grooves may be used to reduce welding costs, distortion, and residual stress.
In other situations, decision regarding joint geometry involve consideration of several issues, including Code requirements, selected welding process, size and type of filler metal, welding position, access to the root of the joint, availability of suitable tools for joint preparation, and economy.
Joint Penetration
Joint penetration refers to the minimum depth that a groove weld extends from its face into the joint, exclusive of reinforcement (i.e., weld metal in excess of the quantity required to fill the joint). With pressure piping, it is normal to aim for full (complete) penetration welds where the weld metal completely fills the groove and is fused to the base metal throughout the total thickness. Limits on incomplete penetration are listed in B31.3 and discussed later in this book.
In some cases, the engineering design may require partial penetration joints. The extent of penetration may be described in terms of the effective throat, although specification of the maximum amount of incomplete penetration is more useful when nondestructive examination methods are applied to verify joint quality.
As an example of a situation where partial penetration joints would be used, consider a butt-welded cement mortar lined piping system. With this type of construction, a thin gasket of suitable diameter (e.g., compressed asbestos or equivalent) is spot glued to the cement surface of one member of a joint. The other member is then fit up tight against the gasket and the joint is clamped. The root bead is then deposited, taking care not to penetrate completely through the root face of the carrier pipe. If they are penetrates the root face of the carrier pipe, the gasket may burn and loose its ability to provide a seal, or concentrated heat from the arc may cause the cement to crack and fall away from the pipe wall.
Backing
While one normally thinks of 200 and 300 series stainless steels in the classification of austenitic materials, the group also includes may nonferrous alloys.
Imposes two special requirements for nonferrous and nonmetallic backing rings, specifically:
- that the designer approve their use, and
- that the welding procedure using them be qualified as required by ¶328.2.1(e).
in addition to the above Code restrictions on backing rings, designers normally prohibit their use for:
- corrosive services where the space between the ring and the pipe might be a location for crevice or pitting attack.
- Cyclic or vibrating services where notches associated with rings become sites for development of fatigue cracks, and
- Cryogenic or low temperature services where notches become sites for initiation of brittle fracture.
Consumable Inserts [¶328.2.1(e), ¶328.3.3]
¶328.3.3] indicates that consumable inserts may be used provided:
- they are of the same nominal composition as the filler metal,
- they will not cause detrimental alloying of the weld metal, and
- their suitability is demonstrated by weld procedure qualification [¶328.2.1(e)].
In general, the B31.3 position on consumable inserts is consistent with that of ASME Section IX, which treats consumable inserts as a nonessential variable for the common arc welding processes, which would use inserts (e.g., GTAW).
However, under strict interpretation, the ASME position on nonessential variables means that a WPS could be amended without requalification, whether the insert were added or deleted. Under B31.3 rules, addition or deleted. Under B31.3 rules, addition or deletion of an insert would not be permitted without a supporting PQR (i.e., requalification)
Pre-heating :
B31.3 defines preheating as the application of heat to the base metal immediately before or during a forming, welding, or cutting process [¶300.2]. This definition has a slightly broader scope than the definition provided in ASME Section IX ¶QW – 492. B31.3 also states that preheat is used, along with heat treatment to minimize the detrimental effects of high temperature and severe thermal gradients inherent in welding [¶330.1]. Although not specifically mentioned in B31.3, these detrimental effects can include:
- cold (hydrogen ) cracking,
- hard, brittle heat affected zones,
- distortion, and/or
- high residual stress.
Preheat can also be used to assist in the fusion (melting) of metals with high conductivity such as copper and copper alloys, and thick sections of aluminum and aluminum alloys. Preheat is sometimes used to assist in the alignment of parts, but such practice is usually discouraged due to lack of control over the alignment activity and the potential introduction of abnormally high stresses.
ASME Section IX defines preheat temperature as the minimum temperature in the weld joint preparation immediately prior to welding; or in the case of multiple pass welds, the minimum temperature in the section of the previously deposited weld metal, immediately prior to welding [¶QW – 492].
Note that the ASME definition of preheat temperature as applied to multipass welds is also known as minimum interpass temperature in other codes, standards, and specifications. In this book, the term minimum interpass will be used when referring to the minimum temperature of the deposited weld metal before starting the next pass of a multipass weld since, from a technical perspective, it is not always necessary that the temperature between passes meet or exceed the minimum preheat temperature at the start of the first pass.
ASME Section IX defines interpass temperature as the highest temperature in the weld joint immediately prior to welding, or in the case of multipass welds, the highest temperature in the section of the previously deposited weld metal, immediately before the next pass is deposited [¶QW – 492]. Again, strictly speaking, the interpass temperature as defined by ASME is the maximum interpass temperature. In practice, it is measured near the start of the next pass.
Most requirements for preheat and minimum interpass temperature control are aimed at prevention of cold cracking in transformation hardenable materials such as carbon steels, low alloy steels, intermediate alloy steels, and martensitic stainless steels. For cold cracks to form, the four conditions listed in the left column of Table 6-7 must be satisfied simultaneously.
The magnitude of any one of the four conditions cannot be defined with accuracy and depends largely on the other three conditions. The beneficial effect of preheat on each of these conditions is shown in the right column of Table 6.7.
Table 6.7 Influence of Preheat and Minimum Interpass Temperature on Conditions Required for Cold Cracking
Conditions Necessary for Cold Cracking |
Benefits of Preheat and Minimum Interpass Temperature Control |
Presence of hydrogen in sufficient quantity. |
Diffuses hydrogen away from the joint, reducing the risk of cracking. |
Sufficient tensile stress, which may be applied, residual, or a combination of both. |
Alters stress distribution during welding and offers a small reduction of residual stress upon completion of welding. |
A susceptible microstructure, which is normally interpreted to mean a hard microstructure, hence the frequent use of hardness tests to assess the risk of cold cracking. |
Reduces probability of forming susceptible microstructure by slowing the cooling rate. |
A temperature threshold below some critical level (e.g.,300ºF), which depends somewhat on alloy content and metal structure. |
Keeps the weldment above threshold temperature for cracking until the weld is completed. |
Another term used by ASME Section IX is preheat maintenance. Although not specifically defined by the code, examination of ¶QW – 406.2 shows that the term applies to the maintenance or reduction of preheat upon completion of welding, prior to any required postweld heat treatment. The primary reason for preheats maintenance after completion of welding is to continue diffusion of hydrogen from the weldment. It may also be used for reduction of thermal gradients and resulting residual stresses or distortions, and/or for isothermal transformation. When preheat maintenance is specified for a welding procedure, it should include both temperature and time. Simply indicating “yes” on the weld procedure specification is meaningless.
For most Code users, the following questions regarding preheat and interpass control must be answered:
- What preheat and minimum interpass temperatures should be used for the application?
- How should the heat be applied?
- How, where, and when should the temperature be measured?
Detailed technical answers to the above questions can be very complex. Since most piping applications involve some legal requirement (contractual and/or jurisdictional), the obvious starting point for answers is to examine the minimum requirements of B31.3 and ASME Section IX.
Preheating for all types of piping welds is covered in B31.3 under ¶330. The second sentence of ¶330.1 states: “ The necessity for preheating and the temperature to be used shall be specified in the engineering design and demonstrated by procedure qualification”. If such requirements are not included in the engineering design, then the minimum Code requirements are generally assumed.
In addition to information contained in B31.3 Table 330.1.1, there are numerous other methods of evaluating or verifying requirements for preheat and interpass temperature control. Some techniques, with associated comments, are described below:
- Nomographs are a favorite tool of technical specialists for estimating preheat requirements. One common method used for carbon and carbon-manganese steels was published by the British Welding Institute in a book entitled Welding Steels without Hydrogen Cracking by F.R. Coe. The technique has a sound scientific basis in that it accounts for base metal thickness, arc energy input, carbon equivalent, and hydrogen potential of the welding process. The publication also describes techniques for dealing with alloy steels.
- For the less technically inclined, the use of “look-up” tables is very common. These may be in very simple or very complex form. For ASME code users, the appendix of a book entitled Weldability of Steels by R.D. Stout and W.D.Doty can be a very useful source of preheat information. This appendix is based on WRC Bulletin 191 first published in January 1974 and republished in March 1978. Although the information may appear to be a bit dated (depending upon the current state of your career), it nevertheless addresses the complex issues of base metal thickness, carbon content and general chemistry (e, g., hardness and hardenability), and hydrogen potential.
- Other sections of the ASME code are often consulted for preheat information including ASME Section VIII, Division 1, Appendix R; ASME Section VIII, Division 2, Appendix D; and ASME Section I, A – 100.
- Several types of preheat calculators have been developed over the years. One common calculator is available from the Lincoln Electric Company. It incorporates the influence of hydrogen, carbon equivalent and thickness on preheat selection.
- Complex preheat calculation techniques have been published, which relate cooling rates calculated by various formulae (e.g., solutions to Rosethal’s equations for heat flow from a moving heat source) to time-temperature transformation (TTT or equivalent) diagrams. However, these techniques find little application within the pressure piping industry, due to the complexity of calculations, the need to select values for “constants” which are not constant over the temperature ranges involved in welding, and the lack of complete time-temperature transformation data for the materials involved. Of course, as computers continue to change our world, one may find increasing application of these more fundamental methods.
B31.3 does not restrict the methods of preheat, but some owner specifications do. Some methods of preheating include:
- Oxyfuel gas fired torch (propane, butane, and sometimes acetylene),
- Electric resistance elements,
- Induction coils, and
- Exothermic kits.
From a practical welding perspective, the method of heating is not generally an issue as long as the correct preheat temperature is achieved, with the heat uniformly applied throughout the full thickness and circumference of the joint. In some cases, the use of oxyacetylene torches is prohibited by owner specifications due to the intensity of the heat source and the risk of local damage to the base metal or weld metal if the heat is concentrated at one location.
B31.3 requires that the preheat temperature be checked to ensure that the temperature specified by the WPS is obtained prior to and during welding [¶330.1.3(a)]. However, B31.3 does not prescribe:
- The exact methods by which temperature must be measured,
- The location of temperature measurements, or
- The timing of temperature measurements.
temperature measurements:
- Temperature indicating crayons, thermocouple pyrometers, or other suitable means shall be used to measure temperature, [¶330.1.3(a)]
- Thermocouples may be attached by capacitor discharge welding without the need for welding procedure and performance qualifications, subject to visual examination of the area after thermocouple removal, [¶330.1.3(b)] and
- The preheat zone shall extend at least 1 inch beyond each edge of the weld. ( Note that many owner specifications require at least 2 inches and some as much as 6 inches) [¶330.1.4].
Although the Code definitions of preheat and interpass temperature refer to the deposited weld metal, temperature measurement directly on hot weld metal can result in contamination and is generally discouraged. Common industry practice is to measure preheat and interpass temperature in a manner which insures that the correct preheat has been reached from the edge of the welding groove to the outer limits of the specified preheat zone width.
Preheat temperature, by definition, is measured immediately before the start of welding; however, interpass temperature measurement can be the subject of some debate. When interpass temperature control is required by a WPS, the interpass temperature is normally measured immediately before the start of the next pass, at the location where the next pass will be started.
Purists may argue that by only measuring the temperature at the starting point of the next pass, it is possible for the next pass to be placed over weld metal thatis not exactly within the interpass range. It’s true, of course, but practically speaking, interpass temperature measurement for process piping is hardly an exacting science.
Gas for Shielding, Backing, and Purging [¶QW – 408]
Protection of hot and molten metal from the atmosphere is a necessary part of most welding operations. Protection may be accomplished using:
- externally supplied shielding, backing, and purging gases, and/or
- fluxes which decompose to give a slag covering and/or a gaseous shield.
Externally supplied protective gases prevent atmospheric contamination of the hot molten metal by displacing air from the weld area. In general, protective gases may be:
- Inert gases like helium or argon, which do not react with the hot metal,
- Reactive gases such as carbon dioxide, nitrogen, or hydrogen, which do react in a limited way with the hot metal and may be oxidizing or reducing depending upon the specific gas/metal interaction, or
- Mixture of inert and/or reactive gases (e.g., 75Ar/25CO2 ).
For many welding applications, shielding gases are actually mixturers of gases, with the composition of the mixture optimized to provide the best combination of shielding characteristics and process operating characteristics. Selection of a gas depends on several somewhat interrelated factors including:
- cost and availability at required purity levels,
- Ease of handling, stability, and physiological effects,
- Metallurgical characteristics including solubility in metals being welded, reactions with metals being welded and resultant degree of protection afforded to hot metal, effects on wetting behavior, effects on penetration as it affects type and thickness of metals to be welded, and effects on end properties of the weld deposit, and
- Welding process characteristics including welding position, ease of arc ignition as influenced by ionization potential of the gas, arc stability, and penetration as affected by thermal conductivity of the gas.
Solubility is a particularly important issue in gas selection, since dissolved gas in the molten metal can lead to porosity on freezing. Insert gases such as helium and argon have very limited solubility in most metals and are therefore used extensively for gas shielded arc welding processes.
Although carbon dioxide is virtually insoluble in most metals, it is reactive and will cause some surface oxidation and some loss of oxidizable elements. Nevertheless, carbon dioxide is used extensively for GMAW and FCAW of carbon and low alloy steels.
In some cases, limited amounts of certain gases are included in the shielding gas mixture to accomplish objectives other than shielding. Three examples are listed below:
- Nitrogen has been added to stainless steel shielding gases as an alloy addition, which imparts improved corrosion resistance and strength, and as a technique of controlling phase balance in duplex stainless steel weld metal.
- Oxygen may be added to argon in amounts typically from 1 to 5%, to improve wetting of stainless steel deposits, to improve bead shape, and to reduce undercutting.
- Hydrogen has been added to shielding gases to increase penetration characteristics, through increased arc voltage and consequent increased heat input.
As a word of caution, minor additions of reactive gases should not be attempted without thorough understanding of the consequences, and procedure qualification to evaluate the effect of such additions.
Cleaning [¶328.4.1]
[¶328.4.1] does provide some motherhood statements about cleaning, but a welding procedure should be specified about cleaning methods, solutions, abrasives, and tools. This is particularly true for nonferrous metals and stainless steels, since inappropriate cleaning methods can lead to cracking (prior to or in service) and/or loss of corrosion resistance.
¶328.5.1(d) prohibits peening on the root pass and final pass of a weld. Peening work hardens the metal, reduces ductility, and therefore increases the risk of cracking during or after welding. Peening between passes can be permitted because heat of subsequent weld passes heat treats (softens) the peened weld metal of previous passes. Note that chipping necessary for slag removal is not considered to be peening.
¶328.5.1(e) is intended to prohibit welding under adverse weather conditions. Moisture can cause porosity and hydrogen cold cracks. Excessive wind blows shielding away causing porosity and brittle welds, for both gas shielded and coated electrodes. Another practical issue with excessive wind under dry or arid conditions is the swirling of dirt, within the welder’s helmet, making it difficult to see the weld pool. If you cann’t see what you’re doing, you can’t weld.
¶328.5.1(f) provides some general advice on preserving the seat tightness of weld end valves. The valve manufacturer should always be consulted concerning welding conditions appropriate to maintaining seat tightness and responsibility for dismantling, reassembly, and testing when necessary.
Some issues to consider include characteristics of sealing materials and risk of heat damage (e.g., plastic or metal-to-metal seat elements), use of extended bodies for soft seated valves, or use of a water quench to cool have materials which do not transformation harden(e.g., austenitic stainless steels).
¶328.5.3 indicates that seal welds must be done by a qualified welder. While this requirement may seem obvious, significant commercial gains can be made through the use of unqualified welders. The need for seal welds to cover all threads is imposed to avoid notch effects, which could cause brittle fracture or fatigue cracks. For the record, a seal weld is not a back weld.
Mechanical Testing
Mechanical testing requirements for welding procedures are found in ASME Section IX. However, if the base metal will not withstand the 180 degree guided bend test required by ASME Section IX, B31.3 permits qualification if the weld bend specimen will undergo the same degree of bending as the base metal (within 5 degree) [¶328.2.1(b)].
As well, when impact testing is required by the Code or engineering design, B31.3 indicates that those requirements shall also be met in qualifying weld procedures [¶328.2.1(d)].
Heat Treatment [¶331]
Heat treatment is used to minimize certain detrimental effects associated with welding, bending and forming processes [¶331].
Depending on the nature of each process, attendant high temperatures, severe thermal gradients, and/or severe metal forming operations (cold work) can result in dramatic loss of toughness, reduction of ductility, increased hardness, and/or high residual stresses. In turn, these can lead to premature, unexpected, and potentially catastrophic failures caused by brittle fracture, fatigue cracking, stress corrosion cracking, and/or hydrogen embrittlement.
B31.3 provides basic heat treatment practices suitable for most welding, bending, and forming operations, but warns that they are not necessarily appropriate for all service conditions [¶331].
Common examples where compliance with minimum B31.3 heat treatment requirements could be considered inappropriate include process streams containing caustics, amines used for gas sweetening operations, and hydrogen sulfide. In the case of process streams containing hydrogen sulfide, it is known that the minimum temperature allowed by Table 331.1.1 may not cause sufficient softening for resistance to sulfide stress cracking in severe sour environments.
This accounts for the careful wording in clause 5.3.1.3 of NACE Standard MRO175-95, which states: “Low-alloy steel and martensitic stainless steel weldments shall be stress relieved at a minimum temperature of 620ºC (1150ºF) to produce a maximum hardness of 22 HRC maximum.” Typically, temperatures required to satisfy the 22 HRC maximum criterion for low alloy steels are well above 620ºC (1150ºF). given the toxic nature of sour environments, before construction one should confirm that proposed heat treatment cycles are capable of satisfying maximum hardness restrictions.
Confirmation would typically involve cross-sectional hardness surveys of the welding procedure qualification test coupons.
Forms of Heat Treatment
There are many forms of heat treatment, each intended to accomplish a certain task. Frequently, more that one task is accomplished by a particular thermal cycle. Heat treatments listed in B31.3 table 331.1.1 are best described as stress relieving heat treatments, since the primary purpose of the treatment is the reduction of residual stresses due to welding, forming, or bending operations.
Such treatment may also result in improved ductility, lower hardness (note that B31.3 does impose some hardness restrictions), better toughness, and reduced distortion during subsequent machining operations.
B31.3 also allows the use of annealing, normalizing and tempering, in lieu of a required heat treatment after welding, bending, or forming, provided that the mechanical properties of any affected weld and base metal meet specification requirements after such treatment and that the substitution is approved by the designer [¶331.2.1].
Stress relief of carbon and low alloy steel is carried out at a temperature slightly below the lower critical temperature (A1 ) of the steel, hence there is some use of the term subcritical stress relief (i.e., there is no phase transformation at subcritical temperatures).
For high alloy materials, such as austenitic stainless steels, considerably higher temperatures are required for effective stress relief due to the inherent hot strength of these materials. Although B31.3 does not mandate application of heat treatment to austenitic stainless steels, when applied (e.g., for service reasons), it is usually carried out at a temperature of approximately 1650ºF.
Annealing is a common term in the heat-treating business, but there are many types of anneal. A full anneal is performed at high temperature (e.g., about 50 to 100ºF above the upper critical temperature for carbon steels), followed by slow cooling, generally in a furnace. It provides maximum softening, resulting in lowest hardness and strength.
A stress relief anneal is performed on carbon and alloy steels at a temperatures slightly below the lower critical temperature, and many also be known as a subcritical stress relief or subcritical anneal.
Both the stress relief anneal and full anneal are applied as softening treatments, but other effects may result from the thermal cycles including changes to mechanical properties, physical properties, and microstructure.
Although “full anneal” is generally implied when the word “anneal” is used without any qualifier, if a “full anneal” is required, fewer surprises will occur if the term “full anneal” is used.
Sometimes the term solution anneal is used to describe what might properly be called a solution heat treatment. In this case, an alloy is heated to a temperature high enough to dissolve one or more constituents into solid solutions, and then cooled rapidly enough to hold the constituents in solid solution.
Solution heat treatments are generally applied to highly alloy steels and other high alloy materials for the purpose of dissolving one or more constituents, which may affect the properties of the material. For example, many of the austenitic stainless steel pipes purchased according to ASTM A 312 are supplied in the solution treated condition.
Normalizing of carbon and low alloy steels is carried out by heating to a temperature range similar to that used for a full anneal, but the parts are allowed to cool in still air. This can save time and money compared to annealing, if the soft structure of the full anneal is not required. Normalizing is also effective in refining the grain size and homogenizing the structure, resulting in better toughness, more uniform mechanical properties, and better ductility.
Tempering is a heat treatment, which may be applied to transformation hardenable steels after a normalizing operation and is generally applied after a quenching operation. Tempering is carried out below the lower critical temperature. It is used to reduce hardness and improve toughness and ductility at the expense of reduced strength.
Heat Treatment Requirements
¶331.1.1 imposes the following heat treatment requirements:
- Heat treatment shall be in accordance with the material groupings and thickness ranges in Table 331.1.1 except as provided in ¶331.2.1 and ¶331.2.2.
- Heat treatment to be used after production welding shall be specified in the WPS and shall be used in qualifying the welding procedure.
- The engineering design shall specify the examination and/or other production quality controls (not less than the requirements of B31.3) to ensure that the final welds are of adequate quality.
- Heat treatment for bending and forming shall be in accordance with ¶332.4.
Governing Thickness for Heat Treatment of Weld [¶331.1.3]
B31.3 contains a detailed treatment of metal thickness rules governing the need for heat treatment, as well as exceptions to the rules [¶331.1.3]. Table 6.8 below may be used to assist with interpretation of B31.3 requirements.
Table 6.8 Governing Thickness and Exemptions for Postweld Heat Treatment (PWHT) of Welds
Weld Type |
PWHT Governing Thickness And Exceptions |
Butt Welds and welds not covered elsewhere in this table |
PWHT required when the thickness of the thicker component measured at the joint exceeds the limits provided in Table 331.1.1. No exceptions. |
Branch Connection Welds for set-on or set-in designs, with or without reinforcement, as per Fig. 328.5.4 D |
PWHT required when the thickness through the weld in any plane is greater than twice the minimum material thickness requiring heat treatment as specified in Table 331.1.1. No exceptions. See B31.3 for assistance with weld thickness calculations |
Fillet Welds for slip-on, socket, and seal welded connections NPS 2 and smaller; and for external nonpressue parts such as lugs and pipe supports in all pipe sizes |
PWHT required when the thickness through the weld in any plane is more than twice the minimum material thickness requiring heat treatment as specified in Table 331.1.1. There are three exceptions to this rule:
|
(1) Note that this can be a dangerous exception for some services and should be used with caution. Just because the filler metals do not harden, doesn’t mean the heat-affected zones of the base metals have not hardened. Furthermore, just because the deposited filler metal may be in a soft and ductile condition, doesn’t mean the base metal heat affected zones are in the same condition. |
Equipment and Methods of Heat Treatment
B31.3 does not impose limitations on heating equipment and methods. It only indicates that the heating method must provide the required metal temperature, metal temperature uniformity, and temperature control, and then lists methods which may be used for heating including furnace, local flame heating, electric resistance, electric induction, and exothermic chemical reaction [ ¶331.1.4].
Heating methods used for heat treatment may be classified in terms of the facility used for heat-treating and the energy source. Facilities can be discussed in terms of local heat treatment and furnace heat treatment.
- Local heat treatment involves the heating of a small band of metal. Normally the band being heat-treated is stationary, but in some manufacturing operations, the band moves. Examples of moving bands include in-line-tempering operations used during manufacture of quenched and tempered pipe and local heating operations used in the manufacture of induction bends.
- Furnace heat treatment generally involves placing the item to be heat treated inside a permanent furnace operated by a fabrication shop or commercial heat treater. However, it is possible to construct temporary heat treatment facilities (e.g., at the job site), which may range from simple ad hoc insulated box constructions to complex portable furnaces.
There are several energy sources used in heat-treating. Current commercial sources of heat energy and characteristics are discussed below:
- Electric resistance heat is produced when an electric current is passed through wires made from a material with high electrical resistivity. The electric current increase atomic movement in the wire, and this energy is then released in the form of heat. There is a wide selection of heating elements available in the marketplace, with various sizes and shapes to fit practically any geometry. Heaters are flexible and durable and are commonly used for local heat treatment of welds during field construction. Although resistance elements may burn out or short circuit against the pipe, there are several advantages supporting use of electric resistance heat, especially for local heat treatment of welds.
- Heat can be continuously and evenly applied.
- Temperature can be adjusted accurately and quickly.
- Welders can work in relative comfort. For preheating applications, they do not have to stop intermittently to raise preheat temperature.
- Heat input can be adjusted fairly easily for example, to control the amount of heat applied to different pipe quadrants or sections of dissimilar thickness such as weld-in valves.
- Heat can be produced by chemical reaction using exothermic kits. The chemical composition of constituents in modern exothermic heat kits is proprietary, however. When materials in the kit are reacted, heat is released. Heating cycles are controlled in terms of the size, shape, and heating value of the exothermic charge; the size, shape, and mass of the component to be heat treated; and the local environmental conditions. Although exothermic kits offer the advantages of portability, low capital equipment cost, and simple operator training, they have two major limitations:
- Once the kit has been ignited, it is difficult to perform any further adjustments.
- It is usually difficult or impossible to satisfy Code and owner requirements on heating rate, holding time, and cooling rate.
For these reasons, use of exothermic kits is restricted by many owner specifications, except perhaps for infrequent use at remote locations such as drilling sites. Successful application of exothermic kits requires careful planning and contingency measures.
- Radiant heaters use infrared radiation generated by a gas flame or quartz lamp to develop heat. Infrared radiation is a form of electromagnetic radiation, which behaves similarly to light. The intensity of the radiation falls off in proportion to the square of the distance between the heat emitter and the part heated. Radiation reaching the part is either absorbed, causing the temperature of the part to increase, or reflected (wasted). Consequently, surface condition of the metal will affect the efficiency of the process, as will the relative positions of the heater and the part, since the heater must “see” the part for effective heating.
- Induction coils create heat with the passage of alternating current (ac). The alternating magnetic field associated with the alternating electrical field penetrates the metal to be heated, changes strength and direction in phase with the external alternating electric current, and produces eddy currents in the part to be heat-treated. The rise and collapse of magnetic fields and their associated eddy currents stimulate atomic movement resulting in the release of heat within the part.
Temperature Measurement
B31.3 does not impose restrictions on the devices used for temperature verification [¶331.1.6]. Although devices such as temperature indicating crayons, thermometers, and optical pyrometers may be used, thermocouple pyrometers are generally used to measure and record the temperature of the surfaces being heat-treated. For proper temperature measurement, the hot end of the thermocouple junction must be in direct contact with the surface of the pipe or kept at the same temperature as the pipe by being inserted into a terminal joined to the pipe.
B31.3 does not impose any restrictions on the thermocouple attachment methods. To this end, one may observe on various job sites, attachment of thermocouples using steel bands, wire, ad hoc clamping devices, or weld metal. The suitability of any of these thermocouple attachment methods should be addresses by specifications developed during the engineering design or by QA/QC personnel monitoring the work. For example, steel bands or wires can become loose at the heat treatment temperature so that the thermocouple is no longer in contact with the surface, leading to false temperature readings. Ad hoc clamping devices can work loose, and the attachment method of such devices can cause local damage to the pieces being heat-treated. Use of weld metal to fix the thermocouple to the pipe surface changes the composition of the junction, resulting in measurement error. Experience with attachment of thermocouples by capacitor discharge welding indicates that the process works well. B31.3 has specific statements permitting the attachment of thermocouples to pipe using capacitor discharge welding without the need for weld procedure and performance qualifications [¶331.1.6, ¶330.1.3(b)]
B31.3 does not address the number of thermocouples required or the placement of thermocouples. Although these issues should be dealt with in construction specifications, perhaps discussion of a few sources of measurement error would be useful in making such determinations.
- Heat rises. With local heat treatment, the temperature measured on the top of a pipe will normally be higher than the temperature measured on the bottom of the pipe. Typically, as diameter increases, steps are necessary to allow introduction of more heat at the bottom and sides of the pipe than at the top of the pipe. The need for additional temperature measurement points and heating controls does have commercial implications.
- The pipe will be hottest adjacent to the source of the heat. During local heat treatment, the pipe is normally heated from the outside, so the inside surface will be a bit cooler than the outside surface, depending upon the thickness of the pipe and the extent to which insulation is used and drafts prevented. For example, if the bore of the pipe is not plugged with insulation and the wind is whistling through it, a substantial difference between the inside and outside surface temperatures might be expected. Since heat treatments are often conducted for service reasons, and the service is usually on the inside of the pipe, specific attention is required to ensure that the inside surface is adequately heated (and that the outside surface is not excessively heated).
- The surface temperature of a resistance coil or other radiant heat source is considerably above that of the pipe being heated. If the hot junction of the thermocouple is not insulated form the heat source, the temperature reading will be higher than the actual temperature at the pipe surface.
- Thermocouple wires should run along the pipe surface under the insulation for several inches before coming outside the insulation on the pipe surface. If the wires are brought straight out of the insulation from the point of contact with the pipe, heat may be conducted away from the hot junction leading to a temperature reading lower than the pipe surface.
- Measurement errors may be introduced if extension wires are not of the same composition as the thermocouple wires, all the way from the hot junction to the cold junction. Don’t accidentally reverse the wires at a connection point.
- Ensure that instrumentation is properly calibrated. Battery operated circuits should be calibrated at regular intervals and the output of regulated power supplies should be checked occasionally for accuracy.
- Damaged or contaminated thermocouples and extensions can lead to measurement error and should be checked regularly for physical damage (severe bends, kinks, partially broken wires, weld spatter or slag trapped between the wires).
Heating and Cooling Rates [¶331.1.4]
B31.3 does not impose restrictions on heating and cooling rates [¶331.1.4]. ASME Section VIII, Division 1, UCS-56 requirements are frequently applied, but there are causes where insulation and coils are ripped off immediately after the soak period. In the stress relieving business, time is money, especially if the heat treater is working by the weld or lump sum. So, if heating and cooling rates need to be controlled, it should be stated in specifications or other contract documents.
Hardness Tests[¶331.1.4]
B31.3 makes the following statements regarding hardness testing.
Hardness tests of production welds and of hot bent and hot-formed piping are intended to verify satisfactory heat treatment. Hardness limits apply to the weld and to the heat affected zone (HAZ) tested as close as practicable to the edge of the weld.
- Where a hardness limit is specified in Table 331.1.1, at least 10% of welds, hot bends, and hot formed components in each furnace heat treated batch and 100% of those locally heat treated shall be tested.
- When dissimilar metals are joined by welding, the hardness limits specified for the base and welding materials in Table 331.1.1 shall be met for each material.
The Code does not discuss many of the technical details necessary to give an accurate and representative appraisal of production weld hardness. Consequently, owner specifications are recommended for guidance on applying this simple but often misused and abused test method. Owner specifications should consider the size of hardness indentations relative to the size of weld zones to be measured, surface preparation of the weld, methods for locating the zones of interest, and training requirements for hardness testing personnel.
********
ASME B 16.5
PIPE FLANGES AND FLANGED FITTINGS
- SCOPE :
General :
This Standard covers
-
- Pressure temperature ratings, materials, dimensions, tolerances, marking, testing.
- for pipe flanges and flanged fittings in sizes NPS ½ through NPS 24 and in rating Classes 150, 300, 400, 600, 900, 1500 and 2500,
- Flanges and flanged fittings may be cast, forged, or ( for blind flanges and certain reducing flanges only ) plate materials,
- Requirements and recommendations regarding bolting and gaskets are also included.
Codes and Regulations :
A flange or flanged fitting used under the jurisdiction of other codes is subject to any limitation of that code or regulation. This includes any maximum temperature limitation, or rule governing the use of a material at low temperature, or provisions for operation at a pressure exceeding the pressure temperature ratings in this Standard.
- PRESSURE-TEMPERATURE RATINGS
Rating Basis
Ratings are maximum allowable working gage pressures at the temperatures shown in Tables for the applicable material and rating. For intermediate temperatures, linear interpolation is permitted.
Rating Temperature
The temperature shown for a corresponding pressure rating is the temperature of the pressure containing shell of the flange or flanged fitting. In general, this temperature is the same as that of the contained fluid subject to the requirements of the applicable code or regulation. For any temperature below –20oF, the rating shall be no greater than the rating shown for –20oF.
Temperature Considerations
Flange Attachment
Socket welding and threaded flanges are not recommended for service above 500oF or below –50oF if severe thermal gradients or thermal cycling are involved.
High Temperature Service
At temperatures in the creep range, gradual relaxation of flanges, bolts, and gaskets may progressively reduce bolt loads. It may be necessary to arrange for periodic tightening of bolts to prevent leakage. Joints subject to substantial thermal gradients may require the same attention.
When used above 400oF, Class 150 flanged joints may develop leakage unless care is taken to avoid imposing severe external loads and/or severe thermal gradients. For other classes, similar consideration should be above 750oF.
Low Temperature Service
Some of the material listed in the rating tables undergo sufficient decrease in toughness at low temperatures that they cannot safely sustain shock loadings, sudden changes of stress or temperature, or high stress concentrations.
System Hydrostatic Test
Flanged joints and flanged fittings may be subjected to system hydrostatic tests at a pressure not to exceed 1.5 times the 100oF rating rounded off to the next higher 25 psi.
- SIZE
The size of a flange or flanged fitting covered by this Standard is its nominal pipe size, NPS. Use of “nominal” indicates that the stated size or dimension is only for designation, not measurement. The actual dimension may or may not be the nominal size.
- MARKING
Name
The manufacturer’s name or trademark shall be applied.
Material
- Cast flanges and flanged fittings shall be marked with ASTM specification, grade identification symbol, and the melt number or melt identification.
- Plate flanges, forged flanges, and flanges fittings shall be marked with ASTM specification number and grade identification symbol.
- A manufacturer may supplement these mandatory material indications with his trade designation for the material grade, but confusion of symbols shall be avoided.
Rating Class
The marking shall be the applicable pressure rating class : 150, 300, 400, 600, 900, 1500 or 2500.
Designation
The designation B16 shall be applied preferably located adjacent to the class designation, to indicate conformance to this Standard.
Size
The nominal pipe size shall be given.
- MATERIALS
General
Flanges and flanged fittings covered by this Standard shall be castings, forgings and (for blind flanges only) plate.
Toughness
Some of the materials listed in Table 1A undergo a decrease in toughness when used at low temperatures, to the extent that Codes referencing this Standard may require impact tests for application even at temperatures higher than +20oF. It is the responsibility of the user to assure that such testing is performed.
Gaskets
The user is responsible for selection of gasket materials which will withstand the expected bolt loading without injurious crushing, and which are suitable for the service conditions.
- DIMENSIONS
Wall thickness
For inspection purposes the minimum wall thickness tm of flanged fittings at the time of manufacture shall be as shown in Tables 10, 13, 16, 19, 22, 25 and 28, except as provided in para 6.1.1. See Annex D for the basis used to establish values of tm.
Additional metal thickness needed to withstand assembly stresses, shapes other than circular, and stress concentrations must be determined by the manufacturer, since these factors vary widely. In particular, 45 deg. Laterals, true Y’s and crosses may require additional reinforcement to compensate for inherent weaknesses in these shapes.
Local areas having less than minimum wall thickness will be acceptable provided that :
- the area of subminimum thickness can be enclosed by a circle whose diameter is no greater than 0.35 √dtm where d is the inside diameter as defined above and tm is the minimum wall thickness as shown in the tables listed in para 6.1; and
- measured thickness is not less than 0.75 tm; and
- enclosure circles are separated from each other by an edge-to-edge distance of more than 1.75 ____
√ dtm.
Facings
Table 4 gives dimensions for facings other than ring joint. Table 5 gives dimensions for ring joint facings. Figure 7 shows application of facings. Classes 150 and 300 fittings and companion flanges are regularly furnished with a 0.06 in. raised face which is included in the minimum flange thickness C. Classes 400, 600, 900, 1500 and 2500 fittings and companion flanges are regularly furnished with 0.25 in. raised face which is additional to the minimum flange thickness C. Any other facing than the above, when required for any class, shall be furnished as follows.
No metal shall be cut from the minimum flange thickness specified herein.
In the case of the 0.25 in. raised face, tongue or male face (other than 0.06 in. raised face for Classes 150 and 300), the minimum flange thickness C shall be first provided and then the raised face, tongue or male face shall be added thereto.
With ring joint, groove, or female face, the minimum flange thickness shall be first provided and then sufficient metal added thereto so that the bottom of the ring joint groove, or the contact face of the groove or female face is in the same place as the flange edge of a full thickness flange.
Flange Facing Finish
The finish of contact faces of pipe flanges and connecting end flanges of fittings shall be judged by visual comparison with Ra standards ( see ASME B46.1 ) and not by instruments having stylus tracers and electronic amplification. The finishes required are given below.
Flange facings
Either a serrated concentric or serrated spiral finish having a resultant surface finish from 125 uin. To 250 uin. Average roughness shall be furnished. The cutting tool employed should have an approximate 0.06 in. or larger radius, and there should be from 45 grooves/in. through 55 grooves/in.
Flange Facing Finish Imperfections
Imperfections in the flange facing finish shall not exceed the dimensions shown in Table 3. Adjacent imperfections shall be separated by a distance of at least four times the maximum radial projection. A radial projection shall be measured by the difference between an outer radius and an inner radius encompassing the imperfection where the radii are struck from the centerline of the bore. Imperfections less than half the depth of the serrations shall not be considered cause for rejection. Protrusions above the serrations are not permitted.
Spot Facing
All cast and forged flanges and flanged fittings shall have bearing surfaces for bolting which shall be parallel to the flange face from within 1 deg. Any back facing or spot facing required to accomplish parallelism shall not reduce the flange thickness C below the dimensions given in Tables 9, 10, 12, 13, 15, 16, 18, 19, 21, 22, 24, 25, 27, and 28. Any spot facing or back facing shall be in accordance with MSS SP-9.
- TEST
Flanged Fitting Training
Each flanged fitting shall be given a hydrostatic shell test as specified below :
Flange Testing
Flanges are not required to be hydrostatically tested.
Hydrostatic Shell Test
The hydrostatic shell test for flanged fittings shall be no less than 1.5 times the 100oF rating rounded off to the next higher 25 psi increment.
The test duration shall be minimum of one min for fittings NPS 2 and smaller, 2 min for fitting NPS 2 ½ -NPS 8, and 3 min for fittings NPS 10 and larger.
No visible leakage is permitted through the pressure boundary wall.
LIMITING DIMENSIONS OF GASKETS
GASKET DIMENSIONS
The actual dimensions of a gasket must be established by the user. Reference to a dimensional standard for gaskets, such as ASME B16.21, is recommended.
Limiting gasket dimensions are given in Tables E1, E2, and E3. These dimensions represent approximately the maximum combinations of widths and diameters of the different types of gaskets covered which meet rating requirements.
Gaskets are divided into three groups based on their gasket loading factors as shown in the ASME Boiler and Pressure Vessel Code, Section VIII, Division 1, Pressure Vessels.
Gasket contact widths for the three groups are as follows :
Group No. I Slip-on flange raised face width
Group No. II Large tongue width
Group No. III Small tongue width minus 0.03 in., but not less than 0.18 in.
Gaskets of Group No. Ia have inside diameters equal to the outside diameter of the corresponding pipe, which follows the principle established in ASME B16.21. In order to avoid pocketing of fluid handled, Group No. I gaskets may be extended to the inside diameter of valves, pipe, or the bore of integral, welding neck, or socket weld type flanges. Group No. Ia gaskets have outside contact diameters equal to the outside diameter of the raised face.
Gaskets of Groups Nos. IIa and IIIa also have inside diameters equal to the outside diameter of the corresponding pipe. It may be desirable under some conditions to make the inside diameter of these gaskets equal to the inside diameter of valves, pipe, or the bore of integral, welding neck, or socket weld type flanges, and this is permissible provided the gasket contact width does not exceed than shown. This provision affects gasket shown in Figs. E4, E5, E8 and E9 and requires a reduction in gasket outside diameters as well as inside diameters.
Additional provisions for varying gasket widths in contact with raised face are covered in para E3(b). Group Nos. IIb and IIIb have outside contact diameters equal to the outside diameter of the raised face.
The outside diameter of gaskets or centering rings extending beyond the raised face is equal to the bolt circle minus one bolt diameter. This type gasket is designed to be aligned by the flange bolts.
Group Nos. IIa and IIIa gaskets are designed for those users who prefer that narrow gaskets be located close to the bore, thereby keeping the pressure area to a minimum and giving maximum flexibility to the flanged joint. See para E3(f). Group Nos. IIb and IIIb gaskets are to be located at the outside of the raised face for ease in aligning the gaskets without a centering ring.
TOLERANCES
Gasket contact widths for Group Nos. II and III shall not exceed specified contact width by more than 10%.
STUDY OF ASME SECTION IX
(WELDING QUALIFICATIONS)
Chap. 1 Introduction to welding qualifications
Chap. 2 Establishing WPS
Chap. 3 PQRs and WPQs and Acceptance Standards
Chap. 4 A Note on Consumables
Chap. 5 Guidelines for review of WPS, PQR
Chap 6 Road map for review of WPS/PQR
- INTRODUCTION TO WELDING QUALIFICATIONS.
“A welding procedure is the detailed methods and practices involved in the production of a weld ment”.
The written welding procedure, required by codes, comprises the step-by-step directions for making a specific weld and proof that the weld is acceptable.
Codes also require proof that welders and welding operators have the necessary skill and ability to follow the welding procedure successfully. This requires that welders and welding operators make specific welds, which are then tested to prove that the welder can produce the weld quality required.
Section IX of the ASME Boiler and Pressure Vessel Code covers welding and brazing qualifications. It is entitled ”Qualification Standard for Welding and Brazing Procedures, Welders, Brazers, and Welding and Brazing Operators”.
This code makes the following statement concerning responsibility : “Each manufacturer or contractor is responsible for the welding done by his organization and shall conduct the tests required to qualify the welding procedures he uses and the performance qualifications. These records shall be certified by the manufacturer or contractor and shall be accessible to the authorized inspector.”
The ASME code calls the welding procedure a Welding Procedure Specification (WPS). This document provides in detail the required conditions for specific applications to assure repeatability by properly trained.
Welders and welding operators. A WPS is a written welding procedure prepared to provide direction for making production welds to code requirements. The ASME provides a sample form, which may be used or modified provided that it covers all information.
The WPS provides directions to the welder or welding operator to assure compliance with the code requirements. The complete WPS describes all of the essential, nonessential, and supplementary essential (when required) variables for each welding process. The WPS should reference the supporting procedure qualification record (PQR). A PQR is a record of the welding data used to weld the test coupons. It shows all conditions that were used when welding the rest coupons and the actual results of the tested specimens. The completed PQR should record all essential and supplementary essential (when required) variables for each welding process used to weld the test coupon. Nonessential or other variables used during the welding of test coupons need not be recorded.
The PQR should be certified accurate by the manufacturer or contractor. This certification is the manufacturer’s or contractor’s verification that the information is a true record the variables that were used during the welding of the …. coupon and that the test results are in compliance ….. Section IX of the code. The manufacturer or contractor cannot subcontract this certification function.
There are three types of variables for welding procedure specifications WPS. “Essential variables” are those in which change is considered to affect mechanical properties of the weld joint or weldment. “Supplementary essential variables” are required for metals for which notch toughness tests are required. “Nonessential variables” are those in which a change may be made in the WPS without re-qualifications.
The variables for each welding process is listed in detail in Section IX. For this reason it is necessary to refer to the code when writing, testing, or certifying the welding procedures.
Welding Procedure Specification :
To help explain the welding procedure specification (WPS) an example is shown. In this example, the ABC Pressure Vessel Company is using the gas metal arc welding process, semi automatically applied for welding P-1 grade steel pipe in the horizontal fixed and vertical positions. Each entry will be explained briefly.
Joints :
The joint design is a single ‘V ‘ groove with a 60 to 700 included angle. It is recommended that a sketch be drawn on the form in the area under details. If more space is needed, use a third sheet. The welding parameters are placed in the table provided. Backing is not used, and backing materials need not be described. However, if backing is used, it must be described.
Base Metals :
To reduce the number of WPS required, P numbers are assigned to base metals depending on characteristics such as composition, weldability, and mechanical properties. Groups within P number are assigned for ferrous metals for the purpose of procedure qualifications where notch toughness requirements are specified. The same P numbers group the different base metals having comparable characteristics.
The P numbers and groupings of most of the different steels are given in the Section IX. Base metal classifications and groupings in AWS B2.1 are slightly different. If a P number is not available for the material involved, its ASTM specification number may be used. If an ASTM specification number is not available, the chemical analysis and mechanical properties can be used. Under base metals the thickness range must be shown, and if it is in pipe, the pipe diameter range must be shown.
Filler Metals :
Electrodes and welding rods are grouped according to their usability characteristics, which determines the ability of the welders to make satisfactory welds with a given filler metal. This grouping is made to reduce the number of WPSs needed. The groups are given F numbers, which relate to the composition and usability. This is filled in on the form. This block also requires ASME specification number and the AWS classification number of the filler metal used.
The ASME specification numbers are the same as the AWS specification number with the addition of the letters SF. These data are given in ASME Section IX and in the AWS B2.1 document. The AWS classification number for the filler metal specification is also given on the label on the filler metal box. The A number is the classification of weld metal analysis. For example, A-1 has a mild steel weld metal deposit. This classification system is given in both specifications.
The size of the filler metal, which is its diameter, must be shown as well as deposited weld metal thickness range for groove or filler welds. In the case of submerged arc, the consumable insert analysis should be shown. Other information relating to filler metals not mentioned above should be given, when available.
Position :
The welding position of the groove or fillet weld must be described according to AWS terminology. If vertical welding is involved, it should be mentioned whether progression is upward (uphill) or downward (downhill).
Preheat :
A minimum temperature shall be given as well as the maximum interpass temperature. Preheat maintenance temperature should be given. Where applicable, special heating should be recorded.
Postweld Heat Treatment :
If a postweld heat treatment is used, it must be described. This includes the temperature range and the time at temperature. If there is not postweld heat treatment, write in “none”.
Gas :
This shielding gas should be identified, and if it is a mixture, should be described. The shielding gas flow rate should be recorded. If backing gas or trailing shield gas is used, the gas composition should be given and flow rate recorded.
Electrical Characteristics :
The welding current should be shown as alternating (ac) or direct current (dc). If direct current is used, the polarity of the electrode should be reported. The amperes and voltage range should be recorded for each electrode size, position, and thickness. This is also presented in a tubular form
In the case of gas tungsten arc welding the tungsten electrode size and type should be described. For gas metal arc welding the mode of metal transfer must be described. The electrode wire feed speed range should be recorded.
In the case of gas tungsten arc welding the tungsten electrode size and type should be described. For gas metal arc welding the mode of metal transfer must be described. The electrode wire feed speed range should be recorded.
Technique :
Under technique, describe the weld as made with stringer or weave beads. Oscillation should be used to make weave beads. This should also show in the sketch. Often, both techniques are used in the same weld. For the gas-shielded process the nozzle inside diameter should be recorded. The method of cleaning before welding and between passes must be recorded. If back gouging is employed, it should be described. The contact tip-to-work distance should be described as a minimum-to-maximum dimension.
It should be stated whether multiple or single-pass technique is used. It is also necessary to indicate whether a single electrode or multiple electrodes are used. It is also necessary to indicate whether a single electrode or multiple electrodes are used. The travel speed range should be described. Peening, if used, must be described, and any other pertinent information concerned with making the weld should be mentioned. For example, pulsing, if employed, would need to be described.
Procedure Qualification :
Record to support the welding procedure specification (WPS), it is necessary to test and certify the weld results. This is done by making the welds described in the WPS, machining them, and testing the specimen in accordance with the code. This is done by the procedure qualification record (PQR) defined as a document providing the actual welding variables used to produce an acceptable test weld, and the results of tests conducted on the weld for the purpose of qualifying a welding procedure specification (WPS). It must reference a specific WPS.
An example of a procedure qualification record is shown in Figures , which are similar to ASME QW-483. This sample PQR is a record of actual conditions used to weld the coupons made in accordance with WPS.
Many of the data required by the PQR are the same as the information on the referenced WPS. In fact, the data on the front sheets are almost identical. The back (sheet 2 of 2) of the PQR is straight forward and is a record of the mechanical test, the tensile test, the guided bend test, the toughness test when required, and the filler weld test when used.
A toughness test, either impact or drop weight, is not required by Section IX of the code. These tests may be required by other sections of the code and must be made according to other provisions of the code or an ASTM specification. The example shows typical data that would be entered.
If the test data meet the requirements of the code, the form is then signed by the manufacturer’s representative, certifying that the statements in the record are correct and that the test welds were prepared, welded, and tested in accordance with requirements of Section IX of the ASME code. The test record of the PQR qualifies the WPS and fulfills the requirements for the code. All changes to a PQR require recertification by the manufacturer or contractor.
It is necessary to have specific WPSs and PQRs to cover all the weld processes, combination of welding processes, different P groupings of base materials and so on, to comply with the variables involved. Every process and base metal used in production of the product must be covered by a WPS, which must be qualified by a PQR.
Record of Welder Qualification Tests :
With the WPS and PQR documents in order, it is then necessary to test the welders and welding operators for the work to be done. Each welder and welding operator involved in manufacturing or installing the products covered by the ASME Boiler and Pressure Vessel Code must be qualified.
The welder who prepares the procedure qualification record (PQR) specimens that pass code requirements is personally qualified within his or her performance qualification variables. All other welders and welding operators are qualified by specific welding tests, which are designed to determine the ability of the welder or welding operator to make welds required by the WPS that will cover work. An example of the “Record of Welder or Welding Operator Qualification Tests” is shown by Figure 21-7, which is similar to ASME QW-484.
The record of welder or welding operator performance qualification tests should include the essential variables, the type of test and test results, and the ranges qualified, for each welder and welding operator. Each welder and welding operator should be assigned an identifying number, letter, or symbol. It is used to identify the work of that person. The tests assigned are in accordance with the code and the mechanical tests should meet the requirements applicable by the code. Radiographic examination may be substituted for mechanical tests accept for GMAW using short-circuiting metal transfer. The radiographic technique and acceptance criteria should be in accordance with the code. In general, welders who meet the code requirements for groove welds are also qualified for filler welds, but not vice versa. A welder qualified to weld in accordance with one qualified WPS is also qualified to weld in accordance with other qualified WPSs using the same welding process, within the limits of the essential variables according to the code..
If a welder has not welded for a period of three months or more, his or her qualifications shall be expired. If there is reason to question the welder’s ability to make welds that meet the specifications, his or her qualification shall be considered expired. There are various other conditions relative to welder qualifications listed in the code. The code must be consulted for this information.
2. ESTABLISHING WPS
ASME Section IX relates to qualification of welders, welding operators, brazers and brazing operators and the procedures that they employ in welding and brazing.
It is divided into parts, part QW gives requirements for welding and part QB contains requirements for brazing. For the purpose of this course we shall deal only with part QW.
WPS & PQR
The purpose of welding procedure specification (WPS) and procedure qualification records (PQR) is to determine that the weldment proposed for construction is capable of providing the required properties for its intended application.
WPS is intended to provide direction for the welder and lists the variables, both essential and non essential and the acceptable ranges of these variables when using the WPS.
It is presumed that welder or welding operator performing the welding procedure qualification test is skilled workman so that welding procedure qualification test establishes the properties of weldment and not the skill of the welder.
The purpose of performance qualification is to determine if the welder is able to deposit sound metal or the welding operator is able to operate welding equipment properly.
Part QW is divided into 4 articles.
Article I – Welding general requirements
Article II – Welding procedure qualifications
Article III – Welding performance qualifications
Article IV – Welding data
Before we proceed let us first understand various test position in groove welds in plates, groove welds in pipes and fillet weld in plates etc. (Ref. Figure 461.3, 4 & 5)
In general, 1G or 1F is called flat positions
2G or 2F is called horizontal and circumferential
3G or 3F is called vertical position &
4G or 4F is called overhead position
Position 5G is only in welds in pipes. It is a position when pipe axis is held horizontal and circumferential seam is welded without rotating. In a way it is combination of 1G, 3G & 4G.
Position 6G is also for the pipes when pipe axis is at 45 deg. to horizontal plate and circumferential seam is welded without rotating the pipe. It is combination of all positions.
(Refer Fig. 461.1) is the diagram defining the position for groove welds depending on the inclination of the axis of the weld and the angle of rotation of the face of the weld.
There is similar (Refer fig. 461.2) giving position for fillet welds.
(Refer fig. 451.1) gives the thickness limits and the type and number of the test specimen required for procedure qualification of groove and (Refer fig. 463.1) a,b,c,d,e,f shows the method of the taking the test specimen.
In case of weld between dissimilar materials where it is difficult to carry out bending so that weld is at the center of convex position, transverse bends are replaced by longitudinal bends and the fig. look like (Refer fig. 463.1 c)
(Refer fig. 451.3 & 451.4) Give the test required to fillet test and (fig462.4) a,d ( it is similar except that instead of bend there is macro examination of 2 sections of ¼ section.)
(Refer fig. 452.1) gives performance qualification limits and type and number of the test specimen required table (fig) gives the diameter limits. It is worth noting that one, two or more welders can be qualified on just one test coupon. Each may be using even different processes.
(Refer fig. 462.4 B & C) gives the requirements for performance qualification of fillet welds.
(Refer fig. 461.9) gives performance qualification position and diameter limits.
Welding Variables :
Article (IV) gives data about various types of welding variables. It also gives tables for various welding processes showing essential variables, supplementary essential variables and non essential variables for procedures qualification; and essential variables for performance qualification.
Essential variables for procedure are those welding variables whose change will affect the mechanical properties (other than notch-toughness) of the weldment (ex. Change in P-number, filler metal, electrode type, preheat post heat etc.)
Supplementary essential variables for procedure are those welding variables for procedure are those welding variables whose change will after the notch toughness properties of weldment (ex. Uphill or down hill vertical welding, heat input, preheat or PWHT)
Non essential variables for performance are those welding variables which will not affect the mechanical properties of weldment (ex. Joint design, method of back gauging or cleaning etc.)
Essential variables for performance are those welding variables which will affect the ability of welder to deposit sound weld (e.g. position, deletion of backing F-number etc.
Change in process is essential variable for procedure as well as performance.
Before we proceed let us first understand the term P-number A-number and F-number.
All those materials are divided into various P-numbers depending on their nominal composition and further divided into groups depending on their nominal composition and further divided into groups depending on the type of refinement / min. specified UTS etc. QW-422 gives the full details.
Plain carbon steels, C-Si, Cr-Mn & C-Mn-Si are grouped as P-1 materials and austenitic stainless steel as P-8 material. Ferrous welding consumable are classified under various A-numbers based on their weld metal chemical composition (table 442) and all welding electrodes and welding rods are grouped in different F-number depending on their AWS classification which is based on type of flux and chemical composition (table 432)
Now let us have look on some essential variables tables.
QW 253 WPS- SMAW
QW 353 WPQ- SMAW
The following tables are to be referred frequently for working with ASME Section IX and hence one has to understand them (how to) in right context.
Refer ASME Section IX.
- Refer Fig. QW 461.3 – Groove Welds in Test Position
- Refer Fig. QW 461.4 – Fillet welds in Plates Test Positions.
- Refer Fig. QW 461.5 – Fillet Welds in Pipe Test Positions
- Refer fig. QW 462.2 – Method of Taking out the Test Specimen
- (a, b, c, d & e) (Performance Qualification
- Refer fig. QW 463.1 – Method of Taking out the Test Specimen
(a, b, c, d,e & f) Qualification)
7. Refer Table QW 451 – Procedure Qualification Thickness Limits and
Test Specimens.
8. Refer Table QW 452 – Performance Qualification and Test
Specimens.
9. Refer Table QW 461.9 – Performance Qualification Position and
diameter limits.
10. Refer Table QW 461.1 – Test Jig dimensions
Acceptance Criteria Procedure Qualification
- QW 153 Tension Test
- QW 163 Bend Test
- QW 183 Micro Examination Procedure Specimens
- QW 184 Micro Examination Performance Specimens
- QW 191 Radiographic Examination
3. ACCEPTANCE STANDARDS.
Welding Procedure Qualification :
The purpose of procedure qualification testing is to demonstrate that the materials and methods prescribed in a procedure specification will in fact produce weld joint mechanical properties that meet the application and specification requirements.
There are four steps in the qualification of welding procedure :
# Preparation and welding of suitable samples
# Testing of representative specimens
# Evaluation of overall preparation, welding, testing and end results.
# Approval (if the result are favorable)
Preparation of Procedure Qualification Sample joints
Test assemblies usually have a representative joint in the middle. The size, type, and thickness are related to the type and thickness of material to be welded in production and the number, type, and size o specimens to be removed for testing. The materials used as well as the welding details are governed by the particular welding procedure specifications that are to be qualified.
Evaluation of Test Results :
The test results for a procedure qualification sample weld, with the records of joint preparation, welding and testing, should now be made available for review. These results will be analyzed by the responsible parties to determine whether the test details and results meet the requirements of the applicable specifications.
Approval Of Qualification Tests and Procedure Specifications :
As a rule, the inspection agency or customer must approve the procedure qualification tests, the test results, and the procedure specifications before any production welding is done.
Qualification is accomplished when the required tests have been completed and approval has been obtained. However, authentic documentary evidence must be available to show that the joints were indeed satisfactory. As an inspector, you should witness the welding and testing of all specimens, if possible, because you will gain factual knowledge of procedure details that will be helpful in later inspections of production welds.
At any time, an ASME Authorized Inspector can call for re-qualification of a procedure if he is not satisfied with the data presented.
Code Qualification Requirements :
AWS Structural Welding Code, in paragraph 5.5 sets forth the requirements for qualifying those welding procedures which do not meet the prequalified status of paragraph 5.1 of that code, or which must be qualified for other reasons, such as contract requirements. The type and number of specimens that must be tested to qualify a welding procedure are given in paragraph 5.10. The test results required are given in paragraph 5.12.
ASME Boiler and Pressure Vessel Code :
The ASME Boiler and Pressure Vessel Code is authoritative about welding procedures. Section IX is the basic document. It is titled Welding and Brazing Qualifications. All sections of the ASME Code require welding procedures to be qualified “in accordance with Section IX” in addition to supplemental requirements of each specific section.
ASME Section III on Nuclear Components for Power Plants, paragraph NB- 2539.2, states. “The welding procedure … shall be qualified in accordance with NB-4000 and Section IX of this Code”. Paragraph NC-2539.2 refers to NC-4000 and Section IX. Similarly, NG-2539.2 refers to NG-4000 and IX.
ASME Section VIII, Division I, on Pressure Vessels, paragraph UW 28, requires the qualification of welding procedures in accordance with Section IX. Paragraph UB 28 requires brazing procedures to be similarly qualified.
Other procedures in ASME Section III, such as NB-4361 on Specially Designed Seals, are no exception. “Each Manufacturer or Installer shall prepare a procedure specification. The procedure shall be qualified as a new procedure and shall be completely re-qualified when any of the essential variables listed below are changed.” Paragraph NB-4381.2 on the requirements for hard surfacing states. “The procedure shall be qualified as a new procedure and shall be completely re-qualified when any of the changes listed in NB-4382 are made.”
The ASME Code is well summarized in a series of identical paragraphs NB-4321, NC-4321 and so forth-entitled “Procedure Specifications and Qualifications.”
Each manufacturer and/or Installer is responsible for the welding done by his organization and shall establish the procedure and conduct the tests required by this Article and by Section IX of this Code.
Changes in a Qualified Procedure :
If a fabricator who has qualified a welding procedure desires at some later date to make a change in that procedure, it may be necessary to conduct additional qualifying tests. Re-qualification is necessary when any one of the essential variables listed in
the governing standard or code is changed.
For example, one such variable is the heat treatment that follows welding. Heat treatment has a profound effect on most welds. Its omission (when called for) or its addition to a welding procedure when not called for would be a change in an important essential variable, requiring requalification of the procedure.
Note :
The most important factors are usually classed as essential variables; if changed, re-qualification is necessary. Much the same situation exists in connection with welder and welding operator qualifications. The variables that are most frequently
considered essential and generally require re-qualification are shown in the following pages. Remember, reference should always be made to the governing code or specification to determine whether the magnitude of a given change requires re-qualification.
*********
4. WELDING CONSUMABLES
A Brief Introduction :
ASME Section II Part `C’ covers classification and properties of consumables for welding and brazing comprising of Welding Rods, Electrodes and Filler metals. These consumables are grouped into a number of sub-sections, in other words, Specifications, referred to as SFA Number.
Each SFA No. covers consumables of overall similar characteristics, grouped together for compatibility with same group of parent metals. For example, electrodes for carbon steel are grouped in SFA 5.1
Periodical Assessment, Approvals & Certification :
Each SFA specification stipulates requirements for chemical composition limits, manufacturing methods, required tests & test methods, acceptance criteria, classification, marking, packaging, intended use of the consumables, and rules for periodical assessment, approvals and certification
Some Common Specifications
Some of the commonly used SFA Nos. are listed below ; the list is not exhaustive. For a complete list refer to Section II-C.
SFA 5.1 Covered carbon steel arc welding electrodes
SFA 5.4 Covered corrosion resisting chromium and chromium-nickel electrodes
SFA 5.5 Low Alloy steel covered arc welding electrodes
SFA 5.9 Corrosion resisting chromium and chromium nickel steel bare filler wire
SFA 5.17 Carbon steel electrodes and fluxes for submerged arc welding ( SAW )
SFA 5.18 Carbon steel filler metals for gas shielded arc welding (GTAW / GMAW )
SFA 5.20 Carbon steel electrodes for flux-cored arc welding ( FCAW )
SFA 5.23 Low Alloy steel electrodes & fluxes for SAW
SFA 5.28 Low alloy steel filler metals for gas shielded arc welding (GTAW / GMAW )
SFA 5.29 Low Alloy steel electrodes for Flux-cored arc welding ( FCAW )
AWS Classification of Consumables :
American Welding Society has evolved a system of identifying classes of consumables in an alfa-numeric code, which is commonly referred to as AWS class. An explanation of what this classification signifies is given below for typical four common examples:
- Classification of covered Electrodes for SMAW
(Shielded Metal Arc – also known as Manual Metal Arc):
AWS – E – XX – YY – G e.g. AWS E-7018
or, AWS E 8018 B2
E …..Coated electrode
XX….. Minimum tensile strength in ksi
YY……Coating Type & chemistry
G…… Alloy addition, if any
2. Classification of GTAW / GMAW / PAW Bare Wire Rod
AWS – ER – XX -S – YY e.g. AWS ER-70-S-G2
ER….. Bare Rod / electrode
XX….. Minimum tensile strength in ksi
S…….Solid
YY……Specific chemical composition
3. Classification of SAW Wire and Flux for Carbon Steel
AWS – F – XXX – E – YYY
F………….Flux
1st X……Tensile strength in 10,000 psig
2nd X…….Condition of Heattreatment ..
A….as welded
P…. Post heat
3rd X……..Impact strength
E…………..Electrode wire
YYY……….Classification of
carbon steel wire, e.g. EL8, EM12K, or EH14.
4. Classification of SAW Wire & Flux for Alloy Steel
AWS – F – XXX – E C- YYY N- ZM
F………….Flux
1st X……Tensile strength in 10,000 psig
2nd X…….Condition of Heattreatment ..
A….as welded
P…. Post heat
3rd X……..Impact strength
E…………..Electrode wire
C…………..Composite electrode
YYY……….Classification of alloy steel wire
N…………..For special purpose
ZM…………Chemical composition of weld metal
Classification of Parent Materials and Welding
Consumables as per ASME Code Section IX
In developing ASME Section IX, each welding process that was included in the Section, was reviewed with regard to those parameters, called VARIABLES, which have significant effect upon welding operations and fabricator’s ability to qualify Welding Procedures and Welders’ performance. Variables are categorized as Essential, Non-essential and Supplementary (for assurance of notch toughness) variables in the case of low temperature operation.
Essential Variables are given in comprehensive details in the chapter called “Welding Data”. Change in an Essential Variable of an established Welding Procedure requires re-qualification of a Procedure with a new set of Essential Variables. Broadly speaking, and for ease of remembering, following main Essential Variables should be considered in proposing any Welding Procedure Specification :
i. Welding Process, e.g. SMAW, GTAW, SAW etc.
ii. Parent Material , material specifications categorized into P Nos.
iii. Material Thickness
iv. Welding Consumable, categorized into F No. & A No.
v. Maintenance of Preheat, Interpass & Post heat
vi. Post Weld Heat Treatment and finally, the supplementary essential requirement of,
vii. Impact Testing to assure notch toughness properties. Assignment of P Numbers
To rationally reduce the number of Welding Procedure required to be qualified, base materials have assigned P Numbers, essentially based on comparable material characteristics, such as chemical composition, mechanical properties and weldability. (Refer QW-442)
Assignment of F Numbers : Electrodes and welding rods have been grouped into F Numbers ( Refer QW-432), essentially on the basis of their usability characteristics, which fundamentally determine the ability of the Welders to make satisfactory welds, with a given filler metal. This grouping also reduces the number of welding procedures and performances which required to be qualified, where it can be logically done.
Assignment of A Numbers :Weld Metal compositions have been classified and grouped
into A Numbers, essentially on the basis of their weldability characteristics, as reflected by the nominal chemical composition obtained from their actual weld metal analyses.
Cautionary Note
These assignments do not imply that base materials and filler materials be indiscriminately substituted for a base metal or a filler metal which was used in the qualification test, without consideration of compatibility , from the standpoint of metallurgical properties, postweld heat treatment, design, mechanical properties and service requirements.
*********
- GUIDELINES FOR REVIEW OF WPS/PQR .
An inspector has to review the WPS, PQR and WPQ documents to ensure that they meet the ASME sect IX requirements. A checklist shall be used to verify that the WPS is properly completed and is addressing all the requirements of ASME Sect IX and construction code. It is also necessary to verify that PQR has been completed to meet all the ASME sect IX requirements (including test results as per acceptance criteria)
The important part here is also to verify that values of essential variables recorded on the PQR properly support the specified range of WPS
Checklist for Review of WPS (SMAW Process)
Refer QW 250 for variables.
(Supplementary variables not needed)
- See identification block showing WPS no.___________, Rev__________ and PQR no.___________. Also at the end the reviewer shall give his comments. There is signature of the viewer at the end.
- QW 402 gives joint details. QW 403 is indicating Base metals for example if a PQR is having base metal thk. 25.4mm the WPS supported by it can be from 4.8mm to 5.8mm. So if these variables are written in QW 403.8 properly in WPS and PQR column then the column at qualification shall indicate OK which confirms that the variable is within the requirements and addressed properly.
- QW 404 is for filler metals
- QW 405 is for positions.
- QW 406 is for preheat.
- QW 407 is for PWST
- QW 409 is for electrical characteristics.
- QW 410 is for technique.
- Additionally QW 401 says “A change in process is an essential variable.” This has to be verified here and documented.
- QW 202.2, 3,4 are mentioned for reminder to the verifier.
- This is reminder for QW 200.4 combination of processes.
- This is reminder for reviewer for bend and tension test as per QW 451.1
- This is reminder for QW 404.5. The basis for assigning A numbers.
- This is reminder for QW 170- Notch toughness – if required by construction code.
- This is to remind if there are any contracts /company/other
- requirements to be addressed (QW201)
Responses