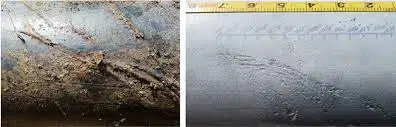
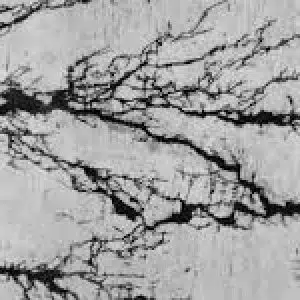
Failure Mechanisms
Welcome to [NDT Inspection Portal]’s failure mechanism group, a place for professionals to connect... View more
Corrosion
-
Corrosion
Corrosion is a major concern in the oil and gas industry, as it can lead to costly damage and failure of equipment. Understanding the different types of corrosion and how they occur is essential for preventing and mitigating their effects.
There are several types of corrosion that can occur in the oil and gas industry, including:
-
General corrosion: This is the most common type of corrosion, and it occurs when a material is exposed to an environment that is chemically aggressive. In the oil and gas industry, general corrosion is often caused by the presence of water, oxygen, and other contaminants.
-
Stress corrosion cracking (SCC): This type of corrosion occurs when a material is subjected to both tensile stress and a corrosive environment. SCC is a common cause of failure in pipelines and other high-stress components.
-
Galvanic corrosion: This type of corrosion occurs when two different metals are in contact with each other in the presence of an electrolyte, such as saltwater. The more noble metal will corrode preferentially, while the less noble metal will be protected.
-
Erosion corrosion: This type of corrosion occurs when a flowing fluid erodes the surface of a material. Erosion corrosion is common in pipelines and other components that are subjected to high fluid flow rates.
Preventing corrosion in the oil and gas industry is essential for ensuring the reliability and safety of equipment. This can be achieved through the use of corrosion-resistant materials, such as stainless steel and other alloys, and by implementing corrosion prevention and control measures, such as coatings and cathodic protection.
Effective corrosion management is also important for optimizing the efficiency and productivity of oil and gas operations. By understanding the types of corrosion that can occur and implementing appropriate prevention and control measures, companies in the oil and gas industry can reduce downtime, extend the lifespan of equipment, and minimize the risk of costly failures.
-
Log in to reply.