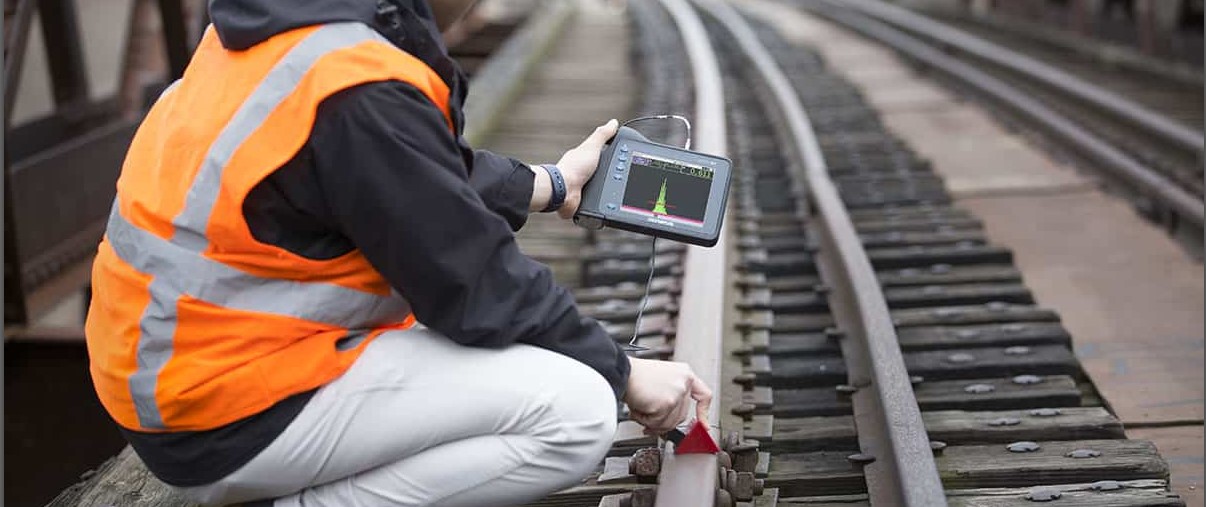
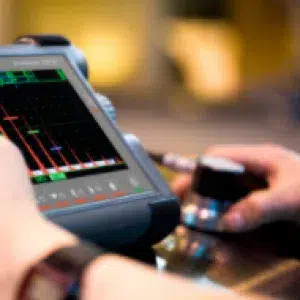
General NDT Group
Welcome to [NDT Inspection Portal]’s general NDT discussion group, a place for professionals in... View more
Magnetic Particle vs Dye Penetrant Testing
-
Magnetic Particle vs Dye Penetrant Testing
Magnetic particle testing and dye penetrant testing are two of the most commonly used non-destructive testing methods for detecting surface and slightly subsurface defects in a wide range of materials. These methods are widely used in industries such as aerospace, automotive, oil and gas, and manufacturing, as they provide a quick and cost-effective way to ensure the integrity and reliability of products and components.
Magnetic particle testing is used to detect defects in ferromagnetic materials, such as steel and cast iron. It works by applying a magnetic field to the test piece and introducing iron oxide or iron oxide-coated magnetic particles to the surface. The magnetic particles are attracted to areas of flux leakage, where there are surface or subsurface discontinuities, such as cracks or laps. The particles can be visible to the naked eye or detected using a black light.
Dye penetrant testing is used to detect defects in non-ferromagnetic materials, such as aluminum, brass, and copper. It involves applying a liquid dye to the surface of the test piece and allowing it to penetrate into any surface-breaking defects. The excess dye is then removed, and a developer is applied, which draws the trapped dye out of the defects and makes them visible.
Both magnetic particle testing and dye penetrant testing are relatively simple, fast, and cost-effective methods for detecting surface defects. They are also relatively non-invasive, as they do not require the removal of material from the test piece. However, they have some limitations. For example, they can only detect defects that are open to the surface, and they may not be effective for detecting defects in certain materials, such as porous materials or materials with rough or uneven surfaces.
In conclusion, magnetic particle testing and dye penetrant testing are important tools for ensuring the quality and reliability of products and components. These methods are widely used in a variety of industries, and they offer a fast and cost-effective way to detect surface defects in a range of materials.
Sorry, there were no replies found.
Log in to reply.