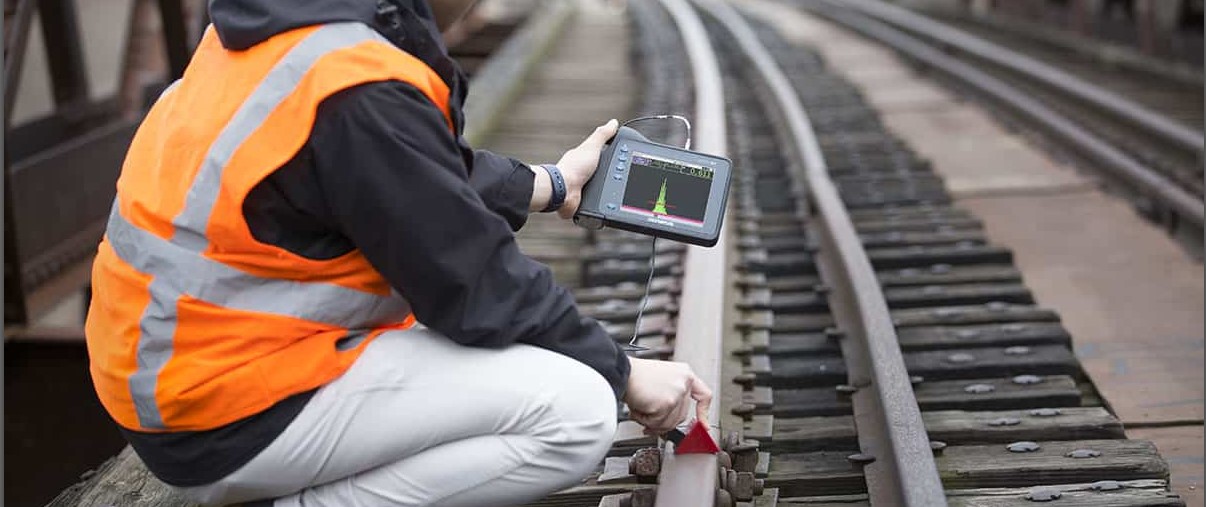
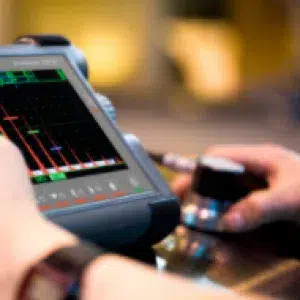
General NDT Group
Welcome to [NDT Inspection Portal]’s general NDT discussion group, a place for professionals in... View more
What is NDT?
-
What is NDT?
This analysis method is applicable to a wide range of industries to detect and assess defects by studying the properties of all types of materials and structures that can cause damage. Eddy current testers such as electromagnetic probes, current fault detectors, ECT, conductivity meters and other accessories are used to perform various types of electromagnetic inspections such as surface scanning, underground inspection, weld seam inspection, fastening hole inspection, pipe inspection, heat treatment inspection and metal sorting.
Non-invasive inspection techniques can be used to assess material properties of components or complete processes and to detect, characterise and measure the presence of damage mechanisms.
NDT (non-destructive inspection), also known as array inspection, is a method that allows inspectors to evaluate and collect information on a material or system component without changing it. It refers to a set of techniques that allow inspectors to collect data without damaging a material.NDT is sometimes referred to as non-destructive testing (NDE), non-destructive assessment (NDE) or non-destructive inspection (NDI).
Non-destructive testing (NDT) consists of a variety of non-invasive testing techniques that assess material properties of a component or of an entire process unit. Non-destructive testing (NDT) is often used as a generic term for all non-destructive inspection methods and inspection tools in the entire area of non-destructive inspection.NDT is the process of inspecting and testing a material, component or assembly for discontinuities, differences or properties without destroying the usability of any part of the system.
Different types of ultrasonic testing methods are used to identify different defects and cavities for material deterioration.Other techniques include acoustic emission testing (AE), guided wave testing (GW), laser testing (LM), acoustic resonance testing (ART), leak testing (LT), magnetic flux leakage (MFL), vibration analysis (VA) and near-infrared (IR) testing.
For example, ultrasonic testing consists of the propagation of ultrasonic waves through a material while magnetic particle testing uses small particles that are influenced by the application of magnetic fields.These can be two forms of ultrasonic testing – for example straight beam ultrasonic testing (UT) is a conventional technique for simple applications, while the phase array ultrasonic testing ( PAUTs) is advanced straight beam ultrasonic testing (UTS ).
In the Cowley Nondestructive Test Program, students develop knowledge and skills needed to carry out the demanding testing techniques required in many industries and areas, such as eddy current blowing, liquid dyes, penetrating magnetic particles and ultrasonic testing.Tests are carried out to assess materials, components, constructions, structures and mechanical components. The basis of inspection technology depends on the ability of technicians to understand physics principles and apply basic mathematical calculations to find material defects.
Welding is tested with NDT techniques such as industrial radiography and industrial computed tomography by X-ray, Gamma, Ultrasound, fluid testing, magnetic particle inspection and eddy current. X-ray and CT scans are used for industrial radiography to see detailed images of the test material.
Magnetic particle tests can be used to detect near-surface defects in ferromagnetic materials. Holographic tests use lasers to detect changes in the surface of a material exposed to stresses such as heat, pressure and vibration.
In this method, an electric current or magnetic field is used to pass through conductive parts. This method limits the use of dielectric materials and uses microwave frequencies to transmit and receive the test probe.
In this technique, a sound beam is inserted into the surface of the test materials. This technique, also known as tensile or destructive testing, uses a controlled stress applied to a sample material to see how it reacts.The electrical conductivity and magnetic conductivity of the material are affected by vortices and currents, and this test method uses a type of material based on these properties.
Leakage testing detects leaks and locates them using a variety of techniques including electronic monitoring devices, pressure gauge measurements, liquid and gas penetration techniques, and simple soap bubble testing.
Typical examples of NDT technicians and engineers conducting tests to identify and identify deficiencies and discontinuities are airplanes, cars, reactors, trains, pipelines, bridges, power plants, oil platforms, and buildings where the material or structure could be catastrophic.An essential feature of the NDT method is that it has no negative effects on the materials or structures to be tested. The devices and testing devices used to perform most Ndt methods are compact and portable.
Non-destructive testing (NDT) uses a wide variety of testing methods to ensure materials and structures perform their functions at cost. NDT uses various principles from scientific fields such as physics, chemistry and mathematics to test components. Ultrasonic tests are used for fault detection and evaluation, measurement, material characterization and more.Non-destructive testing (NDT) is a combination of different inspection techniques that evaluate the integrity and properties of a material, component or system without damaging the component or system. In other words, each part needs the use of one or more of these techniques used in the inspection process.
Similarly, NDT methods have different levels of success depending on the type of material on which they are used and some techniques such as the magnetic particle NDT work best on certain materials that are magnetized.Non-destructive testing (NDT) is an efficient method of inspecting equipment without having to shut down or set into operation to increase availability and productivity.
NDT is also known as non-destructive testing ( NDE) or non-destructive inspection (NDI) depending on the industry. Also known as liquid penetrant inspection (LPT), the traditional method used for NDT in field laboratories is penetration testing (PT ) in which non-ferrous materials such as metals, composites and ceramics are used to identify surface anomalies such as cracks, seams, laminations, blow holes, defects, external breakouts and welding defects.
Conventional ultrasonic testing (UT) uses NDT techniques to measure the propagation of mechanical vibrations (ultrasonic waves) on a material to investigate properties, measure thickness, determine elasticity and detect a range of discontinuities including corrosion, erosion, defects, cracks and more.
Log in to reply.