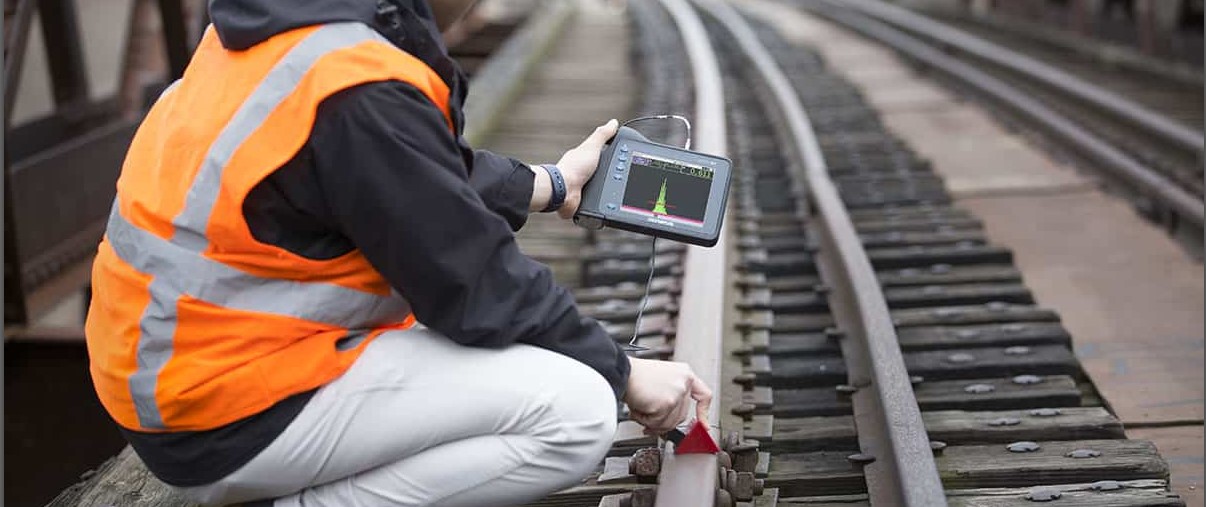
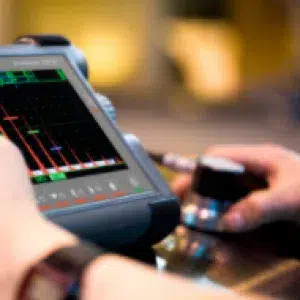
General NDT Group
Welcome to [NDT Inspection Portal]’s general NDT discussion group, a place for professionals in... View more
What Is Nondestructive Testing
-
What Is Nondestructive Testing
What Is Nondestructive Testing?
Nondestructive testing (NDT) is the process of inspecting, testing, or evaluating materials, components or assemblies for discontinuities, or differences in characteristics without destroying the serviceability of the part or system. In other words, when the inspection or test is completed the part can still be used.
In contrast to NDT, other tests are destructive in nature and are therefore done on a limited number of samples (“lot sampling”), rather than on the materials, components or assemblies actually being put into service.
These destructive tests are often used to determine the physical properties of materials such as impact resistance, ductility, yield and ultimate tensile strength, fracture toughness and fatigue strength, but discontinuities and differences in material characteristics are more effectively found by NDT.
Today modern nondestructive tests are used in manufacturing, fabrication and in-service inspections to ensure product integrity and reliability, to control manufacturing processes, lower production costs and to maintain a uniform quality level. During construction, NDT is used to ensure the quality of materials and joining processes during the fabrication and erection phases, and in-service NDT inspections are used to ensure that the products in use continue to have the integrity necessary to ensure their usefulness and the safety of the public.
It should be noted that while the medical field uses many of the same processes, the term “nondestructive testing” is generally not used to describe medical applications.
https://www.asnt.org/MajorSiteSections/About/Introduction_to_Nondestructive_Testing.aspx
Log in to reply.