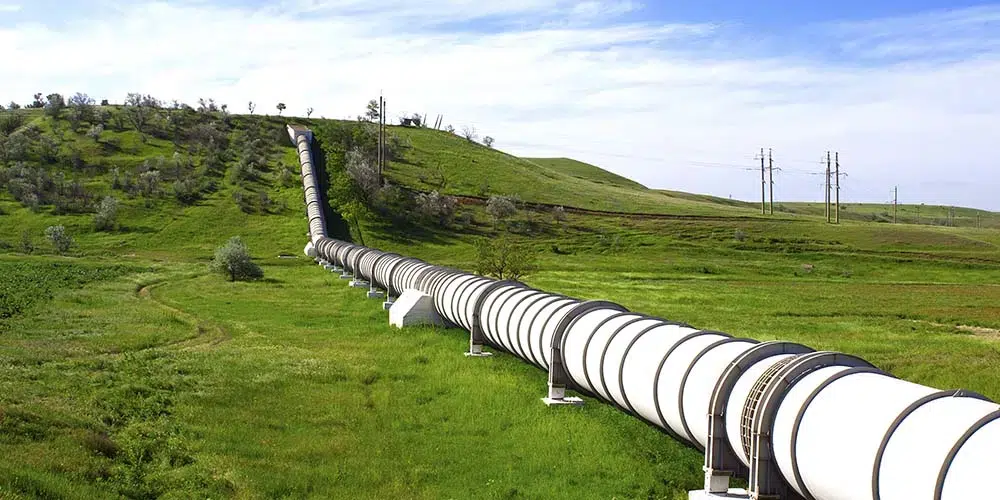
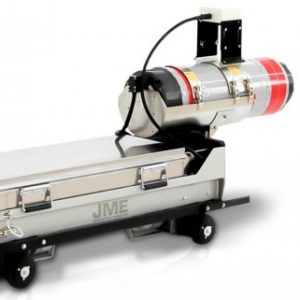
Pipeline X-Ray Inspection
Public Pipeline
Active 4 months ago
Welcome to [NDT Inspection Portal]’s pipeline X-ray inspection group, a place for professionals to... View more
Public Pipeline
Group Description
Welcome to [NDT Inspection Portal]’s pipeline X-ray inspection group, a place for professionals to connect and discuss the latest techniques and technologies in pipeline X-ray inspection.
Pipeline X-ray inspection is a specialized technique used to evaluate the condition and performance of pipelines using X-ray technology. It is an important aspect of ensuring the integrity and reliability of pipelines in various industries, including oil and gas, water and wastewater, and transportation.
Pipeline X-ray inspection involves the use of specialized X-ray equipment and techniques to produce detailed images of the internal structure of pipelines. These images can be used to identify any potential issues or defects, such as cracks, corrosion, or weld defects, and to evaluate the condition of the pipeline. Pipeline X-ray inspection is often used in conjunction with other non-destructive testing (NDT) methods, such as ultrasonic testing and magnetic particle inspection, to provide a comprehensive evaluation of the pipeline.
Our member group offers a platform for sharing knowledge and best practices on pipeline X-ray inspection and its applications in various industries. Join our community of experts from around the world and be a part of the conversation on advancing the practice of pipeline X-ray inspection and its applications in the field of NDT and inspection. Whether you are new to pipeline X-ray inspection or an experienced professional, you’ll find valuable resources and a welcoming community in our group.
Reply To: AUT for mainline pipe inspection
-
It depends on the diameter and the wall thickness of the pipeline. You have to consider the time for the band/scanner positioning. Then the scanning time and the interpretation time. For most of the commonly used AUT systems, the scanning speed is in the range 30 to 80 mm/sec. Based on that, you can try to calculate the scanning time for your scope of work. On top of that, you have to consider the time for the calibrations (depending on the specification/procedure, it can be every weld or every 5 welds or every 10 welds, etc.). Interpretation time is a “random” variable. A clean strip chart requires relatively “no time” to be assessed. “Dirty” welds will require much more time.
The crew depends again on the diameter of the pipeline. If it is a large OD pipe for that type of production rate, I would say that you need at least 2 AUT operator (or 1 operator and 1 supervisor) and probably 3x scanner technicians (2 working on the “scanned” weld and the third one that can clean the following weld/cooling it if needed/setup the band/etc). 100 welds on a 10 hours shift means one weld every 6 min. It looks to me a really challenging target for one spread (for both welding and AUT). However, AUT would be faster than RT done with crawlers.
A complete backup for the AUT system on site I would say that is “mandatory”.