Aerospace Maintenance and Inspection: The Importance of NDT
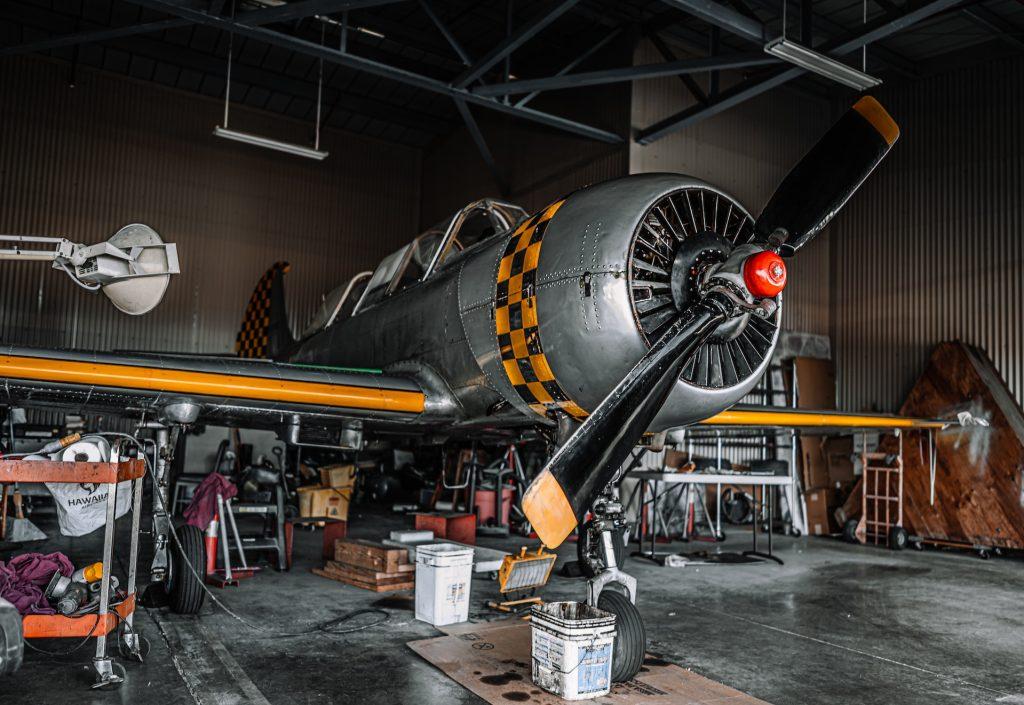
The aerospace industry is one of the most technologically advanced industries in the world. With the constant advancement of technology, it is essential that maintenance and inspection procedures keep pace to ensure the safety and reliability of aircraft. One of the most crucial aspects of aerospace maintenance and inspection is non-destructive testing (NDT).
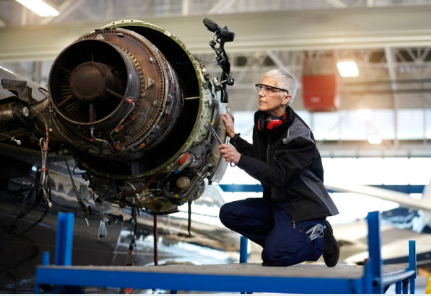
NDT is a method of evaluating the properties of a material, component, or system without causing damage. It is used to detect and evaluate internal and surface defects, as well as measure the thickness of materials. NDT is an important tool for the aerospace industry because it allows for the detection of potential issues before they become major problems. This helps to ensure the safety of aircraft and the passengers and crew on board.
There are several different types of NDT that are commonly used in the aerospace industry. These include:
- Ultrasonic testing (UT): This method uses high-frequency sound waves to detect internal defects in materials. It is commonly used to inspect metal parts, such as aircraft fuselages, wings, and engines.
- Radiographic testing (RT): This method uses X-rays or gamma rays to create an image of the internal structure of a material or component. It is commonly used to inspect welds and other joints in aircraft structures.
- Magnetic particle testing (MT): This method uses a magnetic field to detect surface defects in ferromagnetic materials, such as steel. It is commonly used to inspect the surfaces of aircraft engines and other components.
- Eddy current testing (ET): This method uses an alternating current to create a magnetic field that induces eddy currents in a material. These currents can then be used to detect defects in the material. It is commonly used to inspect the surface of aluminum and other non-ferromagnetic materials.
- Visual testing (VT): This method uses visual inspection to detect defects in materials and components. It is commonly used to inspect the surfaces of aircraft structures, such as the fuselage and wings.
Most commonly inspected components on an aircraft
A variety of components on an aircraft are inspected to ensure their safety and proper functioning. Some of the most commonly inspected components on an aircraft include:
- Wings: The wings of an aircraft are inspected for structural integrity, damage, and signs of wear or fatigue. This is important because the wings bear the majority of the load during flight and must be able to withstand the stresses of flight.
- Fuselage: The fuselage of an aircraft is inspected for structural integrity, damage, and signs of wear or fatigue. The fuselage is responsible for protecting the passengers and crew, as well as housing the aircraft’s systems and equipment.
- Engines: The engines of an aircraft are inspected for proper operation, wear and tear, and signs of damage. Engines are critical for propulsion and must be in good working condition to ensure the safety of the aircraft.
- Landing gear: The landing gear of an aircraft is inspected for proper operation, wear and tear, and signs of damage. The landing gear is responsible for supporting the aircraft on the ground and must be in good working condition for safe take-off and landing.
- Flight control surfaces: The flight control surfaces of an aircraft, such as the elevators, ailerons, and rudder, are inspected for proper operation and signs of wear or damage. These surfaces are critical for controlling the aircraft’s flight and must be in good working condition to ensure the safety of the aircraft.
- Electrical systems: The electrical systems of an aircraft, such as the wiring, batteries, and generators, are inspected for proper operation and signs of wear or damage. Electrical systems are critical for powering the aircraft’s systems and must be in good working condition to ensure the safety of the aircraft.
- Avionics: The avionics systems of an aircraft, such as the navigation, communication, and flight control systems, are inspected for proper operation and signs of wear or damage. These systems are critical for the safe operation of the aircraft and must be in good working condition to ensure the safety of the aircraft.
- Safety Equipment: Safety equipment such as emergency slides, oxygen system, emergency lighting, fire extinguisher and emergency exits are also inspected for proper operation and signs of wear or damage.
These are just a few examples of the many components that are inspected on an aircraft. The reason for inspection is to ensure that all the parts of the aircraft are in good working condition and to detect and fix any issues that may arise in order to ensure the safety of the aircraft and the passengers and crew on board.
NDT in aircraft inspection
NDT is an essential tool for ensuring the safety and reliability of aircraft. It allows for the detection of potential issues before they become major problems, which helps to keep aircraft in safe operating condition. The aerospace industry has a strict set of guidelines for NDT, and all NDT inspections must be conducted by qualified and certified personnel. NDT is a cost-effective method of ensuring the safety of aircraft and the passengers and crew on board.
In conclusion, NDT is a vital tool for maintaining and inspecting aerospace components and systems. It allows for the detection of potential issues before they become major problems, which helps to ensure the safety and reliability of aircraft. As technology continues to advance, it will be essential that aerospace maintenance and inspection procedures keep pace. The use of NDT will continue to be an important aspect of the aerospace industry, and it will continue to play a crucial role in ensuring the safety of aircraft and the passengers and crew on board.
Responses