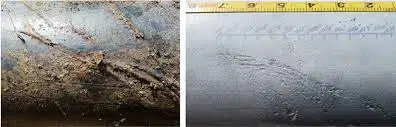
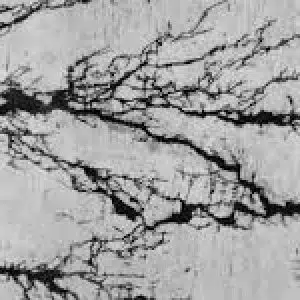
Failure Mechanisms
Welcome to [NDT Inspection Portal]’s failure mechanism group, a place for professionals to connect... View more
Chloride Stress Corrosion Cracking
-
Chloride Stress Corrosion Cracking
The combination of tensile stress and a specific corrosive environment can crack stainless steels. This mode of attack is termed stress corrosion cracking (SCC). The most common environmental exposure condition responsible for SCC of stainless steels is the presence of chlorides. Although no stainless steel grade is totally immune to chloride SCC, the relative resistance of stainless steels varies substantially.
Influence of Alloy Composition
The relative resistance to chloride SCC is dependant on the stainless steel family. The austenitic family of stainless steels is the most susceptible. The resistance of austenitic stainless steels to SCC is related to the nickel content of the steel.
The most susceptible austenitic grades have nickel contents in the range of 8 to 10 wt%. Therefore, standard grades such as 304/304L and 316/316L are very susceptible to this mode of attack. Austenitic grades with relatively high nickel and molybdenum contents such as alloy 20, 904L, and the 6% molybdenum super austenitic grades have substantially better chloride SCC resistance.
The ferritic family of stainless steels, which includes grades such as type 430 and 444 is very resistant to chloride SCC. The duplex stainless steel with their dual austenite/ferrite microstructures has a resistance that is in between that of the austenite and ferrite grades.
Corrosion Testing
The relative resistance of a stainless steel to chloride SCC is often quantified by the use of standard boiling salt solutions. The table attached summarizes the results of testing in boiling salt solutions of 26% NaCl (sodium chloride), 33% LiCl (lithium chloride), and 42% MgCl2 (magnesium chloride). The boiling LiCl and MgCl2 test solutions are very aggressive relative to practical applications and only austenitic alloys with compositions that approach those of nickel-base alloys will routinely resist cracking in these test solutions.
Crack Appearance
The typical crack morphology for chloride stress corrosion cracking consists of branched transgranular cracks. Figure 1 shows the cracking that occurred on a 6Mo super austenitic stainless steel (N08367) exposed to 0.2% chlorides at 500 °F (260 °C).
Environmental Factors
The environmental factors that increase the cracking susceptibility include higher temperatures, increased chloride content, lower pH, and higher levels of tensile stress. Temperature is an important variable. When stainless steels are fully immersed, it is rare to see chloride stress corrosion cracking at temperatures below 60 °C (150 °F).
There is a synergistic relationship between dissolved oxygen and the chloride level. If the oxygen level is reduced to the 0.01 to 0.1 ppm range, aqueous solutions containing low to moderate chloride levels are not likely to crack austenitic alloys, such as 304L and 316L. The normal solubility of O2 in water at room to moderate temperatures (e.g. up to 140°F/60°C) is 4.5 to 8 ppm at atmospheric pressure.
In actual service environments, evaporation can produce a local build-up of aggressive corrosive substances, such as chlorides and the H+ ions, resulting in conditions that are substantially more aggressive. Under severe evaporative conditions, stainless steels can crack at temperatures well below the thresholds measured under conditions where there is full immersion. Because of this, one must use caution when specifying materials for applications that involve the evaporation of chloride-bearing solutions on hot stainless steel surfaces.
The Materials Technology Institute (MTI) of the Chemical Process Industry has reviewed the literature and collected case histories to define guidelines for the chloride SCC susceptibility of types 304L and 316L stainless steel in neutral water environments.
Figure 2 shows the cracking threshold for 304L and 316L stainless steel as a function of temperature and chloride content. The level of chlorides required to produce cracking is relatively low. Failures have been reported in environments with as little as 10 ppm chlorides. This is particularly true for environments having concentrating (evaporating) mechanisms such as wet/dry interfaces or a film of solution in immediate contact with a heat-rejecting surface. In these situations, a few ppm of chlorides in the bulk solution can concentrate to hundreds of ppm in the area of evaporation.
Sorry, there were no replies found.
Log in to reply.