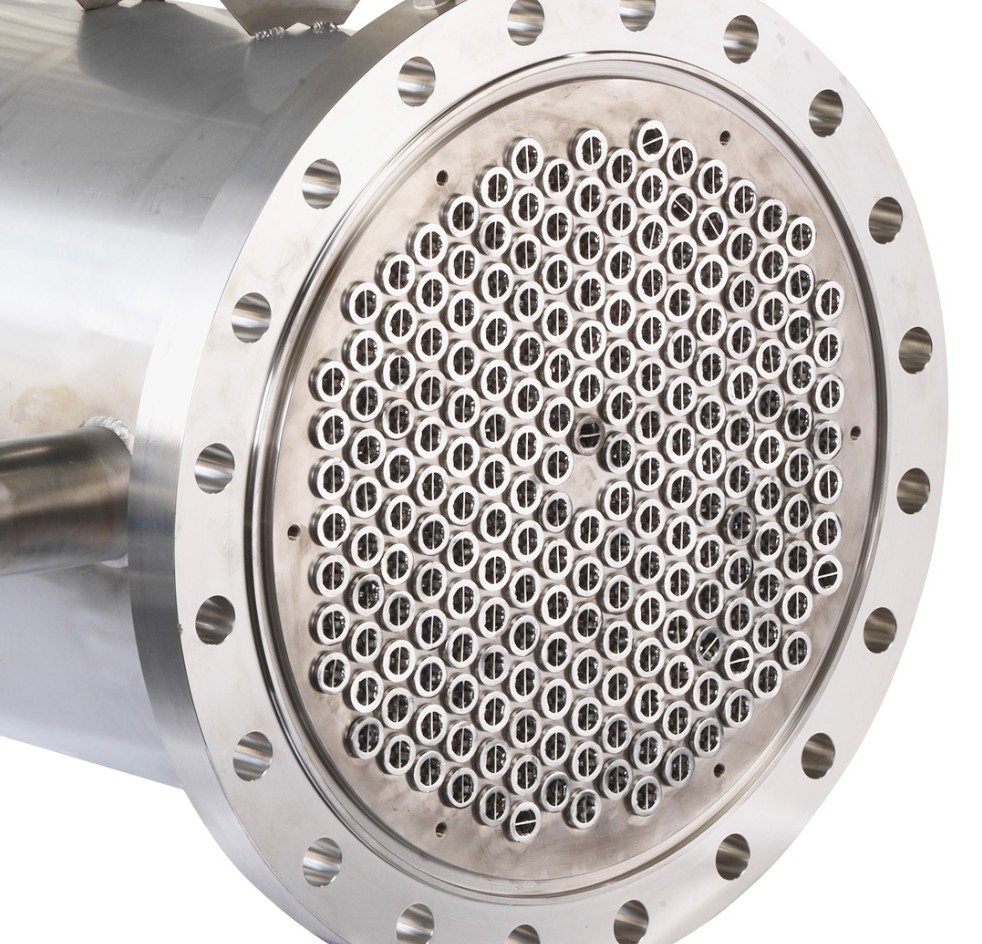
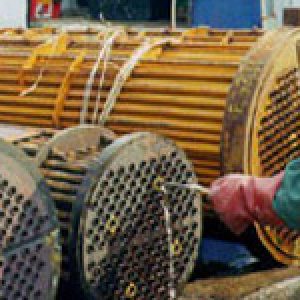
Internal Rotary Inspection (IRIS)
Welcome to [NDT Inspection Portal]’s internal rotary inspection (IRIS) group, a place for professionals... View more
Internal Rotating Inspection System (IRIS)
-
Internal Rotating Inspection System (IRIS)
Internal Rotating Inspection System (IRIS)
Internal Rotating Inspection System (IRIS) is an effective nondestructive examination technique used to detect and size corrosion in pipes and tubing. The method first began development in the 1970s and saw its first field use in 1978. IRIS works by inserting and pulling a probe through a piece of equipment where it directs an ultrasonic beam towards the internal tube wall. By measuring these sound waves, the probe can detect things like internal and external erosion, corrosion, pitting, denting, and fretting. It can also detect bulges, restrictions, remaining wall thickness, channeling, and tube sheet defects.
IRIS is used to inspect many different types of process equipment, including feed water heaters, air fin coolers, condensers, boilers, heat exchangers, process piping, loading lines, and product flow lines. The method is able to detect flaws on both the inside and outside of tube walls.
Compared to other methods of NDE, IRIS is fairly complex. It requires extensive cleaning before an inspection can begin. If a tube isn’t fully cleaned it is possible that the probe might jam, causing unexpected delays. The probe must be moved slowly to obtain the best results, so it is not as quick as other methods. Moreover, IRIS can be rather expensive because it requires highly trained and experienced technicians to obtain proper results.
Sorry, there were no replies found.
Log in to reply.