
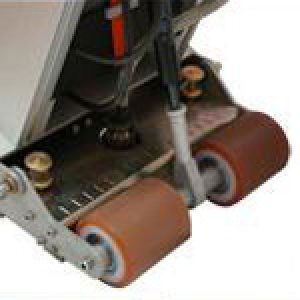
Magnetic Flux Leakage (MFL)
Welcome to [NDT Inspection Portal]’s magnetic flux leakage (MFL) group, a place for professionals... View more
MFL principle
-
MFL principle
MFL principle
As a MFL tool navigates the pipeline a magnetic circuit is created between the pipewall and the tool. Brushes typically act as a transmitter of magnetic flux from the tool into the pipewall, and as the magnets are oriented in opposing directions, a flow of flux is created in an elliptical pattern. High Field MFL tools saturate the pipewall with magnetic flux until the pipewall can no longer hold any more flux. The remaining flux leaks out of the pipewall and strategically placed tri-axial Hall effect sensor heads can accurately measure the three-dimensional vector of the leakage field.
Given the fact that magnetic flux leakage is a vector quantity and that a hall sensor can only measure in one direction, three sensors must be oriented within a sensor head to accurately measure the axial, radial and circumferential components of an MFL signal. The axial component of the vector signal is measured by a sensor mounted orthogonal to the axis of the pipe, and the radial sensor is mounted to measure the strength of the flux that leaks out of the pipe. The circumferential component of the vector signal can be measured by mounting a sensor perpendicular to this field. Earlier MFL tools recorded only the axial component but high-resolution tools typically measure all three components. To determine if metal loss is occurring on the internal or external surface of a pipe, a separate eddy current sensor is utilized to indicate wall surface location of the anomaly. The unit of measure when sensing an MFL signal is the gauss or the tesla and generally speaking, the larger the change in the detected magnetic field, the larger the anomaly.
Sorry, there were no replies found.
Log in to reply.