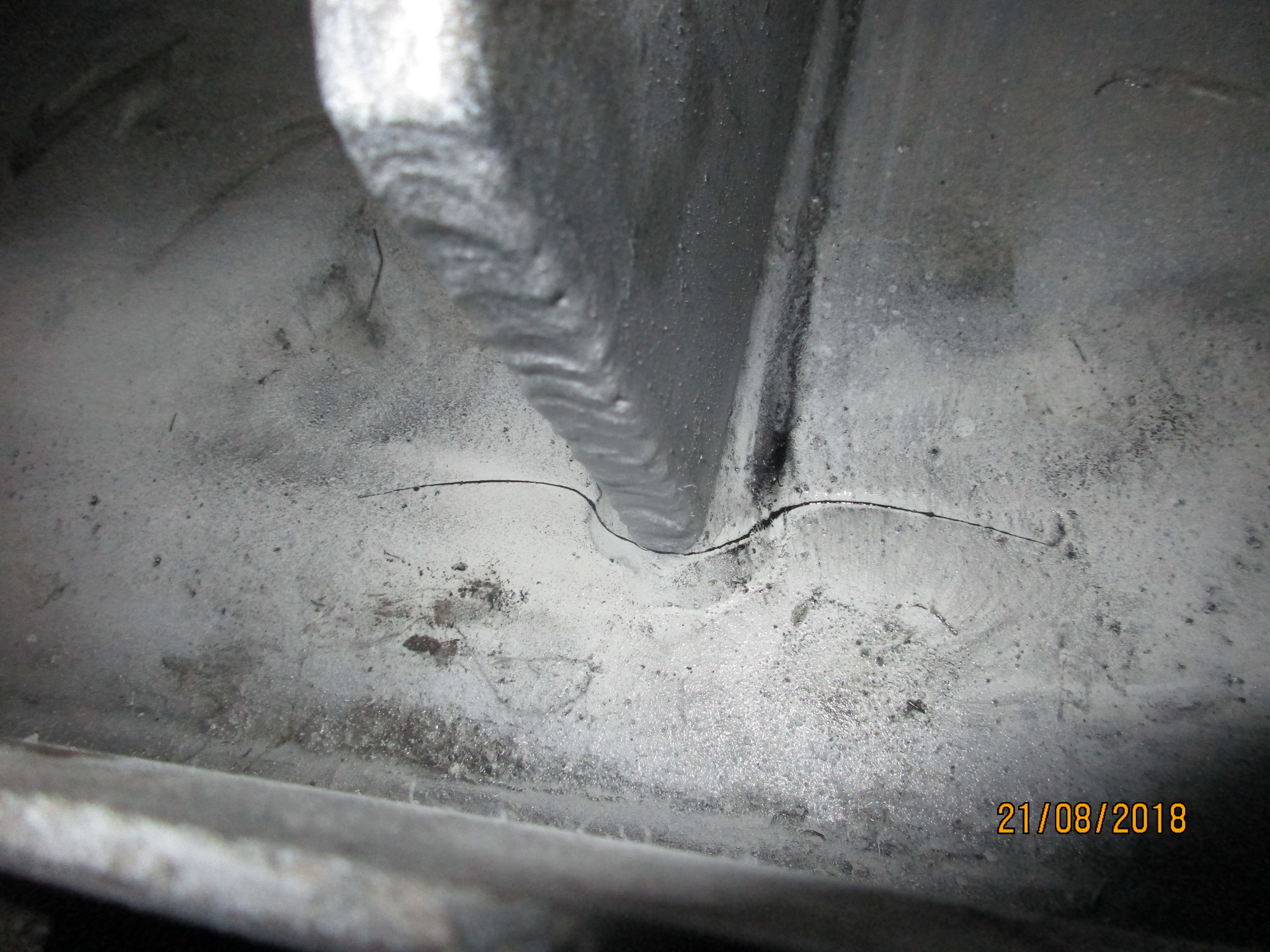
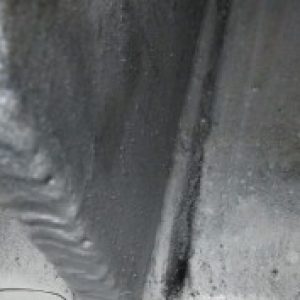
Magnetic Particle Inspection (MPI) (MT)
Welcome to [NDT Inspection Portal]’s Magnetic Particle Inspection (MPI) group, a place for... View more
Choose the Most Reliable MPI Method
-
Choose the Most Reliable MPI Method
Magnetic particle inspection methods vary in terms of ease of use as well as the level of detail.
Magnetic particle inspection (MPI) can be performed a number of different ways and oftentimes any of these methods are acceptable under the specification called out for performing the test. In many cases, these specifications leave the door open for the nondestructive testing personnel to select the method for performing the inspection. But, be aware that all methods are not created equal. As explained below, they not only vary in terms of ease and time to perform, but also in the level of detail provided in the test results.
Since safety and reliability are priorities for anyone in a position responsible for quality, when given an option, it makes sense to choose the MPI method for your finished products that will provide the most dependable results. When purchasing inspected material, you may want to dig a little deeper to find out how the material was certified:
- Type of electrical current used to create the magnetic field in the test piece
- Type of medium or particles used to perform the testing
For this article, three different magnetic particle inspection methods were performed on the same test piece for comparison. Any of the three would be acceptable for meeting the requirements of many base specifications. The following techniques were utilized:
- Visible dry powder with an alternating current (AC) yoke
- Visible dry powder using full wave direct current (FWDC) in a horizontal bench unit
- Fluorescent wet by full wave direct current (FWDC) in a horizontal bench unit
Due to the loose powder used in the visible dry method, we know that this process is more labor intensive, messier and takes longer to perform than the fluorescent wet technique. Of more importance, visible dry MPI is also less sensitive than fluorescent magnetic particle inspection. The comparison of our three MPI methods and their results are reviewed below to make this point.
By choosing these different test methods, we are able to compare the impact of each of the following on the level of detail in the test results:
- Current: AC versus full wave DC
- Medium/Particles—visible dry powder and fluorescent wet suspension
The examples below were taken from an actual order processed in our lab. We were instructed to inspect the same part using the two different visible dry powder magnetic particle techniques mentioned above. Although orders for visible dry powder are common, performing basically the same inspection on the same test piece with two different visible dry processes was not typical. After being surprised by the results, we decided to complete our comparison by inspecting the same part using the fluorescent wet continuous technique with the FWDC bench unit.
Visible Dry Powder with an Alternating Current (AC) Yoke
The initial inspection results using the visible dry powder with the AC Yoke revealed only what would be termed as gross surface defects (forging laps) in an as-forged area of the test piece. These defects were in fact severe enough to be seen by visual inspection with the naked eye. We observed no magnetic particle indications in the machined areas of the part.
Visible Dry Powder using Full Wave Direct Current (FWDC) in a horizontal bench unit
The next inspection was performed with visible dry powder and a direct contact head shot followed by a coil shot using FWDC in our horizontal bench unit. This particular test is not often performed, so our first concern was to protect the fluorescent bath and as much of the bench unit as possible from contamination by the visible particles.
In all honesty, we didn’t expect to see much difference in the results from the previous visible dry powder inspection using the AC yoke. We were confident that the gross defects (forging laps) previously observed would be detected again. Other than the as-forged areas, the part appeared to be of very high quality in the machined areas. What we didn’t expect to find—which is part of the fun of NDT—were the multiple linear indications believed to be inclusions or stringers throughout the machined areas of this test piece. These indications were not found using the visible dry powder with the AC yoke and could potentially be detrimental to the part, depending on its application.
We concluded that the more detailed results were due to the different current used in our bench unit, since DC current is deeper penetrating than AC. While AC current can successfully detect surface discontinuities, DC current can locate deeper and more hidden defects such as these stringers and inclusions.
Fluorescent Wet by Full Wave Direct Current (FWDC) in a Horizontal Bench Unit
The final inspection of our study was performed using the fluorescent wet continuous method in the FWDC bench unit. As expected, the gross defect in the forged area was easily found again. Also as expected, the multiple linear indications believed to be inclusions/stringers in the machined areas were even more pronounced and much more populous than observed by the previous visible dry powder inspection.
Since all other factors were the same for the two tests performed in the bench unit, we attribute the more defined results of the fluorescent wet inspection to the medium used and the lighting in the inspection area. While both visible dry and fluorescent wet inspections are performed by covering the test surface in fine iron oxide particles while applying a magnetic field, the application and inspection processes differ. The visible dry powder is applied and removed by hand, which leaves room for human error, and the results are observed under a standard white light. The fluorescent method allows for the use of smaller particles transported in a liquid bath for better flow to small leakage fields, and these test samples are evaluated in a darkened inspection area under a black light where the fluorescent colors provide better visibility of indications.
In conclusion, when the MPI test method is not specified, opt for the fluorescent wet method over visible dry inspection. This will help ensure that you are getting the most reliable test results and information about your materials and finished products. If visible dry is required, the use of the HWDC unit is definitely the best option to ensure accurate results.
Sorry, there were no replies found.
Log in to reply.