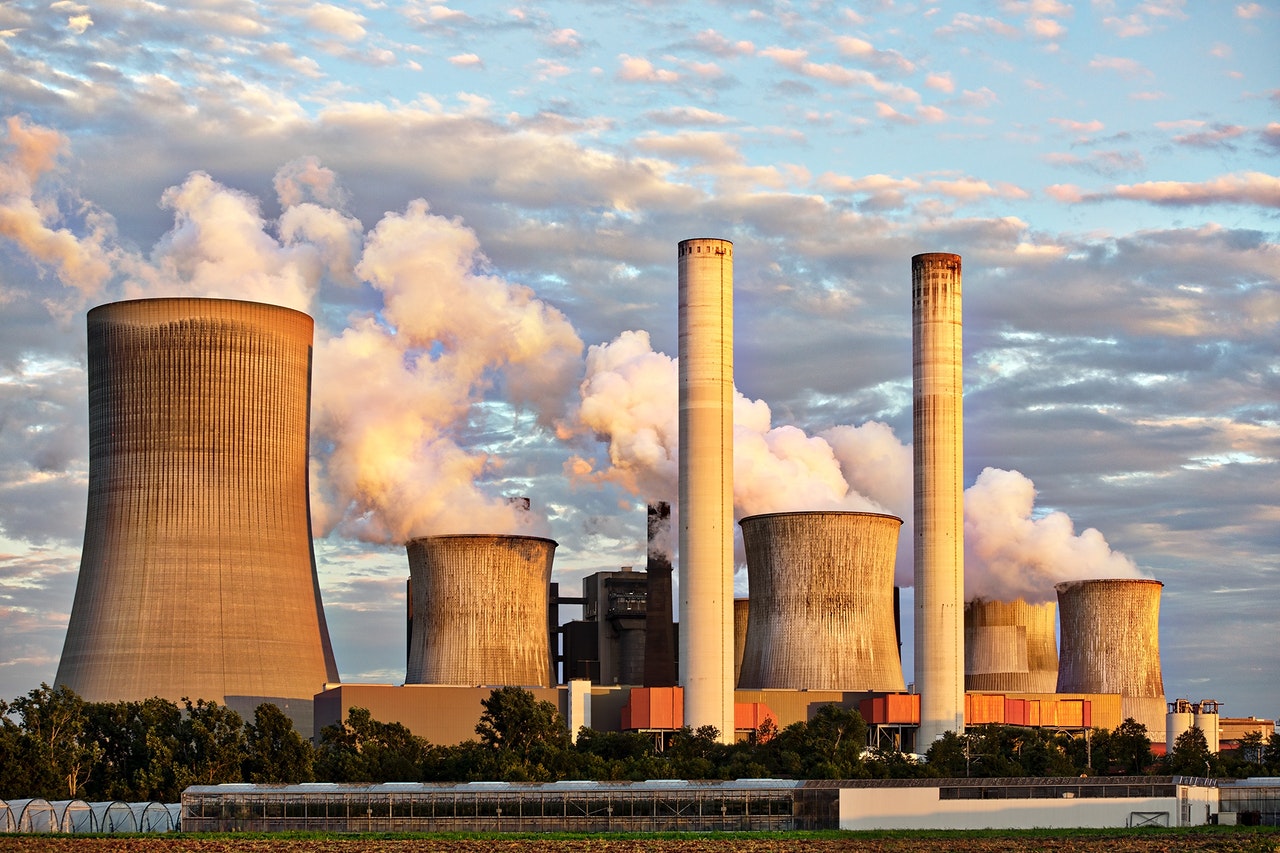
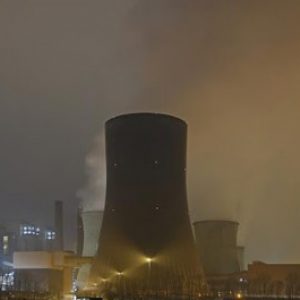
Nuclear Sector
Public Sectors
Active a year ago
Nuclear
Public Sectors
Future NDT work in Nuclear Sector
-
Future NDT work in Nuclear Sector
Posted by imtiaz-alam-bd on 29/07/2023 at 11:51 amWhat kind of NDT work is done in this sector after commissioning?
NDT-Inspect replied 2 years ago 2 Members · 1 Reply -
1 Reply
-
In-service inspections (ISI) in the nuclear sector are crucial for maintaining the safety, integrity, and efficiency of the facility. During ISI, various equipment and components are tested to ensure they are functioning correctly and to identify any signs of wear, degradation, or damage. Here’s a detailed look at the equipment that is typically tested during in-service inspections and the reasons why:
-
Reactor Pressure Vessels (RPVs):
- Why: To detect cracks, corrosion, or other defects that could lead to failure under pressure.
- Methods: Ultrasonic Testing (UT), Radiographic Testing (RT), Magnetic Particle Inspection (MPI).
-
Steam Generators and Heat Exchangers:
- Why: To identify tube wear, cracking, or corrosion that could affect heat transfer efficiency.
- Methods: Eddy Current Testing (ECT), Visual Inspection (VI).
-
Piping Systems and Valves:
- Why: To detect leaks, corrosion, erosion, or mechanical damage that could lead to loss of containment.
- Methods: Ultrasonic Testing (UT), Acoustic Emission Testing (AET), Leak Testing.
-
Turbines and Generators:
- Why: To assess wear, misalignment, vibration, or other mechanical issues that could reduce efficiency or lead to failure.
- Methods: Vibration Analysis, Visual Inspection (VI), Thermographic Inspection.
-
Cooling Towers and Condensers:
- Why: To identify scaling, fouling, or corrosion that could affect cooling efficiency.
- Methods: Visual Inspection (VI), Eddy Current Testing (ECT).
-
Containment Structures:
- Why: To ensure structural integrity and the ability to contain radioactive materials in the event of an accident.
- Methods: Visual Inspection (VI), Ultrasonic Testing (UT), Radiographic Testing (RT).
-
Fuel Assemblies and Control Rods:
- Why: To assess physical condition, alignment, and potential defects that could affect reactor control.
- Methods: Visual Inspection (VI), Gamma Scanning.
-
Electrical Systems and Switchgear:
- Why: To detect overheating, insulation breakdown, or other electrical faults that could lead to failure or fire.
- Methods: Thermographic Inspection, Electrical Testing.
-
Emergency Systems and Safety Equipment:
- Why: To ensure readiness and proper functioning in the event of an emergency.
- Methods: Functional Testing, Visual Inspection (VI).
-
Waste Storage and Handling Equipment:
- Why: To prevent leaks, spills, or other failures that could lead to environmental contamination.
- Methods: Leak Testing, Visual Inspection (VI).
- Environmental Monitoring Equipment:
- Why: To ensure accurate monitoring of radiation levels, air quality, and other environmental factors.
- Methods: Calibration and Functional Testing.
- Cranes and Lifting Equipment:
- Why: To prevent mechanical failure during the handling of heavy or hazardous materials.
- Methods: Load Testing, Visual Inspection (VI).
In conclusion, in-service inspections in the nuclear sector encompass a wide range of equipment and components, each with specific functions and potential failure modes. Regular testing and monitoring through various NDT methods enable early detection of issues, compliance with regulatory standards, and assurance of safe and efficient operation. By understanding the condition of these critical assets, nuclear facilities can implement timely maintenance, repairs, or replacements, minimizing risks and maximizing performance.
Hope that helps 🙂
-
Log in to reply.