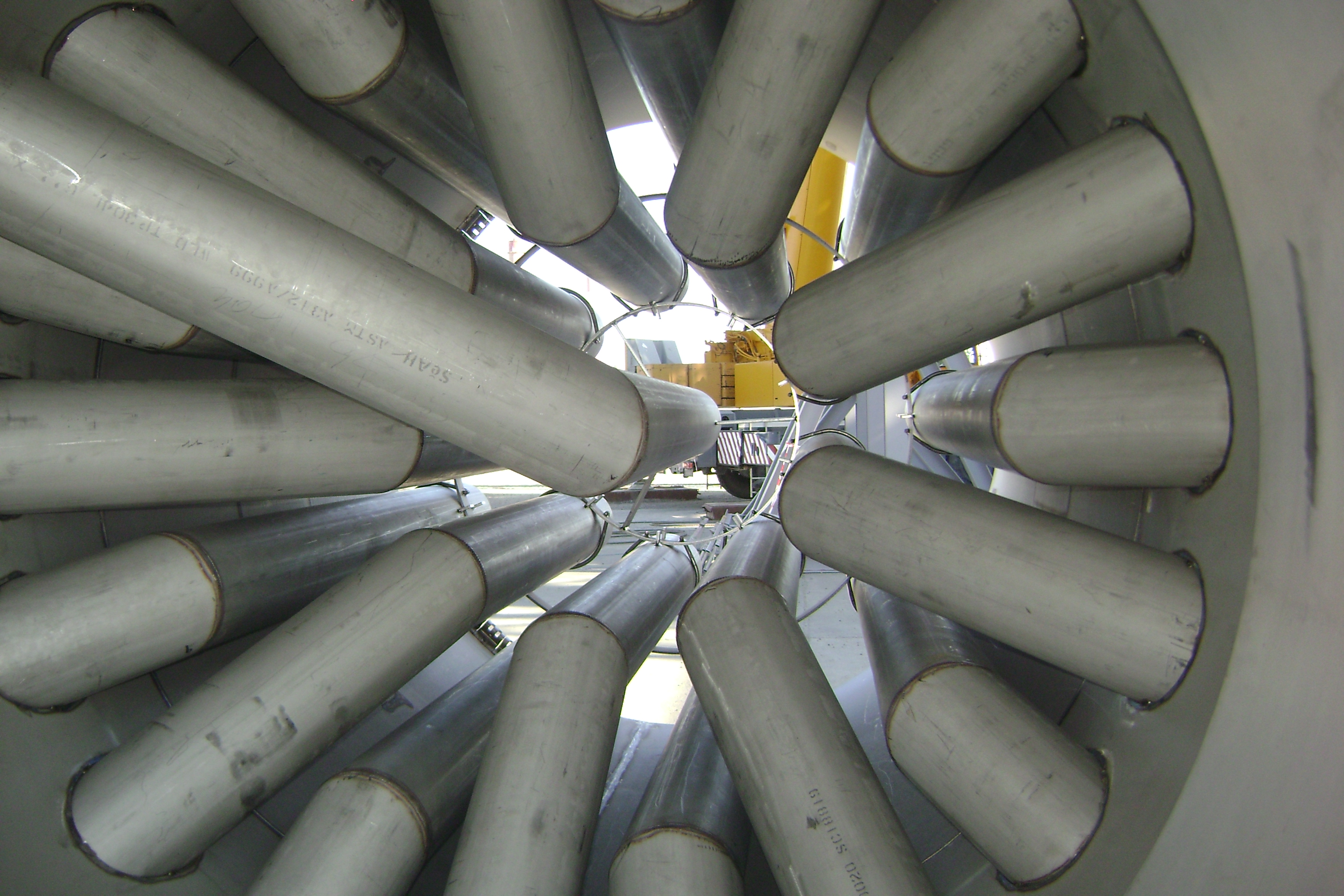
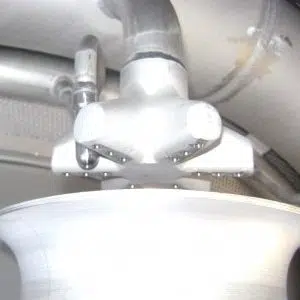
Quality Control (QC)
Welcome to [NDT Inspection Portal]’s quality control group, a place for professionals to connect... View more
Maximizing the Benefits of NDT for Quality Control in Manufacturing
-
Maximizing the Benefits of NDT for Quality Control in Manufacturing
Quality control is a critical aspect of manufacturing, as it ensures that products meet certain specifications and standards and helps to prevent costly defects or failures.
Non-destructive testing (NDT) is a valuable tool for achieving high levels of quality control, as it allows practitioners to evaluate the properties and condition of materials, components, and systems without causing damage.
In this discussion, we will explore the various ways in which NDT can be used for quality control in manufacturing, as well as best practices and case studies for maximizing the benefits of this technique.
Subtopic 1: Common NDT Techniques for Quality Control in Manufacturing
There are several NDT techniques that are commonly used for quality control in manufacturing, including:
-
Ultrasonic testing: This technique uses high-frequency sound waves to inspect the internal structure of a material or component. It is often used to detect defects such as cracks, voids, and inclusions.
-
Eddy current testing: This technique uses an alternating current to induce a magnetic field in a conductive material, and then measures the response of the material to the field. It is often used to detect surface and near-surface defects such as cracks, corrosion, and delaminations.
-
Radiographic testing: This technique uses X-rays or gamma rays to create an image of the internal structure of a material or component. It is often used to detect defects such as cracks, voids, and inclusions, as well as to measure thickness and dimensions.
Subtopic 2: Benefits of Using NDT for Quality Control
There are several benefits of using NDT for quality control in manufacturing, including:
-
Early identification of defects: By using NDT to inspect materials and components at various stages of the manufacturing process, practitioners can identify defects early on, before they become a problem. This allows manufacturers to take corrective action before the product is shipped, which can save time and money.
-
Prevention of costly defects or failures: By using NDT to identify and correct defects, manufacturers can prevent costly failures or recalls down the line. This is especially important in industries such as aerospace and automotive, where defects or failures can have serious consequences.
-
Reduction of the need for destructive testing: NDT allows practitioners to evaluate materials and components without causing damage, which can save time and money compared to destructive testing methods. In some cases, NDT may be the only feasible option for evaluating certain materials or components, such as historic artifacts or one-of-a-kind prototypes.
Subtopic 3: Challenges of Using NDT for Quality Control
While NDT is a powerful tool for quality control, there are also challenges that practitioners may face when using it, including:
-
Complex geometries: Some materials and components may have complex shapes or features that make them difficult to inspect using NDT techniques. For example, an airplane wing may have intricate internal structures that are hard to access or visualize using ultrasonic testing. To overcome this challenge, practitioners may need to use specialized NDT equipment or techniques, or develop custom inspection procedures.
-
Difficult-to-inspect materials: Some materials may be difficult to inspect using NDT techniques due to their physical properties or characteristics. For example, materials with high conductivity, such as copper or aluminum, may interfere with eddy current testing, while materials with high attenuation, such as lead or concrete, may absorb X-rays or gamma rays, making it difficult to get a clear image using radiographic testing. In these cases, practitioners may need to use alternative NDT techniques or adjust the inspection parameters to get accurate and reliable results.
-
Limited depth of inspection: Some NDT techniques may only be able to inspect the surface or near-surface of a material or component. For example, ultrasonic testing may only be able to detect defects that are within a few millimeters of the surface. In these cases, practitioners may need to use multiple NDT techniques or combine NDT with other inspection methods, such as visual inspection or destructive testing, to get a complete picture of the material or component.
-
Log in to reply.