Nuclear Sector and NDT Use
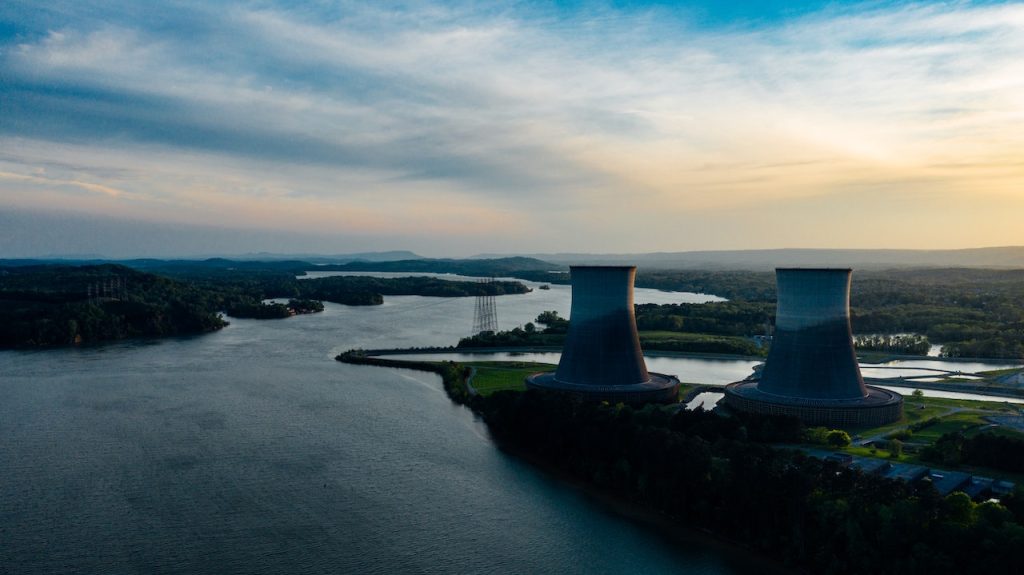
The nuclear industry plays a vital role in providing energy to the world and has continued to grow in recent years.
One of the most important aspects of this industry is ensuring the safety and reliability of the nuclear reactors and equipment.
Non-destructive testing (NDT) is an essential tool used to achieve this goal, as it allows for the inspection of critical components without causing damage to them. In this article, we will discuss the use of NDT in the nuclear industry, the most common components inspected, and the most critical components that require inspection and maintenance.
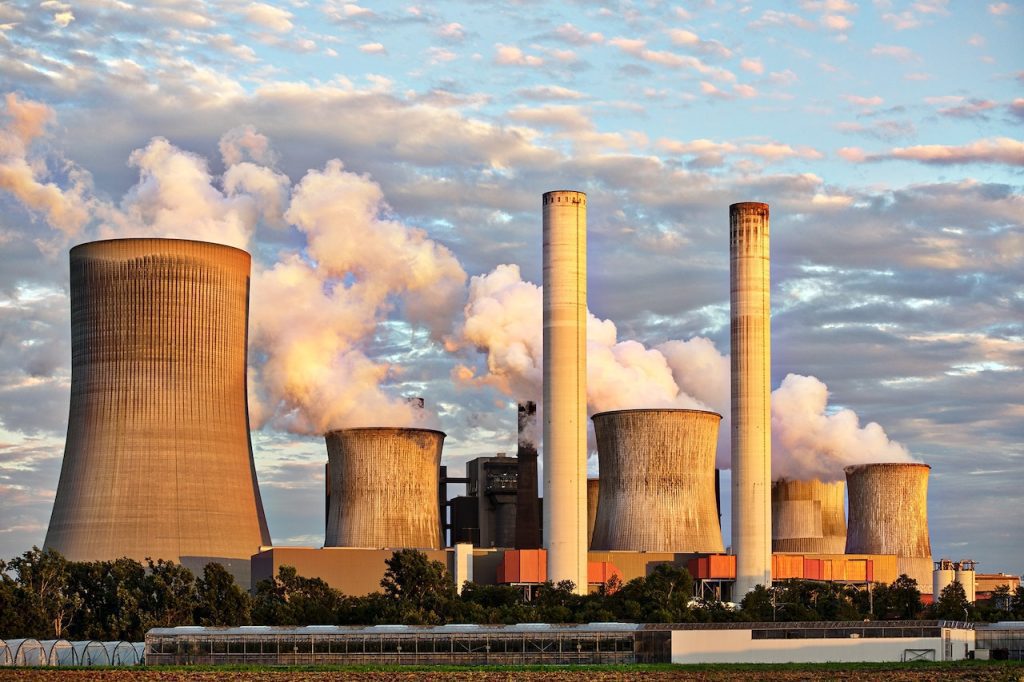
NDT in the Nuclear Industry
NDT is a group of techniques used to evaluate the properties of a material, component, or system without causing any permanent damage.
This is particularly important in the nuclear industry, where the safety of the reactors and the surrounding environment is of the utmost importance.
NDT is used to check for defects, cracks, corrosion, and other issues that could potentially compromise the safety of the reactor.
Common Components Inspected
Some of the most common components inspected using NDT in the nuclear industry include:
- Reactor pressure vessels: These are the primary containment for the reactor and must be able to withstand high pressures and temperatures. NDT is used to check for cracks, defects, and corrosion.
- Steam generators: These are used to transfer heat from the reactor to the turbine and must be able to withstand high temperatures and pressures. NDT is used to check for cracks and corrosion.
- Pipes and tubing: These are used to transport coolant and other fluids throughout the reactor and must be able to withstand high pressures and temperatures. NDT is used to check for cracks, defects, and corrosion.
Most Critical Components in Nuclear Industry
The most critical components in the nuclear industry that require inspection and maintenance include:
- Reactor pressure vessel: The integrity of the reactor pressure vessel is crucial for ensuring the safety of the reactor. Any defects or cracks in the vessel could lead to a release of radioactive material.
- Control rods: Control rods are used to control the rate of the nuclear reaction and must be able to function properly to ensure the safe operation of the reactor. Any defects or damage to the control rods could lead to an unsafe situation.
- Coolant system: The coolant system is responsible for removing heat from the reactor and must be able to function properly to ensure the safe operation of the reactor. Any leaks or other issues with the coolant system could lead to an unsafe situation.
Incidents in nuclear industry due to cracking and corrosion
- Cracking and corrosion can occur in various components of a nuclear power plant, including the reactor vessel, piping, and cooling systems.
- One example of a significant incident due to cracking and corrosion was the Davis-Besse Nuclear Power Station in Ohio, USA in 2002. The incident was caused by corrosion of the reactor vessel head, which had gone undetected for several years.
- Another example was at the San Onofre Nuclear Generating Station in California, USA in 2012, where a leak in a steam generator tube was caused by corrosion and wear.
- In both cases, the incidents were caused by a failure to properly maintain and inspect the affected components, leading to prolonged exposure to harsh operating conditions.
- Cracking and corrosion can also be caused by stress corrosion cracking (SCC), a type of corrosion that occurs in materials under mechanical stress and specific environmental conditions.
- To prevent cracking and corrosion incidents, nuclear power plants conduct regular inspections and maintenance on their components, using NDT methods such as ultrasonic testing and eddy current testing to detect any signs of damage.
- Nuclear power plants also have strict guidelines and regulations in place to ensure that all components are designed and constructed to withstand harsh operating conditions and to minimize the risk of cracking and corrosion.
- Additionally, research and development in materials science and corrosion-resistant alloys are ongoing to improve the durability and longevity of nuclear components.
- Proper operation, maintenance, and monitoring of the nuclear power plants are critical to prevent such incidents and keep the public safe.
- International Atomic Energy Agency (IAEA) also developed the Integrated Regulatory Review Service (IRRS) to help countries review their regulatory frameworks to ensure the safety of their nuclear power plants.
Conclusion
NDT is an essential tool used in the nuclear industry to ensure the safety and reliability of the reactors and equipment. It is used to check for defects, cracks, corrosion, and other issues that could potentially compromise the safety of the reactor.
The most common components inspected using NDT include the reactor pressure vessel, steam generators, and pipes and tubing.
The most critical components that require inspection and maintenance include the reactor pressure vessel, control rods, and coolant system.
Regular NDT inspections and maintenance are crucial for ensuring the safe and reliable operation of nuclear reactors.
Please visit our Nuclear Sector NDT forum or or Group for more information.
Responses