What is NDT Non-Destructive Testing
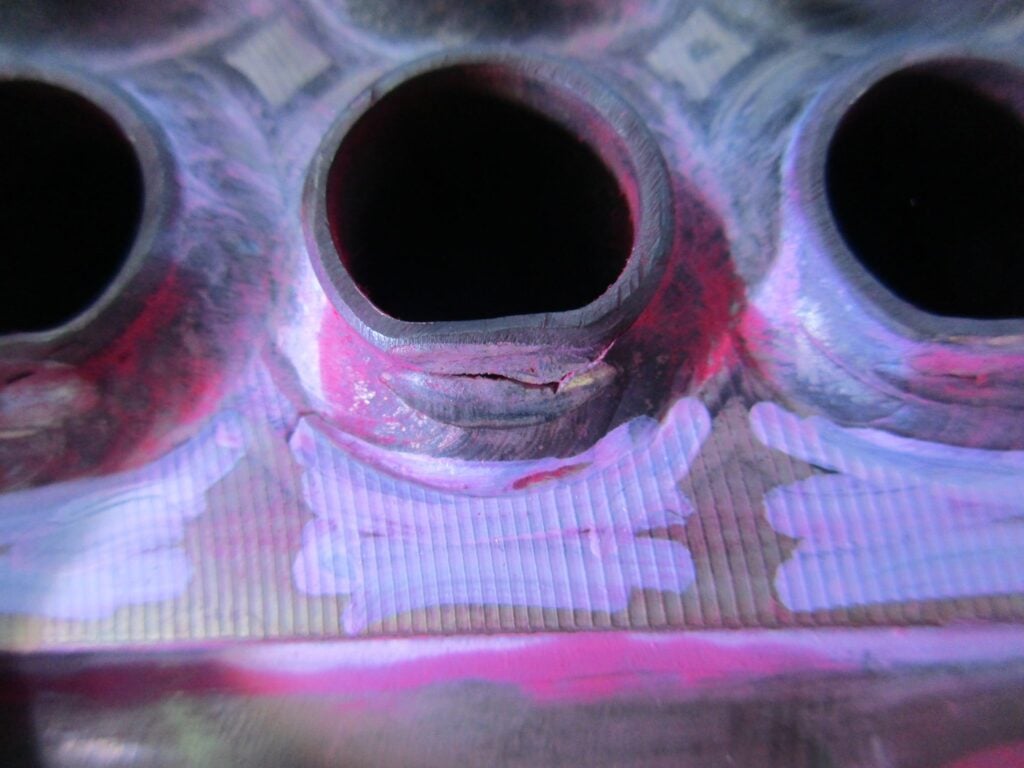
An evaluation of the materials or structures without damaging the integrity of the product, their surface texture and usefulness in future is described as Non-destructive testing (NDT).
Destructive testing (DT) includes techniques where the information of the material is taken out by damaging the integrity of the component. In certain applications, the evaluation of engineering materials or structures without destructive testing is very significant, such as, failure analysis, stoppage of failure of engineered systems in provision and quality control of the products.
What is NDT and its scope.
The scope of the NDT is wide-ranging and interdisciplinary that plays a vital role in inspection; that systems and structural components execute their functions in a reliable manner.
Standards are implemented to ensure the reliability of testing techniques to many folds and also to avoid errors due to fault in equipment used, skills and knowledge of the operator.
Without destructive testing of the original part, NDT is used in various industries to assess the properties of materials, components, structures and systems for characteristic variances or welding flaws and discontinuities.
Apart from phrase ‘Non-Destructive Testing’, Non-Destructive Inspection (NDI) and Non-Destructive Examination/Evaluation (NDE) phrases are also commonly used.
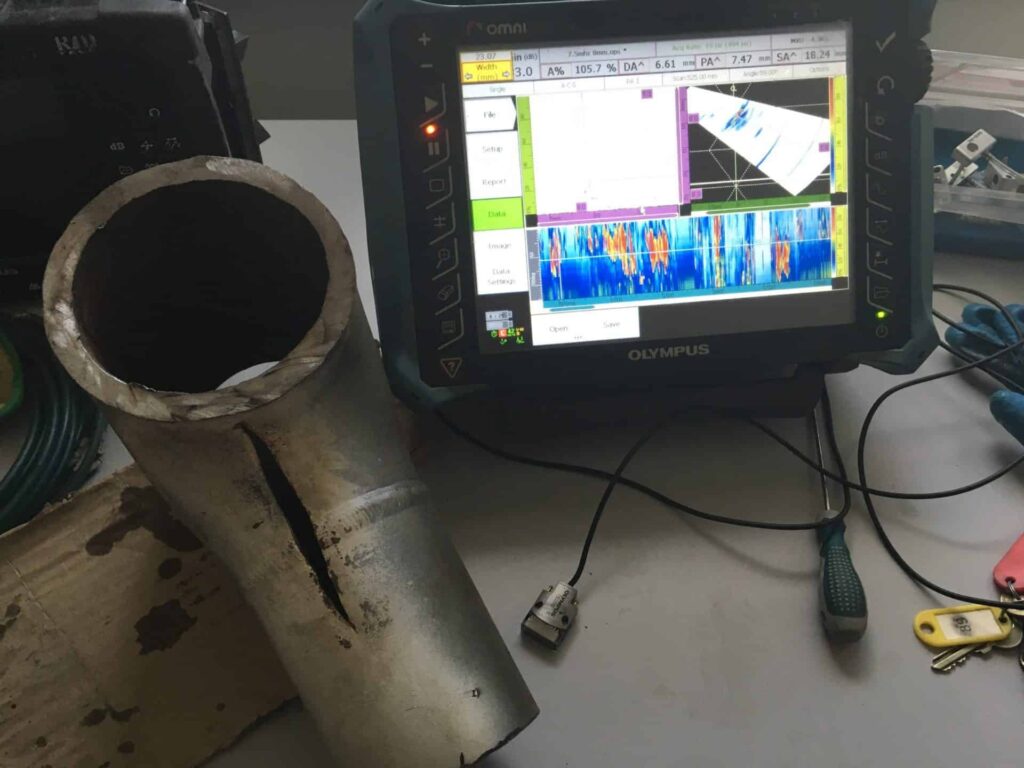
1. How many different techniques are developed for Non-Destructive Testing? (NDT Methods)
Eight major types of inspection techniques are in common use at industrial level.
It is the most common non-destructive testing technique where visual data is collected on the status of material. It is capable of detecting macroscopic surface flaws and unable to detect small or subsurface defects.
It is a technical field of using microscope to observe samples which can’t be seen through naked eye. It is capable of detecting flaws at micro-level and not suitable to subsurface defects or on large components.
In this technique, radiations (Gamma or X-ray) are used on materials to detect the imperfection or discontinuity. It can detect subsurface defects but it is not applicable for the subsurface flaws of porous materials.
It can detect imperfections/defects open to the surface but cannot be used for porous materials. It is considered among the most cost-effective method of NDT.
This technique is used to measure the thickness of the materials and also defects under the surface. Sound waves are used in this technique for mentioned purpose. Material should be a good conductor of sound.
It is used to spot the surface and subsurface defects on ferromagnetic material by running a magnetic current through it.
It is highly sensitive technique which can detect very small (~0.5mm) defect on the surface or beneath the surface. It is not capable of detecting defects parallel to the testing object’s surface.
It requires expensive equipment and capable of finding defects throughout the structure but the data is difficult to interpret.
• Leak Test (LT)
Leak tests are used to detect leakages in pressure container. It can be carried out by using liquid/gas penetration technique, electronic listening devices, pressure gauge measurement or by soap bubble test.
2.Which materials can be inspected by utilizing NDT methods?
All major classes of materials, such as metals, alloys, ceramics, coatings, polymers, composites and cermet, can be tested non-destructively by utilizing suitable techniques. Such as RT can’t be used for porous materials. Nickel, copper, iron and cobalt are ferromagnetic material and perfect candidate for MPT.
On surfaces, ET is equally suitable for ferromagnetic as well as non-ferromagnetic materials. Finding a defect through NDT requires the understanding of more than one technique in many cases.
It usually needs multiple techniques and also factfinding, invasive openings. In order to ensure the success of the evaluation, a good understanding of background, benefits and constraint of each NDT technique is indispensable.
3.What are the benefits of NDT techniques?
These techniques possess several benefits at industrial level and also can benefit your business. Few of the advantages are as follow;
4.Which industries are facilitated by Non-Destructive Testing methods?
These techniques are used in various industries whether it is being utilized in industrial machinery testing or qualification of end product. Few industries which are facilitated by these techniques are given below;
NDT techniques are well developed but there is always room for research and modification. In that aspect, researchers are still exploring that field extensively and stating their findings in order to open the gates for further future work. As per Sanjay Kumar & Dalgobind Mahto, most of the NDT methods are mainly used in the manufacturing and aerospace industry.
These techniques have the potential to be used for assessing civil infrastructures. In another research by Gabriel Dan Taşcă, Gheorghe Amza, UT evaluation technique is utilized to inspect/examine the features beneath the surface in titanium alloys.
We also discovered that for critical and intricate part examination the ultrasonic testing gives the appreciable results among all NDT techniques. Utilization of latest research work, is emphasized for better understanding and utilization of NDT techniques.
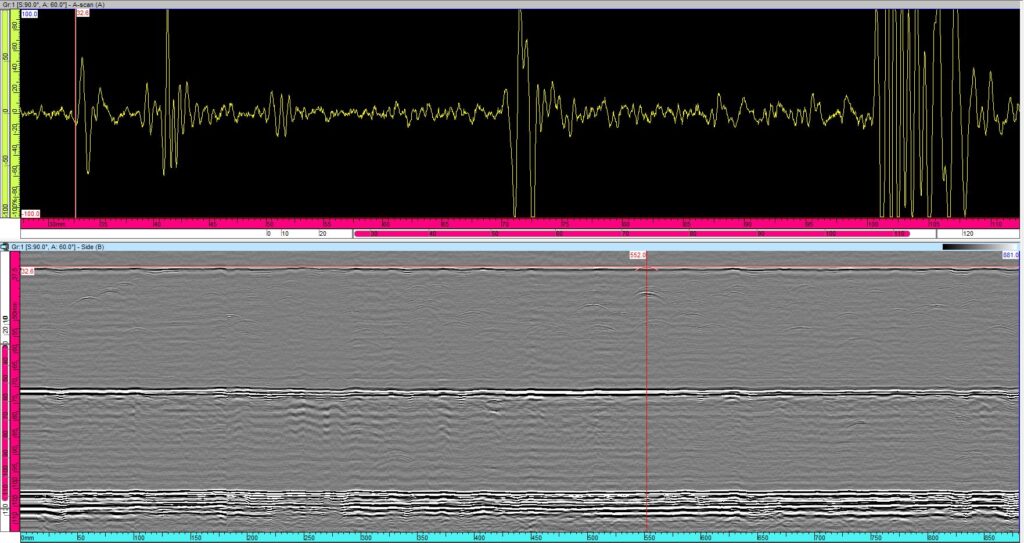
Please join our NDT Forum where more information can be obtained.
Responses