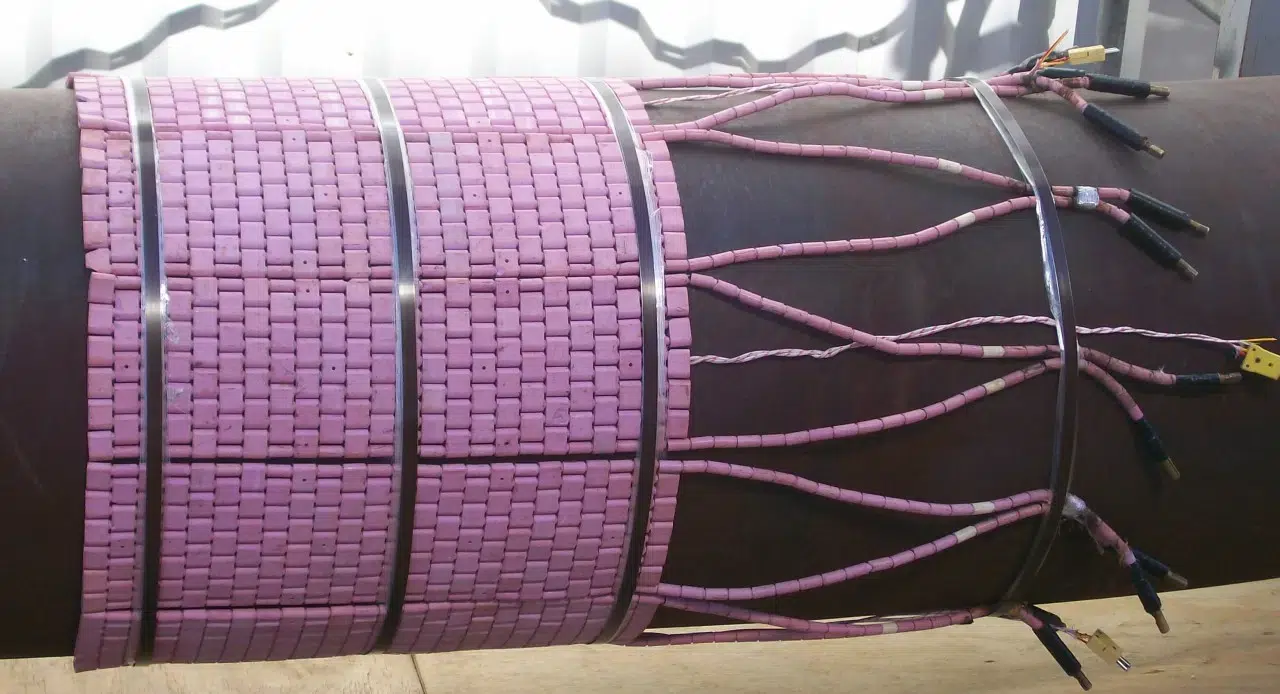
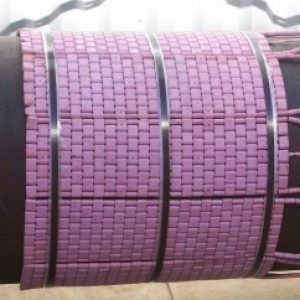
Heat Treatment (PWHT)
Public Heat Treatment
Active 11 months ago
Welcome to [NDT Inspection Portal]’s heat treatment (PWHT) group, a place for professionals to connect... View more
Public Heat Treatment
Group Description
Welcome to [NDT Inspection Portal]’s heat treatment (PWHT) group, a place for professionals to connect and discuss the latest techniques and technologies in heat treatment.
Heat treatment is a process used to alter the physical and mechanical properties of materials through the application of heat and cooling. It is often used to improve the strength, hardness, ductility, and other properties of materials and is an important aspect of ensuring the quality and performance of products and structures in various industries.
Post-weld heat treatment (PWHT) is a specific type of heat treatment that is applied to welded joints and components to improve their properties and performance. It involves the application of heat to the welded joint or component after welding is complete, followed by a controlled cooling process. PWHT is often used to reduce residual stress and improve the toughness and corrosion resistance of welded joints and components.
Our member group offers a platform for sharing knowledge and best practices on heat treatment and its applications in various industries. Join our community of experts from around the world and be a part of the conversation on advancing the practice of heat treatment and its applications in the field of NDT and inspection. Whether you are new to heat treatment or an experienced professional, you’ll find valuable resources and a welcoming community in our group.
PWHT and hardness
-
PWHT and hardness
Posted by harry on 27/11/2021 at 6:34 pmAssume the Hardness value was not reduced to 22 HRC after the PWHT testing on the pipe weling. In that case, How can we reduce again the hardness to less than 22 HRC to suit the NACE sour service requirement
anthony-wohali replied 3 years, 9 months ago 2 Members · 1 Reply -
1 Reply
-
Dear Sir,
Generally PWHT (post weld heat treatment) is called stress relieving (SR) treatment and its objective as applicable to carbon and low-alloy steel weldments is mainly to relieve the residual stresses caused by welding.
In this process the high hardness of the heat affected zone (HAZ) and also that of the weld are considerably reduced/homogenized, ductility and notch toughness are improved, and diffusible hydrogen is dissipated.
But the main aim of this PWHT is to relieve the harmful residual stresses.
When it comes to the reduction of hardness (like reduction of residual stresses), it depends on many factors like 1. Initial hardness and its distribution in weld metal, parent metal and HAZ. 2. The peak temperature used for stress reliving. 3. The duration of hold time at the peak temperature (which is arrived based on the thickness of the part/weld) 4. Cooling cycle chosen up to 300°C.etc.
Based on the composition the stress reliving temperature ranges from 550° to 675° C. For T22 material it can go up to 690° to even 720°. The SR temperature is very much dependent on the composition and the degree of reduction/homogenization required in the stresses.
The stress relieving temperature is normally kept below (normally by about 30°C) the tempering temperature known as Ac1, also called the lower critical temperature. If the temperature exceeds this (Ac1) more metallurgical changes occur where by hardness reduction is rapid. As such the SR is done below this Ac1 temperature. When the heat treatment is done above the Ac1 it is known as tempering.
In general higher the stress relieving temperature lower are the residual stresses and higher is the reduction in hardness.
Similarly if the hold time is on the higher side, higher is the reduction in hardness and residual stresses. Hold time at the peak temperature is generally given as one hour per/ inch of thickness, but in no case less than 1/2 hr, and the weld shall be allowed to cool slowly and uniformly.
Having said the above, please remember that the hardness reduction is not uniform in all the three zones, namely, weld, HAZ, and parent metal. Based on factors like welding method, composition of the parent metal and welding rod, preheat temperature, even the welding rod size (dia.), speed of the welding, inter-pass temperature the hardness can vary widely between weldments and HAZ. (Basically these are some of the factors that control the heat input during welding).
The hardness reduction after PWHT is dependent on its initial value and distribution, as measured before PWHT. At a given SR temperatures the HAZ hardness may come down steeply but not that of weld. The point is that after PWHT the reduction in hardness is not uniform in all the three zones.
The above are some of the general points governing the reduction in hardness in PWHT. If you give more details like composition, welding process etc. you may get more specific and better opinions from other experts.
Best wishes
Log in to reply.