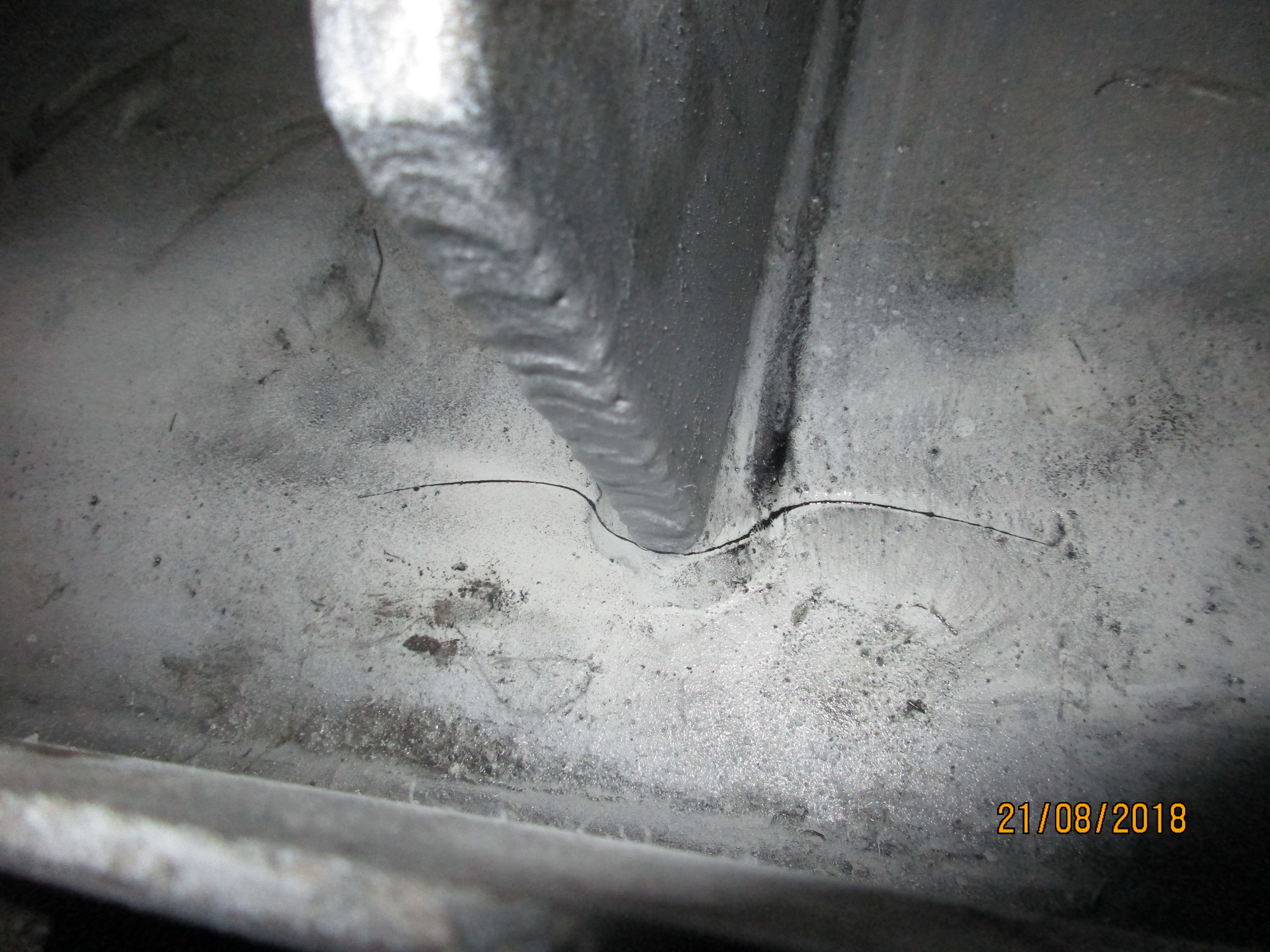
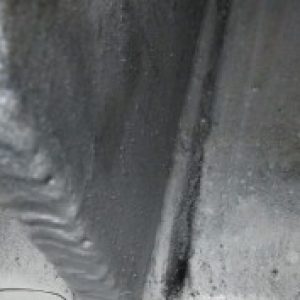
Magnetic Particle Inspection (MPI) (MT)
Welcome to [NDT Inspection Portal]’s Magnetic Particle Inspection (MPI) group, a place for... View more
What is MPI/ MPT
-
What is MPI/ MPT
A fine ferromagnetic particle is applied to the surface of the magnetised part and aligns with the magnetic flux leakage area indicating the presence of discontinuities. In this course, students learn the principle of magnetism, as it refers to the detection of errors in a ferrous magnetic material.
An error attracts more particles because it cuts more magnetic force lines and the ability to show the error depends on the depth of the error, the angle of its force line to the magnetic field and the strength of the induction magnetization.
Magnetic particle testing uses magnetic fields to find superficial discontinuities in ferromagnetic materials such as steel. Ferromagnetic material, such as iron and steel, is flawless because it transmits lines of magnetic flux fields to each other without interruption. When these lines release the magnetic flux, the magnetic field collects ferrous magnetic particles (iron powder) that reveal size, shape, cracks, and other discontinuities.No signs of discontinuities such as cracks parallel to the line of magnetic flux leakage can be observed. Detection of discontinuity is more sensitive to vertical discontinuities, so it is important to inspect from different angles when changing the magnetic field. Remaining continuous techniques, in which a flow of particles is used to give a part a high degree of magnetism, lead to larger flux leaks at discontinuity points, which leads to a clearer indication.
This technique requires a current or magnetization force, which is applied simultaneously with the application of the particles to the specimen under test.When the particles accumulate in the area, a magnetic flux leak indicates the characteristic type of discontinuity that is detected. Smaller particles, which are held in a weak magnetic field, can be detected with fine indications.
The number of particles attracted by discontinuity depends on how local magnetic poles are formed. Larger particles adhere to the surface of discontinuity. Longer particles tend to have pronounced magnetic poles, allowing particle chains to form for clues.The iron fillings that accumulate on the edge of the fault will reveal cracks and other defects. If the fault lies on the surface, the flux leakage field pulls metal particles away from the damage site. Defects that occur are eliminated and the area repaired by re-examining the same method.
Iron particles are applied to the component in a dry or wet suspension. For dry particles use an alternating current yoke or DC prod with a permanent magnet. For particles used in a wet system, pigments are applied fluorescing at 365 nm in UV light and require 1,000 MW / cm2 (10 W / m2) on the surface of the component for proper inspection.Magnetic particle inspection (MPI) is a non-destructive testing method (NDT) for the detection of superficial and superficial discontinuities in ferromagnetic materials such as iron, nickel, cobalt and their alloys. It is a non-destructive testing method (NDT) used to check the near-surface or near-surface discontinuity of ferrous materials. In a wet horizontal MPI machine, a 36 x 910 mm coil is used, or in a similar US Navy machine, a technician sprays magnetic particles to test parts with ultraviolet light.
Magnetic particle inspection (MPT), also known as Magnetic particle inspection or NDE (non-destructive testing) is a technique used to detect surface and substrate defects in most ferromagnetic materials such as iron, nickel, cobalt and their alloys.Magnetic particle testing (MT) is one of the oldest and most reliable NDT methods and is not considered a glamorous but necessary method in the field of material testing. One important variable to take into account is the procedure for carrying out the inspection, but the MT is a simple and reliable method that can be carried out by qualified personnel with qualified procedures and appropriate equipment.
Magnetic particle testing is a great tool if you’re looking for a crane or hook to inspect your hooks and equipment that require ASME standards for use, but you don’t need it if it’s a specific application where you know you’re stressing and fatiguing the material unnaturally. If you are thinking about non-destructive testing in other ways, use it when it is not needed.
In summary, magnetic particle investigation is a useful non-destructive method of investigation for new buildings and inspections. In general, it is a fast, cost-effective inspection and a good NDE method for detecting surface and subsurface discontinuities.
Sorry, there were no replies found.
Log in to reply.